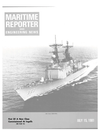
Rubber Fendering Reduces Damage To Vessels And Piers
According to Michael W. Brakey, chief engineer of the Duramax Marine Division, The Johnson Rubber Company, in times of climbing ship repair costs and expensive general maintenance, rubber fendering is proving itself to be a highly flexible, energy-absorbing friend to the marine industry. Vessels are built today with the maximum economy of materials to minimize capital investments and can ill-afford drydocking due to berthing accidents. The same can also be said for the harbors. Berthing damage and repairs are unneeded expenditures and far too costly to be repeated time and time again. For this reason it may prove worthwhile to understand, at least to some degree, the forces involved with a berthing vessel and how a properly selected fender comes into play.
A berthing vessel can only come to rest by transferring all the "motion energy" within it to the surrounding environment.
This motion or kinetic energy must be absorbed and dissipated by (1) the sea, (2) the elasticity of the fendering, (3) the elastic deformation of the vessel's hull, and (4) the elastic deformation of the pier. As evidenced by ships and harbors throughout the world, if the sea and fendering do not use their maximum energy-absorbing capabilities, damage can result to the vessel, to the berthing structure or both.
Begin with the speed and angle of the approaching vessel. The motion energy of the ship varies as the square of its velocity.
A ship that berths at a speed of 3 feet per second has nine times greater energy than the same vessel berthing at 1 foot per second.
Also of major significance is the angle of approach by the ship in berthing. Only the vessel's velocity perpendicular to the pier is used for determining the amount of motion energy to be absorbed. A vessel moving at 1 foot per second at an angle of six degrees to the pier would have a berthing velocity of 0.10 per second.
Remembering to square the velocity term, we find that the total motion energy to be absorbed by the vessel berthing at six degrees is 100 times smaller than the same vessel berthing at 90 degrees (striking the pier head on).
When a ship makes contact with the pier at an angle other than 90 degrees, it will be acting as a lever and will rotate around its axis. This will reduce the force of impact considerably. The percentage of motion energy absorbed by the sea under such action can be as high as 75 percent where the berthing point of contact between the ship economical fender for a specific task, a simple, ratio R/E, has been found useful.
Maximum Reaction Load _R_ Acceptable to the Ship or Pier E Motion Energy to be Absorbed by the Fender • j j i f u — A double row of several heavy duty tubular rubber fenders are fastened in place with chains letting each section independently perform protection to both vessel and dock.
and pier is far forward or astern of the vessel's center of gravity. It is usually assumed that quarter point berthing shall occur, which results in half of the total motion energy being absorbed by the sea. The remainder must be absorbed by the fendering, the vessel's hull, and the pier.
When a marine fender is struck, it deflects.
This deflection is proportional to the amount of motion energy it must absorb. As the fender deflects it offers increasing resistance, which is measured as a reaction load. This growing resistance by the deflecting fender is experienced by both the pier and vessel's hull. (Imagine trying to compress a coil spring between your hands. The further you compress it, the more resistance it offers.
Which hand feels the greater resistance?) A properly selected marine fender should be capable of absorbing this motion energy without offering a resistance so high that it might lead to structural damage of either the pier or vessel hull.
A high resistance often results when a selected fender is too small for a required energy absorption. Energy absorption is equal to the fender's deflection times its resistance to deflection. When a fender can only offer a small amount of deflection compared to the energy absorption demands made upon it, higher resistances result.
Once the fender can no longer deflect any farther, the remaining motion energy must be absorbed by the harbor pier and the vessel's shell. Here lies the danger of berthing damage.
Two factors to be weighed carefully in selecting a marine fender are energy absorption capabilities and corresponding reaction loads (the fender's resistance to a given deflection).
It is generally seen that larger fenders offer greater energy absorptions and relatively lower reaction loads when compared to smaller fenders of the same geometry.
To aid in the selection of the most The appropriate fender for any installation should have an R/E equal to or less than the value calculated above.
Yesterday's economics could afford to believe an old tire suspended from a chain was good fendering. In today's economy, unfortunately, such thinking is proving itself costly. The need for efficient, energy-absorbing fendering and an education of its potential is of growing importance. Fortunately, research and product improvement is being actively pursued, not only by Johnson Rubber Company but by many fender manufacturers.
By such action, rubber fendering will today, and tomorrow, continue to be the flexible friend of the marine industry.
Read Rubber Fendering Reduces Damage To Vessels And Piers in Pdf, Flash or Html5 edition of July 15, 1981 Maritime Reporter
Other stories from July 15, 1981 issue
Content
- Bay Building Barge With First Conveyor To Handle Wet Phosphate Rock page: 6
- Robert Ware Establishes His Own Maritime Public Relations Service page: 7
- Circular Detailing New Suez Canal Regulations Available From Candia page: 7
- IMODCO Receives Order From Petrobras For $5-Million SPM Terminal page: 7
- Wartsila Turku Shipyards Delivers Superferry 'Silvia Regina' page: 8
- U.S. Combat Systems In Foreign Built Ships Topic At ASNE Meeting page: 8
- Puget Sound Tug & Barge Will Build 12 Barges Costing $39.5 Million page: 9
- Seaco Energy/Coastal Carriers Joint Venture Plans Floating Terminals page: 9
- First Of New Destroyer Class Commissioned At Ingalls Yard page: 10
- Santa Fe Diving Services Awarded Contract To Provide RCV And Crew page: 10
- National Steel Lays Keel For U.S. Navy Cable Repair Vessel page: 10
- Second Crandali Dock At National Sea Products Yard Rebuilt And Enlarged page: 12
- Anthony McAllister Jr. Elected Chairman Of New York Towboat Association page: 14
- $172-Million Navy Order To Bell For New Type Landing Craft page: 14
- Theriot-Modec To Build Ammonia Barge For Energy Transportation Subsidiary page: 15
- Edward Campbell Named To Board Of Trustees At Webb Institute page: 15
- $140-Million Contract For Two Offshore Rigs Awarded To Gotaverken Arendal Shipyard page: 16
- Benson, Basse And David Join Tampa Barge In Management & Production page: 16
- Delaware Valley ASNE Chapter Discusses Government Contracting page: 16
- Hudson Delivers The 'Gulf Dolphin7 To Gulf Fleet Marine page: 18
- Third Seaboard RO/RO Ordered At Fredriksstad Yard Will Have MacGregor Hoistable Decks page: 18
- Grumman Hydrofoil For Israel Launched At Lantana Boatyard page: 20
- Dravo-Built Towboats For China Get A Lift From Dock Express page: 20
- Petronio Elected VP-Engineering At Pool Company Of Houston page: 21
- Two MARCO Oil Skimmers Delivered To Mexican Navy page: 21
- David Taylor Naval R&D Center Hosts Hydromechanics Meeting page: 22
- W.B. Buhrmann Elected President Of Newly Formed U.S. Steel Companies page: 24
- Valley Line Asks Title XI For $90.1-Million Barge And Towboat Project page: 24
- Petro Marine Services To Build $25-Million Shipyard In Alaska page: 26
- Riverway Completes Second Drydock For Its Own Repair Division page: 27
- New Brochure Describes National Crane's Line Of Marine Lifting Systems page: 27
- Shipyard Conference Honors Past Chairmen McKay And Pirozzolo page: 28
- HUDSHIP To Build Four Big Towing/Supply Vessels For Zapata page: 29
- U.S. And Canada Agree To Cooperate In Marine Transportation R &D page: 34
- Philadelphia Resins' New Brochure Describes The Company And Its Products page: 34
- Griffin & Alexander Jackup Rig Commissioned At Bethlehem-Beaumont page: 35
- Lima Electric Announces New Model Alternator- Literature Available page: 35
- Raytheon Opens New Marine Sales And Service Facility In Mississippi page: 36
- Partnership Between AMCA International & McDermott Formally In Business page: 36
- Seminars On Rig Moves Organized By Marine Design International page: 37
- Dome Acquires Davie Shipbuilding At Total Cost Of $38.6 Million page: 38
- Riverway Shipyard Delivers GM-Powered Towboat 'Waterways Explorer7 page: 38
- Largest DMI Dredge Delivered To Mexican Owner page: 39
- Rubber Fendering Reduces Damage To Vessels And Piers page: 40
- Sembawang Yard Completes Multimillion-Dollar Overhaul Job On McDermott Barge page: 40
- APL Ready To Build 45-Foot Production Unit Containers page: 41
- Tracor Marine Awarded $2.5-Million Navy Contract To Manage OCEI Facilities page: 42
- Ned Smith Named Vice President-Finance For American Steamship page: 42
- Dravo To Provide People's Republic With Technical Assistance And Equipment page: 42
- McDermott Incorporated Promotes Four To « Vice President Posts page: 43
- Multipurpose Cargo Vessel Launched At GHH Sterkrade Yard page: 44
- New York Maritime Day Ceremonies Featured Presentation Of Two Awards page: 58
- Todd Shipyards Awarded Navy Study Contract On DDGX Producibility page: 58
- Butterworth Tank Washing Machines Ordered For Eight New Product Carriers page: 59
- Bulk Carrier 'Star Of Texas7 Launched At Levingston Yard page: 59