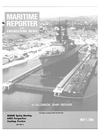
Mitsui Delivers Big Ore Carrier With M a n y Energy-Saving Features
The 197,060-dwt ore carrier Asakasan Maru, built at the Chiba Works of Mitsui Engineering & Shipbuilding Company (MES), was delivered recently to joint owners Mitsui O.S.K. Lines and Sawayama Kisen Kaisha, Ltd. The big vessel has an overall length of 984.25 feet, beam of 164 feet, depth of 79 feet, and full-load draft of 58.5 feet. She is powered by a slow-speed Mitsui/ B&W 7L80MCE diesel engine with a maximum continuous output of 20,700 bhp at 80.8 rpm. On sea trials the ship attained a speed of 16.35 knots.
A special feature of the new ore carrier is the superstructure located aft, which is shaped like a compact, streamlined tower. Such towershaped superstructures have been used by MES in the past for the construction of only four vessels— three tankers built in 1965 for Fred Olsen of Norway, and another in 1968 for Anders Wilhelmsen & Company, also of Norway. Reflecting the current increasing need for energy efficiency in ships, use of this unusual type of superstructure to reduce air resistance is now attracting renewed interest.
The Japan Marine Machinery Development Association, taking note of the advantage of this superstructure design, in 1981 set up a research subcommittee to study the resistance of offshore structures to wind pressures. As the effects of the tower-shaped superstructures had not been fully assessed in numerical terms, the subcommittee carried out research and investigation in various aspects, both theoretically and experimentally.
Participating in this research project, MES was commissioned to conduct an experimental study on the effect of reduced resistance on compact, streamlined superstructures on ships. With the cooperation of her co-owners, such a superstructure was incorporated into the design of the Asakasan Maru.
A Mitsui ATG-V turbogenerator system (mixed-pressure turbine system) is installed for maximum utilization of the waste heat of the main engine exhaust. The ship is also equipped with a thyristor convertor- invertor type shift generator (that can be used as an emergency propulsion motor), and a power management system for maximum effective utilization of the turbogenerator's output.
Other energy-saving features include a Mitsui Integrated Duct Propeller, a reaction rudder, and extensive use of high-tensile steel in the hull structure. The hull bottom and waterline area are coated with selfpolishing antifouling. Windlasses, mooring winches, and deck washing system are fitted with remote control systems with a view to reducing the crew's workload. The engine control room and cargo control room are integrated for more rational performance of the duties of both.
The engine room is designed for unmanned operation, and has obtained NK's "MO-A" notation. •
Other stories from May 1985 issue
Content
- Slaybaugh Named Vice President And COO For Bombardier/Alco Power page: 5
- MARDATA Adds Baltic Index To Its Maritime Database Service page: 5
- Scheidt Named Marketing And Sales Vice President For American Steamship page: 5
- Radio-Holland USA, B.V. Automates Coastal Station WLO's Radiotelex Service page: 5
- Self-Propelled Drillship for India Completed By Hitachi's Osaka Works page: 6
- Terry Announces New GLT Single-Stage Turbine page: 6
- V e r s a t i l e Corporation Buys Davie Shipbuilding Yard From Dome Petroleum page: 7
- N e w l y Formed Company Acquires Compressor Line From Allis-Chalmers page: 7
- Bath Iron Works Receives $321-Million DDG 51 Contract page: 8
- NEW GHH-Constructed Drydock, Mission Bay, For Continental Maritime page: 8
- Free Brochure From Baldt Details Moor-Free™ Rapid Release System page: 8
- O'Sullivan Appointed President Of Fairbanks Morse Engine Division page: 9
- Annual CIMARE Meeting Scheduled For May 8-10 At Hyatt Hotel In Montreal page: 9
- Raytheon Establishes New Ventures Unit— Steadman Named President page: 10
- Brochure on Tensar® Geogrids Offered By Armco Construction Products page: 10
- Korobov Elected Vice President-Finance For COMSAT TeleSystems— Mutnick Named Controller page: 10
- Tano Receives Additional Coast Guard Contract Valued At $2.7 Million page: 10
- Daewoo Wins $16.5-Million Contract To Build Offshore Vessel For India page: 10
- Exclusive Rep For Danish Firm Introduces Radiotelephone System page: 10
- Mitsui Delivers Big Ore Carrier With M a n y Energy-Saving Features page: 11
- Weerts Named Senior Program Manager For American Systems page: 11
- ABS Developing New Computer Programs To Aid Ship Designers page: 11
- SNAME SPRING MEETING/ STAR SYMPOSIUM page: 12
- Smith Appointed Senior Vice President For American Steamship page: 14
- Bohme Named Product Development Manager For Simpson Timber page: 14
- Joseph Joins COMSAT As Executive Vice President page: 14
- Patti Shipyard Moves To N ew Site On Bayou Chico In Pensacola page: 15
- Illman Jones Has N e w Location And Name To Meet Growth page: 16
- Pugh A p p o i n t e d Vice President O f M a r k e t i ng For L u b r i q u i p - H o u d a i l le page: 16
- Lundberg Reappointed Director General Of INMARSAT page: 16
- Literature Available On Clemco Industries' 'Educt-O-Matic' page: 16
- Hubbard Named To Newly Created Position At American President Lines page: 16
- SNAME Introduces New Quarterly— The Journal Of Ship Production page: 16
- Cambridge Instruments Completes New Plant page: 16
- Marathon's Brownsville Yard Launches Jackup Rig For Penrod Drilling page: 17
- Big Car Carrier Delivered By Hitachi Zosen's Hiroshima Yard page: 17
- Fairbanks Morse Opens New Parts Distribution Center In Indianapolis page: 18
- Navigation & Communications Equipment — A R e v i e w— page: 18
- Southwest Marine Yard Completes Renovation Of Rowan Jackup Rig page: 19
- PIMA Agent For Three Repair Groups page: 20
- Sonat Marine Acquires Tug And Barge Unit For Petroleum Transportation page: 21
- Free Literature Available On ZF Marine Gearboxes page: 21
- WORLDWIDE SHIP REPAIR page: 22
- Gunderson Purchases FMC's Marine And Rail Equipment Division page: 31
- Bridge Named President And CEO For Volvo Penta Of America page: 31
- Elliott White Gill Thrusters Offer Unique Advantages page: 32
- Tompkins To Market BFGoodrich Bearings In Four Eastern States page: 33
- WHERE'S THE PORK BARREL? page: 34
- Los Angeles SNAME And ASNE Sections Meet In Joint Session page: 34
- Literature Available On FIRE-PREP® 2012 From Nalco Chemical page: 34
- Skantek Announces SK-401, An OCR Software Technology Breakthrough page: 34
- John Crane Offers Literature On Their Line Of Bellows Seals page: 34
- Marine coatings & corrosion control page: 36
- Flakt Offers 20-Page Brochure On Facilities And Capabilities page: 36
- Clemco Pipe Cleaning Tools Blast-Clean Pipe Interior Without Rotating The Pipe page: 39
- Hitachi Delivers Jackup Rig Built For O N G C Of India page: 39
- PRC Announces Availability Of New Family Of Mercaptan Functional Polymers page: 40
- New Boiler Cleaning Technique Offers Savings For Vessel Owners page: 45
- Gulfport Orders Second Paceco Container Crane page: 45
- Brochure Available On HF-SSB Radio Products From Harris Corporation page: 45
- Halter Marine Awarded $85-Million Navy Contract To Build Six T-AGOS Ships page: 46
- Bailey Joins Selkirk Metalbestos As Staff Engineer For Piping Line page: 46
- Zito Named Vice President- Marketing & Development Of COMSAT Technology page: 46
- No Claims Yet On Cat's Over-The-Counter Parts Availability Guarantee page: 46
- Racal Wins $2.8-Million For Marine Simulators page: 46
- McTighe Offers Brochure On High-Flow & Low-Flow Oil/Water Separators page: 46
- OSG And P&O Agree To Form Joint Venture For LPG Transportation page: 49
- New Products From Dahl Help Solve Diesel Fuel Problems In Cold Weather page: 49
- Ingalls Yard Christens First Ship With Vertical Missile Launchers page: 50
- Young Appointed Marine Operations Vice Presient For American President page: 50
- New York S N A M E Meeting Hears Paper On Preventive Maintenance page: 50
- Furness Withy Offers Folder On Group's Structure And Services page: 54
- 32-Page Bulletin From Falk Details Their Crowned Tooth Gear Couplings page: 54
- 1985 Product Catalog Available From Furuno page: 54
- Pumps & Power Ltd. Of Vancouver Signed To Represent Omnithruster page: 54
- Odense-Built Containership Sea Wolf Equipped With Bromma Telescopic Spreaders page: 59
- Ward Leonard Offers Catalog Listing Quality Controls For Defense-Maritime Applications page: 59
- Hyundai Delivers First Of Three Bulk Carriers For Norwegian Owner page: 60
- Los Angeles S N A M E Meeting Discusses Shipboard Fiber Optics page: 60
- Blount Marine Yard Delivers Dinner Cruise Vessel 'Bay Queen' page: 60