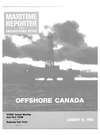
Optimizing Efficiency Levels Of Boiler Feed Turbo Pumps
The majority of steam-driven ships now in service were built in an era of low fuel oil prices, with their steam plants designed at or near maximum performance ratings. In those bygone days, operating a ship at lower horsepower was not a practical consideration. However, with the escalation of fuel oil prices during the past decade or so, the need exists for slower steaming to reduce fuel consumption as much as possible.
Derating of the boiler feed pump is a major, positive step in this direction.
The boiler feed pump is totally amenable to efficiency improvement through derating, and relatively easy to achieve (Figure 1). As about 90 percent of all steam-driven tankers and containerships employ either DEB-16 or DEB-22 Coffin® feed pumps, it is a simple matter for the installer to obtain the needed parts from the original equipment manufacturer, either directly or through a marine agent. The marine agent could also provide whatever field service that may be needed.
The less steam it takes to run the boiler feed pump, the less fuel is burned. Using a standard two-stage DEB-16 turbo pump operating at 532 hp, even a 10-percent saving effected through derating would be the equivalent of not having to run a 50-hp motor. All that the service specialist or the ship's engineer needs to know are the flow and pressure readings to begin the derating process. If, for example, the present pump steam flow is 900 gallons per minute, and 500 gpm is calculated to be an efficient level, the conversion might entail a new impeller, diffuser, diaphragm, or perhaps all of these parts.
Whenever a reduction in vessel speed is indicated, the steam plant and feed pumps operate at a lower capacity, and generally at lower efficiency.
The reduction is such that exhaust steam from the feed pump normally returned to the deaerator tank goes back to the condenser and is wasted. The amount of water a feed pump must deliver to the boiler is an approximate function of the ship's speed (Figure 2). If, for example, a 35,000-shp VLCC requires some 160 cubic meters per hour of feed water to reach a speed of 16 knots, it would take approximately 60 m3/h of feed water to attain speeds of between 10 and 11 knots.
Consequently, this capacity reduction could be even greater if derating is initiated.
It is possible to set up a curve (Figure 3) to show how effective derating can be when comparing a derated pump with an existing pump.
These curves correspond to just two of a variety of possible internal configurations that can be fitted to either the DEB-16 or DEB-22 pumps to obtain a specific performance characteristic. Such characteristics are only approximate, and are intended to show the relationship between water flow and steam consumption.
However, they also demonstrate how boiler feed pump efficiency can be improved to meet slower steaming conditions.
In terms of dollar outlay, in a typical situation where a shipowner or operator has a VLCC or ULCC fitted with a 35,000-shp power plant, operating at a reduced speed under 12 knots, a modified boiler feed pump can net an annual saving of between 0.25 and 1.0 percent in the fuel rate.
The payback period for this type of suggested modification averages about 18 months, based upon a formula calling for an assumed fuel cost of $175 per ton. In reality, the exact value of an efficiency gain depends on the type of steam cycle, and should be evaluated for each situation.
Reducing horsepower from 35,000 to 15,000 shp, the corresponding feed pump capacity of 60 m'5/h achieved would permit a saving of about 1,200 kg/h of steam—some 228 tons annually. The saving could be more or less, depending on the type steam cycle and the original internal combination fitted in the pump.
If a standard turbo boiler feed pump is being used, very likely the modification would involve replacing the impeller/diffuser combination with the associated wearing parts. These replacement parts would differ from the original equipment in that the flow passages would be designed to achieve low flows with higher efficiency.
In a situation where the derating work calls for a major reduction in performance, the discharge head and associated diaphragm would undoubtedly need to be changed.
Still, it would not be necessary to disconnect any of the piping to make external changes.
Whatever the modifications, the internals must maintain the highest optimum turbine speed for best results.
One or both nozzle plates in the turbine should be replaced and, therefore, the most energy can be extracted for the available steam.
It is entirely feasible to perform all derating modifications within a day or two. The changes are also reversible; if a return to full steam capacity is desired at some point, the original parts can easily be retrieved from on-board storage. They can also be retained for emergency use and as replacement equipment.
Marine agents are available on short notice to handle derating conversions throughout the world.
Recirculation management is another means of effecting savings. To aid preventive maintenance, the recirculation system should be checked routinely for the following: system opened too early, system that is always open, leaking valves, and oversized orifices (caused by wear or excessive sizing in the original design).
There are other advantages to derating. At all reduced volume flows, the differential pressure system requires the least power and provides the boiler feed pump with the following: lowest rpm; lowest part stress levels; lowest NPSH required, providing additional NPSH margins; lowest recirculation rate required and less wear for the orifice parts; and lowest noise level.
Over the years, the boiler feed pump aboard ship has been a reliable performer. Even so, fuel oil prices are likely to remain high for some time to come, so any means at hand to improve the efficiency of fuel-consuming systems is a plus. By derating boiler feed pumps, shipowners and operators have an exceptional opportunity to boost efficiency, save on fuel, and reduce costly maintenance.
For full literature and complete information on FMC Coffin boiler feed pumps, Circle 24 on Reader Service Card
Read Optimizing Efficiency Levels Of Boiler Feed Turbo Pumps in Pdf, Flash or Html5 edition of January 15, 1986 Maritime Reporter
Other stories from January 15, 1986 issue
Content
- Bay Shipbuilding Expands Foreign Trade Zone page: 5
- Gladding-Hearn Shipbuilding To Build Large, Fast Passenger Catamarans On The East Coast page: 6
- Free Literature Describes New Repair Compounds From Philadelphia Resins page: 6
- ODECO Elects Kilpatrick Executive Vice President page: 6
- Combustion Engineering A w a r d e d $12 Million In Navy Boiler Contracts page: 7
- Huthnance Consolidates Management Of Nine Offshore Drilling Rigs page: 7
- Hagglunds Offers Elaborate 72-Page Full-Color Booklet On Cranes And Equipment page: 7
- Navy Ends Suspension; Tracor, Inc., Resumes Government Contracting page: 8
- ' 85 Sales Of Imperial Survival Suits Nears 100,000 page: 8
- Aalborg Yard Launches Third Reefer For Delivery To USSR's Sudoimport page: 8
- 38th Annual CSSRA Conference And First Canadian Shipbuilding & Offshore Exhibition page: 12
- $5-Billion Hibernia Offshore Project Will Get Under Way Early This Year page: 13
- Major Manufacturers Attend First Diesel Propulsion Conference Held In Seat page: 14
- Roger Nejes Appointed Assistant To President, Todd Shipyards Corp. page: 14
- Armco Continues To Upgrade Speciality Steels Facilities page: 14
- Westport Yard Building Fiberglass Passenger Vessel For TravAlaska page: 15
- Simrad, Inc. Opens U.S. East Coast Branch Office page: 15
- Balehi Marine Christens Twin-Screw Harbor Utility Boat page: 16
- Fast Sealift Ship USNS Altair Dedicated At Avondale Industries Shipyard Division page: 16
- Fincantieri Completes Major Overhauls On Two RO/RO-Containerships page: 17
- Shelley To Succeed Holmes As President Of Raytheon page: 17
- Ingersoll-Rand Purchases Fafnir Bearing Division page: 17
- McDermott Gets $48-Million Offshore Contract From Chinese Petroleum Corporation page: 18
- Pool Arctic Alaska Orders Bardex Hydranautics Island Rig Skidding System page: 18
- Bay Shipbuilding Lays Keel For Second Of Three Containerships page: 18
- Omnithrusters Delivered For Canadian Government Vessels page: 18
- Ingram Barge Completes Organization Changes— Reports Rapid G r o w th page: 19
- Optimizing Efficiency Levels Of Boiler Feed Turbo Pumps page: 20
- Russellstoll Offers Full-Color Bulletin On Heliport Lighting System page: 20
- Nichols Brothers Delivering Catamaran To Glacier Bay Yachts page: 21
- Simultaneous Drydocking Requires Separation Of 70,000-Ton Drydock At Penn Ship page: 21
- REDUCING FUEL COSTS page: 24
- BP Offers 60-Page Brochure On Facilities/Capabilities page: 28
- Farboil Offers Two Free Directories On Marine Coatings and Systems page: 28
- Todd Galveston Awarded $21.6-Million Modification Of Second T-AVB Vessel page: 28
- PNOC Marine And Bardex Hydranautics Build World Class Shipyard page: 29
- Gems Sensors Expands Line Of Level Indicators page: 29
- White Named Senior Vice President At American Systems Engineering page: 29
- Karl Senner Offers Sales And Service For Reintjes Marine Gears page: 30
- DDA Offers Expanded Product Line And Streamlined Manufacturing Facilities page: 30
- Steamship Company Chief Given Top Federal Academy Alumni A w a rd page: 31
- New Marine Overcoat Sea-Slide™ Increases Speed, Saves Fuel page: 31
- Valley Line Reorganizes And Expands Marketing Department— Three N e w Executives Join Firm page: 31
- First Lucander-Designed Tug Nozzle Built By ideal Machine page: 31
- American Metal Bearing's Rubber Bearing Staves Approved By Navy page: 32
- Brochure Explains N e w USCG Survival Suit Regulations page: 32
- Saab Electronics Introduces TankRadar page: 33
- Alden Electronics Introduces Tactical Facsimile Receiver page: 33
- Furuno Introduces Digitized Small Radar page: 33
- Offshore Triple-Effect Water Makers From Atlas-Danmark Save Thousands In Operating Expenses page: 34
- Acoustical Barrier Material Data Sheet Available page: 34
- Robertshaw Literature Describes Versatile Diaphragm Actuators page: 34
- Gladding-Hearn Delivers Two Tugs To Bermuda's Department Of Marine page: 34
- Belgian Shipbuilder "Floats7 Massive GRP Mold On Film Of Air page: 36
- Navigation Sciences Offers VIEWNAV® Master Mariner Brochure page: 36
- Bailey Offers N e w Color Brochure On Recorders And Data Loggers page: 36
- Cummins Uprates B Series Marine Diesel Engines page: 38
- Titeflex Offers 22-Page Catalog On Smooth Bore Teflon Hose page: 38
- Cincinnati Gear Offers Free Color Brochure On Large Gears And Parts page: 38
- Baldt Offers New 12-Page Full-Color Facilities Brochure page: 38
- N e w Compact Thermocoil Diesel Fuel Heater From Racor page: 43