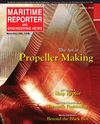
The Ballast Water Management Conundrum
U.S. System Approvals are Key; Detailed Pre-Planning Urged
Ten years on, there’s little certain about ballast water management regulations that the industry can chart a course around other than that it will be expensive – possibly the most costly marine retrofit to date. With install estimates running from $500,000 to as much as $5 million per vessel, across some 68,000 commercial ships estimated by the IMO to transfer 7 billion tons of ballast water annually – industry players say we could be looking at as much as an $80 billion market. Eventually, that is, because there is not a lot of activity right now.
That’s because much of the industry is waiting for the International Marine Organization (IMO)’s regulations to finally come into force, which by most estimates will happen in 2016, a year from whenever the widely anticipated final ratification of the IMO ballast water convention occurs sometime this year.
But no one really knows when ratification will take place. Or when the United States Coast Guard (USCG) will start announcing system approvals. Or when more vendors will step up to the plate and submit their products and data to the USCG’s two independent test labs. Or when the IMO will finish its recently agreed to review of the G8 testing protocols. Or whether suppliers and shipyards will be able to meet pent up demand down the road. And on and on.
In the face of so many unknowns it’s hard for ship owners to justify taking the BWMS plunge as the irresolution of so many issues has left every option fraught with risk.
“The owners just don’t want to take a substantial cap-X decision since the regulations are still vague and the technology is not proven,” shrugs an executive at global tanker company.
And so at the start of of 2015, well after the passage of the initial 2013 compliance deadlines, and almost two decades after the IMO first started to look at the issue, frustration is as widespread among the owners as their coping strategies are wide ranging.
Tragedy of BW Regulations
“This legislation was pushed before the technology was ready, and it has led to a massive amount of uncertainty and a massive financial burden on the industry,” said Graham Westgarth, COO of GasLog Logistics, Ltd., and a former chairman of Intertanko. “When you look at the amount of money that must be spent on this, it’s really something of a tragedy. [Ship owners] run the risk of spending billions on equipment that doesn’t fulfill the purpose for which it was intended.”
And, to put it simply, nobody wants to do that.
“The market has changed, or correctly said, slowed down considerably. We have not been approached by any supplier during this [past] year,” said Kjell Gestranius, Bore Ltd.’s technical manager.
The reverse is also at work. Although Bore had installed Hyde Marine’s Guardian BWMS in two ships, the Bore Sea and Bore Song, “there remain seven ships, where we have done pre-studies and have some idea of what to do,” said Gestranius. “We had a few candidates, where we [have] decided to go further, if the regulation comes into force. But, this has also been put [on hold], waiting for what will happen.”
Many owners and operators are just not installing anything if they can help it. The global tanker company has put all BWMS on hold, outside of new build contracts it has taken over that already included treatment systems. “As a supplier, you could not pay us enough to take the risk that you’ll be obsolete in a couple of years, so no deal,” said the company executive, who asked not to be named.
For those owners who prefer to wait, Kathy Metcalfe, director of maritime affairs for the American Council on Shipping (ACS), is advising members to seek extensions from the Coast Guard. To date, it has issued 340 such waivers to vessels scheduled for dry docking in 2014 and 2015, says CMDR Ryan Allain, who is the chief of the Coast Guard’s Environmental Standards Division.
Maersk Covers Its Bases
Not doing anything, however, is impractical for some companies, such as shipping conglomerate Maersk Group, which is taking a mixed, measured approach to ballast water management. “What we are concerned about is U.S. Coast Guard approval. Our strategy is to install in new buildings with systems where we have a commitment from the supplier that they expect to obtain U.S. Coast Guard approval, and a commitment to ensure that they will,” said Palle Wredstrom, department head of Maersk Maritime Technology. The company has so far installed UV technology-based BWMS on about 30 ships – all new builds.
That strategy echoes the strongest piece of advice (see sidebar on page 37) that shipyards, classification societies and even the U.S. Coast Guard are giving owner/operators: Make sure vendors guarantee their products will meet USCG standards and revised G8 testing protocols, and negotiate up front who will pay for this retrofit of the retrofit, if it comes to that.
Maersk is taking a different tact with its existing fleet, which includes 260 container vessels, 160 tankers and 60 supply ships. The company has said it expects to invest more than $600M to meet the new requirements over time. One thing Maersk learned from installing on new builds is that the process is challenging. “It’s even more challenging to install ballast water management systems on board older ships,” said Wredstrom, who adds that the company is going to wait for the renewal survey and the safety of dry dock before installing BWMS on its existing fleet.
Similarity GasLog will probably have five or six ships in dry dock this year. “I’d very much like to install a system that the Coast Guard approved. I think most ship owners think if you can’t trade with the U.S., you’re devalued to a degree,” said Westgarth, adding one thing he could do is get an extension until such time as the Coast Guard approves a system.
He could also opt to install a Coast Guard–approved AMS, or Alternative Management System, good for 5 years – but like many of his peers, he is wary of “paying $2 million for a system and having to write it off over five years, versus the lifetime of the ship.”
But he says there is a high probability that GasLog will install something when its ships dock.
Interest in waiting for scheduled dry dock dates before retrofitting is so widespread that Frost & Sullivan lists as a key industry challenge, “persuading ship owners to purchase ballast water treatment systems, especially for retrofits.”
U.S. Type Approval: The Gold Standard
That’s not likely to happen while everyone waits for the implied safety of U.S. –approved systems to buy. “Ship owners are reticent to fit a system that won’t be able to operate in the U.S.; they are all hanging on, waiting for U.S type-approved systems. Ships are generally designed for worldwide trade; we’re not asking for anything special, just systems that will operate in our normal sphere,” said Jonathan Spremulli, technical director of International Chamber of Shipping (ICS), which claims to represent 80% of the world’s fleet.
Toward that end, the ICS, and its brethren, including Intertanko, Bimco and the American Chamber of Shipping (ACS), succeeded last fall in winning agreement from the IMO to strengthen its G8 testing protocols. This is important because although ships in global trade operate in a wide range of conditions, the G8 protocol doesn’t require testing in all those situations. For ex., the G8 only requires testing to two levels of salinity, yet global shippers operate across three levels, as well as in a range of temperatures. “This means you could have a system not verified to operate in all of the water conditions in terms of salinity that you’d expect a worldwide ship to encounter over its lifetime,” exclaims Spremulli.
And that’s the big worry.
There’s a reason for the U.S. Coast Guard to set up their own rules for approval, said Maerk’s Wredstrom. “I’m sure if a supplier fullfills U.S.Coast Guard approval – which is more stringent than the G8 protocls – then we are sure it does work under most of the conditions.” And it will, according to CMDR Allain.
“I would say the U.S. Coast Guard requirements are consistent with the G8 protocols, but more stringent and with less room for interpretation. Whenever you have guidelines, there is room for interpretation. When you have multiple countries reviewing multiple systems to the guidelines you are going to have multiple variations on how certain aspects of those guidelines are interpreted. Here [the U.S.] you have regulations and one entity reviewing. It’s going to be very consistent,” promises the Coast Guard Commander.
That’s what the industry is counting on. “If we install a $2M system per ship, we expect it to meet the demands of the IMO and U.S. Coast Guard. If you buy a car that fullfills all the requirements for emmissions, you would not expect to have to have extra equipment to montior this. If we invest this kind of money, we expect that when the system got all those approvals, that it will live up to the convention,” said Maersk’s Wredstrom.
And yet the skepticism about whether existing G8-tested systems will indeed live up to the IMO convention is such that some ship owners are convinced that there are no working, or trustworthy, systems on the market today. This is reflected in the decision by some outfits to take delivery of new builds with no BWMS – just space reserved for a future installation.
“The existing technology is not fit for purpose,” according to GasLog’s Westgarth.
The Waiting Game Continues
Still, ship owners know that invasive organisms must be stopped, and they are anxious to cross compliance off their regulatory to-do list. But the already interminable waiting period is about to get longer. Despite the much bandied about estimate that the U.S. Coast Guard will start issuing approved systems by mid-2015, the reality, says the man who should know, is it will probably be mid- to late 2016 before that happens.
The reason, says Thomas Stevens, technical manager at NSF International, one of two independent labs contracted by the Coast Guard to test BWMS for U.S. compliance, is that system testing requires a minimum of 18 months to two years (and at a cost of $1M to $2M to the vendors, according to some estimates.) Once the testing is done, the labs have to package up the results for delivery to the Coast Guard, which will then review the data before issuing approvals. And depending on how much time is involved, that could push the availability of U.S. approved systems into an industry patience busting 2017.
Worse, there are only 10-12 products in the testing cycle, according to Stevens, USCG CMDR Allain and Intertanko, which actually surveyed vendors on their plans for obtaining U.S. approval.
Don’t Look at Us
“People are not waiting for the Coast Guard; our regulations came out in 2012. What they are waiting for is for the vendors to get system type approval from the Coast Guard. The onus is on the vendors to complete . . . the process,’’ said Allain. Trojan Marinex, a maker of UV systems, and one of three vendors chosen to partner with Damen shipyards, says it tested from the start to meet U.S. requirements and believes it is one of three products that have completed testing at DNV GL, the other independent testing lab. “The balance of the other seven to nine are in the early stages and need to complete both land and ship-based testing, will take them well into 2016,” said Jim Cosman, market manager for the company. “The Coast Guard has said it can review test results in as little as 30 days,” he adds, predicting that his company’s products will receive USCG approval at the latest by second quarter this year.
The Perils of Pent-Up Demand
2016 approval dates are not what ship owners and operators are going to want to hear. The longer pent-up demand builds, the more concern there is that overwhelmed vendors and overbooked shipyards could force vessels into waiting queues, screwing with scheduled dry docking dates, creating a backlog situation and increasing the amount of time a ship is offline.
Like other shipowners, Maersk recognizes the issue. The challenge for ballast water is from the existing fleet, says Wredstrom. “We see 60,000 ships needing to be compliant in the next five years.”
The Maersk Group was so concerned about the possibility of a backlog, that in 2009, back when the convention was expected to be ratified quickly in the face of a handful of system managment suppliers, it invested in a joint venture with Skjølstrup & Grønborg ApS and the Desmi Group to develop and help test ballast water treatment systems. Fast forward five years into a more robust market and Maersk no longer feels the need for its system “insurance.”
“DESMI Ocean is not part of Maersk any more. The reason for the investment was that we were very concerned about suppliers, as the demand was far bigger than the number of suppliers, but today I think the numbers may be sufficient,” said Wredstrom. Today there are 51 IMO-approved suppliers that “hopefully” will all have U.S. Coast Guard approval, he adds. “I expect that they have done their calculations” and are prepared to meet demand.
And should bottlenecks turn up with suppliers or the shipyards, CMDR Allain notes that those situations qualify for Coast Guard extenions.
From Maersk’s point of view, the bigger issue is the extension of time a ship will need in drydock when it goes in for its renewal survey and mandated BWMS retrofit. “Without a doubt, [the retrofits] will extend the time needed. There might be increased demand for years.”
And not just on the ship yards. “It will demand a lot from the whole supply chain. The classification societies need to approve all installations. These things have to be tested to make sure they actually work. We’ve seen on a new build how it can be a challenge to integrate the [system] into the ship’s control system. I have to imagine it will be an even bigger challenge on a retrofit,” Wredstrom said.
“So to ensure that all systems work to expectations, and the training of the crew post installation, it would be beneficial to all to extend the time involved, ’’ he adds, echoing a growing push among ship owners and operators to get the IMO to once again push out compliance dates.
Shipyards Gearing Up
Shipyards too are worried about the time involved in retrofitting BWMS, particularly during scheduled dry docks, which typically run two weeks. Ship owners who want to stick to that schedule will need to start preparing 10 to 12 months in advance of a vessel’s dry dock date, warns Gert-Jan Oude Egberink, manager, ballast water treatment, Damen Shipyards. “Later is too late.”
“A lot of ship owners are just looking at the cost of the treatment system. There’s also a high cost involved in engineering and installing the system. Sign off of integration, drawings and plan by class can worst case take several weeks.”
“You need to do pre-fabrication, engineering, and testing has to be prepared. If you don’t time it right, you’ll have to stay in dry dock longer,” he warns. “The pressure will be on the owners once the convention is in force. The IMO says they have to be compliant after the renewal survey, so they can only sail away when the system is installed.”
Egberink agrees with Wredstrom that owners who do not plan ahead may run into backlogs in other areas, such as finding people to do the pre-engineering work and scheduling class societies to review their designs.
In fact, choosing a technology and a vendor specific to the needs of each vessel’s type, characteristics and operating zone, requires a great deal of advance work. All these ship owners who are sitting tight should be working their way through the necessary and time-consuming prep work in advance of eventual retrofits. Damen, and others, can organize and oversee the entire process if needed.
Maersk, Bore and GasLog have all done the legwork needed to put together a short list of suppliers and technologies that they can focus on once they do decide to move ahead with retrofits. In the case of Maersk, another strategic decision has been to focus on bigger suppliers. “It’s mainly because of worldwide service, and without a doubt, there will be a huge demand for support based on our experience from new build installations. It’s an even higher challenge on retrofits,” says Wredstrom.
As a practical matter, Maerk will spread its retrofit work around. “We have a huge fleet; these ships will drydock at different yards.” Gaslog is looking at Samsung and Hyundai.
Scheduling yard time will be easier for companies in the liner trade, where it’s possible to have an idea of the position of the ship out in the future. In the tramp trade, where you don’t have the benefit of predictability of where a ship will be, it creates more of a scramble to find drydock space. “The single biggest avoidable cost of dry docking is the amount of time the ship is steaming without cargo, so the position of the yard in relation to the position of your ship is quite important,” according to the tanker company executive.
All three shipping companies expect ship and repair yards to pitch their own solutions – and all seem open to at least discussing those options, recognizing that shipyards can’t possibly be expert in a large number of specific systems, including systems they are leaning toward.
Partnering with Clients and Suppliers
As for the shipyards, there is of course money to be made in retrofit work. But there is more money to be made in both allying themselves with vendor partners and in guiding clients through the heavily detail-oriented pre-planning and design work, lining up needed expertise to handle specific parts of the job.
Damen has partnered with three vendors across several technologies in order to “cover the whole range of vessels’ and provide flexibility in choice. It also enables the ship yard to build expertise with specific systems. “To be efficient and cost-effective, we need to specialize,” says Egberink.
The partnerships also enable Damen to do product development. For example, when it saw the need for a smaller flow rate capacity in the market, it worked with partner Bio-UV to develop “a small flow rate plug-and-play system.”
Separately, Damen has developed a fourth option it calls InvaSave - a mobile, self-contained ballast water Discharge Technology that it is marketing as an alternative or emergency measure. It is targeted at older vessels where owners do not want to install a retrofit, waste water collectors and barges, and port-states for emergency use.
“Say a ship owner has installed a system but it malfunctions in port. What will they do then? They’ll have to wait, at a very high cost. There needs to be a service provided in port to deal with this,” says Damen’s Egberink.
Retrofits can prove particularly challenging to older vessels, and it is expected that the cost involved laid against the lifespan and value of an older vessel may in some cases lead to either early scrapping or force owners into alternative strategies, for example offloading ballast to a third party or using a portable treatmenert system on deck, such as Damen’s InvaSave containerized technology.
The advantage with InvaSave is owners can put it on top of the deck and when the vessel is at the end of its life, it can be removed and placed on another ship, keeping its economic value versuss losing the investment in an expensive retrofit.
On the client project management side, Damen is offering Global One Stop Ballast Water Treatment Retrofit Service, which provides project management, consulting, design and engineering services. The shipyard is suggesting that owners can avoid supply problems in a booming market by signing on to its turnkey package of services.
All the uncertainty surrounding ballast water management compliance aside, there is one certainly after all. Ship owners and operators who plan ahead for their retrofits, doing the due diligence to fit the right system to their vessels, and who snag guarantees of U.S. test approvals, stand the best chance of serving both the environment and their bottom lines well.
(As published in the January 2015 edition of Maritime Reporter & Engineering News - http://magazines.marinelink.com/Magazines/MaritimeReporter)
Read The Ballast Water Management Conundrum in Pdf, Flash or Html5 edition of January 2015 Maritime Reporter
Other stories from January 2015 issue
Content
- Editorial: BWTS. Like it or Not, Here it Comes page: 6
- Marine Casualties & Fast Ferry Follies page: 8
- Bayonne Drydock Logs Successful '14 page: 10
- N-KOM Sees Increased Tanker Business page: 10
- Limitless Salvage page: 12
- What Keeps ‘Good Ship’ RINA Buoyant page: 20
- Dynamic Positioning & the Potential for USCG Regulations page: 24
- Chemical Tanker Turned OSV page: 26
- Shipbuilding, Repair and Conversion: Brazil's Quick Fix page: 30
- The Ballast Water Management Conundrum page: 34
- The Art of Propeller Making page: 44
- Lindner Sees Strong 2015 page: 48
- Beyond the Black Box page: 50
- BICERA Explosion Relief Valve page: 53
- Transas: The Bridge to Tomorrow page: 54
- Volvo Penta Debuts New Marine Engines page: 56
- VapCor Introduces Lindemann Marine Products page: 56
- New YANMAR EPA Tier III Engine page: 56
- New Gasket from Victaulic page: 56
- Clean Seal Molded Specialties Launched page: 56
- Dometic Debuts New Product Line page: 56
- First Container for LNG Hybrid Barge page: 56
- Wärtsilä to Power LNG-fueled RoPax Ferry page: 56
- Kidde Fire Systems: Multi-Language ARIES NETLink page: 56
- Next Generation Bridge Concept page: 57
- BCG Delivers Training Upgrades page: 58
- RescueME MOB1 page: 58
- New Stereo from ASA Electronics page: 58