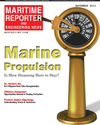
ReFRESCO: Understanding & Designing Energy Saving Devices
Using Computational Fluid Dynamics (CFD), new insights can be obtained into the working principles of Energy Saving Devices (ESDs), which all serve to increase the fuel efficiency of a ship. The advantages of using ReFRESCO to study ESDs are explored in this article. The capability of simulating different moving objects, and their interaction in on calculation (applying the so-called Sliding Interfaces Technique) has increased the range of applications of the viscousflow CFD code ReFRESCO. The new Sliding Interfaces Technique enables MARIN to study and reveal the oldest and perhaps the greatest mystery in the world of maritime propulsion: the reduction in fuel consumption when applying an ESD.
A Short Introduction to ESDs
The idea of saving energy by placing a device in front of the propeller was already published in 1949 by Van Lammeren, but the first commercial ESD was probably the Mitsui Integrated Duct Propeller (MIDP) introduced in 1980. Although the working principles responsible for the energy saving were not completely understood, in a world controlled by the second oil crisis, the MIDP was a great success. Shortly after, many other companies came with their own ESD designs. After the 80s, as the world economy recovered and oil prices dropped, interest in ESDs diminished. However, with the current challenging world economy, increasing oil prices and the upcoming new EEDI regulations, an ESD giving a possible 5% power savings gain becomes attractive to many ship owners.
Advantages of CFD
By using CFD, there is now the possibility to observe the effects of an ESD in a level of detail which is impossible when using only model tests (Figure 1). Another advantage of CFD is that the evaluation of many design variations, with small geometrical changes, is more cost efficient compared to model testing. Perhaps the greatest benefit of CFD is the possibility to evaluate the ESDs at full-scale Reynolds number. The performance of an ESD optimized during model tests can be severely reduced at full scale. It has often proven difficult to measure the large gains in efficiency that were found in the model tests during the sea trial. Since the possible gains of ESDs are in the order of 5%, CFD simulations have to be very accurate. To obtain accurate results, a fully verified and validated CFD code for ship and propeller flows, such as ReFRESCO [1] is a must.
Even with an accurate CFD code, achieving good quality results is challenging because the complex interactions between the propeller, hull and ESD make the CFD simulations extremely intricate. The geometries are complicated and care has to be taken when making simplifications and the quality of a computational grid has an important influence on the accuracy of a CFD calculation. Recent developments at MARIN facilitate the generation of high quality structured grids for propellers, without making concessions to the propeller geometry (see Figure 2). This results in a better iterative convergence and improves the accuracy of the calculation.
Additionally, time consuming unsteady calculations are needed to capture all interaction effects. This is only possible with the combined use of our in-house CFD code ReFRESCO (requiring no license fee) and our HPC clusters (maximum of 2,000 cores.)
MARIN participates in the European Union project Green Retrofitting through Improved Propulsion (GRIP). One of the main pillars of the project is to identify working principles of ESDs. Once working principles have been identified, new concept designs can be made, for example, the BSD concept design presented in Figure 3 and [2].
MARIN will continue to study and design ESDs in order to fully understand their underlying principles to enable it to give independent advice to clients on ESD performance predictions. In terms of CFD, accuracy (by decreasing the numerical uncertainties and by using finer turbulence models) and performance (by decreasing computational times) are the major areas of focus for the coming years.
[1] RIJPKEMA, D. and VAZ, G., “Viscous Flow Computations on Propulsors: Verification, Validation and Scale Effects,” In Proc. Of Developments in Marine CFD, London, UK, March 2011
[2] SCHUILING, B. “The Design and Numerical Demonstrations of a New Energy Saving Device,” NUTTS, September 2013.
Bart Schuiling is a researcher at the R&D department of MARIN. e: [email protected]
(As published in the November 2013 edition of Maritime Reporter & Engineering News - www.marinelink.com)
Read ReFRESCO: Understanding & Designing Energy Saving Devices in Pdf, Flash or Html5 edition of November 2013 Maritime Reporter
Other stories from November 2013 issue
Content
- Interview: Dr. Herbert Aly page: 12
- Knowledge is Power page: 16
- ReFRESCO: Understanding & Designing Energy Saving Devices page: 18
- Nontank VRP Regs page: 20
- The Magic Ingredients of a Healthy Safety Culture page: 24
- e-Compliance: Revolutionizing the Efficiency of Compliance for Maritime Regs page: 28
- Pull the Handle Down... page: 30
- Return of the Electric Boat page: 38
- Fast Ferry Gets a New Power Package page: 42
- Cat tackles Tier 3 and Tier 4; Completes Berg Deal page: 44
- Konrad, Cummins Propulsion Package Partnership page: 46
- Scania 13L Inline; 16L V8 for EPA Tier 3 page: 48
- The Switch: New Drive Train Tech page: 48
- John Deere Tier 3 Engine Line Up page: 49
- GE Power Conversion page: 49
- EPA’s Vessel General Permit (VGP) & You page: 50
- Are PAGS the Answer? page: 51
- Don’t Forget: Seawater is a Free EAL page: 51
- Lukoil: Cylinder Oil to Reduce Wear, Consumption page: 52
- Agip Rebrands as Eni Powers Ahead in North America page: 52
- Floating Production Systems: Market Update page: 54
- Offshore Brazil: The Libra Field & Brazil’s Pre-Salt Policy page: 56
- On Ballast Water, Time is Running Out page: 60
- Standardization for Safer Shipping of e-Navigation & Training page: 62
- Apprenticeship Training & Academic Degree: The Pathway to Success page: 64
- The Drawing Board: Innovative OSV Design from the Ground up page: 68
- Product Tanker Hijackings page: 72
- The Trinidad & Tobago Maritime Sector page: 74
- Seatorque Boost for Brazil’s Biggest Superyacht page: 76
- Raytheon Anschütz Launches New Gyro Compass page: 85
- Emsys Upgraded to Measure Mass Emissions Rates page: 85
- Thuraya SatSleeve Transforms iPhone into Satellite Phone page: 85
- Kongsberg Debuts New Drilling Rig and Ship Simulator page: 85
- Martek: “BNWAS Password Protection is Essential” page: 85
- Northrop Grumman Radars for USN page: 85
- Imtech Debuts SeaPilot 76 page: 85
- FORAN in Indonesia page: 85
- Raymarine Autopilot page: 86
- Computer Gaming & Maritime Training page: 86
- Jeppesen Updates VVOS Software page: 86
- Harris CapRock & Carnival Sign Contract page: 86
- Carlisle & Finch SmartVIEW Technology page: 86
- Thomas Gunn Unveils New Digital Chart Management System page: 86
- CM-1000 Series: Smart Fluid Handling Tech page: 87
- Paperless Navigation page: 87
- TNKC Fleet & BASS Software page: 87
- Cobham Touchscreen Navtex page: 87
- GE Dynamic Positioning System page: 87
- Ecospeed Fuel Savings Calculator page: 87
- Boatracs’ BTConnect AIS page: 87
- New Brakes from Wichita Clutch page: 88
- Home Study Programs page: 88
- New PowerShark Tool Eats through Biofouling page: 88
- VIKING Expands Training page: 88
- SUPREME Athmos Zero-Pollution Seal page: 88
- New Inertia-Engaged Turbine Air Starter page: 88