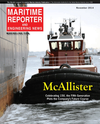
Floating Production: Huge Opportunity for Shipyards, Manufacturers
Floating production has been one of the most significant achievements in the upstream oil and gas industry over the past four decades. The ability to produce in deepwater has opened a new frontier in oil and gas development – and has generated a huge business base for suppliers of floating production systems
Types of Floating Production Systems
There are two basic types of floating production systems: oil/gas production units and LNG/gas processing units. Common to both is the use of a floating facility to support an oil and/or gas processing plant to monetize oil and/or gas deposits.
• Floating oil/gas production systems: These production systems are positioned on offshore fields and used to produce oil and gas contained in subsea reservoirs. Fluids and gas in the subsea reservoir are conveyed from the wellhead to the production unit via flowlines, manifolds and risers. Specialized equipment mounted on the production unit and/or on the seabed is used to control well operations. Umbilicals connecting the production unit and well are used to monitor the well and power subsea systems. Production floaters come in a variety of shapes, sizes and productive capability. Some are shipshape (FPSOs), some rectangular (Production Semis, TLPs, Barges), some cylindrical (Spars, a few FPSOs). Storage capability is built into some units, others directly export produced fluids to shore via pipeline. Production capability ranges from
• Floating LNG/gas processing units: These systems are used in the natural gas supply chain as LNG production or receiving/regasification facilities. They enable methane to be monetized when a land-based liquefaction plant is commercially infeasible and provide an attractive option to a land-based receiving/regasification terminal. FLNGs are designed to be positioned on gas fields offshore or at coastal locations near an onshore gas field. The production unit is fitted with cryogenic systems needed to transform natural gas to liquid form for ocean transport. They also have storage capability and can offload liquefied gas to LNG transport carriers. FSRUs are positioned in locations that require gas delivery. They are designed to receive LNG from transport carriers, store the product in cryogenic tanks and transform LNG back to gaseous state for delivery to consumers. The unit can be moored offshore with subsea pipeline connection to shore. Or it can be moored in port alongside a specially equipped jetty. There are currently 30 floating LNG/gas processing units in service or on order – 5 FLNGs and 25 FSRUs. All of the FLNGs are still on order. 13 of the FSRUs are in service, 12 on order.
(See Chart 1)
Four Decades of Industry Expansion
The history of floating production is short – only four decades. It dates from 40 years ago when Hamilton Brothers (now BHP) converted the semisubmersible drill rig Transworld 58 to the Argyll production semi and used the unit for ten years as a production facility in the UK North Sea. This was quickly followed by Shell, who in 1977 converted a tanker to the Castellon FPSO and used the unit for ten years as a production facility offshore Spain. Growth since the mid-1970s has been impressive, with the number of units in service steadily increasing. It took the first ten years to reach 15 units in operation. By the end of the second decade there were just over 50 units in operation. At the end of the third decade the number had grown to around 170 units in service. By the end of the fourth decade, at end 2015, the number will be around 310 units. There has not been a year in which the number of units in service declined – new deliveries have consistently exceeded the number of units decommissioned in the year.
(See Chart 2)
Where Systems are Being Built
East Asia is clearly the leading location for building production floaters. More than 35 production or storage units are under construction in Korea, China and Japan. Several huge projects are among the orders, including a massive FLNG being built in Korea.
South Asia is the dominant location for conversion of tankers into production and storage floaters. There are more than 15 conversion projects in progress in Singapore and Malaysia.
Brazil has increasingly become a major player in building production floaters. The topsides for more than 15 FPSOs are being fully or partially assembled and integrated in Brazilian facilities. Construction of 8 standardized FPSO hulls is also underway in a Brazilian shipyard, though some of the fabrication has been subcontracted in China.
Around 70% of the floating production systems now on order are destined for four major locations. 26% of the units on order are to be installed offshore Brazil, 19% off Northern Europe, 14% in SE Asia and 10% off West Africa.
Six units on order are being built on speculation and do not have an installation contract.
In the Planning Stage
There are currently more than 230 projects in the planning stage that will likely require a floating production system. Almost 80% of these projects are in five major regions -- West Africa, Brazil, Southeast Asia, Gulf of Mexico and Northern Europe.
Of the total planned projects, 28% are in water depth exceeding 1500 meters, 14% in 1000-1500 meters and 58% in water depth less than 1000 meters. Brazil, Africa and the Gulf of Mexico account for 90% of the ultra-deepwater projects in the planning stage.
(See Chart 3)
New Report: Outlook for Orders
We have just completed a study of floating production system requirements through 2019. Depending on the underlying market conditions, we are forecasting orders for 105 to 146 floating production systems over the next five years, with a contract value in the range of $112 to $150 billion. FPSO construction and conversion will account for around 67% of the total expenditure. The balance will be in orders for other type oil/gas production floaters, floating liquefaction plants, LNG regasification units and storage/offloading vessels. Full details are provided in Analysis of Future Business Drivers and Forecast of Floating Production System Orders Between 2015-2019, a new 150-page report completed in October 2014. Find more information and ordering details at:
www.worldenergyreports.com
(As published in the November 2014 edition of Maritime Reporter & Engineering News - http://magazines.marinelink.com/Magazines/MaritimeReporter)
Other stories from November 2014 issue
Content
- Editorial: 75, 150 ... What’s in a Number? page: 6
- Is Glycerine the Next Marine Fuel? page: 16
- The Legal Consequences of 46 CFR Subchapter “M” page: 20
- Avoiding the Edges of the Sea page: 22
- Will Congress Pass Any Maritime Legislation in 2014? page: 26
- World’s Largest Containership First Tested at MARIN page: 30
- What’s All the Noise at IMO? page: 34
- From Security to Efficiency Modern Vessel Tracking page: 40
- Marine Insurance & the “Human Factor” page: 44
- Subsea Defense & the Changing Paradigm of Submarine Programs page: 48
- ZF Geared up for a Commerical Maritime Push page: 52
- Interview: Matthew Paxton, President, Shipbuilders Council Of America page: 58
- Offshore: Ulstein and the First U.S. Built X-Bow page: 66
- OilCraft’s TwinBow Challenge page: 74
- The McAllister Towing Legacy page: 76
- Denet Towing Repower Saves 20% in Fuel page: 92
- Eltorque Pushes into US Market page: 93
- AHTS Proves Strength on (in & through) Ice page: 94
- Kleven Orderbook Pumped up to $1.8b page: 96
- Z-Drive Use Spreads on US Inland Waterways page: 96
- Floating Production: Huge Opportunity for Shipyards, Manufacturers page: 98
- Special Vessels “Built by Flensburger” page: 100
- Danish Maritime Takes Center Stage page: 104
- Safety is Job One page: 110
- Focus: Heavy Duty Lifting page: 114
- Lifting Costa Concordia page: 118
- RV Sikuliaq: Modern Electric Propulsion & Power Management page: 122
- Talking Turbines with Bolsinger, VP at GE Marine page: 134
- DSME Returns for More Dual-Fuel Engines page: 138
- Volvo Penta Triple IPS and DP for New Fast Response Boat page: 138
- New Propulsion Couplings from Renold Hi-Tec page: 139
- Cummins Auxiliaries for New OSV page: 139
- Tier III Marine Power: Genset with SCR page: 140
- New Generation of Turbochargers page: 141
- Class Approval for Wärtsilä Steerable Thruster page: 142
- Cat, Deltamarin Develop Modular FPSO Power Unit page: 144
- WEG’s CFW11W Offers Higher Power page: 144
- John Deere Expands Tier 3 Engine Lineup page: 144
- Successful MTG Light Off for USS Zumwalt page: 145
- MJP Introduces Hybrid Waterject page: 145
- This is One, Big Specialty Valve page: 148
- DNV GL Updates Phast Software page: 148
- SGB 2000 Gyrocompass Class Approved page: 148
- B COOL A/S Acquires Memac page: 148
- Hatteland’s 20-inch Display page: 148
- New Cutting Machine from ESAB page: 148
- Shell Launches App to Track Marine Lube Orders page: 148
- Hempel Launches AvantGuard Primers page: 150
- Underwater Locator Beacons for VDR page: 150
- Automatic Lubrication System for Shell’s Prelude page: 150
- Livorsi Launches New Throttle Lineup page: 150
- Delta-Y Assembly for Offshore Oil Bulk Cement/Barite Piping Systems page: 150
- Cummins Debuts Mobile Tier 4 Generators page: 150
- New Heater Kits for Northern Sea Route Vessels page: 151
- New Plasma Cutting and Gouging System page: 151
- New Simulation Tool for Collision Reconstruction page: 151
- ACO Unveils New Plant for Upcoming Wastewater Rules page: 151
- Survitec Escape Slide for Norwegian Ferry page: 151
- New Rolling Bearing Grease from Klüber page: 151
- KO-LINK Towing Ring from Lankhorst Ropes page: 151
- New Gear Grease and Oils from Klüber page: 152
- Portable Fire Extinguishers page: 152
- Self-Leveling, Height Adjustable Chocks page: 152
- ESAB’s New Welding Wire page: 152
- PalmScope Video Inspection System page: 152
- J D Neuhaus Hydraulic Lifts page: 152
- Flow Control for Multi-pump Applications page: 152