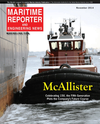
Talking Turbines with Bolsinger, VP at GE Marine
As the commercial marine market faces increasingly stringent propulsion system emission restrictions and fuel cost pressures, propulsion technologies such as gas turbines can gain traction in more mainstream commercial applications. Maritime Reporter & Engineering News recently spent some time with Brien Bolsinger, GE Marine’s VP of Marine, for insights from this traditional gas turbine power.
As GE is mammoth, can you concisely explain the products and services that GE Marine offers to the global marine market?
We sell complete propulsion systems for diverse ship applications in both the commercial and naval marine markets. GE Marine is one of the world’s leading manufacturers of aeroderivative marine gas turbines, ranging from 4.5 to 52 MW. Our gas turbines are excellent prime movers for mechanical drive, hybrid, or all electric propulsion systems. On the commercial front, our gas turbines are used in oil & gas for floating production, storage and offloading vessels, as well as on platforms. Our units are on passenger ships of various types: cruise ships, fast ferries and yachts. In the future, we see gas turbines bringing advantages to LNG carriers, too. From a naval perspective, we have a fleet of marine gas turbines powering various military ships, ranging from patrol boats on the small side, to aircraft carriers and may other ship classes in between. Our engines power ships in 33 navies around the globe and have garnered more than 13 million operating hours. But we are more than an equipment supplier. We offer complete service capabilities through our own overhaul facility, as well as through a network of authorized service providers.
Shipowners today – commercial and naval – are faced with new rules regarding emissions, and perpetually battle the fuel cost issue. How are these and other drivers affecting the use of gas turbines to power new commercial vessels?
Key market drivers remain tightening of worldwide emissions regulations as well as fuel pricing. New IMO guidelines will require lowering of SOx emissions by January 1, 2020. In concert, we anticipate the price gap to shrink between Marine Gas Oil and low sulfur diesel fuel, thus improving gas turbine economics. We also are seeing an extraordinary global build-out of the LNG infrastructure to support widespread use of this clean-burning and least expensive fuel in the marine industry.
Our turbines are fuel-flexible, capable of burning diverse fuels including LNG. All the while, GE gas turbines can meet stringent environmental emissions regulations, especially when equipped with our Dry Low NOx emissions (DLE) combustion system. This optional technology can meet Tier III IMO/Tier IV United States Environmental Protection Agency requirements now operating on gas or liquid fuel, with no exhaust treatment and no methane slip.
And the power density of our gas turbines – meaning their high power in a light weight, small footprint – offers room for more cargo or passengers. Simply stated this means GE’s gas turbine-based systems bring value to operators of nearly any commercial ship requiring 4 MW or more in power.
We know that GE Marine is a ubiquitous name in world maritime circles, but for the benefit of our readers can you discuss GE’s gas turbine experience in the global commercial marine sector?
We have delivered more than 90 of our marine gas turbines worldwide since 1995 for many commercial applications, including 17 cruise ships, five high speed yachts and 19 fast ferries. All told, the worldwide industrial and marine gas turbine fleet has garnered more than 85 million operating hours, 13 million of which are in marine applications.
A recent pioneering project that relies on GE gas turbines is the fast ferry Francisco. Operated by Buquebus, between Buenos Aires and Montevideo, Francisco is the world’s fastest commercial ship. Francisco began operating in July 2013, powered by two GE’s dual fuel 25 MW gas turbines; the ferry has the ability to operate on both MGO and LNG. These engines power the ship to speeds in excess of 50 knots during normal operation on either gas or liquid fuel. Also, the (compact footprint of the) gas turbines allowed the ferry to incorporate a 11,840-sq. ft. duty-free shop – reportedly the largest shopping area ever installed on a fast ferry.
GE gas turbines (also) blazed a trail in the cruise market; the only gas turbines installed on cruise ships anywhere in the world today.
And we have been in the commercial market for quite some time as demonstrated with the two 4.5 MW GE marine gas turbines that have been operating since 1995 onboard TurboJET’s Foilcat fast ferry. This multihull hydrofoil catamaran, which links Hong Kong to Macau, can carry 423 passengers, with a maximum service speed of 45 knots.
From where you sit, what are some of the operational advantages of gas turbines on commercial ships?
There are many, including:
• Power density: As I mentioned, one of the most obvious benefits of using our gas turbines is their size and weight advantages. This power density offers flexibility as to where you can place the propulsion system onboard the ship, requiring reduced structural steel to support the system within the ship, and freeing up more revenue-generating payload space. A perfect example is on cruise ships, where the gas turbines have been placed inside the funnel at the top of the ship, opening up space for an additional 45 state rooms in the hull below.
• Low NOx emissions: With our dual fuel DLE combustion system, GE gas turbines in a combined cycle operation meet even the most stringent pending 2016 levels when burning either (MGO or natural gas fuels, without exhaust after treatment. To date, we have manufactured 880 DLE systems for our aeroderivative gas turbines for industrial applications.
• Fuel Diversity: Our gas turbines offer fuel flexibility by being able to operate on various fuels including MGO, biodiesel, bio-synthetic paraffinic kerosene blends and natural gas. Fuel flexibility is even more beneficial today as commercial ship operators adopt dual-fuel operating scenarios to meet new emissions regulations. Dual fuel gas turbines operate in gas fuel mode (without liquid pilot fuel), or liquid fuel mode, and change between modes at any power level within 30 seconds.
• Reduced maintenance costs: We follow an “on condition” maintenance philosophy. This means that engine overhaul is not time-limited, but arranged when necessary as revealed during a regularly scheduled inspection. Even while operating at full power, 100% of the time, combustor and hot section repair intervals can stretch to 25,000 hours when burning natural gas.
• Increased availability: This maintenance philosophy yields increased availability of the vessel. When an engine overhaul is required, the gas turbine is removed and replaced by a spare unit, usually within 24 hours. Overhaul is not performed in-place (onboard the ship), but under shop conditions at a land-based depot facility.
What are the most popular ship configurations to use GE gas turbines?
Since propulsion architecture is based on the power required, the duty cycle, environmental concerns and many other factors, these are the most popular cycles used for ship propulsion:
• Combined gas turbine system mechanical drive - driving propellers (COGAG)
• Combined gas turbine and diesel mechanical drive (CODAG)
• Combined gas turbine or diesel mechanical drive (CODOG)
• Hybrid drive options: combined diesel electric or gas turbine (CODOG)
• Combined gas turbine, electric and steam system (COGES) for electric drive
We recently signed a MOU with Lloyd’s Register to identify potential gas turbine-powered commercial ship projects. This allows GE and Lloyd’s Register to work with shipyards to approve in principle GE gas turbine-powered commercial vessels for global customers. Separately, GE is teaming with Dalian Shipbuilding Industry Company and Lloyd’s Register to jointly develop a design for a gas turbine-powered LNG carrier.
Are there any other noteworthy,new technologies is GE Marine pursuing that would have application in the marine market?
GE teamed with Echogen Power Systems to provide Echogen’s exhaust heat-to-power products using CO2 in a closed loop configuration. These products enhance GE’s mechanical, hybrid and all-electric propulsion system solutions, boosting efficiency by capturing the heat inherent in the gas turbine or diesel engine exhaust stream and turning it into electricity. Echogen’s system allows for a more compact, lighter and economical configuration than traditional steam systems. Converting energy that traditionally gets exhausted into useful power allows the overall system thermal efficiency to increase to near 50%.
(As published in the November 2014 edition of Maritime Reporter & Engineering News - http://magazines.marinelink.com/Magazines/MaritimeReporter)
Other stories from November 2014 issue
Content
- Editorial: 75, 150 ... What’s in a Number? page: 6
- Is Glycerine the Next Marine Fuel? page: 16
- The Legal Consequences of 46 CFR Subchapter “M” page: 20
- Avoiding the Edges of the Sea page: 22
- Will Congress Pass Any Maritime Legislation in 2014? page: 26
- World’s Largest Containership First Tested at MARIN page: 30
- What’s All the Noise at IMO? page: 34
- From Security to Efficiency Modern Vessel Tracking page: 40
- Marine Insurance & the “Human Factor” page: 44
- Subsea Defense & the Changing Paradigm of Submarine Programs page: 48
- ZF Geared up for a Commerical Maritime Push page: 52
- Interview: Matthew Paxton, President, Shipbuilders Council Of America page: 58
- Offshore: Ulstein and the First U.S. Built X-Bow page: 66
- OilCraft’s TwinBow Challenge page: 74
- The McAllister Towing Legacy page: 76
- Denet Towing Repower Saves 20% in Fuel page: 92
- Eltorque Pushes into US Market page: 93
- AHTS Proves Strength on (in & through) Ice page: 94
- Kleven Orderbook Pumped up to $1.8b page: 96
- Z-Drive Use Spreads on US Inland Waterways page: 96
- Floating Production: Huge Opportunity for Shipyards, Manufacturers page: 98
- Special Vessels “Built by Flensburger” page: 100
- Danish Maritime Takes Center Stage page: 104
- Safety is Job One page: 110
- Focus: Heavy Duty Lifting page: 114
- Lifting Costa Concordia page: 118
- RV Sikuliaq: Modern Electric Propulsion & Power Management page: 122
- Talking Turbines with Bolsinger, VP at GE Marine page: 134
- DSME Returns for More Dual-Fuel Engines page: 138
- Volvo Penta Triple IPS and DP for New Fast Response Boat page: 138
- New Propulsion Couplings from Renold Hi-Tec page: 139
- Cummins Auxiliaries for New OSV page: 139
- Tier III Marine Power: Genset with SCR page: 140
- New Generation of Turbochargers page: 141
- Class Approval for Wärtsilä Steerable Thruster page: 142
- Cat, Deltamarin Develop Modular FPSO Power Unit page: 144
- WEG’s CFW11W Offers Higher Power page: 144
- John Deere Expands Tier 3 Engine Lineup page: 144
- Successful MTG Light Off for USS Zumwalt page: 145
- MJP Introduces Hybrid Waterject page: 145
- This is One, Big Specialty Valve page: 148
- DNV GL Updates Phast Software page: 148
- SGB 2000 Gyrocompass Class Approved page: 148
- B COOL A/S Acquires Memac page: 148
- Hatteland’s 20-inch Display page: 148
- New Cutting Machine from ESAB page: 148
- Shell Launches App to Track Marine Lube Orders page: 148
- Hempel Launches AvantGuard Primers page: 150
- Underwater Locator Beacons for VDR page: 150
- Automatic Lubrication System for Shell’s Prelude page: 150
- Livorsi Launches New Throttle Lineup page: 150
- Delta-Y Assembly for Offshore Oil Bulk Cement/Barite Piping Systems page: 150
- Cummins Debuts Mobile Tier 4 Generators page: 150
- New Heater Kits for Northern Sea Route Vessels page: 151
- New Plasma Cutting and Gouging System page: 151
- New Simulation Tool for Collision Reconstruction page: 151
- ACO Unveils New Plant for Upcoming Wastewater Rules page: 151
- Survitec Escape Slide for Norwegian Ferry page: 151
- New Rolling Bearing Grease from Klüber page: 151
- KO-LINK Towing Ring from Lankhorst Ropes page: 151
- New Gear Grease and Oils from Klüber page: 152
- Portable Fire Extinguishers page: 152
- Self-Leveling, Height Adjustable Chocks page: 152
- ESAB’s New Welding Wire page: 152
- PalmScope Video Inspection System page: 152
- J D Neuhaus Hydraulic Lifts page: 152
- Flow Control for Multi-pump Applications page: 152