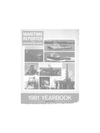
MOBILE JACKUP PLATFORMSPAST, PRESENT AND FUTURE
In November 1955, the first electromechanical, three-legged offshore s e l f - e l e v a t i n g drilling platform was launched from what was then R.G. LeTourneau's manufacturing facility on the Mississippi River south of Vicksburg.
Christened Scorpion by its owner, Zapata Offshore Company, this self-elevating offshore drilling platform was designed to operate in 80 feet of water.
That first-generation mobile offshore jackup rig was a giant step in the evolution of the offshore oil and gas industry. Earlier "mobile" offshore drilling platforms were often inland barges and drilling tenders, limited to the marshes and relatively safe shallow c o a s t a l w a t e r s of the Gulf of Mexico and Lake Maracaibo.
Although the triangularleg Scorpion's 80-foot operating depth is far less than the 300- to 350-foot capabilities of today's jackups, from another perspective it was a remarkable technological breakthrough. Scorpion's operating depth was twice that of its predecessors.
The decade f r om the mid-fifties to mid-sixties saw a remarkable spurt of inventiveness in design and manufacturing t e c h n o l o gy for jackup rigs. Like most technological revolutions, the rapid and successful development of the jackup was tied directly to economic conditions. Vast amounts of offshore oil and gas were known to exist. These energy reserves were in demand and return on investment in offshore exploration and production was attractive.
What had been missing was an economical, mobile, sturdy offshore d r i l l i n g p l a t f o r m from which experienced drilling contractors could exploit known offshore reserves. That piece of equipment had to be a true openwater vessel that could be safely towed to a drilling site, position itself securely, get the job done, then move on to the next location.
Once those initial engineering and fabrication challenges were overcome, the trend in jackup design took the direction of expanding water depth, drilling depth and operating environment capabilities.
This trend continues to dominate jackup technology today.
The improvements that have taken place in jackup capability have historically been stimulated by the need to find and produce a d d i t i o n a l offshore energy reserves.
Important desigri changes that increased operating water depths came d u r i n g t h e midsixties.
A unit was developed t h a t could operate in 250 feet of water. This j a c k u p had slanted legs. This change was based on two factors: first, the types of steel then readily available could not withstand the calculated combined loads when the spud legs were in a vertical configuration; second, the slanted legs increased the rig's overturning moment without requiring a larger and heavier hull.
These first slant leg jackups extended operating water depths by 100 feet. Later models of the slant leg self-elevating drilling platform could operate in over 300 feet of water.
By the early seventies, the use of higher strength steels made it possible to build jackups with vertical legs that could operate in water depths up to 350 feet.
Looking at the history of the offshore energy industry from our present perspective, it is accurate to say that the jackup is the success story of that industry.
It provides the offshore drilling contractor with the essential advantage of a stable, fixed area from which to work. Once a jackup is on location, it also provides important time and cost advantages over floating drilling equipment.
Of the several types of deepwater mobile offshore drilling units in use, jackups have proven they can drill more foot of hole per dollar spent.
Statistics bear out the jackup's dominant role in offshore operations.
At the start of 1981, there were 549 mobile offshore drilling rigs of all types. Of that total, 270 were jackups. Of the 204 mobile rigs on order or under construction at the start of the year, 152 were jackups. Jackups make up more than half of the total mobile offshore rig fleet. By the end of the eighties, the total number of jackups may well be 600.
The current state-of-the-art in jackup design and manufacture c o n s i s t s of building versatile units that meet the wide variety of drilling contractor requirements while at the same time satisfying the guidelines of regulatory agencies. Offshore exploration and development drilling now takes place in a number of areas that have a variety of meteorological and other environmental characteristics. There are jackups specifically designed for remote, deeper water areas where weather conditions such as frequency of storms, excessive wind and wave heights must be taken into account. A totally different class of self-elevating platform is specifically designed for accessible areas where weather, water depth or remoteness from supply sources are not major obstacles.
Between these two extremes of offshore operating environments are a number of other situations that call for jackups with different operating capabilities.
In addition to providing units tailored for specific environments, the rig construction industry took a major step toward meeting operator requirements with the introduction of the cantilever drilling jackup. This feature is now found on shallow water, moderate environment units as well as on large, deepwater units that can withstand wave heights up to 88 feet.
The incorporation of cantilever drilling into the jackup design concept added a remarkable degree of versatility. In rough waters, jackups provide a stable base so t h a t the cantilevered drilling package can remain extended and drilling operations continued.
In addition, the cantilever lets the s e l f - e l e v a t i n g offshore drilling platform p e r f o r m p r o d u c t i on drilling and well servicing functions in addition to exploratory drilling. In those areas where there are a number of bottomsupported production platforms, a cantilever jackup can take up position next to such a permanent structure, cantilever its drilling package over the structure without placing any weight on the platform, and carry out whatever drilling and well servicing activities are called for. When working on very large production platforms, it is feasible to move the drilling structure onto the permanent platform and use the mobile platform as a tender. The cantilever jackup has thus become a valuable and economic tool for extending the productive lives of older offshore wells.
In deeper waters, where there are fixed platforms that provide for multiple wells, cantilever jackups can drill exploratory or development wells in rough weather conditions that previously would have shut down drilling operations.
They can do this without exerting dead or static loads normally brought to bear on sea floor units by package drilling units resting entirely on the fixed platform.
This capability is extremely important in exploiting offshore oil and gas fields that previously had been judged as economically marginal. In such fields, the estimated recoverable reserves were not great enough to j u s t i fy large permanent, and costly, bottomsupported platforms from which to drill, complete and service multiple wells.
Such a situation offers a glimpse of what the future may hold for jackup rig application. For example, a North Sea operator plans to cut development costs of the Morecambe Bay offshore gas field by approximately $240 million.
Key elements in this plan are the use of jackup drilling platforms, a derrick package designed for slant drilling and a number of minimal fixed platforms.
These bottom-supported, fixed platforms will be strategically placed so as to permit depletion of as much of the field's reserves as possible. These platforms will be smaller, less expensive and quicker to construct than if conventional drilling techniques were used from large fixed drilling platforms.
The Morecambe Bay development plan calls for the self-elevating drilling platforms to be positioned alongside each of the minimal platforms. The drilling packages with slant drilling capabilities will then be skidded onto or cantilevered over the fixed platforms. Flexible control and drilling fluids lines will extend from the mobile platform to the drilling floor. With the mobile platform serving as tender, the jackup can move from fixed platform to fixed platform drilling and completing development wells to bring the field on stream and generate early cash flow.
Another innovative use of jackup drilling rigs presently under c o n s i d e r a t i o n is a mobile, retrievable early production system.
Such a system would be made up of a sea-floor concrete and steel storage unit, the jackup with a portable drilling template, and sea-floor as well as surface controls. The mobile p l a t f o rm would carry the drilling and production hardware.
Again, worldwide energy supply and demand factors will play a key role in the acceptance of such a system. This kind of retrievable, "reusable" system may well meet offshore requirements for lower total investment in early development of marginal fields. The system could be used to develop fields estimated at less than 500,000 barrels per day of crude production over a productive life of less than 10 years.
More immediately, a definite trend in jackup design is toward increasing not only the operating water depth but also the jackup's capacity to store consumable items such as fuel, cement, pipe, drilling mud, potable and nonpotable water, etc. Three criteria, namely operating water depth, drilling depth, and variable load capacity are directly related to environments in which the new "super" jackups will be operating.
This new generation of super jackups includes a massive unit that can operate under those extremely hostile c o n d i t i o n s of weather, water depth and remoteness which presently constitute the major frontiers of offshore operations. This "hostile environment" jackup can not only operate in these regions but can be safely towed from location to location under sea conditions that previously would have prohibited relocation. Such conditions exist in the North Sea, off the coasts of southern Africa and eastern Asia, both coasts of North and South America, and the Bering Sea. On location wave heights up to 88 feet combined with wind speeds of 100 knots were some of the factors that had to be accounted for in designing such a rig.
An important factor in the development of a jackup with these capabilities has been the effective use of higher strength steels to keep hull weight to a minimum and at the same time provide maximum strength.
The newest member of the jackup family is a unit specifically designed for those offshore areas where conditions are labeled "harsh" rather than "hostile." This unit's strong suit is its greater capacity to store more consumable items necessary for offshore drilling at greater distances from supply bases. This capability is a necessity because in most harsh offshore areas, frequent scheduled re-supply of consumables is impractical and unpredictable.
Speculation about the f u t u r e of any facet of offshore operations is risky. As for f u r t h e r development of the self-elevating offshore drilling platform, there will p r o b a b l y not be any radical changes in the basic jackup design in the near future. However, the proven and tested elements of this design will probably be f u r t h e r refined under the stimulus of worldwide demand for oil and gas. As a result, we may see operating water depths reach beyond the 300-400 foot maximums of the present. Storm rat- New York Office: JOTUN-Baltimore Copper Paint 74 Trinity Place/Suite 402 New York, N.Y 10006 (212)962-6500 Telex 8-7549 ings may increase and new techniques may permit the jackup to go on and off location in greater wave heights than permissible today.
Any of these developments are contingent on a number of economic and geopolitical factors.
One certainty is that the established jackup rig builders have demonstrated the expertise and capacity to build units that will go anywhere drilling contractors search for offshore oil and gas.
Other stories from June 1981 issue
Content
- SPC Coatings Combat Rising Fuel Costs- Literature Available page: 5
- Ryan-Walsh Bulk Terminal In New Orleans Resumes Coal-Handling Operations page: 5
- Brochure Available On Gilkes Self-Priming Pumps For Marine Market page: 6
- Henschel Changes Name Of Its Oklahoma Unit To Tulsa Division page: 6
- Atlantic Marine To Build Cat-Powered Drill Barge For Mecom Company page: 6
- National Marine Service Adds Sixth Drydock At Its Harvey Shipyard page: 6
- General Ship Expands Its Facilities In South Boston page: 6
- Floating Doughnut Crane Shown At Shugart Crane Conference page: 7
- EMD-Powered 'Gulf Condor' Delivered By Quality Shipyards page: 8
- RCA Opens Marine Services Office In Morgan City, La. page: 8
- Hans Schaefer Succeeds Arthur Stout As President Of Todd Shipyards page: 8
- FELS To Construct Semisubmersible Rig For Western Company page: 9
- David Parrot To Head New Aldenships Division Of John G. Alden Firm page: 9
- Edward Walsh Named Asst VP And Controller At J.J. Henry Company page: 9
- Oosterhuis Talk Describes Decline In Fuel Q u a l i t y - Free Copies Available page: 10
- Second Occidental Tug/Barge Unit Christened At Avondale Yard page: 10
- Megasystems To Provide Automation Package For Southern-Built Dredge page: 10
- Interlake's 'De Lancey' Christened- Longest Vessel On The Great Lakes page: 12
- Dravo Negotiating To Buy Operating Assets Of Nilo Barge Line From Olin page: 14
- Brochure Available On Foster Wheeler Boilers And Auxiliary Equipment page: 14
- A TIME OF GREAT EXPECTATIONS, ENTHUSIASM AND EXCITEMENT page: 15
- Vincent Ferraro Named Estimating VP For Savannah Shipyard page: 15
- Paceco Container Crane Arrives At Massport's Castle Island Terminal page: 15
- NASSCO Lays Keel Of First In Series Of Product Carriers For American Tankships page: 16
- Bay Shipbuilding Completes EMD-Powered Columbia Star page: 16
- Bryant Named Manager Of McGraw-Edison's New Marine Marketing Dept. page: 17
- Three New Technical Reports Available From Ship Structure Committee page: 17
- Penske Offers Brochure On Diesels/Gas Turbines For Marine/Offshore Power page: 18
- Subsidy Approved On USL Conversion Job To Cost $5.3 Million page: 18
- Consolidated Inland Opens East Division Office— R.R. Simms Named Manager page: 18
- El Paso Promotes Three- Harry Ray Named VP Of El Paso Marine page: 18
- MOBILE JACKUP PLATFORMSPAST, PRESENT AND FUTURE page: 19
- Serrie Joins Levingston As VP Of Operations page: 19
- lotron Conducts ARPA Demonstration In New York City page: 20
- First Of Five Hydrofoil Combatants Launched By Boeing Marine Systems page: 20
- ALL INDICATORS POINT TO DRAMATIC INCREASE IN DEMAND FOR BARGE CAPACITY page: 22
- Levingston Reorganized— Barrios, Covington And Wise To Head Three Units page: 22
- B IW Awarded $247-Million Navy Contract To Build Three Missile Frigates page: 24
- North Florida Shipyards Appoints Three—White Named Production Manager page: 25
- Captain Barry Roberts Named CO Of USCG's Curtis Bay Shipyard page: 25
- James Retert Joins Waukesha Engine As Director Of Marketing page: 27
- New U.S. Built Coal-Fired Ship To Be Powered By G.E. Steam Turbine page: 27
- Wasacz Succeeds Gray As President Of Matson Navigation page: 28
- Bel-Aire Yard To Build Two Tuna Seiners At Total Cost Of $20 Million page: 29
- AWO'S AMERICAN WATERWAYS SHIPYARD CONFERENCE IS SHAPING POLICY FOR LONG-TERM GROWTH page: 33
- Washburn & Doughty Delivers Combination Scalloper-Dragger page: 34
- GE-Powered Product Carrier For Union Oil Christened At NASSCO page: 34
- South Jersey Port Orders Heavy Duty Multi-Purpose Crane From Kocks page: 35
- U.S. NAVY - A MORE POWERFUL FUTURE page: 39
- RORO81 PREVIEW page: 39
- First Of Three Waterman Combination Carriers Features Largest MacGregor Stern Ramp page: 40
- OFFSHORE DRILLING RIGS, SUPPORT VESSELS, NAVY SHIPS, INLAND BARGES, AND REPAIR WORK BRIGHTEN THE U.S. PICTURE page: 41
- Canadian Yards And Government Speed Up Shipbuilding Training page: 41
- EDO Gets $3.9-Million Navy Award To Improve Existing ASW System page: 42
- Barber Steamship Lines Names Steven Roberts Assistant Vice President page: 43
- Navy Awards $276-Million Contract To Todd For Three Additional FFGs page: 43
- Promet Gets $60-Million Order For Drill Rig For Sedco Incorporated page: 44
- A VIEW OF WORLDWIDE SHIPBUILDING REVEALS SIGNS OF REVIVAL IN SOME SECTORS page: 45
- CANADIAN EAST COAST OFFSHORE SERVICE VESSELS-EXPERIENCES AND PROBABLE FUTURE REQUIREMENTS page: 50
- CANADA'S EAST COAST OFFSHORE OIL POTENTIALOPPORTUNITIES FOR SHIPBUILDING page: 52
- First Aegis Missile Cruiser Christened At Ingalls Yard page: 58
- Blount Delivers Commuter Boat To Fire Island Ferries page: 58
- Promet Private Limited Completes Jackup Service Barge For Sun Contractors page: 60
- Cornelsen Named Manager- Technical Operations For Well Control Systems page: 60
- Northern New England ASNE Holds Joint Meeting With NCAA & NANTS page: 64
- 'Griffin-Alexander I' Now In Service- First Of Eight Costing $280 Million page: 66
- SNAME Philadelphia Section Hears Report On Stack Performance page: 66
- Captain Sandberg Honored At New York Section SNAME Meeting page: 66
- Smit International Performs Tow Of Huge Production Platform page: 70
- Jackup For Houston Offshore Commissioned At Bethlehem Yard page: 70
- Joe B. Foster Named An Executive Vice President Of Tenneco Inc. page: 71
- New Booklet Lists Oil Spill Prevention And Cleanup Organizations page: 74
- New Brochure Describes Goodway's Full Line Of Tube Cleaning Equipment page: 74
- New Armco Weld Wire Accepted By U.S. Navy —Literature Available page: 77
- New Brochure Describes Sewage Treatment Plants From Weir Pumps Limited page: 78
- J.D. Cain Appointed A Division Manager For Racal-Decca Survey page: 79
- Wilson Walton Develops New Marine Incinerator —Literature Available page: 79
- DCC Orders Satellite Ground Equipment From Scientific-Atlanta page: 80
- Charles Orem, President Of Bird-Johnson, Named Chief Executive Officer page: 80
- J.P. Elverdin Appointed Vice President-Shipping For United States Steel page: 81
- Uniroyal Collapsible Rubber Drums Are Rugged —Literature Available page: 81
- Student Paper Presented At SNAME Northern California page: 82
- Catalog Detailing Its Full Line Of Products Available From Kraissl page: 82
- Ordering Brisk At Dravo, Including Four Towboats At Cost Of $16 Million page: 84
- N.A. DiRenzo To Head New Philadelphia Office Of Designers & Planners page: 84
- Western Gear Awarded $1.5-Million Contract For Six Drilling Rig Drives page: 84
- Jan van Lier Named A Vice President Of Moore McCormack Resources page: 85
- Student Papers Presented At Los Angeles SNAME page: 85
- Sedco Jackup Drilling Rig Christened At Promet Yard page: 86
- Detroit-Powered Towboat Delivered To FOSTI By Orange Shipbuilding page: 86
- W.L. Kwitchoff Named VP-General Superintendent At Savannah Shipyard page: 87
- Lunceford Elected Board Chairman And President Of National River Academy page: 87
- Vu-Gctge Systems Ordered By NASSCO For Tankers page: 88
- Wood Elected President Of Northwest Towboat Association, Seattle page: 88
- R.E. Fisher Appointed VP-Marine Services At SeaTec International page: 88
- DEBEG Marine Opens New U.S. Headquarters page: 89
- Hampton Roads SNAME Meeting Featured Sailing Film-Narration page: 91
- Puget Sound ASNE Hears Firsthand Account Of 'Prinzendam' Incident page: 92
- Rivtow Straits Orders EMD-Powered Tugboat From John Manly Yard page: 92
- Fred Shumaker Joins McClure Associates As Vice President page: 92
- Sun Transport's Latest Carrier Has Many Advanced Features page: 93
- Albert Termo Named VP-Marketing And Planning At Universal Maritime page: 94
- Norshipco Names New Officers—Wesley Payne Promoted To Senior VP page: 94
- Yugoslav Shipyards Licensed To Build Rigs Designed By Levingston page: 95
- Walter Beam Named Vice President-Research And Development At Sperry page: 95
- Brochure Available On O i l / W a t e r Emulsifier From Cleanodan A/S page: 97
- Levingston To Build Rig For Mexican Owner At its Port Arthur Division page: 97
- $1.2-Million In Marisat Terminal Contracts Goes To Scientific-Atlanta page: 98
- Madeo Appointed Vice President-Operations For Ocean Salvors page: 98
- Riva Schwartz Promoted To Sales Manager For Simrad, Inc. page: 100
- $622,500 Contract For Atlantic Marine Yard Authorized By MSB page: 100
- New Brochure Describes High-Level Tanker Alarm With Automatic Shutdown page: 100
- Marinette Marine Awarded $1-Million Navy Contract For MCM Evaluation page: 102
- Forthofer And Reardon Named Vice Presidents For Perry Oceanographies page: 102
- Hitachi To Supply Four B&W Type Marine Diesels To People's Republic page: 103
- Hermann Helms Named VP-International For Lykes Bros. Steamship page: 103
- Reception Honors Wheeler's Appointment As Exclusive Agent For Schelde Yard page: 104
- New Kawasaki Stern Bulb System Provided Impressive Fuel Savings On Trial Run page: 104
- Marine Moisture's Tank Gauging Meets IMCO Rules —Literature Available page: 105
- Orders For Vessels Built To American Bureau Class Surged In 1980 page: 107
- Matson Promotes Three- John Couch Appointed Senior Vice President page: 107
- Macawber To Prepare Coal-Handling Manual Under MarAd Contract page: 108
- Hartzell Marine Blowers Meet Federal Specs- Literature Available page: 108
- Rick Comoglio Appointed Sales Engineer For EG&G Sea-Link Systems page: 108
- Ingalls To Build Second Jackup For Bonito Offshore page: 109
- Drew Promotes Three In Ameroid Marine D i v i s i o n - Kay Named Vice President page: 109
- Big Living Quarters Module For North Sea Production Rig Delivered By Blohm + Voss Yard page: 110
- N a t i o n a l Supply Promotes Three In Sales—Petersen Named VP-Marketing page: 112
- Boston VLCC Companies Ask For Title XI Aid On Tanker Retrofits page: 115
- New Gems Flow Switches Designed For Heavy D u t y - Literature Available page: 115
- Selfbulk Vessel Provides Versatile Cargo-Handling System page: 116
- Bender Yard Awarded Contract To Re-power Towboat 'Great America' With S.E.M.T. Pielstick Engines page: 117
- Bayou Black Shipyard Delivers Crewboat And Pusher To Sundance page: 134
- Admiral John M. W i l l - Navy And Merchant Marine Leader-1900-1981 page: 134