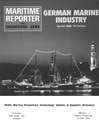
Norshipco: Striving To Strike A Military & Commercial Balance
Norfolk Shipbuilding & Drydock Corporation (Norshipco) in Norfolk, Va., is a privately held corporation that has served the Port of Hampton Roads in the marine industry since 1915. Norshipco is a fullservice shipyard, and has enjoyed a reputation as one of the largest repair facilities on the East Coast of the U.S.
At present, the workforce numbers approximately 2,000 people working in 23 diversified trade shops and departments.
The Main Yard At Berkley Norshipco's Berkley Plant features the Titan — one of the world's largest and most modern floating steel drydocks. The Titan is 950 ft.
(290 m) long, 192 ft. (59 m) wide and 160 ft. (49 m) between wingwalls, with a 54,250-ton lifting capacity.
The Titan is moored to a 1,030-ft.
(314-m) long concrete pier used to service and repair ships as long as 1,200 ft. (366 m). Two cranes service the Titan and the pier, one of which is a giant Kroll K-1800 Hammerhead jib trolley, with a stance of 250 ft. (76 m) in the air and a reach of 214 ft. (65 m). The Berkley Plant has eight full service piers and extensive crane service.
Complementing the Titan is the Virginian, a 20,000-ton lifting capacity drydock with wingwall cranes. The Virginian is an all-steel floating drydock that measures 670 ft. (134 m) long by 126 ft. (38.5 m) wide.
Brambledon Norshipco's Brambledon Plant services medium-sized oceangoing vessels. The plant is complete with seven full-service piers, four 30-ton diesel cranes, a 2,500-ton floating steel drydock, Challenger, and two marine railways. The Challenger is 200 ft. (61 m) long and 70 ft. (21 m) wide, and was built at the Berkley Plant.
The Brambledon Plant performs "downriver" work. Vessels in need of production work and not requiring entry into a repair facility, or vessels having limited time, can stay at their present location ("downriver") and shiprepair teams from the Brambledon Plant facility will travel to the vessel to perform the required work or services. In a sense, these shiprepair teams bring the shipyard to the ship.
Today: A Commercial & Military Mix Norshipco drydocks an average of 80-plus vessels a year. This includes tandem dry dockings of Navy combatants, and triple dockings of commercial vessels in the same drydock. Extensive hull painting and blasting, piping and machinery system repairs and modifications, as well as steel and structural repairs are performed on a routine basis. In 1993 Norshipco received 107 marine-related contracts: 72 commercial contracts and 35 for the U.S. government. Government awards included one contract for the Army, three for the National Oceanic and Atmospheric Administration (NOAA), six for the Maritime Administration (MarAd), 10 for the Navy, and 15 for the Military Sealift Command (MSC).
The U.S. government has been one of Norshipco's major customers for most of the life of the corporation, which was rated one of the Top 100 defense contractors for 1991 in terms of dollar value of Defense Department contracts awarded.
Norshipco's two steel floating drydocks at the Berkley Plant performed a total of 58 drydockings in 1993, 14 for U.S. government ships and 44 commercial ships.
Norshipco performed work on eight cruise ships during 1993, including the Sovereign of the Seas, Festivale, Royal Princess, Regal Princess, Meridian, Nordic Empress, Regent Sun and the Rotterdam. Notably, Norshipco worked with Sea-Land Service, Inc.
on an aggressive drydocking, repair and maintenance contract for six Atlantic class containerships.
Each ship underwent a seven-day schedule of required drydocking, blasting and painting, sea-valve work, readings on tailshaft and rudder, tug reinforcement (involving internal structural back-up support) and regulatory body ballast tank inspections by ABS and the U.S.
Coast Guard. Norshipco also worked on three smaller Lancer class vessels and the Sea-Land Expedition for Sea-Land, under separate contracts.
Contracts awarded to Norshipco performed to date for 1994 include both commercial and government contracts. By the end of the first quarter of 1994, the Berkley Plant had performed or was performing two Navy contracts, seven MSC and MarAd contracts, three cruise ship contracts and 11 other commercial contracts. The second quarter produced one additional Navy contract, two MarAd contracts, one cruise ship and eight other commercial contracts.
Third quarter awards have produced two Navy contracts, four MSC/MarAd contracts, two cruise ship contracts and seven more commercial contracts.
Major awards to Norshipco from the Navy slated for the fourth quarter include: • USS Simpson FFG 56, for a Selected Restricted Availability (SRA), to be performed from June 27, 1994 through October 21, 1995.
• USS Normandy (CG 60), for a Drydocking Selected Restricted Availability (DSRA), from August 1, 1994 through November 3, 1995.
• Floating drydock Resolute (AFDM 10), for a Regular Overhaul (ROH), from October 1,1994 through March 10 1995 • USNS Niagara Falls (T-AFS 3), an MSC nationwide "Best Value Procurement" solicitation. Awarded to Norshipco with a 274-day availability to include voyage repairs, overhaul, habitability arrangement, addition of elevators, drydocking and repair and maintenance, to be performed from November 4, 1994 through August 4, 1995.
• The Phased Maintenance Program (PMP) for the LSD/LPD class vessels homeported in Norfolk. This PMP includes the vessels USS Pensacola (LSD 38), USS Portland (LSD 37) and the USS Austin (LPD 4). The award for the LSD/LPD includes nine availabilities for three ships. The PMP has a performance period from the first ship's availability of October 12, 1994 to the last ship's availability of November 6, 1998. The Phased Maintenance Program was also for AO-177 class vessels homeported in Norfolk. This includes USS Monongahella (AO 178), USS Merrimack (AO 179), and the USS Platte (AO 186). The three AO 177 class vessels are slated to undergo eleven availabilities during the life of the program. The PMP has a performance period between October 4, 1994 and December 3, 1999. The downsizing of the U.S.
military has produced a shift towards an increase in commercial shiprepair and conversion markets.
Norshipco also provides a number of specialized services through the following subsidiaries: Diesel Marine Norshipco. A subsidiary developed to meet increasing demands for diesel service.
Norshipco joined with Europe-based Diesel Marine International, which supplies, reconditions and exchanges diesel engine components.
Diesel Marine Norshipco offers special parts exchange services that eliminate the lengthy, expensive wait for parts. Norshipco's multimillion- dollar investment in an autonomous machine shop, chromeplating and reconditioning facility, combined with a full staff of European- trained diesel mechanics, offers customers state-of-the-art services at competitive U.S. prices.
Industrial Conversion & Repair Services. Norshipco is able to use its shipbuilding and repair capacities in diverse industrial repair and construction projects. The division specializes in industrial plant construction, repair and conversion.
Services are available 24 hours a day, seven days a week, throughout the U.S.
With the drive to increase its participation in the national and international markets, Norshipco is committed to meeting the challenges of the shiprepair market by providing high quality work, special component reconditioning and engineering services to a wide range of markets including international shipping, defense, power generation and the industrial market. To meet the needs of the domestic and international marketplace, Norshipco has increased its efforts toward the commercial shiprepair and conversion market. Norshipco prides itself on operating in a safe and environmentally responsible manner and in providing products and services that fully meet the customers' requirements economically and in a timely manner. Norshipco strives for total customer satisfaction and the elimination of quality deficiencies through the application of an effective Quality Management System based upon the requirements of the International Standards Organization (ISO 9002).
For more information on Norshipco Circle 82 on Reader Service Card
Other stories from September 1994 issue
Content
- Clipper III: A Case Study In Monitoring Systems page: 74B
- Permea Maritime Finishing Membrane Nitrogen Generator For Offshore page: 6
- 1969 Tonnage Convent HI Now Fully Operative page: 7
- USCG Announces Mandatory Registration of EPIRBs page: 8
- Vessel Financing In The '90s page: 11
- Dredging Feasibility Study For Jacksonville Harbor page: 13
- ILU Reports A Disappointing First Half of '94 page: 15
- CRIS: An Affordable, High-Risk Insurance Solution page: 17
- Colvic Craft Delivers 12 Of 44 Patrol Vessels To G r e e k Coastguard page: 18
- Bay Fabrication Lengthens OSV Ensco Endeavor page: 18
- Cutters Become First N . A . Surface Ships To Reach N o r t h Pole page: 18
- Designs for the 21st century page: 20
- Tuna war and subsidy accusations add to fishing industry woes page: 21
- Maximum Vessel Length To Transit Seaway Is Increased page: 23
- Gladding-Hearn Delivers High-Speed Cat To Maine Whale Watch Co. page: 24
- Elliott Bay Design Group Performs Finite Element Analysis For Arco page: 24
- State Of The German Shipbuilding Industry page: 27
- SMM '94 Product Showcase page: 28
- Blohm + Voss Shortens Sea-Land Ships, Gels QE2 page: 28
- Meyer Werft: The New Old Yard page: 30
- The German Maritime Industry page: 30
- HDW's Shipyard 2000 Plan In Full Swing page: 31
- Lindenau: Developments On The Containership, Tanker Fronts page: 32
- HydroComp, HSVA GmbH Announce Alliance page: 37
- MWH To Focus On Service As Well As Products page: 37
- SMM '94 page: 38
- Unger Named President Of Raytheon Marine Company page: 40
- Lykes Bros. Announces Organizational Changes page: 42
- Textron M&LS President Honored By Navy League page: 42
- Garrow Retires From Newport News page: 42
- Ingalls Christens Aegis Stethem, Commissions Aegis Stout page: 45
- Renewing Engine Monitoring Systems In Old Ships Saves Money page: 45
- Predicting Thermochemical Performance Of Materials Made Easier By NIST page: 46
- MES Completes Natural Gas-Fired High Efficiency Large Low-Speed Diesel Demonstation Plant page: 46
- Global Ocean Carriers Considers U.S. Yards, Title XI For Fleet Expansion page: 46
- N.E. Waterborne Gaming Conference & Exposition page: 47
- Casino Vessel Market Roots Spread To N.E. page: 47
- House Approves $ 1.35 Billion For Maritime Reform page: 48
- Trinity Wins $120-Million Contract For Two Vessels page: 48
- M T W Delivers Containership, Westerdeich page: 55
- Larger Vessels — Good Or Bad For The Liner Industry? page: 56
- Propulsion Machinery Review page: 58
- Newport News Pursues The Electric Drive page: 72
- GE LM2500+: Packing A More Powerful Punch page: 74
- Stolt Selects MMS' FleetWORKS For Tankers, Houston Office page: 77
- COMSAT President To Deliver Keynote Address At Satellite Communications Users Conference page: 78
- Sonsub Awarded Contracts From McDermott, Texaco page: 78
- Thor Dahl Shipping Expands To South Pacific page: 79
- SCN Container Line Linking South Florida, 12 Latin American Countries page: 79
- Fish Expo '94 - Boston page: 80
- Raytheon Subsidiary Teams With Scottish Firm On Undersea Project page: 81
- Navatek II Features Unique Fixed Stabilizer With Split Rudder System page: 83
- Keels & Appendixes page: 83
- Tanker Escorts, COFRs Fill OPA 90 Agenda page: 84
- VTS Participation Becomes Mandatory page: 86
- DGPS Given Go-Ahead In Northwest page: 87
- CSI: Offering Systems For Compliance With U.S. Coast Guard Requirements page: 90
- Hyde Products Offers Full Spill Response Line page: 90
- Annual Certification Of Alaska Advisory Group page: 90
- MarAd Gives Go-Ahead To Extend Cherry Valley's Subsidizable Life page: 91
- MarAd Expands Electronic Bulletin Board page: 92
- MarAd Receives Section 9 Applications page: 92
- Great Lakes Ports May Handle Preference Cargoes Under Program page: 92
- MarAd Approves Section 9 Requests page: 92
- Research Report — Shipboard Piloting Expert System — N o w Available page: 93
- NRC's Vikoma-Built Skimmer Proves Valuable In Oil Spill Cleanup page: 94
- Union Noval de Levante Launches Advanced-Technology Asphalt Carrier page: 94
- Bender Completes Riverboat To Operate In Bossier City, La. page: 94
- MarAd OKs APL Section 804(a) Waiver Request page: 96
- MarAd Issues Order Regarding Seabulk America page: 97
- THE WORLD ORDERBOOK page: 98
- Marco Designs N e w Class Of Combination Vessels page: 99
- Variable Draft SWATH DSV To Be Constructed page: 100
- Norshipco: Striving To Strike A Military & Commercial Balance page: 101
- Two Promotions At Midland Manufacturing; Increased Focus On Marine Market page: 106
- Alfa Laval Tapped For New Ships page: 106
- Nautronix To Supply DP System For USCG WLB page: 107
- Astilleros Espanoles' Puerto Real Yard Preps Shuttle Tanker For Delivery page: 108