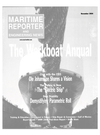
Electric Boat Optimizes Nuclear Sub Repairs
The shipbuilding and repair industry faces many challenges given the mission- critical complexities of maritime projects, as well as some misperceptions.
The industry faces a challenge: how to find more efficient ways to build new ships as well as to repair and upgrade aging ships. One leading resource. General Dynamics Electric- Boat, has implemented a solution that, in addition to expediting project tasks, also demonstrates the dynamic side of this industry. Electric Boat is a premier designer and builder of nuclear submarines, and also provides a full range of repair, overhaul and lifecycle support activities. A recent project demonstrates the company's adherence to maintaining excellence.
Electric Boat turned to Climax Portable Machine Tools (Newberg, Ore.) to expedite one of its more important responsibilities: performing maintenance on submarine missile tubes for the U.S. Navy. Bob Johnson, Senior Test Operating Engineer for Electric Boat, initiates these maintenance projects. He manages the test measurement program which determines exactly where a piece of equipment must be installed to tackle a job. or what modifications must be made to ensure the tool will fit. Johnson describes the challenges found in the maintenance tasks on the missile tubes.
"Setting up our old boring system took several man-days before we could start the actual work." he said. "We had to weld in blocks to hold the machine, and continually chalk it to offset drifting during the bolt-down process. We also had to test to make sure no damage was caused to the surrounding material by welding in and later cutting out those blocks. Later, we needed to repaint the entire work area." All these steps were not only timeconsuming, but required the involvement of numerous personnel, from machinists and riggers to specialists able to safely handle lead-based paints.
"Completing work on just one missile tube could take 10 full days with three shifts working eight hours," said Johnson. "Considering that the average boat has 24 tubes to maintain, the time and expense involved was incredible." After hearing favorable reports from colleagues, Johnson contacted the team at Climax.
"Climax came up with a design for a custom machine based on its standard boring bar system, and instructions on how it would operate. Down in the tube, I went through the motions of what we would do and how it would work. The time savings were quickly apparent." The missile tubes are re-bored as part of the year-long maintenance routine every submarine undergoes every 10 to 20 years. Sea pressure from frequent diving causes the tubes to get out of round. The tube Electric Boat worked on for its test case, however, was extremely "ovalized" as Johnson put it.
"It was a challenge to set up," Johnson said. "We basically learned in a worst Maritime Reporter & Engineering News case scenario situation, but our new machining system managed it beautifully." Johnson reported his findings and recommendation to Electric Boat's home office, and received approval for eventual purchase of six Missile Tube 5656 Boring machines which, thanks to on-site training and support from Climax proved successful from the start.
The new tool eliminates the need for set-up welding, cutting out blocks, damage testing, and repainting.
There's also no need for constant chalking to keep the machine in position. "The Climax machine is already set up," said Johnson. "You just snug it into place, and boring can begin." Electric Boat has seen a savings in time and manpower, as the new system is more than six times faster. Set-up takes just four hours, compared to 18 hours with the old system. And instead of 10 threeshift days, maintenance on a missile tube now takes a single shift just four to five days.
Three boring systems are in use in the Puget Sound Naval shipyard to maintain both SSGN and SSBN submarines.
Three other machines are available at the Norfolk naval yard pending the completion of training sessions Johnson is currently conducting. In addition, the Puget Sound location is considering purchasing a second model for the lower part of the missile tubes.
Johnson cites cost savings, ease of operation and simplicity of design as benefits that any type of shipbuilding or repair operation could look forward to by putting a similar machine to work.
"This type of tool would be effective in any type of work involving water tight boundaries, such as a door, a hatch area, or valve seats," Johnson said. "A Climax machine would work great in maintaining any area that takes a great amount of sea pressure, on any type of submarine or ship." Circle 21 on Reader Service Card
Other stories from November 2004 issue
Content
- Austal Launches 417 ft. Aluminum Ship page: 9
- Design Completed for Steamship Authority Ferry page: 9
- Blount to Deliver MV Isleno page: 10
- SF Bay Ferry Logs Impressive Performance page: 11
- NASSCO Holds Ceremony for Fourth BP Tanker page: 12
- K&C Wins $6M Navy Contract page: 12
- Air Emissions from Ships page: 14
- Shipboard Training Comes of Age page: 17
- Demystifying Parametric Roll page: 20
- A Bright Spot in Oil Patch Vessel Construction page: 26
- Senesco Marine Signs Contract For 140,000-Barrel DH ATB page: 30
- Coffee Company Investigates MContainer-on-BargeM Service page: 31
- USCG Invests in Low Engine Exhaust Temps page: 33
- Seacraft Delivers RV Hercules page: 36
- Caterpillar Gets "ACERT"-ive page: 37
- Making the Mark For Crescent Towing's Fleet page: 40
- The New Wartsila 46F page: 41
- Market Vision with Wartsila s Ole Johansson page: 42
- VT Halter Launches PCTC page: 44
- Aluminum Industry Continues Support for the Marine Market page: 46
- Film Celebrates Golden Age of NW Boats page: 47
- Pressure Transmitter Receives ABS Approval page: 48
- Fire Prevention: "Rising" to the Occasion page: 48
- For Those in Peril page: 50
- A Future in Composites page: 52
- Extra Value in Chinese Construction page: 53
- Record Spend on Propulsion? page: 54
- Collaboration Creates Vehicle for CNG Solutions page: 56
- Milestone Reference with MAN B&W page: 58
- The Will for Business page: 58
- Wider Remit for Dutch Matchmaker page: 58
- 2n d Generation Onboard NAPA Tanker Released page: 58
- Nichols Named "Maritime Man of the Year" page: 59
- ACBL Makes Appointments page: 59
- International Paint Japan K.K. - Open for Business page: 60
- European Yard Initiative - Will it Work? page: 62
- A.P. Meller-Maersk Creates Dedicated Tech Group page: 64
- SembCorp Signs Breakthrough, Long Term LNG Deal page: 66
- Keppel Batangas Completes SemiSub Repair page: 68
- A&P Tyne Re-Delivers FPSO Haewene Brim page: 68
- Crane Materials Launches TimberGuard page: 70
- Fincantieri Orders Water- Lubed Shaft Bearings page: 70
- Bilge Water Treatment Unit Approved By LR page: 71
- Electric Propulsion for Coastal Ships page: 72
- ALSTOM Wins $102M Navy Deal page: 73
- Offshore & Marine Chose Vacon AC Drives page: 73
- Successful Full Load Operation of 5-MW Ship Propulsion Motor page: 74
- Innovative Tweendeck Patented in U.S. page: 76
- MAN B&W Records Busy Hamburg Show page: 77
- Transas Demonstrates New Tech at SMM page: 77
- BV Launches Project Management Solution page: 78
- Xantic Offers New Web-Based Tool page: 79
- New AIS Targets U.S. Workboat Market page: 80
- Hepworth Makes a Good Show at SMM page: 80
- New PVC-Free Alternatives for Interior Decoration page: 80
- A High-End Global Satcom Presence page: 82
- IPS Marine Lands New Blue Chip Casino page: 85
- Rigdon Marine Promotes Harkness to CFO Post page: 85
- Tidewater: Effects of New Tax Bill Are Positive page: 86
- Bollinger to Design, Build Five DH Hot Oil Barges page: 87
- B+V Wins Passenger Ship Contract page: 88
- In Remembrance: Captain Fred Kosnac Jr. (1928-2004) page: 92
- Electronic Charting Aboard APL China page: 93
- Electric Boat Optimizes Nuclear Sub Repairs page: 94
- Kramek, Liu Snare Top SNAME Honors page: 97