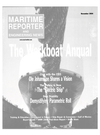
Successful Full Load Operation of 5-MW Ship Propulsion Motor
American Superconductor Corp.
announced that its prototype 5- megawatt (MW) High Temperature Superconductor (HTS) ship propulsion motor has been demonstrated successfully at full load, under steady state operational conditions, at the Center for Advanced Power Systems (CAPS) at Florida State University in Tallahassee.
The motor was developed under contract with the U.S. Navy's Office of Naval Research (ONR) to prove the viability of HTS technology for both military and commercial marine propulsion.
After the 5-MW motor completes load and ship mission profile simulation tests at CAPS, it will undergo additional performance testing at the Naval Surface Warfare Center. Carderock Division in Philadelphia. The Navy will then define further land-based and at-sea testing for this motor.
"We continue to be pleased with these new test results on the 5-MW superconductor motor," said Rear Admiral Jay Cohen. Chief of Naval Research. "The HTS ship propulsion motors we have been developing continue to perform above our expectations and are providing an important new option for future Navy propulsion systems." HTS motors are ultra-compact, measuring as little as one-third the weight and one-half the size of copper-based motors of the same power and torque rating, which means Navy ships can carry more fuel and munitions and have more room for crew's quarters and weapons systems, and commercial ship owners and operators can carry more passengers and cargo.
Technical Background Significantly, the HTS motors being developed by AMSC involve no major changes in fundamental motor technology.
The machines operate in the same manner as conventional motors, gaining their substantial advantages by replacing copper rotor coils with HTS rotor coils.
The rotors of HTS motors run "cold," so they avoid the thermal stresses experienced by conventional machines during normal operation. The inability to achieve proper thermal management has been a key impediment in developing power dense, high torque motors required for naval and commercial marine applications.
AMSC's 5-MW (6,667 shp) HTS propulsion motor rotates at 230 rpm and generates 200,000 Newton-meters of torque at full power. This power and speed rating are typical for copper-based electric propulsion motors currently used in ferries and small cargo ships around the world. This class of superconductor motor also is expected to become a standard power rating for certain military ships.
The 5-MW HTS motor is a subscale version of the 36.5-MW (49,000 hp), 120 rpm HTS motor currently being built by AMSC and Northrop Grumman under a $70M three-year contract from ONR. The 36.5-MW motor, which will produce 2.9 million Newton-meters of torque, is due to go through a Detailed Design Review with the Navy in October - the next major step in its development. Scheduled to be delivered in the spring of 2006. the 36.5-MW motor is being specifically designed to provide propulsion power for the next generation of Navy warships. A motor of this scale also has direct commercial application in large cruise ships and merchant vessels. As an example, two 44-MW conventional motors are used to propel the famous Queen Elizabeth 2 cruise ship. These motors each weigh over 400 metric tons: the 36.5-MW HTS motor will weigh approximately 75 metric tons. Newer vessels, such as the QE2's sister ship Queen Mary 2, which sailed on her maiden voyage in January 2004 and has a total propulsion requirement of 84-MW. are ideal candidates for HTS motors.
Circle 26 on Reader Service Card
Other stories from November 2004 issue
Content
- Austal Launches 417 ft. Aluminum Ship page: 9
- Design Completed for Steamship Authority Ferry page: 9
- Blount to Deliver MV Isleno page: 10
- SF Bay Ferry Logs Impressive Performance page: 11
- NASSCO Holds Ceremony for Fourth BP Tanker page: 12
- K&C Wins $6M Navy Contract page: 12
- Air Emissions from Ships page: 14
- Shipboard Training Comes of Age page: 17
- Demystifying Parametric Roll page: 20
- A Bright Spot in Oil Patch Vessel Construction page: 26
- Senesco Marine Signs Contract For 140,000-Barrel DH ATB page: 30
- Coffee Company Investigates MContainer-on-BargeM Service page: 31
- USCG Invests in Low Engine Exhaust Temps page: 33
- Seacraft Delivers RV Hercules page: 36
- Caterpillar Gets "ACERT"-ive page: 37
- Making the Mark For Crescent Towing's Fleet page: 40
- The New Wartsila 46F page: 41
- Market Vision with Wartsila s Ole Johansson page: 42
- VT Halter Launches PCTC page: 44
- Aluminum Industry Continues Support for the Marine Market page: 46
- Film Celebrates Golden Age of NW Boats page: 47
- Pressure Transmitter Receives ABS Approval page: 48
- Fire Prevention: "Rising" to the Occasion page: 48
- For Those in Peril page: 50
- A Future in Composites page: 52
- Extra Value in Chinese Construction page: 53
- Record Spend on Propulsion? page: 54
- Collaboration Creates Vehicle for CNG Solutions page: 56
- Milestone Reference with MAN B&W page: 58
- The Will for Business page: 58
- Wider Remit for Dutch Matchmaker page: 58
- 2n d Generation Onboard NAPA Tanker Released page: 58
- Nichols Named "Maritime Man of the Year" page: 59
- ACBL Makes Appointments page: 59
- International Paint Japan K.K. - Open for Business page: 60
- European Yard Initiative - Will it Work? page: 62
- A.P. Meller-Maersk Creates Dedicated Tech Group page: 64
- SembCorp Signs Breakthrough, Long Term LNG Deal page: 66
- Keppel Batangas Completes SemiSub Repair page: 68
- A&P Tyne Re-Delivers FPSO Haewene Brim page: 68
- Crane Materials Launches TimberGuard page: 70
- Fincantieri Orders Water- Lubed Shaft Bearings page: 70
- Bilge Water Treatment Unit Approved By LR page: 71
- Electric Propulsion for Coastal Ships page: 72
- ALSTOM Wins $102M Navy Deal page: 73
- Offshore & Marine Chose Vacon AC Drives page: 73
- Successful Full Load Operation of 5-MW Ship Propulsion Motor page: 74
- Innovative Tweendeck Patented in U.S. page: 76
- MAN B&W Records Busy Hamburg Show page: 77
- Transas Demonstrates New Tech at SMM page: 77
- BV Launches Project Management Solution page: 78
- Xantic Offers New Web-Based Tool page: 79
- New AIS Targets U.S. Workboat Market page: 80
- Hepworth Makes a Good Show at SMM page: 80
- New PVC-Free Alternatives for Interior Decoration page: 80
- A High-End Global Satcom Presence page: 82
- IPS Marine Lands New Blue Chip Casino page: 85
- Rigdon Marine Promotes Harkness to CFO Post page: 85
- Tidewater: Effects of New Tax Bill Are Positive page: 86
- Bollinger to Design, Build Five DH Hot Oil Barges page: 87
- B+V Wins Passenger Ship Contract page: 88
- In Remembrance: Captain Fred Kosnac Jr. (1928-2004) page: 92
- Electronic Charting Aboard APL China page: 93
- Electric Boat Optimizes Nuclear Sub Repairs page: 94
- Kramek, Liu Snare Top SNAME Honors page: 97