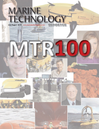
High Precision MEMS Silicon Sensing Inertial Sensors and Systems
Formed in 1999 Silicon Sensing’s is known for precision in the field of MEMS inertial sensors. 30 million MEMS gyroscopes, accelerometers, and Inertial Measurement Units (IMUs) have been supplied to hundreds of customers worldwide for use in a diverse spectrum of applications from marine applications through to space vehicle control.
Recent developments have expanded these capabilities to meet the accuracy requirements typically reserved for FOG (Fiber-optic Gyroscopes) and RLG (Ring Laser Gyroscopes) technologies by providing evolutionary high precision MEMS inertial products with low output noise and bias instability. These products have emerged from pedigree processes and platforms to offer lower cost, robust, and reliable products coupled with compact packaging to help meet the ever decreasing space and cost constraints of today’s marine applications.
Silicon Sensing produces a wide range of single-axis silicon MEMS gyroscope sensors and modules to suit a diverse range of applications with varying performance specifications. The family of gyroscopes all use the same unique patented Vibrating Structure Gyroscope (VSG) resonating ring technology to sense rotation rate through the Coriolis Effect. VSG ring technology is designed to provide superior performance in high shock and vibration environments. Silicon Sensing has coupled this base technology with in-house foundry expertise to successfully and efficiently develop high yield mass production capability of three generations of MEMS VSGs. These field proven generational technologies include Inductive (VSG3), Capacitive (VSG4), and the latest fifth generation PZT (VSG5). Silicon Sensing leverages its inertial experience to develop custom and discrete electronics in conjunction with the various VSGs to assemble and package the family of products with the desired performance characteristics and output parameters. These intrinsic capabilities allow Silicon Sensing to produce a wide range of MEMS VSG gyros from low-cost, precision, chipscale sensors (e.g.PinPoint) up to FOG-grade high performance MEMS Gyro modules (e.g. CRS39 and CRH02).
Silicon Sensing provides a diverse group of single-axis MEMS gyroscope sensors and modules products with performance in the 0.08 °/hr – 14 °/hr bias instability range. The latest of which being the PinPoint chipscale sensor which is built around the VSG5 technology incorporating unique thin film PZT MEMS processing. This sensor offers low angle random walk (0.28 °/√hr) performance characteristics.
Silicon Sensing also provides a range of high performance single-axis MEMS gyroscopes which deliver very low bias instability (0.7 °/hr - <0.08 °/hr) performance. These sensors are suitable for marine attitude and positioning control system applications requiring high accuracy and reliability, in a compact and affordable module. Following the success of the CRS09 gyro (0.7 bias instability and <0.1 °/√hr angle random walk) gyro, the CRH01, CRS39, and CRH02 emerge from Silicon Sensing offering lower cost, robust and compact alternatives to expensive FOG and RLG technologies. These sensors further expand the well-established VSG3 inductive technology for superior performance with proven reliability. Typical performance characteristics are indicated in the table below.
The CRS39 series high performance sensors offers a dynamic range of ±25 °/sec and four variants of the CRH series sensors are available to accommodate user dynamic range requirements from ±25 °/sec to ±400 °/sec.
Traditionally MEMS gyroscopes have exhibited performance that was an order of magnitude greater than good FOG devices. The Silicon Sensing MEMS gyroscopes are now delivering performance levels comparable to FOG devices.
These high performance product offerings have expanded the Silicon Sensing MEMS inertial sensor capability to include gyro compassing applications. Using these sensors, specifically CRS39, in a gyro compassing application it is typical to see <1° of pointing accuracy within 1 minute and <0.2° of pointing accuracy within 12 minutes.
Silicon Sensing will continue to expand these capabilities through continued development efforts to gain additional high performance improvements in the VSG3 inductive technology product line. These improvements will be integrated into future robust, reliable, and compact product offerings consistent with Silicon Sensing current high quality product portfolio.
Along with the wide range of MEMS gyroscope products, Silicon Sensing also offers a MEMS accelerometer, Gemini. Gemini is a high performance two-axis accelerometer in a single package that offers five product variants across dynamic ranges from 0.85g to 96g in a small robust and compact planar or orthogonal mounted package. Precise linear acceleration sensing is achieved by a Silicon MEMS detector forming an orthogonal pair of sprung masses. Each mass provides the moving plate of a variable capacitance formed by an array of interlaced ‘fingers.’ Linear acceleration results in a change of capacitance which is measured by demodulation of the square wave excitation. This design and measurement technique yields exceptional performance results for bias and scale factor repeatability (1 year) across the product variants.
Silicon Sensing leverages its in-house gyroscope and accelerometer technology and products to produce an organic MEMS combi-sensor chip, Orion, as well as complete package six-degrees-of-freedom (6-DOF) Inertial Measurement Units (IMUs).
Orion is a single axis gyro (VSG5 PZT MEMS resonating ring) and dual-axis low-g accelerometer (Gemini MEMS accelerometer element) MEMS combi-sensor. The unit features user-selectable dynamic range and bandwidth, with a digital SPI output. The Orion combi-sensor chip is available in flat and orthogonal formats with a hermetically-sealed ceramic LCC surface mount package.
Silicon Sensing currently offers IMUs and is in the final stages of development for a new dynamic measurement unit; DMU10, which will be available in the early fall of 2014. DMU10 is designed to be a low-cost, high precision, 6-DOF IMU which offers robust and user friendly formats with OEM and Module configurations, either of which can be supplied un-calibrated, calibrated at room temperature, or calibrated over the full operating temperature range. Silicon Sensing has also designed in expansion capability to integrate additional sensors (e.g. magnetometers and pressure sensors). Evaluation units are currently exhibiting <8 °/hr gyro bias instability and <0.05 mg accelerometer bias repeatability across all three axes.
Silicon Sensing is also currently engaged in development of a MEMS High Performance IMU (HPIMU); DMU30, which is slated for customer evaluation units in spring 2015 and production in the summer of 2015. This unit will integrate the new high performance VSG3QMAX (high ‘Q’) inductive resonating ring gyro technology together with the capacitive MEMS accelerometers. The entire assembly will be sealed in a metalized housing and ISA block. The DMU30 is being designed with flexibility and customization in mind to accommodate the end-user’s interface and performance requirements.
(As published in the September 2014 edition of Marine Technology Reporter - http://www.marinetechnologynews.com/Magazine)
Read High Precision MEMS Silicon Sensing Inertial Sensors and Systems in Pdf, Flash or Html5 edition of July 2014 Marine Technology
Other stories from July 2014 issue
Content
- MTR100: All American Marine page: 8
- MTR100: Aquatec House page: 8
- MTR100: Applanix page: 8
- MTR100: AXSUB Inc. page: 10
- MTR100: AXYS Technologies Inc. page: 10
- MTR100: Cal Dive International page: 12
- MTR100: C&C Technologies page: 12
- MTR100: Caley Ocean Systems page: 12
- MTR100: JW Fishers Mfg. page: 12
- MTR 100: Teledyne Marine Acoustic Imaging Group page: 14
- MTR 100: SeaBotix page: 16
- MTR 100: ACSA page: 17
- MTR 100: BIRNS, Inc. - Celebrating 60 Years page: 18
- MTR 100: Catalina Sea Ranch page: 18
- MTR 100: DeepSea Power & Light page: 20
- MTR 100: Franatech GmbH page: 20
- MTR 100: IP Subsea page: 20
- MTR 100: Battelle page: 21
- MTR 100: EdgeTech page: 22
- MTR 100: Cygnus Instruments, Inc. page: 22
- MTR 100: McMillan Design, Inc. page: 23
- MTR 100: Prometheus Inc. page: 24
- MTR 100: Novacavi page: 24
- MTR 100: James Fisher Mass Flow Excavation page: 24
- MTR 100: Falmouth Scientific, Inc. page: 25
- MTR 100: ROMOR Ocean Solutions page: 26
- MTR 100: Bibby Offshore page: 26
- RDSEA International, Inc. page: 28
- Bluefin Robotics page: 29
- Imagenex Technology Corp. page: 30
- INNOVASUB page: 30
- Rowe Technologies page: 32
- Seafloor Systems Inc. page: 32
- Kongsberg Maritime page: 33
- L-3 Communications Klein Associates, Inc. page: 34
- Kraken Sonar Systems Inc. page: 34
- LinkQuest, Inc. page: 35
- MTR 100: Teledyne Marine Systems Group page: 36
- MTR 100: Caris page: 38
- MTR 100: Greensea Systems Inc. page: 39
- MTR 100: Hypack page: 39
- MTR 100: Makai Ocean Engineering page: 40
- MTR 100: Planet OS page: 42
- MTR 100: QPS page: 43
- Getting Defensive page: 44
- MTR100: The Norway Way page: 50
- MTR 100: Maritime Training & Competence Solutions page: 62
- MTR 100: MMT page: 62
- High Precision MEMS Silicon Sensing Inertial Sensors and Systems page: 62
- MTR 100: The Oceanscience Group page: 63
- MTR 100: Ulstein page: 64
- MTR 100: Wachs Subsea LLC page: 65
- MTR 100: Xsens page: 65
- MTR 100: Liquid Robotics Inc. page: 66
- MTR 100: Polarcus page: 66
- MTR 100: Sensor Technology Ltd. page: 67
- MTR 100: OceanServer Technology, Inc. page: 68
- MTR 100: SBG Systems page: 68
- MTR 100: Ohmsett page: 69
- MTR 100: MacArtney Underwater Technology Group page: 70
- CTI SonarWiz page: 70
- SonarPro Now with Language Options page: 70
- High Resolution Data Logging page: 70
- MTR 100: Think Sensor Research Inc. page: 71
- DANTE’s Solar PowerPak Makes Debut page: 71
- Turner Designs Launches Chlorophyll Sensor page: 71
- MTR 100: Sonardyne International Ltd. page: 72
- MTR 100: SL Hydrospheric page: 73
- MTR 100: Valeport Ltd. page: 73
- Gemini Profiling Sonars for STR page: 73
- Rowe Adds New DVL to SeaPILOT Line page: 73
- MTR 100: Black Rock Tidal Power - a SCHOTTEL subsidiary page: 74
- SS260 Series Deep Blue Vector page: 74
- MTR 100: Saab Seaeye Ltd page: 75
- MTR 100: Shark Marine Technologies page: 76
- MTR 100: SeeByte page: 76
- MTR 100: Texas A&M University at Galveston page: 77
- MTR 100: Southwest Electronic Energy page: 77
- MTR 100: Royal Dutch Shell page: 78
- MTR 100: SeaView Systems Inc. page: 80
- MTR 100: SEA CON page: 80
- MTR 100: Teledyne Marine Interconnect Solutions page: 82
- MTR 100: Unique Maritime Group page: 86
- MTR 100: Turner Designs page: 86
- MTR 100: Tritech International Limited page: 87
- MTR 100: Hydroid page: 88
- MTR 100: Fischer Connectors page: 89
- MTR 100: Forum Energy Technologies, Inc. page: 89
- MTR 100: Silicon Sensing Systems Ltd. page: 90
- MTR 100: Digital Edge Subsea page: 90