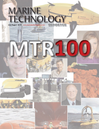
MTR 100: Royal Dutch Shell
Courtesy of its investment in the world’s first Floating liquid natural gas (FLNG) facility, a structure which is longer than four football fields, as heavy as 6 Nimitz-class aircraft carriers and almost as tall as the Taipei 101 skyscraper, costing an estimated $11 to $13 billion and essentially turning the maritime and energy world’s upside down, Royal Dutch Shell PLC earns a much deserved spot on the MTR100.
As Shell moves the LNG processing out to sea, it incorporates more than its fair share of subsea technologies.
FLNG Prelude will measure at 488 x 74 m, and it will clock in at 600,000 tonnes when fully ballasted. The FLNG facility, which is under construction at the Samsung Heavy Industries shipyard in South Korea, will be the largest object ever floated on the ocean. Designed to last 50 years, withstand level 5 cyclone winds and liquefy gas to minus 162 degrees Celsius, it is scheduled to go into service in 2017, spending the next 25 years tapping the Prelude and Concerto gas fields in the Caswell sub-basin of the northern Browse Basin, about 200 km off the coast of Broome, Western Australia. Once in place, it is expected to produce 3.6 MMt/a of LNG, 0.4 MMt/a of LPG and 1.3 MMt/a of gas condensate annually, enough gas to fuel Hong Kong for a year.
Some observers scoff at the idea of using a hugely expensive facility to extract gas from small fields. But one of the beauties of FLNG facilities is that they are mobile and can flit from gas field to gas field, servicing one or many wells at the same time, while pipelines to onshore processing plants are essential tied to one field. Once its targeted field is sucked dry – the expensive pipeline has no further use. The plant can still receive LNG for processing, of course, but at that point it’s coming in on tankers from various distances and the facility will have to be able to accommodate those ships and the necessary offloading process.
Knowing where the gas is, and getting to it, however, are two different things. There are many so called “stranded” deep water gas reserves that have been considered either too small in terms of likely productivity or too far out, to tap into in an economical manner. Factors such as geographical proximity, slowing oil production rates, technological advancement, abundant supply and unprecedented demand growth in Asia point towards a locus of FLNG development in Australian waters, according to Murray Dormer, an analyst with Douglas-Westwood. Douglas-Westwood expects the market for construction of FLNG vessels to increase from $3.7B in the period 2007-2013 to $64.4B over 2014-2020, according to its report, “World FLNG Forecast.”
As its name implies, the Prelude won’t be alone for long. Nor will it remain the world’s largest floating offshore facility. There are at least three other similar projects following in its wake. One of these, from Exxon, and others in the planning stages at Shell, will pump up the size equation even more.
Competitors include:
• Exxon in partnership with BHP Billiton is looking to install what would be the world’s largest FLNG - a 495 meters (1,624 feet) long facility - in its Scarborough gas field off the Australian coast. Design specs call for it to produce an estimated 6 million to 7 million mt/year of LNG from five trains, and to hold 10 storage tanks with a capacity of 380,000 cubic meters.
• Malaysia’s PETRONAS plans to launch an FLNG plant in 2015, and has already announced plans for a second FLNG plant. It’s PFLNG 1 is expected to be the first such facility in operation, beating Prelude by two years. It will be 365 meters long, about 60 meters wide, weigh approximately 125,000t when fully loaded and is expected to produce 1.5 million tonnes of LNG per year.
• GDF Suez of France and Santos, which are looking to put an FLNG plant in the the Bonaparte project off northern Australia.
Before Shell can hope to reap FLNG’s many anticipated advantages, it must first surmount some very big challenges, not the least of which is force-fitting an entire LNG processing plant onto what some have likened as a “barge” in the middle of the ocean.
Shell had to find a way to adapt its shore-based technology for a much smaller, floating platform. This was solved in part by stacking components on deck vertically to save space.
A related solution kills two birds with one stone. Shell plans to eliminate the need for some components on deck by extending eight 1-meter-diameter pipes to a depth of 150 meters, in order to pump frigid seawater up to help cool the gas – 50 million liters (50,000 cubic meters an hour.)
Among other challenges, there’s the fact that Prelude will be sitting out in the middle of nowhere in cyclone alley central. Shell has no intentions of untethering the facility every time a bad wind blows and towing it to shore. Instead, a number of factors are supposed to ensure that Prelude sits tight in savage seas. First there is its sheer size and weight. But more important, Gilmour claims Prelude’s mooring system can stay on station even in the face of a category 5 hurricane.
Four groups of mooring lines will be attached to the world’s largest (93 meters) mooring turret on one end, anchoring the facility, via connections to suction pile anchors, to the ocean floor on the other. The swiveling turret turns slowly with the wind, reducing the impact of water and weather conditions. The links in the record-setting mooring chains are said to be large enough to stand inside of .
Meanwhile, the offloading of LNG onto an LNG carrier required the design of a special loading arm system with swivel joints and quick connect/disconnect flanges, capable of offloading both LNG and LPG.
How It Works
The Prelude plant will include 7 wells, four flow lines approximately 4 km in length, umbilicals and flexible risers, as well as the FLNG facility. The management of subsea wells and manifolds is carried out via the umbilicals, which are connected to a control rom. The plant itself is comprised of liquefaction units, production storage (with capacity of 436,000 cubic meters of LNG, plus LPG condensate) and loading facilities, utility systems, control room, maintenance facilities and accommodation. It will sit on top of the gas field where a series of wells will feed gas and condensate from the reservoirs via four flexible risers into the facility that will draw gas up into the turret for processing.
Next, the LNG has to be separated from a mix that included condensate, LPG, water and CO2. After which the LNG will be liquefied, using Shell’s Dual Mixed Refrigerant (DMR) process, which uses steam-driven refrigerant compressors and ultra-cold seawater to chill the gas to –162°C, shrinking the volume by 600 times. Stored in tanks in the hull with an overall capacity of over 430 million liters (114 million US gal), it will be transferred by special loading cryogenic arms to tankers moored next to the facility.
(As published in the July/Aug 2014 edition of Marine Technology Reporter - http://www.marinetechnologynews.com/Magazine)
Other stories from July 2014 issue
Content
- MTR100: All American Marine page: 8
- MTR100: Aquatec House page: 8
- MTR100: Applanix page: 8
- MTR100: AXSUB Inc. page: 10
- MTR100: AXYS Technologies Inc. page: 10
- MTR100: Cal Dive International page: 12
- MTR100: C&C Technologies page: 12
- MTR100: Caley Ocean Systems page: 12
- MTR100: JW Fishers Mfg. page: 12
- MTR 100: Teledyne Marine Acoustic Imaging Group page: 14
- MTR 100: SeaBotix page: 16
- MTR 100: ACSA page: 17
- MTR 100: BIRNS, Inc. - Celebrating 60 Years page: 18
- MTR 100: Catalina Sea Ranch page: 18
- MTR 100: DeepSea Power & Light page: 20
- MTR 100: Franatech GmbH page: 20
- MTR 100: IP Subsea page: 20
- MTR 100: Battelle page: 21
- MTR 100: EdgeTech page: 22
- MTR 100: Cygnus Instruments, Inc. page: 22
- MTR 100: McMillan Design, Inc. page: 23
- MTR 100: Prometheus Inc. page: 24
- MTR 100: Novacavi page: 24
- MTR 100: James Fisher Mass Flow Excavation page: 24
- MTR 100: Falmouth Scientific, Inc. page: 25
- MTR 100: ROMOR Ocean Solutions page: 26
- MTR 100: Bibby Offshore page: 26
- RDSEA International, Inc. page: 28
- Bluefin Robotics page: 29
- Imagenex Technology Corp. page: 30
- INNOVASUB page: 30
- Rowe Technologies page: 32
- Seafloor Systems Inc. page: 32
- Kongsberg Maritime page: 33
- L-3 Communications Klein Associates, Inc. page: 34
- Kraken Sonar Systems Inc. page: 34
- LinkQuest, Inc. page: 35
- MTR 100: Teledyne Marine Systems Group page: 36
- MTR 100: Caris page: 38
- MTR 100: Greensea Systems Inc. page: 39
- MTR 100: Hypack page: 39
- MTR 100: Makai Ocean Engineering page: 40
- MTR 100: Planet OS page: 42
- MTR 100: QPS page: 43
- Getting Defensive page: 44
- MTR100: The Norway Way page: 50
- MTR 100: Maritime Training & Competence Solutions page: 62
- MTR 100: MMT page: 62
- High Precision MEMS Silicon Sensing Inertial Sensors and Systems page: 62
- MTR 100: The Oceanscience Group page: 63
- MTR 100: Ulstein page: 64
- MTR 100: Wachs Subsea LLC page: 65
- MTR 100: Xsens page: 65
- MTR 100: Liquid Robotics Inc. page: 66
- MTR 100: Polarcus page: 66
- MTR 100: Sensor Technology Ltd. page: 67
- MTR 100: OceanServer Technology, Inc. page: 68
- MTR 100: SBG Systems page: 68
- MTR 100: Ohmsett page: 69
- MTR 100: MacArtney Underwater Technology Group page: 70
- CTI SonarWiz page: 70
- SonarPro Now with Language Options page: 70
- High Resolution Data Logging page: 70
- MTR 100: Think Sensor Research Inc. page: 71
- DANTE’s Solar PowerPak Makes Debut page: 71
- Turner Designs Launches Chlorophyll Sensor page: 71
- MTR 100: Sonardyne International Ltd. page: 72
- MTR 100: SL Hydrospheric page: 73
- MTR 100: Valeport Ltd. page: 73
- Gemini Profiling Sonars for STR page: 73
- Rowe Adds New DVL to SeaPILOT Line page: 73
- MTR 100: Black Rock Tidal Power - a SCHOTTEL subsidiary page: 74
- SS260 Series Deep Blue Vector page: 74
- MTR 100: Saab Seaeye Ltd page: 75
- MTR 100: Shark Marine Technologies page: 76
- MTR 100: SeeByte page: 76
- MTR 100: Texas A&M University at Galveston page: 77
- MTR 100: Southwest Electronic Energy page: 77
- MTR 100: Royal Dutch Shell page: 78
- MTR 100: SeaView Systems Inc. page: 80
- MTR 100: SEA CON page: 80
- MTR 100: Teledyne Marine Interconnect Solutions page: 82
- MTR 100: Unique Maritime Group page: 86
- MTR 100: Turner Designs page: 86
- MTR 100: Tritech International Limited page: 87
- MTR 100: Hydroid page: 88
- MTR 100: Fischer Connectors page: 89
- MTR 100: Forum Energy Technologies, Inc. page: 89
- MTR 100: Silicon Sensing Systems Ltd. page: 90
- MTR 100: Digital Edge Subsea page: 90