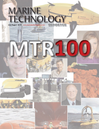
MTR 100: Teledyne Marine Interconnect Solutions
Describe the companies in your group, citing examples of your group collaboration.
Teledyne Oil & Gas consists of Cormon, DGO, Impulse, PDM, ODI, Storm Cable and VariSystems. This synergistic collection of product lines formed from Teledyne companies with 13 locations around the globe. They work in symphony to provide a broad range of power and data transmission interconnect solution options from terrestrial and topside applications to littoral and deep ocean environments. Applications include demanding explosion proof systems, dry-mate submersible instrument and vehicle harnesses, high differential pressure penetrations, and connections to wet-mate electrical and hybrid jumpers for high reliability long performance life in deep ocean.
In a single ocean observatory distributed sensor network, the Teledyne Oil & Gas organization via the Teledyne Marine Interconnect Solutions (TMIS) vertical market provides the backbone for power and communications transmission enabling interconnect from the shore station all the way through to the most remote deployed sensors in the system. This begins with shore station equipment networking cable and molded harness assemblies, moving to the cable termination assemblies at the backbone to power node junction. The TMIS kit in the CTA moves the raw power and optical through the power and optical conditioning equipment with high reliability subsea wet-mate power connectors and wet-mate optical connectors and provides the transmission capability at the output into the network. The wet-mate hybrid connections on the back end of the CTF provide the sole path of power and communications out to the secondary nodes or SIIMs (Science Instrumentation Interface Modules) allowing for long distance data transmission to a network of modularly expandable sensors deployed in wide area networks on the ocean floor in deep water. These science instruments are powered through dry-mate submersible to wet-mate Ethernet transmission jumpers that allow for the wet configuration that enables high bandwidth data transfer and unlimited reconfiguration, upgrades, and modular expansion. One hundred percent of the world’s modern ocean observing systems are using Teledyne Marine Interconnect Solutions technology. The reliability is driven by the partnership between Teledyne Scientific Corporation (formerly Rockwell Scientific Materials Laboratory) and the Teledyne Oil & Gas Technology Development Center to meld science and engineering practice. Together they design and verify long performance life reliability through a structured program of qualification of materials systems, component designs and systems exposed to combined stress analysis in simulated ocean conditions to provide accelerated aging life performance metrics. All are tested to failure to create a true understanding of the mechanisms, time and conditions to create robust solutions for high reliability survival in harsh environments. In addition, the harsh operating environment of the deck systems and the ROV deployment vehicles and systems themselves require high reliability interconnect harnesses to power and transmit data to and from the many instruments in the deployment operations.
What is your group’s most exciting technology advancement since MTR 100 2013?
The size, breadth and depth of the world’s oil & gas production fields, along with the need for more advanced communication from the expanding network of health management sensors, has driven an investment in new product development at Teledyne Oil & Gas. Our solutions focus on complex challenges for subsea power and data transmission to meet new requirements for enhanced oil recovery and subsea processing capabilities. The ocean science community directly benefits from the technology outputs funded by the major oil & gas operators. The most exciting recent examples of this new technology include the development of “Active Flying Leads” which describes an expanding family of ruggedized wet and dry-mate jumper assemblies that can expand the length of sensor deployments beyond the ranges available just a few short years ago. This is achieved through the use of a qualified set of subsea repeater systems and miniature subsea media converters combined with application specific cabling for high integrity data transmission across very long distances. E2FL (Extended Ethernet Flying Leads) surpass the length of deployment distances for reliable Ethernet transmission from the 70 meters available just years ago to a full 100 meter lengths using special Ethernet cables. Up to 300 meters is accomplished by using recently qualified repeater systems and to a distance of up to 10 kilometers using recently subsea qualified miniature E/O media converters in symphony with electrical Ethernet connectors and hybrid cable systems. CAB Bus transmission systems are available in similar configurations designed to follow the qualification path and utilizing component housing developed for the Ethernet systems. These advances enable ocean bottom instruments to be deployed at great distances from the SIIMs and nodes to allow scientists to observe organisms in an environment free of the distractions of manmade structures, a reality that has frustrated scientists for many years in this market.
What market trends are fueling your group?
Our primary market, oil and gas production and exploration is driving trends for higher subsea power and more advanced levels of data transmission due to emerging legislation requiring higher yields for production from existing fields in order to earn new leases. These conditions introduce challenges that until recently were determined as too expensive to feasibly tackle. Increased production yields requires a greater understanding of the evolving conditions of the reservoirs, which in turn demands greater and more capable sensors, such as dense networks fixed seismic life of field networks, requiring more transmission bandwidth. Additional challenges for maintaining and increasing pressure in the well reservoirs, is driving the need for high power subsea motors and pumps to re-pressurize the wells to increase production flow. These systems require high power wet-mate connectivity for long life reconfiguration and high pressure differential / high temperature differential penetrations in order to make meeting these new requirements possible.
Teledyne has grown tremendously in recent years via acquisition, a strategy we have covered in our pages previously. What are the advantages? What are the challenges?
The benefit provided through the Teledyne Marine Interconnect Systems and Teledyne Oil and Gas is the synergy delivered through a cohesive group of aligned product lines that provides a powerful level of reliability and security of supply to our customer community. The ability to construct a contract with a single PO, with a single set of terms and a single warranty across a mix of what was once seven companies requiring separate contracts and contract management is a powerful differentiator for our customer base. Simply having a total interconnect harness consisting of components from a single organization is a concept unheard of just five years ago. It lowers operational risk and reduces instances associated with assigning warranty that have until now been a nuisance and a normal fact of life. The immediate access to broad levels of expertise in technology available through the expansive network of Teledyne companies in and beyond the market place is very powerful in identifying and generating engineered solutions to complex challenges for our customer base. The challenges are manifested in maintaining the lines and aisles of communication between Teledyne consolidated business units and the teams that are calling on the same customer base offering various and differing parts of an overall solution. At Teledyne, we are investing in awareness training and networking among the teams to understand how to recognize applications where our sister organizations have technology and skill sets that are a match to our customers challenges. We grow better in this area each and every day through combined exhibits at conferences, cooperation with presentations at sales and technology training events and through friendly camaraderie.
Teledyne DGO
DGO incorporates the unmatched reliability of glass to-metal seals into electrical and optical penetrators and interconnect solutions for harsh environments. In the over 1 million solutions delivered since 1962, these seals have never failed to maintain pressure integrity. Combining this capability with strong design, material and process controls, DGO delivers interconnect, penetrator and high pressure/high temperature feedthrough solutions with the greatest level of long-term reliability for high pressure and/or high temperature applications.
Teledyne Impulse
Impulse designs and manufactures highly reliable electrical and optical interconnection systems for a broad range of harsh environment applications. Impulse’s proven dry mate, splash mate, wet mate, and custom interconnect solutions are complemented by unsurpassed customer satisfaction, quality assurance and rapid response. Impulse provides engineering, flexible manufacturing process and dedicated customer support. Impulse-PDM in Alton specializes in complex molding technology in polyurethane and polyethylene for cable assemblies, complex sealing mold designs and molded bend restrictors.
Teledyne ODI
ODI is a leader in subsea power and broadband data transmission interconnect systems. ODI’s wet mate connectors include signal and high-power electrical, fiber optic and hybrid electro-optical products. All are based on patented oil-filled, pressure-balanced technology. Companion dry mate submersible connectors complement these wet mate lines. These rugged components can be used at any ocean depth and in the harshest environments.
Teledyne Storm Cable
Storm Cable delivers engineered application specific multi-core cable and complex over-molded interconnect assemblies/harnesses requiring rugged performance in harsh environments.
(As published in the July/Aug 2014 edition of Marine Technology Reporter - http://www.marinetechnologynews.com/Magazine)
Other stories from July 2014 issue
Content
- MTR100: All American Marine page: 8
- MTR100: Aquatec House page: 8
- MTR100: Applanix page: 8
- MTR100: AXSUB Inc. page: 10
- MTR100: AXYS Technologies Inc. page: 10
- MTR100: Cal Dive International page: 12
- MTR100: C&C Technologies page: 12
- MTR100: Caley Ocean Systems page: 12
- MTR100: JW Fishers Mfg. page: 12
- MTR 100: Teledyne Marine Acoustic Imaging Group page: 14
- MTR 100: SeaBotix page: 16
- MTR 100: ACSA page: 17
- MTR 100: BIRNS, Inc. - Celebrating 60 Years page: 18
- MTR 100: Catalina Sea Ranch page: 18
- MTR 100: DeepSea Power & Light page: 20
- MTR 100: Franatech GmbH page: 20
- MTR 100: IP Subsea page: 20
- MTR 100: Battelle page: 21
- MTR 100: EdgeTech page: 22
- MTR 100: Cygnus Instruments, Inc. page: 22
- MTR 100: McMillan Design, Inc. page: 23
- MTR 100: Prometheus Inc. page: 24
- MTR 100: Novacavi page: 24
- MTR 100: James Fisher Mass Flow Excavation page: 24
- MTR 100: Falmouth Scientific, Inc. page: 25
- MTR 100: ROMOR Ocean Solutions page: 26
- MTR 100: Bibby Offshore page: 26
- RDSEA International, Inc. page: 28
- Bluefin Robotics page: 29
- Imagenex Technology Corp. page: 30
- INNOVASUB page: 30
- Rowe Technologies page: 32
- Seafloor Systems Inc. page: 32
- Kongsberg Maritime page: 33
- L-3 Communications Klein Associates, Inc. page: 34
- Kraken Sonar Systems Inc. page: 34
- LinkQuest, Inc. page: 35
- MTR 100: Teledyne Marine Systems Group page: 36
- MTR 100: Caris page: 38
- MTR 100: Greensea Systems Inc. page: 39
- MTR 100: Hypack page: 39
- MTR 100: Makai Ocean Engineering page: 40
- MTR 100: Planet OS page: 42
- MTR 100: QPS page: 43
- Getting Defensive page: 44
- MTR100: The Norway Way page: 50
- MTR 100: Maritime Training & Competence Solutions page: 62
- MTR 100: MMT page: 62
- High Precision MEMS Silicon Sensing Inertial Sensors and Systems page: 62
- MTR 100: The Oceanscience Group page: 63
- MTR 100: Ulstein page: 64
- MTR 100: Wachs Subsea LLC page: 65
- MTR 100: Xsens page: 65
- MTR 100: Liquid Robotics Inc. page: 66
- MTR 100: Polarcus page: 66
- MTR 100: Sensor Technology Ltd. page: 67
- MTR 100: OceanServer Technology, Inc. page: 68
- MTR 100: SBG Systems page: 68
- MTR 100: Ohmsett page: 69
- MTR 100: MacArtney Underwater Technology Group page: 70
- CTI SonarWiz page: 70
- SonarPro Now with Language Options page: 70
- High Resolution Data Logging page: 70
- MTR 100: Think Sensor Research Inc. page: 71
- DANTE’s Solar PowerPak Makes Debut page: 71
- Turner Designs Launches Chlorophyll Sensor page: 71
- MTR 100: Sonardyne International Ltd. page: 72
- MTR 100: SL Hydrospheric page: 73
- MTR 100: Valeport Ltd. page: 73
- Gemini Profiling Sonars for STR page: 73
- Rowe Adds New DVL to SeaPILOT Line page: 73
- MTR 100: Black Rock Tidal Power - a SCHOTTEL subsidiary page: 74
- SS260 Series Deep Blue Vector page: 74
- MTR 100: Saab Seaeye Ltd page: 75
- MTR 100: Shark Marine Technologies page: 76
- MTR 100: SeeByte page: 76
- MTR 100: Texas A&M University at Galveston page: 77
- MTR 100: Southwest Electronic Energy page: 77
- MTR 100: Royal Dutch Shell page: 78
- MTR 100: SeaView Systems Inc. page: 80
- MTR 100: SEA CON page: 80
- MTR 100: Teledyne Marine Interconnect Solutions page: 82
- MTR 100: Unique Maritime Group page: 86
- MTR 100: Turner Designs page: 86
- MTR 100: Tritech International Limited page: 87
- MTR 100: Hydroid page: 88
- MTR 100: Fischer Connectors page: 89
- MTR 100: Forum Energy Technologies, Inc. page: 89
- MTR 100: Silicon Sensing Systems Ltd. page: 90
- MTR 100: Digital Edge Subsea page: 90