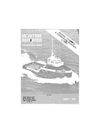
Practical Compliance With Latest USCG and IMCO REGULATIONS
The introduction of IMCO regulations, last amended in 1978, and the publication of USCG regulations, September 1979, require that all ships calling on U.S. and IMCO nations' ports will be required to comply with these regulations by the specified dates.
In the U.S. this date is June 1, 1981. IMCO will be implemented two years after ratification, however, several member nations have already required implementation.
For new ship construction, the regulations are specific and compliance offers no particular problem since initial ship designs will integrate the required changes.
However, for existing ships, compliance requires complex modifications.
The regulations allow several options for compliance, which gives the operator some leeway.
For example, for tankers over 70,000 dwt, the owner has the option of converting the ship to a segregated or clean ballast tanker or installing a crude oil washing system in the cargo tanks. Obviously, economics will direct the approach. The most difficult portion of this will be to predict accurately the future utilization of the ship, i.e.: trade routes, charters, guaranteed pumping rates, fuel costs and fuel availability.
However, in order for timely compliance with regulations decisions must be made based upon best estimates. This paper outlines some of the methods which can be utilized, which factors are important and how to best comply with the regulations.
The regulations apply to all ships in the applicable tonnage categories. However, ships other than tankers can usually comply with minor additions of equipment and modifications.
The Intergovernmental Maritime Consultative Organization (IMCO) has published standards and regulations which form the basis of the U.S. as well as each member nation's regulatory policy.
The U.S. regulations are nearly identical to those of IMCO and are published in the Code of Federal Regulations and are administered by the U.S. Coast Guard.
Alternatives Existing tankers over 40,000 dwt must have either Crude Oil Washing (COW) or Segregated Ballast Tanks (SBT). Clean Ballast Tanker (CBT) is allowed until June 1, 1985 for 40,000 to 70,000-dwt crude carriers or until June 1, 1983 for 70,000-dwt crude carriers. This allows an operator to plan future modifications for the newer ships or a planned phase-out of older ships.
For existing VLCCs or ULCCs, there usually is an obvious choice of only COW. Most of the more modern ships already have a COW system installed even though it probably does not meet IMCO or USCG requirements. To upgrade an existing COW system is usually the best alternative.
Those ships with no COW system are more difficult to convert to COW, especially tankers with deepwell pumping systems. Additionally, ships with COW systems must have an Inert Gas System (IGS). Should an existing ship not have IGS, the additional cost of an IGS installation may direct a different approach.
It is imperative that before a decision is made for each vessel, a complete economic analysis be performed which includes the trade routes, cargo revenue and operating costs as well as conversion options. In each case, the life expectancy of the ship and the guaranteed pumping rate of the charter are additional factors to consider.
System Selection Owners of vessels in the charter business (and fleet operators) are interested in modifications which will not affect the charter rate of the vessel and which will allow the vessel to operate in a variety of trade routes and have the capability to carry different types of cargo on different voyages.
The time frame in which these modifications can be carried out is also very important. The USCG date may affect the vessel's operation in an existing charter. The law allows no provisions for granting extensions to these dates for compliance with the regulations.
Recent amendments to the regulations, from the November 1980 IMCO meeting, allow owners to switch the trade of the vessel, i.e., from a product carrier to a crude carrier, without recertification.
This allows an owner to operate a vessel in the crude trade on one voyage and in the product trade on the return leg of the voyage without recertification.
Under these conditions, a ship must comply with the ballast system regulations for each trade.
Ballast Systems A permanent ballast system is an alternative to meet the regulations.
The ballast system consists of designated tanks and associated piping systems to carry ballast only, and all other remaining tanks are used for cargo.
The selection and arrangement of tanks for ballast use is primarily based on the amount of ballast needed to meet the draft and trim requirements of the regulations and the size and the number of tanks on the vessel.
These requirements, along with the vessel's bending and shear limitations, determine the possible ballast tank arrangement. It is apparent that a vessel with a large number of tank divisions will have more possible tank arrangements available.
The final arrangement of tanks can be based upon the alternatives of pumping and piping arrangements and the trade in which the vessel will operate in the future. This arrangement must be submitted to regulatory bodies for approval.
There are basically two types of ballast systems, clean ballast tanker and segregated ballast tanker. It should be noted, however, that a CBT system is a means of compliance for a temporary period of time.
In a clean ballast system, it is possible to isolate one of the existing cargo-oil pumps and suction lines such that it may be used for ballast. This may require small piping modifications both in the cargo tanks and in the pump room. The modifications will consist of connecting and breaking pipe connections and installing valves for the double valve isolation. The disadvantage of this system is that the cargo pumping capacity will be reduced with one pump used for ballast.
This arrangement will, however, accommodate cargo pumping and ballasting operations simultaneously.
A segregated ballast system will require the installation of an additional pump specifically designated for ballast service. Placement of the new pump is dependent on available space in the pump room and/or machinery space.
With a pump located in the pump room and its driver in the machinery space, a new ballast main is installed through the cargo tanks. This new ballast main services the designated ballast tanks.
Any existing cargo lines servicing the designated ballast tanks will be removed or blanked.
The owner also has the option of installing a pump and driver in the machinery space. With the pump in this location, a main line can be run to the upper deck servicing the ballast tanks.
It should be noted that the use of line blinds for segregation of ballast from oil is not acceptable.
A positive break in the system is required with stored spool pieces which would be used for specific emergencies.
Crude-Oil Washing Crude-oil washing is another alternative for compliance with the regulations.
A COW system basically consists of a number of fixed tankcleaning machines in which crude oil is directed at a high pressure and velocity at the sides and There's a new focus at Sun Ship. After 60 years in the shipbuilding business, Sun Ship is now concentrating all of its resources on the repair and conversion of ships.
And our resources are considerable: a very experienced workforce and some of the best facilities on the East Coast, including five piers, a large floating dry dock, two 1100-ft. outfitting piers, an 800-ton floating derrick, t wo 250-ton gantry cranes, many types of shops and labs, plus much more.
structure of the cargo tanks to remove the waxy asphaltic deposits that build up from the voyage.
The tank-cleaning machines used in these operations either have a programmed pattern or have a selective program option to the pattern. The tank-cleaning machines are supplied by a main line that is connected to the discharge side of the cargo pumps, either in the pump room or on the upper deck (sometimes supplied from the cargo manifolds).
We can do short-term repairs, major repairs and conversions.
And we can do them fast. We're the ones who converted the tanker S.S. MANHATTAN to an ice-breaking tanker in only eight months. We've even stretched vessels by adding sections amidships.
Our dry dock capabilities —up to 70,000 tons with a 197-ft.
beam—let us lift almost any ship clear of the water for major structural or hull repairs.
So if you want a ship put in shape, come to Sun Ship. We've got what it takes to get the job The number and placement of the COW tank-cleaning machines is determined by the computation of shadowed areas in the tanks.
Shadows are those which do not receive a direct impingement from the tank-cleaning machines.
The amount of shadowed areas allowed, as stated in the Regulations, is 10 percent for horizontal surfaces and 15 percent for vertical surfaces.
As essential to the satisfactory placement of COW tank-cleaning machines is the design and installation of a tank stripping system which is capable of maintaining the tank bottom free of standing oil during the tank cleaning operation. It has been the practice of many owners to increase the tank stripping capability of the vessel. An increased capability in the tank stripping system will allow for the simultaneous operation of a greater number of tank-cleaning machines, thereby reducing total tank cleaning cleaning and terminal time.
One application utilizes a constant- pressure regulating valve to reduce any pressure surges that may be caused by stopping the tank-cleaning machines. Also, the use of this valve may decrease the terminal time of the vessel due to additional shore discharge of cargo which is not needed for COW operations.
On the ballast leg of the voyage, the clean-ballast-designated tanks are crude washed and water rinsed prior to receiving clean ballast. Dirty ballast (departure and/or emergency) is discharged in accordance with the regulations without regard to tank washings.
Inert Gas Systems The Inert Gas System require- ments of the regulations requires modifications to the system.
An inert gas system directs flue gas from existing boilers (or from an inert gas generator) through a scrubber unit, blower, and pressure regulating valve to suitable distribution piping located on the upper deck. A deck water seal is also included in the system. The IGS system must maintain an oxygen content of less than 5 percent in gas.
One major area of importance in the design of the system is the consideration of what type of materials should be used for the components in the system. This is due to the corrosive nature of the gas. Some owners have opted to use reinforced thermosetting resin type piping in the distribution system. It should be noted that the use of this piping has not yet been approved by all regulatory bodies.
Another major concern is that the system is designed to maintain a positive pressure in the cargo tanks, e s p e c i a l l y during cargo pumping and COW operations.
The venting arrangement is extremely important.
Costs and Conclusions The following costs for modifications of existing ships can be used as a guide in estimating future modifications. Each ship will be different due to its particular configuration.
Inert gas installations, for existing tankers, are in the vicinity of $1,000,000 per ship for a 100,- 000-dwt crude carrier.
Crude oil wash system installation for a 280,000-dwt crude carrier should cost $600,000 to $1,000,000. However, most recently constructed VLCC and ULCC vessels have an existing COW system which probably does not meet regulatory body requirements.
A typical modification requiring additional fixed deck machines, some submerged machines, new piping and a modified s t r i p p i n g system would cost $300,000 to $400,000.
For a deepwell-pump-type tanker, the cost will increase due to the necessity of providing improved stripping capability.
For existing tankers, 150,000- dwt, installation of a segregated ballast tank system with new piping, a new pump and electrical modifications might cost $500,000 to $600,000. For an 80,000-dwt tanker, the modification of an existing system to a dedicated clean ballast tank system, including isolation of one of the existing cargo pumping systems for use in the CBT, will cost approximately $150,000.
It is then obvious that the costs are considerable and are an important factor in the decision of which approach to take. However, it is imperative to evaluate the entire regulatory requirement and operational profile as well as the expected life and utilization of each ship before undertaking the modernization of the ship.
Other stories from August 1981 issue
Content
- 143 Ships In Five-Year Naval Shipbuilding Plan page: 4
- R.A. Simpson Promoted To N e w l y Created VP Post At Crowley Division page: 4
- Lehman Joins Bultema M a r i n e Transportation page: 5
- Southwest Marine Purchases San Pedro Y a r d From Beth Steel page: 5
- Navire Cargo Gear Wins Kuwait Linkspan Contract page: 6
- Detroit Diesel Engines Commercial Marine Models —Brochure Available page: 6
- Tracor Marine Salvages 500-Ton Restaurant Vessel page: 6
- Walz & Krenzer Conveyor Belt Doors Solve Problem On New Keystone Collier page: 6
- Halter Delivers Two Crewboats For Offshore Service In California page: 6
- Valmet Yard To Build Feeder Type Barge Carriers For Soviets page: 7
- CDS Awarded Chestnut Sh ipping To Retrofit Tanker At Northwest Marine page: 7
- Racal-Decca Marine Expands U.S. Operations page: 7
- Phoenix Management Rig To Be Built By Bethlehem Sparrows Point page: 7
- John Manly Shipyard Delivers MTU-Powered Patrol Vessel page: 8
- Twin City Barge To Acquire Transload And Transport, Inc. page: 8
- $70.8-Million Conversion Contract Awarded AMSHIP page: 8
- 34 Ways For Tugs To Assist Tanker—Test Results Available page: 9
- Bender Shipyard Builds Own Floating Drydock page: 9
- $1.5-Million Tanker Contract Signed By Halifax Shipyards page: 9
- Nordquist Appointed At Twin Disc, Inc. page: 9
- First Of A New Hybrid Line From Halter page: 10
- SNAME Chesapeake Section Hears Landing Craft And Steering Gear Papers page: 10
- J Storm XVI Is 50th Jackup Commissioned At Bethlehem, Beaumont page: 10
- Inert Gas Generators To Operate On #6 Oil —Literature Available page: 10
- $326-MiIIion Order For 8 Rigs Awarded To Marathon Manufacturing page: 12
- HAC Names Lauth VP Technical And Nautical page: 12
- Three Key Appointments Announced In Marine Department At Texaco page: 12
- Chromalloy Acquires Flowers Marine Group For About $15 Million page: 12
- Tracor Wins $8.3 Million Four-Year Navy Contract page: 12
- McDermott Scotland Is Awarded $150 Million In Offshore Contracts page: 13
- International Paint Enters Korean Coatings Market page: 13
- ITT Mackay To Market Oil Pollution Monitoring Equipment In The U.S. page: 13
- Luquette Sales Manager For Offshore Express page: 13
- W.J. Magratten Joins TOOLTECH As VP, Marketing/Development page: 14
- Two Tuna Seiners Christened At Peterson Builders Yard page: 14
- M / V Jeffboat page: 14
- French Group Purchases Marine Structure Firm page: 15
- New 34-Page Brochure Describes Marathon Offshore Drilling Rigs page: 15
- Mid-Coast Marine Yard Delivers Its First Twin-Screw Tugboat page: 16
- Dravo SteelShip Delivers Coastal Tugboats 'Sioux' And 'Maya' page: 16
- NABRICO Dedicates New Facilities page: 16
- Jos. L. Meyer Shipyard Delivers LPG Carrier Dorothea Schulte page: 17
- $13-Million In Title XI Guarantees Sought For 50 Hopper Barges page: 18
- Du Pont Offers Brochure On Planned Corrosion Control Program page: 18
- W.R. Martyn Appointed Commodity Director-Grain For Dravo Mechling page: 18
- Great Lakes Dredge Is Apparent Low Bidder On $32.9-Million Job page: 19
- Dan Mortimer Elected President Of New Yard —Gulf Coast Fabrication page: 19
- Swiftships Will Build Two Supply Cargo Vessels For L & P Boat Rentals page: 20
- J. Frank Williams Receives N a v y Meritorious Citation page: 20
- Nashville Bridge Delivers Two Integrated Tows To Coastal page: 20
- Tacoma Boat Launches $3.4-Million Oil Test Barge For Sohio Use page: 20
- 33rd Annual Gulf Section Spring Meeting Featured Six Interesting Papers page: 21
- Richard Palk Elected President Of American Trading Transportation page: 22
- $58-Million Navy Order For 8 Oceanographic Systems To Hydroscience page: 22
- Shell Caprinus® R Oil 40 Meets Requirements Of Auxiliary Engines page: 22
- Offshore Express In $10-Million Expansion- 'Lightning Express1 Delivered By Progressive Shipbuilders page: 22
- Another Panamax Bulker Delivered By B&W Yard To Liberian Owner page: 24
- Hyundai To Build 9 Ships For United Arab Shipping - T o t a l Cost $400 Million page: 24
- Paper On Adaptive Steering Module Available From Sperry page: 25
- $33-Million Ore Handling Facility Dedicated At Port Of Toledo page: 25
- Westinghouse Awarded $40-Million Order For Navy Generator Sets page: 26
- Hvide Delivers First Two Catug Vessels To Occidental Petroleum page: 26
- 500th Raytheon RAYCAS page: 26
- Brown & Root Promotes Akin, Sides And Muellner page: 26
- Port Of Hamburg Completes Tour Of The United States page: 28
- First Of 3 Rigs For Danish Firm Completed At Hitachi Zosen page: 28
- Geiger Succeeds Zuehlke As President Of Bay Shipbuilding Corp. page: 29
- Hawaii Awarded Major New OTEC Project page: 31
- RCA Service Company Introduces Marine Services Global Network page: 31
- HUDSHIP Delivers Utility Vessel To Gray Mackenzie Marine page: 32
- Bay Shipbuilding Lays Keel For Ocean Barge Corp. Bulk Cargo Barge page: 32
- Racal-Decca Introduces New ARPA Radar System At Whitehall Club Reception page: 32
- IOT Opens New Southern Fleet Center In Tampa page: 34
- Reel-O-Matic Modifies Standard Product For Special Application page: 34
- Bath Iron Works Plans New $46.7-Million Portland Yard page: 34
- $400 Million To Be Spent On Newfoundland Offshore Oil Drilling This Year page: 35
- Bayou Black Shipyard Delivers Cummins-Powered Push Boat To Hillman Marine page: 36
- Panamax Bulker For Greek Owner Delivered By Hitachi Zosen page: 36
- Largest U.S.-Built Tug/Barge Unit Enters Service page: 36
- Burmeister & Wain Shipyard Delivers The M/S Baumare page: 36
- Tacoma Boat $20-Million Debentures To Finance Expansion Program page: 38
- John G. Smith Promoted To General Manager Of Krupp Atlas Electronik page: 38
- Raytheon's 'Sub Sig II' To Provide Sea Trial Support For Electric Boat page: 39
- Lockheed Shipbuilding Awards LSD-41 Contract To J.J. Henry Co., Inc page: 39
- James Sessions Named President At Newpark — Haskew And Lehman Appointed VPs page: 39
- Deutz Producing Air-Cooied Diesels At Richmond Plant- Free Spec Sheets Offered page: 39
- Marine coatings & corrosion control page: 40
- Dravo Acquires Nilo Barge Line From Olin page: 40
- Halifax Industries Ltd. Appoints Kenneth Wood As President And CEO page: 40
- Transamerica Delaval Runs Diesel On Liquid Coal —Report Available page: 41
- Augsburger And Sylvester Promoted At Tenneco page: 42
- Foss To Order New Tugs With Voith Schneider Systems page: 42
- Skagit Offers 130-Page Catalog On Full Line Of Offshore Deck Machinery page: 42
- M/V Ogden Dynachem Christened At Avondale page: 44
- Four Directors Elected At Levingston Industries page: 53
- NABRICO Delivers New Two-Barge Tow To Alabama River Barge page: 53
- New Officers Elected At NCAA National Conference page: 53
- Houston Offshore Takes Delivery Of Two New Rigs, Orders Another page: 63
- General Morris Named President Of National Waterways Foundation page: 64
- Sperry Awarded $51-Million Contract By U.S. Navy For Spanish Combat Systems page: 64
- Swiftships Completing 20-Acre Repair Yard In Freeport, Texas page: 65
- First Of Five For Mexico From MARCO page: 66
- New York Harbor Carriers Association Issues Ten User Charge Guidelines page: 66
- Design Contract Let For New Container Terminal In Port Of Los Angeles page: 70
- Goldston Shipbuilding To Build Supply Vessel For Jackson Marine page: 70
- Bird-Johnson's 100th Controllable Pitch Propeller For U.S. Navy page: 71
- Practical Compliance With Latest USCG and IMCO REGULATIONS page: 72
- Bay Shipbuilding Delivers M/V Columbia Star To Oglebay Norton Company page: 78
- Swiftships Delivers M / V C/Wanderer To Co-Mar Offshore Corporation page: 79
- John K. Stuart Named Fleet Engineer At Oglebay Norton Company page: 80
- Bailey In New Orleans Building Stores Boxes For Five Avondale Tankers page: 80
- Tracor Marine Awarded $1.7-Million Contract For R/V Conrad Overhaul page: 81
- Simrad Track Plotter Extends Loran C Use- Literature Available page: 82
- Armco Offers Bulletin On High Strength, Low Alloy CT Steels page: 82
- Joseph Coco Appointed Controller Of Consolidated Inland Marine page: 82
- ASNE/SNAME Joint Meeting Hears Report On Clearing Of Suez Canal page: 89
- Dravo SteelShip Delivers Two Crane Boats To Weber Marine page: 95