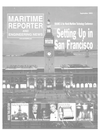
Very Large Systems
Ackerman's study also assumed electric pod drive in his analyses, which also maximized the revenue space made available in the former engine room.
What he did not discuss was the difficulty that conventional electric drive or even direct diesel drive faces at very high power — the larger ships in his study need up to 77-MW of propulsion power, preferably in a single shaft for simplicity. This much power is not available with today's electric drive technology and is also problematic with direct drive diesels, currently the most common propulsion system in modern container ships. A recent issue of Marine Engineers Review suggests that direct-drive diesels may be reaching their practical size limit because of the vibration, heat stress and ship hogging they cause. Here again. HTS motors offer a solution. Because of the high flux densities and gap shear stresses generated by the superconducting field coils, HTS motors follow fundamentally different scaling laws than do conventional motors. HTS motors scale according to a 1/5 (0.2) power rule instead of the conventional 1/3 (0.3) power rule. This means that very high horsepower HTS motors are not much bigger than more moderate-sized HTS motors. For example, a 25-MW 120- rpm will be only 1.4 times dimensionally larger than AMSC's 5-MW HTS motor, despite having five times the power and ten times the torque of the smaller machine. Replacing the diesel with a gas turbine will remove the design limitations created by the diesel engine's great size and weight, HTS technology also greatly improves today's electric ship propulsion systems.
Consider t h e conversion to electric propulsion of the Queen Elizabeth 2 in 1987. The electric propulsion modification designers were constrained by the existing engine room layout and volume in which they could install, leading to the selection of two 44-MW 150-rpm synchronous pancake motors. Each weights about 400 cu. tons and measures about 29.5 ft. (9 m) in width and height and about 20 ft. (6 m) in length. Each motor is so large, and the ship's installation restrictions so severe, that each was built, delivered and installed in quarters — two half stators and two half rotors.
The motors and the other ship's electricity needs are met by nine 10.5-MW medium speed conventional diesel generator sets with a total weight of more than 2,000 tons.
Conversion of the QE2 to electric drive was a remarkable achievement.
The installation has worked well and the ship continues to operate today as the premier transoceanic cruise ship of our time. But what would have been possible if HTS technology were available in 1987? An HTS 36.5-MW motor, developing the identical torque of the QE2 motors, 2.1 million ft.-lbs., would be very much smaller and lighter. Table 2 compares the pair.
The HTS motor would have been far easier to ship to the construction site and install. Further, because the HTS motor is an AC synchronous machine, it can be driven by any conventional synchronous drive, including the technology used on the QE2. Nothing new is needed here.
As to the nine diesel generators, three 36-MW GT HTS generator sets would provide more power, would weigh far less at about 210 tons, and could have been mounted in the superstructure to open up vast areas in the engine room for productive revenue-generating purposes.
Water jet drive motors for large, ultrahigh speed ships are another attractive target for HTS technology. HTS GT generator sets located in the ship's superstructure and HTS electric water jet drive motors below may be an enabling combination for such ships.
HTS motor and generator commercialization is occurring at a rapid rate, prompted by the Navy's marine propulsion motor development contracts and TVA's order of five SuperVAR dynamic synchronous condensers, both involving AMSC. Earlier predictions of significant size and weight benefits, as well as greater efficiency, are being validated through these efforts. Further, no technology shortfalls have been revealed and none are foreseen.
The space, weight, efficiency and quietness advantages of HTS technology can translate directly into unique propulsion system arrangements and more revenue producing space in future passenger and cargo ships, as well as spawn the development of new ship designs of novel hull forms. The benefits to the maritime industry will be profound.
For more information Circle 1 7 6 on Reader Service Card About the Authors Stuart C. Karon is Director, Government Programs and Director, Business Development for the SuperMachines Business Unit at American Superconductor. Formerly a U.S. Navy Officer arid subsequently marketing & sales director in the commercial sector.
Stuart is responsible for structuring effective government-funded R&D and system design/development programs, and for bringing about the business relationships necessary for the American Superconductor Corporation SuperMachines Business Unit to achieve its objectives. For more information, you can reach him at [email protected].
Dr. Swam Kalsi is Director of Advanced Design for the SuperMachines Business Unit at American Superconductor. He has more than 35 years of directly related experience in all aspects of superconducting magnet technology and electrical engineering.
Read Very Large Systems in Pdf, Flash or Html5 edition of September 2003 Maritime Reporter
Other stories from September 2003 issue
Content
- New SWATH From ACMA page: 8
- IZAR Delivers LNG Inigo Tapias page: 10
- Wallace McGeorge Modified for Deep Dredging page: 11
- Careful, Your Species May Be Non-Indigenous page: 12
- U.S. Sub Christened in "Home" Port page: 16
- HSV 2 Swift Delivered to U.S. Navy page: 17
- A Change in Course page: 18
- Univan Reports Steady Growth page: 20
- Payload Pivotal to Fast Sealift Ship page: 24
- The Chairman's Influence on Design page: 24
- The Lure of the Electric Drive page: 26
- Very Large Systems page: 27
- Generators And Synchronous Condensers page: 27
- Cat Power For Unique Boat page: 30
- MAN B&W Flexibility With Two Strokes page: 31
- "Ink" It In: WMTC a Must for Maritime Professionals page: 34
- Guido Perla: Colombian Born, American Made page: 38
- Thrane & Thrane Offers the Capsat Fleet33 page: 42
- SeaWave Family Designed for Ease of Use page: 42
- PGS Geophysical Renews With Telenor page: 43
- Nera F 5 5 Terminal Gets Inmarsat Type Approval page: 44
- Monitoring Technology...Advanced page: 45
- Outlook for Floating Production Systems page: 52
- Meyer Werft Delivers to RCCL page: 57