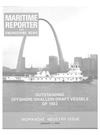
Modern Fuel Systems Symposium
Exchanges Of Experiences—Problems And Solutions—Prove Use Of Heavy Fuels In Medium-Speed Diesel Engines Is Increasing And Economical Two years ago Alfa-Laval, Inc.
of Fort Lee, N.J. sponsored a symposium on modern fuel systems.
This symposium was so successful that a second symposium on the same subject was held recently in St. Louis, Mo. This year's symposium was sponsored by both Alfa- Laval and Diesel Progress. It brought together engine builders, oil companies, shipyards, vessel owners and manufacturers of fueltreatment additives.
The program was oriented to the needs of inland and coastal waterways operators. The topics covered included basic fuel chemistry, fuel purification, additives, fuel blending, heavy-fuel burning, engine design and operating experience.
The following excerpts from the papers presented (in order of presentation) indicate the wide range of thoughts presented, including present and future problems with suggested solutions: Cletus H. Jones, Belcher Oil Company of Miami Fla., presented comments on "The Quality and Availability of Blended Marine Fuels in 1983." He stated that his definition of quality is "if the product does the j ob it was intended to do, that's quality. It may not smell good or look good—the laboratory analysis may indicate major deficiencies, but if it passes the performance test in the engine, it is a quality product." He went on to state: purchasing blended marine fuels has an element of art to it. First of all, insisting on the lowest possible price at all times assures you of one thing—if there is a problem fuel in the market place, you will get your share of the headaches.
Another simple rule is to avoid confusing a fuel-supply specification with an engine specification.
The fuel coming over the rail, in most instances, is not the fuel injected into the combustion chamber.
One is a treated fuel, the other is not. I realize this is basic stuff, but it amazes me how often sophisticated operators buy an expensive grade of blended fuel because, I suspect, they either don't know or don't trust their onboard treatment procedures.
In summary, the current highspeed diesel operator contemplating installation of medium-speed residual-burning diesel engines will have to make some judgement calls on blended-fuel quality and availability. Unlike No. 2 diesel, the specifications for blended fuels are vague and there is a lot of information missing. Progress on testing and the exchange of information is improving, but we still have a way to go.
Alternately, there are operators worldwide successfully using this type of equipment despite the aforementioned shortcomings.
Practically speaking, medium-speed engines are in general use everywhere except the U.S. inland waterways.
Finally, let us keep in mind that the diesel engine originally was conceived to run using pulverized coal as fuel. It is a wonderfully adaptive and forgiving piece of equipment. Certainly in today's technological environment it will work in the heartland of the United States.
Nicholas H. Chavasse, Alfa- Laval, Inc., presented "The Alfa- Laval Line-Up Past and Present." He stated that the Alfa-Laval MAB-103 and MAB-104 are small, manually cleaned centrifuges used today for turbine lube oil and for lube and diesel fuel on small diesel engines. Benefits of the 100 series is that they are inexpensive, easy to install, simple to run, and the controls are simple. The drawbacks to the MAB-100 Series are that they have limited or small capacities and that their sludgeholding capacity is rather limited.
The Alfa-Laval MAB-200 Series of purifiers are similar to the 100 Series but with the following major differences. There are five units available. They are larger both in size and capacity. They have removable sludge liners and selfdraining bowls. They have paring disc pumps built into the bowl for pressurized discharge of the light (oil) phase and all of these give the following benefits: Longer runs between cleaning, easier to clean, and on the larger units (MAB-205 and up) built-on bowl cranes for lifting the bowl top and stack out of the unit and to the side. The benefit of the paring disc pump on the light phase is that back pressure can be applied to the oil outlet if required. The drawbacks to the MAB-200s are that they are more expensive, larger, heavier, still labor intensive if applied to a dirty product and limited in their application to diesel fuel, small engine diesel lube oil, turbine lube oil, hydraulics and other similar applications.
The next step in the Alfa-Laval line of marine purifiers (by-passing the nozzle machines) is the MAPX or MOPX line of self-cleaning purifiers. There are six sizes in the family ranging from the small 204 to the large 313 size unit. The MAPX/MOPX units solve the problems that exist with the MAB Series of units. They can handle just about any type of marine fuel and lube oil application if sized and installed properly and are a tried and proven piece of equipment.
The Alfa-Laval WHPX Series of purifiers, introduced in 1972-73, does not lose any oil in the shoot, requires no pressurized water or hot water, generates less sludge volume and requires less water. It has become the industry standard, and although more expensive than the conventional unit, has a payback in normally less than two years.
Last is the ALCAP FOPX Series of fuel oil purifiers. The FOPX is neither a purifier nor a clarifier but a combination of both is the best way to describe it. The FOPX was developed to solve the problem with the upper limits presently imposed on purifiers, to get rid of the problems presently associated with the gravity rings, to make the centrifuge less sensitive to temperature control, and primarily to give the marine industry a piece of equipment that the operators could feel a little bit happier with.
Nels J. Hendrickson, Drew Chemical Corporation, spoke on "The Role of Chemicals and Fuel Analysis in the Marine Industry." He introduced his subject by stating that "Even though the price, quality and availability of marine fuels have not deteriorated as rapidly as forecasted, there still can be compelling economic reasons for vessel operators to consider burning heavy marine fuels. However, a hasty switch to a lowercost fuel without full consideration for the consequences of the switch to lower-quality fuels on equipment and the need for greater personnel attention and control can have quite the opposite desired cost outcome." The use of fuel additives has taken longer to be accepted than the use of chemicals in other systems and is an area of continued misunderstanding and controversy.
Part of the problem is caused by the large number of additive manufacturers as well as by the lack of proper understanding by operators of the types of additives available and their role. Fuel additives have, however, been used successfully to solve many problems.
Additives have been used in lube oils, as pour point depressants, ash modifiers and demulsifiers, as well as for many other applications. Drew AMEROID'1 Marine's products and services have also expanded and changed from one or two relatively simple products to our extensive present line.
These products are being used worldwide on over 4,000 vessels.
It is our opinion that diesel engines can effectively burn today's fuels and those expected in the near future. This is especially important for operators who are considering burning blended fuels with engines capable of doing so. However, the operator, in order to realize the full cost benefit, must take advantage of the treatment tools available (i.e., fuel analysis, mechanical and chemical treatment).
Ole Schnohr, MAN, B&W, Alpha Propulsion Systems, spoke on "Engines on the River." Basically, the quality of heavy fuel has not really changed since fuels entered the marine market.
Any fuel considered of poor quality today for reasons of high viscosity, high Conradson Carbon content or high content of catalytic fines, etc., could be produced and was actually produced and found on the market in the early days of heavy fuel operation.
In recent years comprehensive test programs have been initiated by the engine industry in order to meet the challenge presented by an overall declining average fuel quality. The systematic accumulation of service results from those ships in service which, according to experience, would be more frequent users of such marginal fuel qualities also has been intensified.
The conclusion to be drawn from the combustion research carried out on full scale engines was the encouraging fact that all these socalled extreme fuel qualities, including coal derivatives, were fully usable in our diesel engines, as has been the case with the traditional heavy fuels in the past.
We are fully aware of the somewhat different modes of operation involved in river boat traffic versus oceangoing operation. The main difference is strongly related to manning requirements and the maintenance pattern.
With the rivers being the "freeways" for bulk cargo in this country the river tugs are operated as trucks on the road. As illustrated the complete propulsion package with its integrated control system allows such running of the engines "from the front seat", i.e., the bridge pilothouse.
The analogy to road transportation is expressing with strength that it is a natural requirement of the operator that maintenance is as fully predictable as when a truck needs service and fuel, but of course with much longer intervals.
With the stability in performance which is outlined and proven by our service experience, we can meet such requirements, meaning that unskilled personnel can operate the engines and actual service be left to shore gangs at "service stations." Hugo Fiedler of MaK presented a paper entitled "Heavy Fuel Operation with MaK Diesel Engines for Multipurpose Application and Marine Propulsion." The MaK diesel engine program consists of five engine lines with an overall range from 740 to 9,000 kw. Basically the engines are designed and built for marine applications, main propulsion and auxiliary service, as well as stationary application. Accordingly, economy, which means reliability, low fuel and lube oil consumption as well as the capability of burning any kind of fuel, is the leading guideline for the design and development.
Though for some engine types V-engines are available, the general tendency is to feature inline engines, especially for marine application.
Low cylinder numbers or in-line engines mean a low number of moving parts. Though today, on account of improved materials and experience in design, a high reliability of the different parts can be achieved, there is no doubt that the all over reliability is directly related to the number of parts involved and bear a direct relation to maintenance and overhaul requirements.
The general trend for reduction of fuel consumption initiated by the increasing price of fuels has resulted in an extensive development work in this direction. Today MaK engines are of the highest efficiency and in particular cases leading in this field, achieving up to 50 percent efficiency.
For more than 15 years the burning of heavy fuels in mediumspeed four-stroke engines has been developed with increasing success.
Today even the highest viscosities can be burned without difficulties, not only at full but also at part load. Wear rates of parts exposed to combustion are in many cases even lower than experienced with older engines running on gas oil Alan C. Barich and Edwin E.
Hodges of Transamerica DeLaval presented a paper on "Exhaust Emission Control Techniques of Today's Large-Bore Medium-Speed Diesel Engines for Heavy-Fuel Operation." Although currently in the embryonic stage for marine application, exhaust emissions are in the process of being regulated for ship operation in our inland waterways, Great Lakes and major U.S.
ports. Control of diesel exhaust emissions will include changes to the basic operation of the diesel engine through such means as to retard fuel injection timing, charge air manifold temperatures and use of exhaust gas recirculation.
The work discussed in this report revealed substantial results.
Injection timing and intake air manifold cooling show clear reductions in NOx emissions, but the extent of the reductions is limited.
Moreover, substantial fuel penalties associated with these techniques were demonstrated. Of the combustion control techniques tried, exhaust gas recirculation was the most effective in achieving significant NOx reductions with minimum fuel-consumption penalty.
However, the hidden costs associated with this method are a major concern at this time. Further development work is needed to improve the EGR system and thus reduce fouling and related gas-handling problems. The effect of EGR on lube oil contamination and ultimately on engine wear also needs additional investigation.
Ammonia-injection catalytic reduction appears to work well in reducing NOx, but again needs further attention. It has not yet achieved expected percentage reductions, and additional work directed toward the control system and related hardware is necessary.
Based on results of the experimental program to date, it is apparent that both catalytic reduction and EGR are deserving of further attention. No mechanical experiments with engine redesign are possible until completion of the present experimental program, but research can be directed at resolving the problems associated with EGR.
Until such a time as more work can be done, it is up to the engine manufacturer and owner alike to help reduce NOx by carefully and precisely sizing auxiliary equipment that will help reduce engine emissions.
C. E. Rosgren, design manager for Wartsila Diesel, spoke on "Reliable Heavy-Fuel Engine Component Designs." This paper deals with the design aspects of some critical components in heavy-fuelburning diesel engines. The theoretical considerations are described as well as the practical outcome of applied engine tests and field experience.
The heavy fuel experiences referred to were gained during the last five years and, consequently, on fuels refined by the latest secondary processes, which means cracking of different kinds. Such fuels have combustion properties which substantially differ from the heavy fuels available 10 years ago.
The evaluations are based on experiences of the purpose designed heavy fuel engines Vasa 32 and Vasa 22HF in a lot of different installation types such as main engines in ro-ro vessels, supply vessels, tugs, icebreakers, ferries and small tankers as well as a number of auxiliary engine applications.
The Vasa 32 engine was introduced in 1977 and has since then attracted much attention. At that time it was one of the first new engine designs developed after the 1973-74 oil crisis. It filled a gap between the heavy fuel burning 15.75-inch bore engines and small marine diesel engines. The Vasa 32 covers an output range of 2,010 to 9,180 bhp.
The Vasa 22HF engine, with the same basic features as the Vasa 32, was introduced in 1980. With the output range of 720 to 3,480 bhp it extends the range of Vasa 32 downwards. In the upper end of the output range it is, with its smaller size and higher speed, an attractive alternative in small vessels.
Practically, it can be said that the Vasa engines are well suited for all heavy fuels existing on the market today. They also form a stable base from which the development towards using further deteriorating future fuels can be continued.
A paper describing the Waukesha AT25 Series of diesel and heavy fuel engines was presented during the second day of the symposium.
The Waukesha AT25 Engine Series consists of a family of four engine models including six and eight-cylinder in-line, and 12 and 16-cylinder vee configurations.
The engines have a common 250-mm bore with a 300-mm stroke and were designed and developed by Sulzer Brothers Limited of Winterthur, Switzerland. The Waukesha Engine Division of Dresser Industries Inc., is manufacturing and further developing this new engine family at Waukesha, Wis., under a license agreement with Sulzer for marketing throughout the world.
The engine series has been designed for both diesel and heavyfuel operation and covers a speed range of 720 to 1,000 rpm. The diesel (distillate) fuel maximum continuous power range covers 1,260 to 4,800 bhp, whereas the heavy-fuel (residual) rated power range covers 1,140 to 4,320 bhp.
This new AT 25 engine series combines the four-stroke diesel cycle with direct injection, turbocharging and intercooling. The design results in a high-density reciprocating power producing package including low fuel-oil and lube-oil consumption, high reliability and durability, and multifuel capability for cost effective operation.
The first engine of this new series produced at Waukesha was a 12-cylinder model.
Over 3,000 engines of the A25 type have been applied by Sulzer and its licensees in universal applications including main marine propulsions (deep sea and inland waterways), ship auxiliary power generation, offshore oil-drilling platforms, railroad traction and stationary power generation.
R. Peter Spock, American Commercial Barge Line Co., described "The ACBL Blended Fuel Program." ACBL decided to pursue blended fuels after a lengthy discussion and study of the current technologies.
Several other conservation methods were put into effect, but blended fuel was to be the major effort because it showed evidence of providing the greatest amount of savings potential. At that time, about 40 percent of ACBL's line haul towboats were equipped with Alco engines, which had undergone previous blended-fuel testing.
Also in 1980, our future new vessel construction called for several vessels to be equipped with Alco engines. Thus in light of the pricing structure of diesel and blended fuels, it was determined that significant fuel cost savings could be obtained in these vessels.
Another factor which influenced the decision was that ACBL had previously purchased a tank farm in Memphis as a hedge against any future oil shortages. This would prove advantageous since the quality of blended fuels must be controlled in order to provide successful operation in diesel engines.
Over the long term, it is expected that diesel fuel prices will increase much more than residual.
This is the most significant reason why blended fuel is a rational approach to controlling operating costs. This must obviously be tempered by the increased maintenance costs associated with blended fuel.
The author then described in detail the impact of these changes and how ACBL arrived at its current position. Finally, the paper takes a look at the most recent ACBL heavy-fuel project which involves the re-engining of the tri- ple-screw towboat M/V Bill Elmer with three MaK engines equipped to burn 3,500-ssu fuel.
Kenneth Siegman of the Midland- Ross Company reported on "Midland's Heavy Fuel Oil Experience." He advised that in late 1981 Midland made the decision to build two boats capable of burning heavy fuel oils of varying viscosity and varying quality. This decision was based on many factors both within the Midland organization and external to the company. The external factors were many, but were primarily concerned with the present and future cost and supply of fuels.
In November 1982, Midland took delivery of the M/V Jim Ludwig from St. Louis Ship. In May 1983, Midland took delivery of the M/V Justin T. Rogers. Both of these boats came out of the yard burning an IF-80 (600-SRI) fuel and have continued to burn this blend.
This paper covers Midland's experiences during design and construction, plus much of their operating experience to date. Much of the operating data is very recent.
Each day a new or unexpected bit of information is learned and they expect the learning experience to continue.
Along with the decision to go to heavier blends of up to 2,100 SRI, there were questions raised on storage tank configuration. The original hull design had two large port/starboard tanks on each side.
This was later changed to divide each of the large tanks in half to give four port/starboard tanks, each side. More but smaller capacity tanks were required for two reasons.
The first and prime reason was the concern of possible fuel compatibility problems. The various bunkers if purchased from different suppliers could be kept separate.
An important part of the boat design once the hull configuration was chosen, was the choice of the main engines. After an extensive search and evaluation, it was decided to go with main engines designed and built by B&W Alpha of Frederikshaven, Denmark.
Much of the data and experience contained in this paper is based on the operating experience of the two boats. From what is known now, Midland feels that they can expect to meet or exceed their expectations of the move to burn heavy fuels.
M.H. Brinker, M.A. Cereno and W.H. Rice, Jr., Heartland Transportation Company, The Inland Waterways Division, Pott Industries Inc., described "The Inland Waterways Division, Pott Industries Inc. Blended Fuel Program." The blended-fuel program of IWD began back in the mid 1950s when Federal Barge Line began operating four towboats on blended/heavy fuel oil. Federal Barge lines operated these four boats on heavy oil from 1956 through 1965 for two boats and 1972 for the other two when, due to the expense of burning heavy oil versus diesel oil, the boats were converted back to diesel oil service and the heavy-oil equipment was removed.
Many lessons were learned from these years of operating on blended fuel oil and these lessons were thoroughly studied and considered when the Inland Waterways Division decided to build the M/V Robert A. Kyle and make it capable of burning blended fuels.
The M/V Robert A. Kyle had operated for approximately 950 hours on blended fuel when the decision was made to replace the power packs in the center engine. Since the first phase of the test was to be a shakedown of the fuel handling and delivery equipment, the power packs were not renewed prior to using heavy fuel even though EMD recommends chrome cylinder liners when using high-sulfur fuel.
The performance of the cast-iron liners during the shakedown phase proved to be quite promising so that we and EMD decided to test both cast-iron and chrome liners in the wear evaluation phase of the test which is currently underway.
Through the cooperation of EMD and the oil companies, the engines were thoroughly inspected and borescope photographs of the cylinder walls, exhaust valves and turbo screen were taken to record their condition before heavy fuel was introduced to the engine. There were no unexpected consequences attributable to the use of heavy fuel during the shakedown phase of the test. The Kyle has experienced no failures on the center engine due to blended fuel oil.
For further information and copies of the above presentations, circle the appropriate number on the Reader Service Card in the back of this issue.
Belcher Oil Company (Quality and Availability of Blended Marine Fuels in 1983)—Circle 51; Alfa Laval, Inc. ("The Alfa Laval Line-Up Past And Present")—Circle 52; Drew Chemical Company ("The Role Of Chemicals and Fuel Analysis in the Marine Industry")—Circle 53; MAN/B&W, Alpha Propulsion Systems ("Engines on the River")—Circle 54; MaK ("Heavy Fuel Operation with MaK Diesel Engines for Multipurpose Application and Marine Propulsion")—Circle 55; Transamerica Delaval (Exhaust Emission Control Techniques of Today's Large-Bore Medium-Speed Diesel Engines for Heavy Fuel Operation's— Circle 56; Warstila Diesel (Reliable Heavy-Fuel Engine Component Designs")—Circle 57; Waukesha Engine (The Waukesha AT25 Series Diesel)—Circle 58; ACBL (The ACBL Blended Fuel Program")—Circle 59; Midland Ross ("Midland's Heavy Fuel Oil Experience")—Circle 60; Heartland Transportation ("The Inland Waterways Division Pott Industries Inc. Blended Fuel Program")— Circle 61.
Read Modern Fuel Systems Symposium in Pdf, Flash or Html5 edition of January 1984 Maritime Reporter
Other stories from January 1984 issue
Content
- Navy Contracts Totaling $477 Million Awarded To Avondale Shipyards page: 5
- Marinette Marine Awarded $1-Million Minesweeper Phase II Design Contract page: 5
- Brown & Root Inc. Forms Joint Venture In Holland With Two Dutch Companies page: 5
- Bethlehem Steel Signs Licensing Agreement For Tension Moored Platforms page: 5
- WEAKENING THE JONES ACT page: 6
- New Bath Iron Works Repair Facility Opens In Portland page: 6
- Penske G M Power Head Discusses Service Support For Maritime Industry page: 6
- Modern Fuel Systems Symposium page: 10
- Jacobson Delivers Shipdocking Tug 'Chessie' To Chessie System page: 10
- Latest Europort Exhibition A "Resounding Success" page: 10
- Carmen Guide Appointed President Of Lake Shore —Malsack Named Chairman page: 12
- Mobile Marine Introduces Advanced-Design Workboat page: 12
- Financing Completed For U.S. Lines Containerships Building At Daewoo Yard page: 13
- Navidyne Unveils New INMARSAT Ship Terminal —Literature Available page: 13
- Indikon Introduces New Web Deflection Indicator —Literature Available page: 14
- T C S Industrial Appointed Distributor for NABRICO —Literature Available page: 14
- Joint SNAME, IME And NYPE Meeting Discusses Use of Inexpensive Fuels page: 16
- OUTSTANDING OFFSHORE/SHALLOW-DRAFT VESSELS OF 1983 page: 18
- Michigan Wheel Awarded Navy Contract For Carrier And Oiler Propellers page: 18
- Seaworthy Engine Systems Shortens Corporate Name page: 18
- Joel Alper Appointed President Of COMSAT World Systems Division page: 18
- REDUCING FUEL COSTS First In a Series-Propulsion Equipment page: 20
- Esercizio Cantieri Launches Tug/Supply Vessel Of New Design page: 41
- NASSCO Begins Conversion Of First Maritime Pre-Positioning RO/RO page: 41
- New Marine Autopilots Introduced By Racal —Literature Available page: 42
- Steam Plant Optimization Topic At New York Port Engineers Meeting page: 42
- AWO SHIPYARDS AND THE JONES ACT page: 44
- BIW Chief Engineer Addresses Northern New England ASNE page: 45
- Lifeboat Quick-Drop System Unveiled By SeaTek And MCR page: 45
- Charles Garman Named Western Sales Manager For Stork-Werkspoor page: 48
- Omnithruster Establishes New Manufacturing Facility In Canada —Literature Available page: 49
- Scholarship For Panamanian Students At Kings Point Funded by Justin Bonanno page: 50
- O'Boyle Firm Appointed Exclusive U.S. Agent For Astilleros Espanoles page: 51
- Epoxo Safety Coating Helps Prevent Slipping —Literature Available page: 53
- Mitsui Delivers First Of Four Bulk Carriers To Egyptian Owner page: 53
- Stork-Werkspoor Engines Will Power Exxon Tugboats page: 56
- Barge-Mounted Nine-Story Hotel Proposed By NKK page: 56
- New Design Cranes Installed On Navy's Auxiliary Drydocks page: 56
- New Fuel Management System From Pandel —Literature Available page: 63