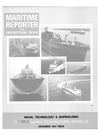
W a r t s i l a Introduces The V a s a GD, N e w Gas-Diesel Engine
The latest achievement in the development of the Wartsila Diesel engine range is the Wartsila Vasa GD, a new gas-diesel engine that can operate on a wide variety of fuels, from poor quality heavy fuel to high quality hydrocarbon gases.
The Vasa GD is a multifuel engine well suited for a number of different installations: land-based and offshore power plants, pumping and compressor stations and fuel-offthe- well operation in the oil industry, to mention just a few. Thanks to flexibility in fuel selection, the Vasa GD engine permits minimizing of operating costs. The gas-diesel concept permits instant switchover to the most economical fuel available.
The risk of disruption in fuel supply can also be minimized since back-up fuel is always available.
As the Vasa GD has the same output range and basic design as the Wartsila Vasa 22 and 32 diesel engines, existing installations with these models can also be easily rebuilt for multifuel operation. Rebuilding does not alter the maximum engine output.
The Vasa GD engine can shift from a gaseous to a liquid fuel and back without interruption. Thermal efficiency is not affected by fuel type, and use of the optimal diesel process in combustion keeps it above 45 percent. Full advantage can thereby be taken of a diesel engine operating as a gas engine, because the output needs not be derated. A conventional gas auto engine does not exploit the full potential of a modern diesel engine because of combustion related factors such as detonation and high thermal load, which also reduce engine efficiency drastically. Wartsila Diesel has therefore chosen to develop the Vasa GD gas diesel engine, which eliminates these obstacles with high-pressure gas injection.
High-Pressure Gas Injection The gas fuel, a methane-based hydrocarbon, is compressed to 250 bar before it is fed to the engine.
This high pressure results in a high energy density, which means that the gas can be injected into the combustion space at the end of the compression stroke in the same way as in a diesel engine operating on fuel oil. Full benefit is therefore obtained from a modern diesel engine with the same high output and efficiency, using either gas or diesel fuel. Due to the higher autoignition temperature needed for gaseous hydrocarbons than for diesel oil, the temperature in the combustion space must be raised before the gas is injected. The temperature is increased by injecting and burning a small amount of pilot fuel a few crank angle degrees in advance of the gas injection. The pilot fuel can be diesel oil, heavy fuel or crude oil, depending on what is best suited to each particular case.
Patented Fuel Injection System The compressed gaseous fuel is transported from the gas compressor, which is normally located outside the engine room, to the injection valve on the engine via a double walled pipe system. The annular space is mechanically vented to a safe place outside the engine room, where the air is checked constantly by hydrocarbon detectors. The key element in the design concept is the combined injection valve, through which both the pilot fuel and the gaseous fuel is injected. The same valve can be used for operation on gaseous fuel with pilot injection or for diesel fuel alone up to full output in both modes. A special valve design makes it possible to run the engine continuously on heavy fuel without causing any risk of damage to the gas admission side.
Computer Based Control/ Safety System The safety system is also an essential part of the design concept.
Gas engines are fitted with both the normal safety system mounted on conventional diesel engines and additional safety devices. The safety system must also meet the requirements of classification societies for marine installations and local regulations for land-based power plants.
The main features of the concept are: a double-walled pipe system eliminates gas leakage to the engine room; an automatic main gas valve in front of each engine and a quick closing valve mounted at each cylinder shut off the gas supply in the event of excessive gas flow to any cylinder, disturbance in the load balance of the engine, gas leakage to the annular space, low output from the engine, or low gas supply pressure.
An electronic governor is used for maximum flexibility. The optimal operating mode, diesel or gas, can be chosen by pushing a button. The changeover from gas-to-diesel mode is automatic in the event of a disruptance in the gas distribution system.
Test Results Wartsila Diesel has made extensive development tests on a Vasa 4R22 medium-speed diesel engine using high pressure gas injection.
The engine has operated at 1,000 rpm and a load range of 20 to 110 percent. The rated output is 162 kW per cylinder, which corresponds to a BMEP of 21.2 bar. The initial tests started with a pilot fuel amount of 10 percent. A very stabile combustion process resulted in further reduction of pilot fuel to 5 percent without any loss in efficiency. No tendency towards detonation was observed during tests with different pilot oil levels. The same high efficiency was recorded during both gas operation and diesel oil operation at all loads.
For free literature giving complete details on the Wartsila Vasa GD, C i r c l e 7 6 on Reader Service Card
Read W a r t s i l a Introduces The V a s a GD, N e w Gas-Diesel Engine in Pdf, Flash or Html5 edition of December 1987 Maritime Reporter
Other stories from December 1987 issue
Content
- B IW Announces M a j o r R e o r g a n i z a t i on page: 5
- Farrell Calls For Presidential C o m m i t m e nt To The U.S. M a r i t i m e Industry page: 6
- Furuno Introduces N e w Products page: 6
- H H I Exports Full D e s i gn P a c k a g e For C r u d e C a r r i er To P o r t u g u e s e S h i p y a rd page: 8
- N e w Solid S t a t e I g n i t i on S y s t em F r om F a i r b a n ks M o r s e page: 8
- OUTSTANDING OCEANGOING SHIPS OF 1987 page: 10
- M I T Announces Spring P r o g r am In Port P l a n n i n g, D e v e l o p m e n t , E n g i n e e r i ng page: 28
- M M S Delivers P l a n n ed M a i n t e n a n c e S y s t em For C a n a r c t i c Icebreaker page: 28
- Furuno Electric C o m p a ny Acquires ISR In Europe page: 29
- Bennex Reports Early Success For N ew L i g h t w e i g h t Oil Booms page: 30
- U.S. N A V Y BUSINESS OPPORTUNITIES — A N UPDATE— page: 33
- N a v y Commissions USS A v e n g e r, Its N e w M i n e Countermeasure Ship, At Peterson Builders page: 36
- Paceco, Inc. Receives O p t i o n A w a r d From N a vy page: 36
- MAJOR N A V Y CONTRACTS page: 36
- Aegis Missile Cruiser 'Leyte G u l f / II 0 0 t h G E - P o w e r e d U.S. N a v y Ship, D e l i v e r e d By Ingalls Shipbuilding page: 48
- JJH Inc. Announces Key Personnel A d d i t i o ns page: 48
- 1 6 - P a g e G e m s C a t a l og F e a t u r e s S o l i d - S t a te Relays A n d Barriers page: 49
- N e w U.S. Coast G u a r d Patrol C r a ft Employ Electrocatalytic's Capac System Selected To Arrest Corrosion In All N a t u r a l W a t e rs page: 49
- Ingalls Christens 1 1 t h Aegis G u i d e d Missile Cruiser For N a vy page: 50
- Selectro G u i d e O f f e r ed Free By M i l l e r Electric page: 50
- M o n A r k Delivers Survey Boat To Corps Of Engineers page: 50
- ASNE To Present Annual A w a r d s At C e n t e n n i al C e l e b r a t i o n In M a y 1 9 88 page: 51
- A v o n d a l e Christens Fleet Oiler W a l t e r S. Diehl For U.S. N a vy page: 51
- S i e m e n s O f f - D e l a y T i m i ng R e l a y s A r e C o m p a c t , R e d u c e P a n e l S p a ce page: 52
- C o n t r o m a t i c s I n t r o d u c es N e w H i g h - P r e s s u r e B a ll V a l v e s page: 52
- W a r t s i l a Introduces The V a s a GD, N e w Gas-Diesel Engine page: 58
- M a c k a y Announces N ew H i g h - F r e q u e n cy M a r i n e Radio Console page: 58
- N a t i o n a l W a t e r w a ys C o n f e r e n c e Elects Officers A n d C o m m i t t e e M e m b e rs page: 60
- W e s t a m a r i n Delivers M T U - P o w e r ed A l l - A l u m i n um Reefer C a t a m a r an page: 62
- O f f s h o r e M a r i n e Service Association Elects N e w Board M e m b e rs page: 62
- Circle Seal Controls O f f e r s Free L i t e r a t u re On C h e c k - R e l i e f V a l v es page: 62
- Raytheon Introduces J U E - 4 5 A, Most Compact A n d Sophisticated S a t C om Of The JUE Series page: 62
- Exxon Introduces C o s t - S a v i n g M a r i ne Lubricant Line page: 63
- River Services Adds Ice Forecast Service page: 64
- St. Philip T o w i n g Adds T w o N e w Trac-Type Tugs page: 64
- Phoenix Products Acquires M a j o r i t y O f Russellstoll L i g h t i n g Line page: 64
- H e m p e l Coatings Announces C h a n g es page: 65
- ITT S t a n d a r d Introduces A n Efficient, Low-Cost M e t h o d Of H e a t i n g Liquids page: 65
- TTS Delivers W o r l d 's Largest S k i d d i n g System page: 65
- K im Hotstart P r e - H e a t i ng Systems Shrink E n g i n e I d l i n g Costs page: 66
- Deutsch H D 1 0 Series Connectors O f f e r O u t s t a n d i n g P e r f o r m a n ce A n d E n v i r o n m e n t a l Protection page: 70
- Stanspec C o r p o r a t i o n 's R i g h t w a y Car Puller O f f e r s N e w Features page: 71
- M A N G H H Reports On Design Requirements For M o d e r n N a v a l Drydocks page: 72
- A d r i a n R. P. D a y N a m ed Racal M a r i n e President page: 73
- ABS A p p o i n t s C r a w f o rd A n d Lee Assistant VPs page: 73
- P B M O f f e r s Free C a t a l og O n 3 - W a y Diverter V a l v es page: 73
- Pusnes M a r i n e & Offshore Services Establishes Factory Service And Sales O u t l e t In N e w Orleans A r ea page: 74
- W a r t s i l a To Build 2 , 2 0 0 - P a s s e n g e r Cruise Ferry page: 74
- A e r o q u i p O f f e r s Rubber Insert Sound Isolation Couplings For S h i p b o a r d A p p l i c a t i o ns page: 75
- Sperry M a r i n e Delivers N e w Type A p p r o v ed M C 5 0 0 M a r i n e C o m p u t er page: 76
- D e u t z M W M T r a d e m a rk G a i n s W i d e Acceptance page: 76
- Lykes Elects Blust, C l a rk Assistant V i c e Presidents page: 76
- N e w Reducing Union Branch Tees C a n Connect T w o Tubing Sizes page: 76
- H a y w a r d Introduces N ew 9 0 - P a g e Users' G u i de O n Pipeline Strainers page: 76
- First Coast S h i p b u i l d i ng Constructing $ 1 2 - M i l l i on Luxury Y a c h t For C l i p p e r Cruise page: 77
- M o o r e M c C o r m a c k Resources Transfers O w n e r s h i p A nd Announces N e w Address page: 77
- H a l t e r M a r i n e Delivers 600-Passenger Dinner Cruise Vessel ' C a j u n Queen' page: 78
- M a c k a y Announces Recent Promotions page: 78
- e u t z - M W M Offers Extensive Range Of Diesel Engines To M a r i n e M a r k et page: 78
- C r o w l e y M a r i t i me Announces M a j or O r g a n i z a t i o n a l C h a n g es page: 81