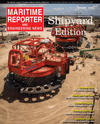
Pipe Joining: Testing Times for Seaworthy Products
For shipbuilders, Type Approval by the International Association of Classification Societies (IACS) is a key criterion in the selection and installation of products and systems for a wide range of shipboard applications. For manufacturers, meeting IACS standards is a major factor in the design, development and qualification of products to ensure the highest levels of safety, fitness for purpose and reliability Len Swantek, Director of Global Regulatory Compliance at Victaulic, outlines the regulatory Type Approval process for its pipe-joining products from design to post production and explains the importance of maintaining high standards for quality and performance.
Of all the market segments where Victaulic mechanical pipe joining products are used, the maritime industry is one of the most strictly regulated. Product testing carried out here is among the most challenging and diverse of all markets and industries – and rightly so. Products need to withstand a wide range of forces and loading conditions generated by vibration, temperature fluctuations, pressure surges, movement resulting from wave motion, not to mention exposure to weather and seawater that pose a constant threat for corrosion of metallic components. If a piping system were to be compromised at sea, it could have serious consequences for the vessel, crew and passengers.
For the maritime market, there are 13 classification agencies within the IACS organization. Victaulic submits new products for design assessment, performance evaluation and Type Approval to a large number of these. The agencies in this group are American Bureau of Shipping (ABS), Bureau Veritas (BV), China Classification Society (CCS), Croatian Register of Shipping (CRS), Det Norske Veritas (DNV), Germanischer Lloyd (GL), Korean Register of Shipping (KRS), Lloyd’s Register of Shipping (LR), Registro Italiano Navale (RINA), Polish Register of Shipping, Indian Register of Shipping, the Russian Maritime Register of Shipping and Nippon Kaiji Kyokai (ClassNK). IACS sets the minimum standard for all of the classification agencies. However, each individual agency may add requirements as needed for a particular system or on a discretionary basis for a critical application. This leads to some variation between agencies, resulting in further challenges during the testing and qualification process.
Regulation is a highly complex and costly business for most manufacturers. With a large range of grooved-end couplings, fittings and valves used in many onboard piping systems, Victaulic has a number of different products in the approval cycle at any given time. Each model and size is subjected to a number of both short- and long-term tests. Additionally, each manufacturing location will be subjected to periodic audits to ensure product quality and consistency is being maintained. Both processes - product testing and factory production control auditing - require considerable management and coordination to meet both agency requirements and customer / market demands.
Getting the groundwork right
Victaulic is a design-focussed company that drives industry trends. Its engineers are involved in research and development year round, evaluating new ideas and working on prototypes that often find their way into unique maritime applications. Since Victaulic invented the grooved piping system more than 85 years ago, it has pioneered many new designs to solve market problems and make products more robust and yet economical to install.
But before the company can even begin the regulatory process to obtain Type Approval, a tremendous amount of time is allocated to research and development and internal testing. The product development process can easily extend over 18 months and entails design, modeling, construction and internal testing of prototypes. The process also includes making adjustments as needed to ensure the product can meet both agency requirements and the established ratings for temperature, pressure, end load, vibration, fire exposure and other possible service conditions. Concurrent with this is process development to assure consistency of global manufacturing to a wide range of international standards.
Once a new design is finalized and the manufacturing controls are worked out, rigorous internal prequalification testing is carried out in preparation for regulatory Type Approval testing requirements. Victaulic replicates known scenarios that could be encountered, applying process technology and even re-engineering products as necessary.
External assessment
Once the product passes internal testing, Victaulic initiates the external assessment process by sending a comprehensive data “package” to each agency that will issue its own unique Type Approval Certification. The information includes application forms, detailed product specifications, manufacturing drawings and any performance data already validated by one of the IACS members within the past five years. The specific approval objectives along with a test proposal outline is also provided for the agencies’ technical review. The components of this package must be accurate and complete, and can take weeks and often several months to compile.
Mechanical bolted couplings are generally understood by the agencies to have pressure holding capabilities that meet or exceed the performance ratings of flanged, welded or threaded systems. This makes the review process a bit easier, yet each system application being applied for will be examined individually, along with any limitations or restrictions imposed by the IACS standards. The agency engineering review process is typically completed within a four- to six-month period for any given product category.
Following the design review and acceptance of the proposed test plan, the agency will advise the scope of testing required and the number of test samples that will need to be prepared. At this point, the difficult and time-consuming task begins to coordinate all of the required testing with a number of independent laboratories which are accredited by one or more of the participating IACS members.
To facilitate performance testing, product samples, pipe of various specifications and other related equipment must be sent to the appropriate test facilities. This is another time-critical operation – as any delays on the part of a manufacturer could result in a lost position in the testing laboratory’s queue. At this stage, documentation must already be available in multiple languages for examiners to assemble equipment themselves, based on an assumed level of skill equal to that of the end user. The testing process can take many months and occasionally more than a year to complete.
The approval authorities are also concerned with the manufacturing and assembly locations of specific finished parts or sub-assemblies. Victaulic manufactures in multiple locations globally to optimize supply chain logistics. However, this can greatly increase costs, as each location must be certified and audited, both for the initial Type Approval certification as well as part of an ongoing surveillance program required to maintain valid certification. In the event of a nonconformance at this late stage a manufacturer risks losing valuable time to market.
Manufacturers like Victaulic can only go to market when they have secured all necessary Type Approval and manufacturing certifications. Once complete, only then can results be reviewed and data fed back to the research and development teams.
Audit management
Audit management is the final phase in the regulatory cycle. This phase starts when a Type Approval is officially released and only ends when the product is no longer produced. Through various follow-up procedures and factory production control audits, manufacturing procedures are reevaluated annually on a set schedule that coincides with the term of validity for each Type Approval certificate.
Auditing is important, since the governing IACS standards are updated on a periodic schedule. These standards are likely to become ever more stringent following the analysis of forensic evidence from equipment failures, accidents and other events at sea. Manufacturers may have little advance notice of pending revisions to these standards and often need to act quickly to keep pace and maintain a competitive position in the market.
Therefore clear understanding of the most up-to-date requirements is vital to the successful completion of the approval cycle and managing time to market.
Responding to customer demands
On occasions approval may be required for a specific application which is not part of the normal Type Approval scheme. In one such example a customer wanted to use Victaulic products on hydraulic winching equipment, which required an extremely heavy load capability to lift chains and anchors up from the ocean bed at a depth of 200m.
In a case like this, a manufacturer must refer to the approving authority to identify specific tests that would be needed to gain special approval – either as an addition to the existing certificate or through a separate approval. The administration, time and cost implications of such programs are evident.
Sharing responsibility
Victaulic views its role in the regulatory process as going beyond simply respecting the rules. Having direct involvement in developing and shaping them is equally important. With over 85 years experience in the mechanical joining of piping systems and related components in a wide range of materials including steel and stainless steel, aluminum, ductile iron, PVC and HDPE, Victaulic is a world leader with a strong message that is being heard globally on many codes and standards committees. Additionally, the company has a department dedicated to regulatory compliance, with oversight responsibility for product specifications, testing and certification, factory production control auditing, codes and standards development and customer related input to these processes.
Victaulic invests heavily to achieve product and service excellence and sees regulation as an area of responsibility where it can contribute to the construction of safe, efficient and durable maritime piping systems. The company’s philosophy is to create a set of meaningful tests that are rigorous enough to replicate known field conditions, yet realistic enough for manufacturers to conduct in a reasonable timescale without undue complexity and cost.
Ultimately, product conformity brings peace of mind to ship builders, operators and owners. The safety and reliability of vessels at sea depends on it.
Grooved mechanical joints explained
The mechanical pipe-joining system begins by cold forming (roll grooving) or machining a groove (cut grooving) into the pipe end. The piping connection is secured by the ductile iron coupling which houses a resilient, pressure-responsive elastomer gasket. The coupling housing fully encloses the gasket, reinforcing the seal and securing it in position as the coupling engages into the pipe grooves. The mechanical joint creates a triple sealing characteristic that utilizes compressive forces from the initial gasket installation and coupling assembly, which is further enhanced when the internal system pressure is applied. This feature enables the assembled joint to accommodate a wide range of pressure applications from full vacuum to the coupling’s maximum positive pressure rating.
Grooved technology is used for class 2 and 3 piping systems and for class 1 systems outside category A areas. Typical applications include ballast, sea and fresh water cooling, lube oil, fire and deck wash, and bilge systems. The technology is also used for class 1 and 2 FiFi systems on tugs and support vessels.
Victaulic mechanical couplings are currently categorized as ‘Slip-on Joints’ within the various classification societies’ rules. Although the couplings are quick and easy to secure with just two nuts and bolts and a single wrench, they should not be overlooked as a reliable pressure- and end load-restraining device. The couplings themselves are cast of durable ductile iron in accordance with ASTM A-536, and are more than capable of handling the full thrust loads generated during pump operation and maximum system pressures to 34 bar. The fact that systems utilizing these products do not require external restraint in itself defies the term ‘slip-on’. Whilst the standards categorization may not seem properly aligned with the product performance capability, maritime users of bolted mechanical couplings are fully aware of the strength, durability and long-term serviceability they afford to the designer, owner and ship operator.
(As published in the August 2013 edition of Maritime Reporter & Engineering News - www.marinelink.com)
Read Pipe Joining: Testing Times for Seaworthy Products in Pdf, Flash or Html5 edition of August 2013 Maritime Reporter
Other stories from August 2013 issue
Content
- Alion Ramp Makes for Safer Ship-to-Ship Transfers page: 11
- From ShipConstructor to SSI page: 12
- Geometry at the Heart page: 14
- Training Challenges page: 16
- Maintenance & Certification: Critical to the Safety of Life at Sea page: 18
- The Busy Signal page: 20
- Satellite Radar page: 24
- Offshore Wind Market Report $19.8B Opportunity page: 30
- Offshore Deepwater Brazil Sevan Drilling’s Big Dig page: 32
- Gulf Copper Keeps “Calm” page: 34
- Eastern: Beyond the Backlog page: 36
- Brasa: FPSO Modules a Specialty page: 38
- ASRY: Bucking the Slowdown Trend page: 41
- Austal USA Powers Ahead page: 42
- Signal International page: 50
- Vessel Ordering Mania – Why? page: 51
- TNG: Talleres Navales Del Golfo page: 52
- Vigor Industrial page: 54
- Maintaining the Ship of Mercy page: 56
- Tips on Reducing Ship Operating Costs page: 58
- Schottel Celebrates CPP Milestone page: 63
- Siemens: Gigantic Gear Unit Technology page: 64
- Book Review: “After the Galaxy” page: 68
- Pipe Joining: Testing Times for Seaworthy Products page: 74