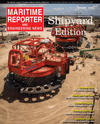
Maintenance & Certification: Critical to the Safety of Life at Sea
The off-load marine hook is found on many workboats and military vessels and is used to launch fast rescue craft and other similar small manned boats from the deck of a ship using a davit or other similar launch and recovery system (LARS). These hooks offer operators the split-second release control often needed at sea and include a self-locking feature, which prevents accidental release while under full load.
When all applicable equipment is in good working order, the nature of launching a manned small boat from an underway larger vessel while at sea is a dangerous task in and of itself and has resulted in many injuries and fatalities throughout maritime history. If this critical load bearing equipment is not kept in perfect working order, it serves to significantly increase the chance of an accident and potential injuries or fatalities during the launch and recovery procedures. Although proper training on the use of launch and recovery equipment plays a key role in minimizing the potential for an accident, the focus of this article is on the equipment involved in the launch and recovery process in general and on the maintenance trends that I have seen develop regarding off-load marine hooks in particular.
As the director of the testing and certification program for Eagle Products’ hooks, I have noticed an alarming trend develop in the many hooks that we have processed. The first and most disturbing trend is the apparent lack of regard for the IMO mandated five-year testing and recertification cycle. More than half of the hooks that I have seen come through our facility for testing and recertification are grossly out of date. When testing and recertification are left up to the responsible party(s) for a vessel, a lack of knowledge on the five-year testing and recertification cycle often drives these hooks far into the out-of-date status.
Although an out-of-date hook may look fine on the outside, often there are hidden issues that cannot be seen which affect the potential performance of this key piece of critical load path safety equipment. Structural issues such as microscopic cracking or hidden wear on locking pins, metallurgical issues such as hydrogen embrittlement as well as relentless corrosion issues each contribute to hidden weakening of the hook. Particularly troublesome are crevice corrosion and pitting corrosion, which occur predominantly on portions of the mounting bolts that are hidden from the naked eye and create the potential for catastrophic failure of the hook.
Another alarming trend is improper hook maintenance. Top on the list is the use of grease to lubricate the working parts of the hook such as the locking pin mechanism, the positive lock, the latch and the rotating hook part. Grease should never be used on these hooks because of its tendency to collect particulate matter and become dry and caked up within the workings of the hook where it acts more like an adhesive than a lubricant. Many of the hooks we have serviced are gummed up with old grease to the point where the locking pin mechanism is only marginally functional. It is imperative that the locking pin be able to move freely within its confines for the hook to maintain the load that it was designed to hold.
Moving down the list of maintenance items, the lock pin spring and the latch spring need to be changed in all Cranston Eagle hooks every 30 months as per the manufacturer’s requirements. This is a simple process that can be undertaken in the field by ship’s personnel, yet it is rarely done. I have seen tired, worn and deformed springs that have not been attended to since the hook was originally manufactured. A faulty or tired lock pin spring can jeopardize the ability of the hook to maintain the load that it was designed to support if it does not fully push the locking pin into place.
Some of the other issues that I have found to be fairly common include frozen or stiffly moving hook parts, substituted sub-par non-OEM parts, highly frayed and improperly tensioned release cables as well as structural damage to the hook body itself.
I have worked my way through these issues to point out the fact that these critical pieces of safety equipment are not being properly maintained, with the goal to raise awareness within the industry.
It is up to each organization with a fleet of vessels to set up its own maintenance schedules, which they generally do very well. Including off-load marine hook maintenance at the top of that list is critical to the safety of the crews of our ships. For U. S. government vessels including the Coast Guard, the Navy and NOAA, the added hurdles of wrestling with reduced budgets, postponed maintenance availabilities and the cuts associated with the sequestration add a new level of difficulty to most vessel maintenance tasks. The critical safety systems and hardware, however, must remain on the top of the list of maintenance items and not be overlooked during these difficult times.
The five year load testing and recertification process will effectively take a tired old marine off-load hook and renew it to a hook that is like new and is safe and fit for its intended duty. The renewal process begins with a preliminary dye penetration test to check for hidden cracks. The hook is then completely torn down and all parts are thoroughly inspected for damage or excessive wear. Following the tear down, the hook body undergoes a three step cleaning process including a degreasing, bead blasting and vibra-polishing using a ceramic bead medium. Other major components such as the locking pin, latch, positive lock components and mounting and assembly bolts are degreased and cleaned by hand. The hook is then rebuilt to factory specifications. When the hook is rebuilt, the locking pin spring, latch spring, rollers, pull cable, positive lock bushings, nylock nuts, cotter pins and all instructional label plates are replaced automatically with new OEM parts.
After the hook has been reassembled, it is mounted on a purpose-built test fixture for load testing.
The load testing for the Cranston Eagle hooks is a critical process undertaken by an engineering team of the highest caliber. Delta P Subsea Systems, Inc. works in partnership with Delta T Systems and is responsible for the load-testing portion of the hook renewal process. David Dupont, VP of Engineering for Delta P Subsea Systems, is in charge of the load testing process.
The load that each hook will be pull tested to is equal to 2.2 times the safe working load (SWL) rating of the hook. Each load test is witnessed and signed off by a DNV or other class society official. Following the load test, the release tension for the pull cable is tested to ensure that the force, which is required to open the hook, falls within the acceptable range as per the manufacturer’s specifications.
Upon completion of the load testing, the hook will undergo the second dye penetration test by a certified technician. The dye penetration test is critical for exposing any cracks or faults in the critical load path components of the hook that are not able to be seen by the naked eye. The hook is then shipped back to the vessel along with a full certification report and is ready to be installed on the vessel for another five years of service.
This “call to action” is for the responsible party for each vessel that utilizes marine off-load hooks to inspect their hooks immediately to make sure that they are within their five year certification window and in good working order. The stakes are far too high to overlook this critical piece of load-bearing hardware.
Michael Gabriel is director of the testing and certification program for Eagle Products’ hooks. In January of 2011, Delta T Systems, Inc. located in Riviera Beach, Fla., took on the role of the U.S. agent for Cranston Eagle (DBA Eagle Products Ky), a Finland-based manufacturer of off-load marine hooks.
(As published in the August 2013 edition of Maritime Reporter & Engineering News - www.marinelink.com)
Read Maintenance & Certification: Critical to the Safety of Life at Sea in Pdf, Flash or Html5 edition of August 2013 Maritime Reporter
Other stories from August 2013 issue
Content
- Alion Ramp Makes for Safer Ship-to-Ship Transfers page: 11
- From ShipConstructor to SSI page: 12
- Geometry at the Heart page: 14
- Training Challenges page: 16
- Maintenance & Certification: Critical to the Safety of Life at Sea page: 18
- The Busy Signal page: 20
- Satellite Radar page: 24
- Offshore Wind Market Report $19.8B Opportunity page: 30
- Offshore Deepwater Brazil Sevan Drilling’s Big Dig page: 32
- Gulf Copper Keeps “Calm” page: 34
- Eastern: Beyond the Backlog page: 36
- Brasa: FPSO Modules a Specialty page: 38
- ASRY: Bucking the Slowdown Trend page: 41
- Austal USA Powers Ahead page: 42
- Signal International page: 50
- Vessel Ordering Mania – Why? page: 51
- TNG: Talleres Navales Del Golfo page: 52
- Vigor Industrial page: 54
- Maintaining the Ship of Mercy page: 56
- Tips on Reducing Ship Operating Costs page: 58
- Schottel Celebrates CPP Milestone page: 63
- Siemens: Gigantic Gear Unit Technology page: 64
- Book Review: “After the Galaxy” page: 68
- Pipe Joining: Testing Times for Seaworthy Products page: 74