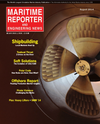
Remote Diagnostics Help Drive Efficiency Gains
With the advent of ever faster, stronger maritime communication links and the influx of the next maritime generation, the first “internet native” generation, a proliferation of shipboard tools are under development that promise to change the very means in which floating assets are built and maintained. Imtech Marine is convinced that accelerated uptake of remote diagnostics and preventive maintenance for shipboard equipment will be built on performance gains that are straightforward and tangible.
Frank Berends heads a team at Imtech Marine typifying a fast-evolving new breed of marine engineering specialists, one whose dedication to optimizing and maintaining shipboard equipment remains unchanged, but whose presence is largely required ashore.
But Imtech is not simply in the business of providing the physical tools to accomplish the task. Realizing the vessel owner operators today are tasked with an ever evolving spiral of technical matters surrounding their fleets, they aim to assist with technical experts.
The marine technology group and global service provider is at the forefront in delivering expertise in remote performance analysis, testing, fault-finding, maintaining and optimizing the performance of shipboard equipment on which efficient operations depend.
Backed by three Global Technology Assistance Centers (GTAC) in Houston, Singapore and Rotterdam, the Imtech Marine technical team is available 24/7 to interpret monitored data, offer diagnostics support and remote maintenance. From the GTAC centers, engineers support technologies as diverse as:
• VSAT
• Integrated Bridge Systems
• Shipboard ICT/Infrastructure
• E-Systems
• Integrated Platform Management
Systems
• AV/Entertainment, and
• HVAC
Nico van Leeuwen, Imtech Marine Director Global Service Sales, positions the Imtech Marine of today as a “systems integrator plus”, taking a “cables to data” approach that combines expertise on shipboard systems with benchmarked performance analysis undertaken ashore. “Having and analyzing the right information through our global service database at the right time means we can make informed decisions on how, where and when to execute routine maintenance, software installations, hardware replacements or upgrades,” he said.
Imtech Marine is also relaunching Radio Holland as the brand to identify its entire navigation and communications service portfolio, including remote monitoring - a move Van Leeuwen says emphasizes the “resilience of the RH brand”, and its strong reputation for service.
“With Remote Monitoring, potential problems will be signalled pro-actively and in many cases before they actually happen,” said Berends. “At the same time, advice offered online can cover anything from routine maintenance to software upgrades, to operator error. If direct intervention is not required, remote support is enhanced via a Customer Portal that gives access to all technical information, such as drawings, manuals, circulars, FAQ’s, Trouble-shooter, updates and software updates.”
One benefit is that fault-finding can be done remotely, avoiding both the costs and inevitable time lags involved in sending, lodging and briefing a field service engineer. In addition, Van Leeuwen stresses, when direct intervention is required by service engineers: “GTAC will inform the Service Coordination Center with all essential background information and full diagnostics for the attending Field Engineer. The ‘First Time Fix’ percentage of field service will increase, reducing repair time.”
Remote monitoring is therefore a critical component that supports the optimization of ship efficiency because it enables expert advice to be given to shipboard engineers immediately on how to adjust operating processes to get the most out of working equipment, said Berends.
In fact, he describes fast-rising expectations from customers for remote monitoring, its predictive capability and its ability to identify root causes in fault-finding, while continuing to stress that the ability of Imtech Marine’s GTACs to respond quickly to incoming calls for assistance remains critical.
“At one level, our most pressing calls will come from customers with a problem that needs to be dealt with immediately. However, owners are increasingly seeking preventive capability, with equipment and systems monitoring backed by expert advice to optimize asset utilization,” Berends said. He describes a common scenario, where a ship’s master might be tempted to reset some or all systems when suspecting impending satellite connectivity outage, when the right course of action is to identify the source of the signal compromising connectivity and isolating the issue.
“Sometimes it is a case of helping the master with the problem he has by identifying that it is not the problem he thinks he has,” he said. “By monitoring equipment remotely, we can establish that the basic problem is a signal feeding into the network, not the network itself, and thus avoid time-consuming reconfiguring.”
At a system-specific level, a problem caused by GPS may present itself to the user as a perceived radar problem, for example, but remote monitoring can identify the root cause and offer alerts on a proactive basis.
Keeping close oversight of shipboard equipment temperatures is also essential, Berends said. “If shipboard equipment is left to operate at too high a temperature, the first warning can be when it burns out.” Imtech monitoring provides the basis for recommendations on preventive action.
“Increasingly, we are also working in close collaboration with engineers onboard ship to enhance their own working processes, based on our performance analysis of the systems they are supporting,” said Berends. “We can also establish accurately the exact moment when it becomes most effective for both Imtech and its customers to dispatch a service engineer to the vessel. We identify the point when saving costs in one area has cost implications elsewhere.”
Today, Berends says that around one half of inquiries dealt with by Imtech’s Global Technology Assistance Centers from shipboard personnel are resolved by changing settings, rather than initiating maintenance. “The situation reflects what landside IT users experience, and comparable troubleshooting takes place, which is particularly effective when dealing with intermittent faults.”
Remote Delivery
Berends said that the economic meltdown of 2008 and lingering global economic malaise had a strong hand in slowing progress towards full condition-based monitoring, partly because owners have been unable to invest. In addition, in order to fully maximize equipment availability, optimize operating costs and minimize maintenance costs relies on collaboration involving operational-, IT- and financial managers in an integrated business case. But Berends is blunt: “It has proved a challenge to get the right stakeholders at the same table.”
“Life-cycle management of vessels is surely available, but owners are skeptical about making investments based on promises that there will be savings later on. They are more receptive to straightforward propositions that are economical, rather than complex proposals whose benefits are hard to measure. Our position is that we can do pretty much anything the owner requests, but our experience is that it is better to offer gains that are simply understood and tangible.”
Berends cites Imtech Marine’s Advanced Support Agreement with Seaway Heavy Lifting (SHL), covering all of the systems onboard. He offers the example of the vessel Oleg Strashnov, where crew working offshore in the Indian Ocean discovered issues with the telephone system but Imtech Marine was able to carry out a remote repair. This avoided a six week application process covering service engineer permits to get onboard.
Berends said that remote monitoring of equipment is, by now, an implicit expectation when it comes to meeting the agenda set by regulators. “Regulatory compliance and environmental protection, such as the verification of CO2 emissions, rely on this type of reporting capability. Data collection is also simply the first step of the staged approach for further measures to increase ship efficiency as proposed at IMO.”
However, to bring home the true potential of the remote approach, one of Imtech’s recent initiatives has been to offer customers an audit after one year. He believes any owner resistance will be best addressed by offering solutions that can be proven to work every step of the way. For this reason, Imtech has broken down its remote services offer into a phased and digestible commitment for owners.
“At the new build stage, where the equipment still has to be delivered, we not only include lay-out and cabling specifications that will facilitate Remote Monitoring; we are prepared to agree a MoU that includes key performance indicators,” said Berends.
“Once the capability is in place, after an agreed period, we as supplier and the end user are in a truly informed position. After 12 months, for example, we take the opportunity to sit down with our customer to evaluate and discuss the way forward, and whether their experience persuades them to include more vessels/other types of vessels in the program.”
Earlier this year, Imtech put another building block in place to enhance remote capability by taking its VDR-connectivity concept live, working with Danelec to offer real time communications between ship systems and shipping offices on the safety critical information harvested from real operations.
“All VDR data from ship to shore are presented via a web interface to the customer’s office, for scrutiny by superintendents and fleet managers,” said Berends. “This provides an overview of navigation equipment data and performance, and the ability to check operational performance such as speed vs. fuel consumption on a random basis. Safety is also enhanced; as well as the chance to review compliance using precise data, Imtech offers an option for real time alerts on non-compliance.
“Reviewing VDR data means the service company can correct settings remotely or, optionally, the remote configuration of all automation and processing technology can be reviewed in advance of the vessel being attended by service engineers.”
Van Leeuwen believes the building blocks have been put in place to overcome owner skepticism on the benefits of the remote service offer. “Identifying problems using consistent data that can be interrogated in the right way, having the right processes in place and having the right people available at our GTACs brings direct cost savings,” he says. “It also ensures that when our service engineers are required to board a ship they do so fully informed and ready to act.”
(As published in the August 2014 edition of Maritime Reporter & Engineering News - http://magazines.marinelink.com/Magazines/MaritimeReporter)
Read Remote Diagnostics Help Drive Efficiency Gains in Pdf, Flash or Html5 edition of August 2014 Maritime Reporter
Other stories from August 2014 issue
Content
- Editorial: software ... is it ‘evolution’ or ‘revolution’ ... page: 6
- Wishful Thinking From Across the Pond page: 8
- Panama Canal: The Billion Dollar Challenge page: 12
- OSV Power page: 14
- Polar Code Afoot page: 18
- Logistical Scenario Analysis for Hydrodynamic Applications page: 22
- Challenging the Myths of Pirate Violence page: 24
- Ballast Water Leadership page: 28
- Floating Production Roundup: August 2014 page: 32
- Keeping Machinery in Line with Laser Alignment page: 38
- Remote Diagnostics Help Drive Efficiency Gains page: 42
- News Flash! Greek Shipowners Prefer Bulkers page: 45
- Five Minutes with Gulf Copper’s Dennis Buffo page: 48
- BAE Systems Ship Repair: Leveraging Location, Infrastructure & Workforce page: 50
- Dry Dock Conference 2014 page: 52
- Spotlight on German Shipbuilding page: 58
- ZF Marine Makes a Strong Towboat Thrust page: 62
- Permanent Magnet Technology for Maritime Propulsion page: 62
- Ship Design and Construction Software Solutions page: 67
- Marorka’s Powerplay page: 72
- Indian Shipbuilding on the Road to Recovery page: 76
- Five Minutes with N-KOM CEO Abu Bakar Mohd Nor page: 80
- Realizing the Promise of Brazil Shipbuilding page: 84
- MTR 100: UTEC Survey Inc. page: 85
- ASRY All in on Project Jupiter page: 88
- Navantia Banks on the Future page: 89
- Energy Markets Buoy U.S. Shipbuilding page: 90
- Vigor: Frank(ly) Speaking page: 94
- Need a Lift? page: 96
- Dockside Load Testing with Unique Seaflex page: 97
- The Lowdown on Lifting page: 102
- SmartGrip: An ‘Evolution’ in Bulk Handling page: 104
- Shippers Must Reduce Costs, Boost Efficiency page: 106
- Fight Piracy – Intelligently page: 110
- Using HydroComp NavCad page: 112
- Keep it Clean & Green page: 114
- Victaulic Vic-Press System Receives Five New Type Approvals page: 119
- Bolidt Decking, Flooring page: 119
- Steering Alert System page: 119
- Bug-O Zipper Welder page: 119
- Envitia Launches MapLink Pro 8.0 page: 119
- Vosta LMG Delivers New Dredge Ball Joints page: 119
- Furuno Adds Color Display to NavPilot 700 Series page: 119