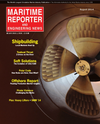
ZF Marine Makes a Strong Towboat Thrust
When German industrial manufacturing giant ZF bought Holland Rudder Propeller nearly five years ago, it was a strategic addition to its ZF Marine portfolio that is now reaping big rewards as it is enjoying strong penetration of its azimuth thruster systems in the U.S. towboat market. Maritime Reporter & Engineering News visited with Frank van der Vegt, Sales Manager, Commercial Craft Thruster Systems, at the ZF Marine Krimpen B.V. factory in The Netherlands for an update.
The marine business, particularly the inland marine business here and abroad, is generally conservative in its uptake of new technologies, particularly when it comes to the vessel’s power system. Simply put, there is still a proliferation of smaller, tightly held companies that have been managed and operated for multiple generations, with the preference to lean on accrued experience.
But the market is changing, driven by larger corporate entities nudging their way into these tightly held markets, and also by a myriad of legislative and operational conditions – namely the rapidly rising cost of fuel. ZF Marine – or more specifically ZF Marine Krimpen b.v., the commercial thruster manufacturer – is poised to profit as it builds an enviable reference list of inland towboat companies enjoying operational advantages and tremendous fuel savings courtesy of its thruster solution.
2009: A Pivotal Year
ZF bought HRP Thruster Systems B.V. in 2009, a strategic purchase that proved to be the proverbial ‘win-win’ for both companies. HRP was at a crossroads, faced with investing heavily in infrastructure and people to grow its organization to a level where it was capable to serve clients globally, or linking up with an organization with a global network in place.
ZF turned out to be a perfect partner.
ZF Group, an industrial behemoth with $22.4 billion in sales and 72,643 employees at the end of 2013, was looking to add marine thruster technology to its ZF Marine family of products, and it already had the established network of sales and service in place, as well as the engineering horsepower and organizational structure to grow the thruster business quickly and effectively.
“Essentially, we went from a small company to a big company, and the way in which we view and approach the market is significantly different,” said Frank van der Vegt, Sales Manager, Commercial Craft Thruster Systems, ZF Marine Krimpen B.V. “For example, we could have never pulled off what we did in the Americas market – the penetration of the inland tow boat market – as a small company.”
“The way it is taking off now means that you need a lot of focus, a lot of attention and a lot of people on site. So we used the strength of the ZF organization, in this case in America, to give this focus and to bring this to the next level.”
What the company has pulled off is a penetration and rapid growth in the inland towboat sector, a conservative niche that traditionally had not embraced azimuth thruster technology. Aside from the fact that it’s “new,” a primary stumbling block was the concern of potential damage to the units on the shallow draft and ever changing inland waterway system.
Key to opening any market in any industry is finding a willing, stable partner, which is exactly what ZF Marine found in the Southern Towing Company, headquartered in Memphis, Tenn. (See related story, page 64). Southern Towing is an innovator in the name of environmental excellence and operational efficiency, and starting in 2008 it started outfitting a number of its new build towboats with the innovative rudder propellers.
“It’s very much an industry where everyone waits for the first guy to do it and everyone watches,” said van der Vegt. “And I think you’re seeing that on the inland waterway market with some of the big companies that can absorb a first vessel project like this to test the technology. These big companies build one or two boats and get them in revenue service and compare them apples to apples. The smaller companies really watch for the results.”
According to van der Vegt, the results in the case of Southern Towing are nothing short of amazing, as the company reported a nearly 30% savings in fuel costs. “When you look at the fuel savings, it’s always difficult to give exact numbers because it is so dependent on how you are using the equipment. The savings is highly dependent on the vessel, route and operator, but I think that at least a 20% fuel savings for this type of push boat application is a safe number to mention.”
“This is America, so it’s big and the industry is big. There the potential is enormous,” said van der Vegt in summarizing the U.S. market.
Opportunities Abound
While the U.S. inland towboat market is large and promising, it certainly is not the only market in play for this propulsion tech.
“The advantage in push boat performance is you have cleaner thrust coming through the kort nozzles, so there is not a parasitic loss of the propulsion power that you have in a traditional vessel,” said van der Vegt.
“So you get more pure directional thrust pushing, pulling and turning the tow. You can get equivalent performance in a smaller power output, and so we are seeing with the tug fleets they are able to use smaller engines, meaning they are lighter, and with less weight penalty they are more fuel efficient.”
“A 1,400 hp pushboat (with the Z-Drive) can perform the same as a conventionally outfitted boat with 2,000 hp– same barges, same loads – as each thruster has full power at 360 degrees. With traditional systems you only have full power in one direction.”
While the U.S. market is large, well-established and still in its infancy in adopting Z-Drives, there are many emerging markets with mammoth river systems, namely South America and the Amazon River system, that present good opportunity as well.
“We see the demand increasing for deck mounted units in the Amazon, as well as some of the big river systems in Africa that are growing along with the oil business,” said van der Vegt. He explained that the rudder propeller solution, particularly the deck-mounted version, is particularly attractive in remote areas where there are a dearth of marine facilities or infrastructure, as the deck-mounted unites are easy to maintain and replace without the need of a shipyard. In addition, many emerging markets want to build the boats locally to feed the local market, and with the deck-mounted solution the countries can build their barges locally than easily add the propulsion solution.”
While azimuth thruster technology comes with a number of advantages, the main reservation has been that the Z-Drive – which hangs below the vessel – is more vulnerable to damage than traditional systems, particularly on the shallow draft, oft changing and sometimes litter-strewn inland waterways.
Here the ZF global network of supply comes into play, as it realizes that keeping a boat in revenue service is priority number one, two and three for these operators. To that end, it emphasizes that a key strategic advantage is that – if the unit is installed as a top-mount thruster – it can be pulled and replaced with a swing unit easily and quickly – sometimes between eight to 10 hours – while the boat stays in the water.
An Engineered Solution
A key challenge in any manufacturing business is controlling costs in the design and production shops, and the ZF Marine thruster business is no exception. In fact, as this business unit produces no ‘standard’ units, it is particularly adept at looking at the project as a whole to design with the naval architect, with the shipyard and ultimately with the owner what is agreed to be an optimal solution.
“If a client comes in and says ‘I want a 2000 horsepower boat,’ our first questions are: What do you want to do with the boat?; What are you going to be pushing?; What kind of thrust do you need?,” said van der Vegt. He explained that thrusters can offers several power and maneuverability advantages; for example of a vessel outfitted a traditional power train may require a 2000 hp power plant, whereas a vessel outfitted with a thruster may need only a 1400 hp power plant, offering substantial space, weight and fuel consumption advantages. “We want to offer an optimum solution based on what the client wants to do with the boat, and the interaction with the client is crucial” because it doesn’t manufacture and house standard thrusters that are simply off-the-shelf.
Prior to the global economic meltdown of 2008, Holland Rudder Propeller – like many of its marine power supply colleagues – had much slower delivery times due in part to the size of the order books, in part due to the fact that parts and materials were sometimes difficult to procure. With the acquisition by ZF in 2009 and the incorporation of its engineering and production philosophies and practices, today van der Vegt said that delivery times range between five and eight months, which is a key plank in extending its platform in North America as he said U.S. shipyards build boats faster than its European counterparts.
Coming Home
While the primary focus of this article is thruster adoption on inland waterways vessels, the market for ZF Marine Krimpen b.v. extends far beyond the towboat sector.
“More and more the azimuth thrusters are used in all types of vessels, said van der Vegt.
“Where traditionally it was generally relegated to ferries and workboats, as the advantages become more obvious we supply units to an ever widening sector, including megayachts, tugboats as well as jack-up vessels and huge offshore construction vessels.”
An interesting application which we witnessed first-hand at the Krimpen facility was a massive 2MW Retractable Azimuth Thruster with a 2.4m propeller – the largest retractable unit in the ZF Marine Krimpen repertoire – destined for installation on a new military tanker.
When the ship is sailing, the thruster will be retracted and not in use. Its use on the ship will include:
• As a thruster when the ship is in Dynamic Positioning mode.
• As a transverse bowthruster when retracted
• As a “homecoming” device that – in the event that main propulsion is lost – can help the ship navigate away from trouble and back home.
This project is notable, too, as it features the company’s next-generation control system, which incorporates the latest in touch screen, multi-function and multi-layer technologies that is aimed to make thruster operations more precise, safe and efficient.
ZF Marine Krimpen b.v.
When ZF took over in 2009, HRP Thruster Systems B.V. was at a crossroads. It was faced with investing heavily in infrastructure and people to grow its organization to a level where it was capable internationally, or it needed to link up with an organization that already had the global network in place. ZF was the perfect partner in this regard, as it had the established network of sales and service in place, as well as the engineering horsepower and organizational structure to grow the thruster business quickly and effectively.
“Essentially, we went from a small company to a big company, and the way in which we view and approach the market is significantly different,” said Frank van der Vegt, Sales Manager, Commercial Craft Thruster Systems, ZF Marine Krimpen B.V. “For example, we could have never pulled off what we did in the Americas market – the penetration of the inland tow boat market – as a small company. This fit was good for ZF Group as well, a privately owned industrial behemoth with $22.4 billion and 72,643 employees at the end of 2013 that wanted to add this technology to its ZF Marine family of products.
HRP has been in the thruster market since 1973, designing and producing a wide range of steerable thrusters for all types of marine applications.
ZF Group By the Numbers
When ZF touts its global capability, it ‘walks the walk’ with the numbers to back it up. Some impressive end of 2013 numbers include:
Sales $22.4 billion
Employees 72,643
R&D Expenditure $1.1 billion
• 122 production companies in 26 countries
• 8 main development locations in
4 countries
• 33 service companies
• 724 patent applications in 2013
(Top 10 in patent applicants in Germany)
Southern Towing: Z-Drive Pioneer
Southern Towing Company, headquartered in Memphis, Tenn., is one of the nation’s largest transporters of fertilizer and other products along the nation’s inland waterways. For more than 50 years, it has operated the largest fleet of anhydrous ammonia barges in the U.S. As ZF Marine will attest, the company prides itself on building and running a cutting edge fleet, including its fuel efficient and environmentally friendly Z-Drive tug boats.
While it certainly was not the first to ever install Z-Drives on towing vessels, it was an early and fervent supporter of the technology. “What you need is someone who is a believer and is willing to take the risk,” said Frank van der Vegt, Sales Manager, Commercial Craft Thruster Systems, ZF Marine Krimpen B.V. “Our believer was Southern Towing Company.”
“It’s very much an industry where everyone waits for the first guy to do it, and everyone watches. And I think you’re seeing that on the inland waterway market with some of the big companies that can absorb a first vessel project like this to test the technology. These big companies build one or two boats and get them in revenue service and compare them apples to apples. The smaller companies really watch for the results.”
Beginning in 2008, Southern Towing unveiled four new Z-Drive boats that were to deliver unrivaled maneuverability on challenging inland waterways, as well as fuel efficiency in the face of rapidly rising fuel costs. Southern Towing vessels with ZF Marine Z-Drives include the vessels listed to the right:
(As published in the August 2014 edition of Maritime Reporter & Engineering News - http://magazines.marinelink.com/Magazines/MaritimeReporter)
Read ZF Marine Makes a Strong Towboat Thrust in Pdf, Flash or Html5 edition of August 2014 Maritime Reporter
Other stories from August 2014 issue
Content
- Editorial: software ... is it ‘evolution’ or ‘revolution’ ... page: 6
- Wishful Thinking From Across the Pond page: 8
- Panama Canal: The Billion Dollar Challenge page: 12
- OSV Power page: 14
- Polar Code Afoot page: 18
- Logistical Scenario Analysis for Hydrodynamic Applications page: 22
- Challenging the Myths of Pirate Violence page: 24
- Ballast Water Leadership page: 28
- Floating Production Roundup: August 2014 page: 32
- Keeping Machinery in Line with Laser Alignment page: 38
- Remote Diagnostics Help Drive Efficiency Gains page: 42
- News Flash! Greek Shipowners Prefer Bulkers page: 45
- Five Minutes with Gulf Copper’s Dennis Buffo page: 48
- BAE Systems Ship Repair: Leveraging Location, Infrastructure & Workforce page: 50
- Dry Dock Conference 2014 page: 52
- Spotlight on German Shipbuilding page: 58
- ZF Marine Makes a Strong Towboat Thrust page: 62
- Permanent Magnet Technology for Maritime Propulsion page: 62
- Ship Design and Construction Software Solutions page: 67
- Marorka’s Powerplay page: 72
- Indian Shipbuilding on the Road to Recovery page: 76
- Five Minutes with N-KOM CEO Abu Bakar Mohd Nor page: 80
- Realizing the Promise of Brazil Shipbuilding page: 84
- MTR 100: UTEC Survey Inc. page: 85
- ASRY All in on Project Jupiter page: 88
- Navantia Banks on the Future page: 89
- Energy Markets Buoy U.S. Shipbuilding page: 90
- Vigor: Frank(ly) Speaking page: 94
- Need a Lift? page: 96
- Dockside Load Testing with Unique Seaflex page: 97
- The Lowdown on Lifting page: 102
- SmartGrip: An ‘Evolution’ in Bulk Handling page: 104
- Shippers Must Reduce Costs, Boost Efficiency page: 106
- Fight Piracy – Intelligently page: 110
- Using HydroComp NavCad page: 112
- Keep it Clean & Green page: 114
- Victaulic Vic-Press System Receives Five New Type Approvals page: 119
- Bolidt Decking, Flooring page: 119
- Steering Alert System page: 119
- Bug-O Zipper Welder page: 119
- Envitia Launches MapLink Pro 8.0 page: 119
- Vosta LMG Delivers New Dredge Ball Joints page: 119
- Furuno Adds Color Display to NavPilot 700 Series page: 119