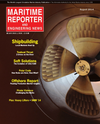
Keeping Machinery in Line with Laser Alignment
Keeping your machinery in line to maximize your bottom line
If you operate a vessel, its machinery, without a doubt, will require alignment many times during the course if its life. When misalignment is present components will be worn, efficiency will be lost, and, if left uncorrected, mechanical failures are imminent. This translates into a strain on mechanical systems, your budget, and your peace of mind.
When speaking of alignment in marine applications, it is usually shaft alignment that is being referenced. Shaft alignment is defined as the positioning of two or more machines which so that at the point of power transfer from one shaft to another, the axes of rotation of both shafts should be collinear when the machine is running under normal conditions (DB Pruftechnik, An Engineer’s Guide to Shaft Alignment, Vibration Analysis & Dynamic Balancing, courtesy of LUDECA, Inc.).
The symptoms of misalignment are often noticeable, and include increased vibration, which can shorten machine life; extra load and added stress on components; and, an increase of heat output from prime movers, which draws more current. This causes increased fuel consumption, in turn, increasing carbon emissions. Misalignment in rotating machinery increases energy costs, coupling damage, and repetitive shaft seal, as well as bearing failure.
There are many causes of misalignment, and one of the most common is the aging of the engine mounts. Engine mounts have rubber elements which over time degrade and harden, causing wear and an inability to properly isolate the forces transmitted by the engine and maintain alignment during operation. Likewise, if the improper mounts were used or incorrectly installed, engine forces would again not be correctly isolated causing misalignment. If left untreated or not replaced, improper support of the engine will cause it to shift and could compromise the running gear.
“Depending on the arrangement and installation, mounts should be changed every 5-10 years since this is when the properties of rubber are most likely to degrade and begin causing problems. It’s considered good practice to change main propulsion thrust bearing mounts more frequently, as the absorption of force reduces their life span,” said Rich Merhige, President, Advanced Mechanical Enterprises, a mechanical engineering services firm headquartered in South Florida. “Mounts should also be kept free of any oil, as its contact with rubber will also cause premature wear.”
Running aground is another frequent cause of misalignment. Even getting some line tangled in a propeller can shift the struts, causing them to move out of alignment. Other causes of misalignment include the changing of the hull shape (hull deflection), which is why pre-and post-hull deflection measurements are crucial for proper alignments. AME uses the Levalign Ultra, a self-leveling rotating laser system to conduct this procedure which is vital to successful haul-outs. Likewise, a final laser alignment check should be done oncethe vessel has been waterborne, and has had a chance to settle 24 hours. Hull deflection is often overlooked during the build process resulting in misalignment.
Misalignment, regardless of its origin, can cause rapid wear on bearings, damage shafts requiring them to be repaired, and in more extreme cases replaced. Extreme vibration can cause increased damage to engine mounts, and the reduction gears, sometimes even causing failure. Shaft sealing systems can also become damaged, and need to be replaced. When machinery is correctly aligned, a 1-3% increase in energy efficiency can be achieved.
Since misalignment is a major source of vibration, the most accurate, efficient, and economic way to diagnose misalignment is to conduct a vibration analysis. Vibration analysis can identify what mechanical issues a vessel is having and eliminates the guesswork that way too often comes into play with repair services. More specifically, it can determine exactly where misalignment is present.
“When a client first calls requesting service work, most specifically an engine alignment, the first thing my staff asks, is if they’ve had a vibration analysis, to verify and pinpoint the cause of the misalignment,” said Merhige. “It’s very easy to proceed on the presumption that the cause and location of the misalignment is known. But, without a proper diagnosis with vibration analysis, a simple service call could turn into a major ordeal when issues are continuously uncovered.”
Data is collected in accordance with guidelines set forth by the Society of Naval Architects and Marine Engineers, as well as different class societies. This data provides a thorough machine condition evaluation and can detect a multitude of problems using known frequencies specific to the vessel, including, but not limited to:
• Misalignment of shaft couplings, flexible machine couplings
• Misalignment of underwater running gear such as propeller struts
• Propeller defects
• Bent shafts
• Unbalance of rotating components
• Main engine misfire problems
• Mechanical looseness
• Deterioration of rolling-element bearings within transmissions and thrust bearings
• Gear tooth wear
• Mechanical rubbing
• Structural resonance
• Machinery soft-foot conditions
Another way to diagnose misalignment is by conducting periodic alignment checks. In accordance with good marine practice, alignment should be checked six months to a year after a new installation; when experiencing a shaft seal or bearing failure or when a bearing is replaced. Once the data from a vibration analysis or laser check is analyzed a proper course of action can be implemented, which includes an alignment procedure based on the mechanical arrangement of the components involved in the misalignment, as well as the specific issue at hand.
Generally speaking, misalignments are corrected with either laser and/or optical alignments. Optical alignments are performed using optical borescopes, and must be done out of the water when the running gear has been removed. Laser alignment is the process of measuring misalignment between mechanical components, usually one or more shafts. It is a precise way to align machinery while minimizing the likelihood of human error. It utilizes laser beam transmitters and receivers to attain alignment within extremely high tolerances.
The first laser alignment systems surfaced in the early 1960’s. Laser beams were applied later to alignment applications to maintain a line of sight. Prior to the use of lasers, piano wire was often used for alignment. Wire posed problems, as one could imagine. The weight of a wire can cause sagging, and even environmental factors can cause it to move, causing great inaccuracies. Since light travels in a straight line, lasers were an easy choice as a replacement for precision alignments.
Today, there are many types of laser alignment systems. PRÜFTECHNIK, a manufacturer for some of the most advanced German-engineered laser alignment systems on the market, is sold locally in the southeast by Ludeca, headquartered in Miami. Some of the most notable units include the Rotalign Ultra IS, and Levalign Expert. The Rotalign Ultra IS is an all-in-one high end alignment system that can be used for geometric applications. It can measure hundreds of positions and allows for one-step machine corrections in vertical and horizontal directions. The Levalign Expert is a self-leveling, spinning laser that measures flatness, straightness, parallelism, and perpendicularity. Both systems are utilized by AME, who works closely with Ludeca to keep up to date on training and the latest alignment applications and software updates. Relationships such as this provide for a plethora of opportunities to solve some of the world’s most challenging misalignment issues, particularly in the marine market.
Most recently, AME was commissioned by one of the world’s largest marine solutions, transportation and logistics company to conduct shaft alignments for newly installed generators on its three 750 Class Articulated Tug Barges (ATB). When the generators were installed, AME field service engineers were tasked with aligning the generator shafts to the PTO of the main reduction gears. First, rough alignments were done with a digital protractor being used to keep the same transversal level with the engine. Axial alignment was attained and set according to the coupling manufacturer’s specifications and radial and angular alignment was set using the Rotalign Ultra. Thermal growth offset was applied to allow for thermal growth of the two units. Aluminum forms were then built for the pouring of Chockfast Epoxy Orange, which is a resin chocking system that has an excellent reputation for setting installations and maintaining alignments, particularly for marine applications. Once poured into the forms, it was left to cure for a period of 18-24 hours. AME field service engineers then conducted their final laser alignment checked, before torqueing the hold down bolts on the unit as required.
“The sensor technology of the Rotalign Ultra allowed for this particular alignment to be attained with a simultaneous horizontal and vertical move using the jacking bolts,” said Daus Studenberg, Applications Engineer, Ludeca, Inc. “Most systems would have required that this move be broken down into two steps to achieve alignment, which would have utilized more man hours and end up costing the client more money.”
Once the alignments were completed, vibration analysis was conducted on each of the units to confirm proper installation and alignment. Recommendations were then made for periodic alignment checks to maintain optimum performance, efficiency, and preventing premature wear of components.
“We use vibration analysis as a diagnostic tool to solve mechanical issues. Misalignment is the cause of those issues a significant amount of the time,” commented Merhige. “Formal education, hands on training, and field experience, coupled with access to the most state-of-the-art alignment systems can prove to be extremely beneficial for maintenance budgets, often, with an immediate and noticeable ROI. Bottom line, an investment in alignment pays dividends when it comes to mechanical health.”
The Authors
Rich Merhige has over 31 years of condition monitoring experience. He founded/is President of AME, which is recognized as an external specialist for condition monitoring by ABS.
[email protected]
Teresa Drugatz joined AME in 2010 as Office/Marketing Manager. She holds a bachelor of science in communication from the University of Miami.
[email protected]
(As published in the August 2014 edition of Maritime Reporter & Engineering News - http://magazines.marinelink.com/Magazines/MaritimeReporter)
Read Keeping Machinery in Line with Laser Alignment in Pdf, Flash or Html5 edition of August 2014 Maritime Reporter
Other stories from August 2014 issue
Content
- Editorial: software ... is it ‘evolution’ or ‘revolution’ ... page: 6
- Wishful Thinking From Across the Pond page: 8
- Panama Canal: The Billion Dollar Challenge page: 12
- OSV Power page: 14
- Polar Code Afoot page: 18
- Logistical Scenario Analysis for Hydrodynamic Applications page: 22
- Challenging the Myths of Pirate Violence page: 24
- Ballast Water Leadership page: 28
- Floating Production Roundup: August 2014 page: 32
- Keeping Machinery in Line with Laser Alignment page: 38
- Remote Diagnostics Help Drive Efficiency Gains page: 42
- News Flash! Greek Shipowners Prefer Bulkers page: 45
- Five Minutes with Gulf Copper’s Dennis Buffo page: 48
- BAE Systems Ship Repair: Leveraging Location, Infrastructure & Workforce page: 50
- Dry Dock Conference 2014 page: 52
- Spotlight on German Shipbuilding page: 58
- ZF Marine Makes a Strong Towboat Thrust page: 62
- Permanent Magnet Technology for Maritime Propulsion page: 62
- Ship Design and Construction Software Solutions page: 67
- Marorka’s Powerplay page: 72
- Indian Shipbuilding on the Road to Recovery page: 76
- Five Minutes with N-KOM CEO Abu Bakar Mohd Nor page: 80
- Realizing the Promise of Brazil Shipbuilding page: 84
- MTR 100: UTEC Survey Inc. page: 85
- ASRY All in on Project Jupiter page: 88
- Navantia Banks on the Future page: 89
- Energy Markets Buoy U.S. Shipbuilding page: 90
- Vigor: Frank(ly) Speaking page: 94
- Need a Lift? page: 96
- Dockside Load Testing with Unique Seaflex page: 97
- The Lowdown on Lifting page: 102
- SmartGrip: An ‘Evolution’ in Bulk Handling page: 104
- Shippers Must Reduce Costs, Boost Efficiency page: 106
- Fight Piracy – Intelligently page: 110
- Using HydroComp NavCad page: 112
- Keep it Clean & Green page: 114
- Victaulic Vic-Press System Receives Five New Type Approvals page: 119
- Bolidt Decking, Flooring page: 119
- Steering Alert System page: 119
- Bug-O Zipper Welder page: 119
- Envitia Launches MapLink Pro 8.0 page: 119
- Vosta LMG Delivers New Dredge Ball Joints page: 119
- Furuno Adds Color Display to NavPilot 700 Series page: 119