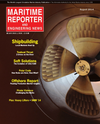
Dockside Load Testing with Unique Seaflex
Static load testing is an essential part of many engineering, building and manufacturing businesses – and the shipping, marine and offshore industry is no exception. Water filled weights (also known as ballast bags) provide a flexible method for load testing. Test weights must be sufficiently heavy to ascertain the maximum load of an object, but they should also be reusable and safe to deploy in a test environment. Where there is easy access to a plentiful supply of water, water-filled weights can provide a quick, efficient means to undertake such testing. When empty the bags weigh a small fraction of the filled weight (typically less than 1% of their capacity) – and can be packed into transit crates, making them easy to deploy and pack down again for storage between jobs. In use they can be partially filled for any exacting requirements, or used in combination to achieve larger test capacities.
Once filled with water, these bags will generally weigh anywhere from 1,000 Kg to 50,000 Kg. Larger sizes are possible, but beyond 50t the handling benefits start to diminish. Objects can be tested in various ways: for example, test weights might be attached to the center of a steel arch to ascertain load capacity before being (vertically) affixed to one end to test tensile strength. Understanding how components, parts or materials behave under extreme loads in different positions can help engineers create safer and more powerful systems.
Although capable of being used almost anywhere, water-filled weights are often deployed in docks to ensure that parts can be tested without fear of causing structural damage (failed components and the weights attached to them can simply fall into the water). To ensure that materials are tested accurately, the risk of cable failure is reduced by the inclusion of telemetry dual-load shackles and tensile load cells. There are no globally-recognized standards governing this field of work, but the nearest are the 051 Guidelines as developed and published by the Lifting Equipment Engineers Association (LEEA) – a U.K. body which is gaining increased worldwide recognition. Its 051 Guidelines cover the design, inspection and use of such bags as test weights within the offshore and marine industries – and focuses in particular upon subjects such as component suitability and traceability, manufacturing test regimes, and the desirability of having drop-tested bags of each size to prove that they are capable of withstanding a peak load of 6x their capacity, or working load limit. Unique Maritime Group’s Unique Seaflex is at the forefront of being able to demonstrate compliance to these LEEA guidelines. Working within the limitations of the largest test rig it could find, all of its water bags have proven themselves capable of withstanding overloads many times in excess of their working load limits – with Type Test Certification and Product Design Assessment Certification from ABS by way of independent verification of the integrity of their designs.
www.uniquegroup.com
(As published in the August 2014 edition of Maritime Reporter & Engineering News - http://magazines.marinelink.com/Magazines/MaritimeReporter)
Read Dockside Load Testing with Unique Seaflex in Pdf, Flash or Html5 edition of August 2014 Maritime Reporter
Other stories from August 2014 issue
Content
- Editorial: software ... is it ‘evolution’ or ‘revolution’ ... page: 6
- Wishful Thinking From Across the Pond page: 8
- Panama Canal: The Billion Dollar Challenge page: 12
- OSV Power page: 14
- Polar Code Afoot page: 18
- Logistical Scenario Analysis for Hydrodynamic Applications page: 22
- Challenging the Myths of Pirate Violence page: 24
- Ballast Water Leadership page: 28
- Floating Production Roundup: August 2014 page: 32
- Keeping Machinery in Line with Laser Alignment page: 38
- Remote Diagnostics Help Drive Efficiency Gains page: 42
- News Flash! Greek Shipowners Prefer Bulkers page: 45
- Five Minutes with Gulf Copper’s Dennis Buffo page: 48
- BAE Systems Ship Repair: Leveraging Location, Infrastructure & Workforce page: 50
- Dry Dock Conference 2014 page: 52
- Spotlight on German Shipbuilding page: 58
- ZF Marine Makes a Strong Towboat Thrust page: 62
- Permanent Magnet Technology for Maritime Propulsion page: 62
- Ship Design and Construction Software Solutions page: 67
- Marorka’s Powerplay page: 72
- Indian Shipbuilding on the Road to Recovery page: 76
- Five Minutes with N-KOM CEO Abu Bakar Mohd Nor page: 80
- Realizing the Promise of Brazil Shipbuilding page: 84
- MTR 100: UTEC Survey Inc. page: 85
- ASRY All in on Project Jupiter page: 88
- Navantia Banks on the Future page: 89
- Energy Markets Buoy U.S. Shipbuilding page: 90
- Vigor: Frank(ly) Speaking page: 94
- Need a Lift? page: 96
- Dockside Load Testing with Unique Seaflex page: 97
- The Lowdown on Lifting page: 102
- SmartGrip: An ‘Evolution’ in Bulk Handling page: 104
- Shippers Must Reduce Costs, Boost Efficiency page: 106
- Fight Piracy – Intelligently page: 110
- Using HydroComp NavCad page: 112
- Keep it Clean & Green page: 114
- Victaulic Vic-Press System Receives Five New Type Approvals page: 119
- Bolidt Decking, Flooring page: 119
- Steering Alert System page: 119
- Bug-O Zipper Welder page: 119
- Envitia Launches MapLink Pro 8.0 page: 119
- Vosta LMG Delivers New Dredge Ball Joints page: 119
- Furuno Adds Color Display to NavPilot 700 Series page: 119