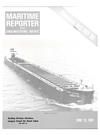
Interlake's 'De Lancey' Christened- Longest Vessel On The Great Lakes
The motor vessel William J. De Lancey (shown above), at 1,013.5 feet the longest vessel on the Great Lakes, was christened recently.
The vessel was built for The Interlake Steamship Company, which is operated by Pickands Mather & Company, Cleveland.
Pickands Mather is a subsidiary of Moore McCormack Resources, Inc., Stamford, Conn.
Named in honor of William J.
De Lancey, chairman and chief executive officer of Republic Steel Corporation, Cleveland, and christened by his wife, Sally Roe De Lancey, the vessel was designed and built by the AmShip Division of The American Ship Building Company at its Lorain, Ohio, shipyard.
"This new vessel will serve as a major element in fulfilling the 25-year haulage contract that we have signed with Republic," said Elton Hoyt III, p r e s i d e n t and chief executive officer of Pickands Mather. "The De Lancey represents one of the final links in the overall material-handling system Republic Steel will utilize to move iron ore from its source to the company's steelmaking complexes.
The PM/Republic haulage contract calls for PM to carry up to seven million tons in 1981 and subsequent years." The De Lancey joins PM's two other 1,000-foot supercarriers, the flagship James R. Barker and the Mesabi Miner. The De Lancey, as well as other vessels in the Interlake Steamship fleet, will carry Republic ore from Silver Bay and other Lake Superior ports to Re- public's newly constructed Lorain Pellet Terminal at Lorain on Lake Erie.
The De Lancey's size is dictated by America's requirement to move raw materials as quickly and economically as possible. Her unparalleled capacity (60,500 long tons of iron ore and in excess of 65,000 short tons of coal per trip), coupled with her fast turnaround time (six hours) and operating efficiency, will play a major role in meeting that need. The De Lancey's beam of 105 feet leaves only 5 feet of clearance at the Poe Lock of the Sault Ste. Marie Canal, widest lock on the Upper Lakes.
The De Lancey has been designed to maximize cargo-carrying capacity while ensuring optimum operating efficiency and reliability.
With all controls and crew q u a r t e r s a f t , maximum space has been devoted to cargo capacity. In effect, the ship is a gigantic powered box. Engine controls and communications are simpler and more direct compared with conventional forward-wheelhouse design.
The vessel is double-hulled below the loadline, and all fuels, lubricants and sewage systems are located within the inner hull as an added safeguard against spills in case of outer hull rupture.
Nine ballast tanks are located along the sides of the ship between the inner and outer hull sections. Each vertical tank has its own pumping system with no i n t e r c o n n e c t e d piping between tanks, simplifying maintenance and providing a high degree of reliability.
The ballast tanks are flooded with water when the vessel is under way without cargo, lowering it in the water for increased maneuverability. The tanks are also kept flooded during loading operations to keep the deck hatches at a required level for dockside loading.
The huge cargo area is divided into five holds. A series of poweractuated gates in each hold feeds pellets or coal onto a conveyor belt that lies beneath the entire length of the cargo hold area. The De Lancey's unloading system is capable of discharging pellets at the rate of 10,000 tons per hour.
The 260-foot boom can swing to either side for piling cargo ashore under high-speed unloading conditions.
Main propulsion power for the De Lancey is provided by two 8,560-bhp Colt-Pielstick diesel engines.
Each engine is directly connected to a four-blade, 17V2-footdiameter controllable-pitch Bird- Johnson propeller through a specially designed reduction gear and shafting system.
Designers of the De Lancey were most concerned with two aspects of the main drive system— reliability and low maintenance.
The result is a simple, unencumbered drive system capable of delivering power to the propellers efficiently and in a minimum of space.
The arrangement of completely independent drive systems for each engine optimizes overall reliability; if for some reason one engine is nonoperational, the other can still power the ship. To keep the drive systems simple but highly reliable, the four 800-kw, 480-volt main electrical generators are driven by separate Caterpillar diesel engines rather than off the main propulsion drive unit as is the case in many other vessels.
The De Lancey has a maximum c a p a c i t y of 152,000 gallons of heavy fuel oil for main propulsion, and carries 31,000 gallons of light diesel oil fuel for generator, heater, and boiler service.
Each controllable-pitch propeller assembly is fitted with four stainless-steel movable blades. An a u t o m a t i c pitch-control system hydraulically changes propeller pitch according to engine speed to provide for optimum running economy and to prevent overloading and stalling the engines when the vessel is heavily loaded at low speeds. For example, when the engines are at maximum throttle, the propellers are at maximum pitch. Conversely, at idle speed, the propellers are at zero pitch.
Single-lever control handles in both the pilothouse and engine room provide for combined control of engine speed and propeller pitch. Provision is also made for a split control of speed and pitch from the pilothouse and engine room. Separate control units connected to the central pilothouse unit are located on both the port and starboard bridge wings.
Maneuvering the huge 1,000- footer is simplified by the twin screws and the arrangement of a rudder behind each propeller.
The ship also can be steered by varying the speed of each engine.
In addition, a 1,500-hp Bird- Johnson electrically driven bow thruster facilities docking by moving the bow to the right or left in much the same fashion as a tugboat.
Reversing is accomplished t h r o u g h the controllable-pitch propellers; the engines do not reverse.
This system greatly shortens the time to generate a reverse response as compared with turbine-powered systems.
Due to the De Lancey's ail-aft design and overall height of 118 feet, a personnel elevator whisks crew members from the engine control room level up the five decks to the level below the pilothouse.
The 31-man crew is housed aft in modern, comfortably furnished quarters. O f f i c e r s have single rooms, with only some of the crew sharing a room. Living quarters, the galley, and engineer's control compartment are all airconditioned.
The onboard St. Louis ship FAST sewage treatment plant, which meets stringent Federal standards, produces completely clean effluent for discharge, or for temporary holding while the vessel is in waters where discharge is prohibited by local regulations.
Read Interlake's 'De Lancey' Christened- Longest Vessel On The Great Lakes in Pdf, Flash or Html5 edition of June 15, 1981 Maritime Reporter
Other stories from June 15, 1981 issue
Content
- SPC Coatings Combat Rising Fuel Costs- Literature Available page: 5
- Ryan-Walsh Bulk Terminal In New Orleans Resumes Coal-Handling Operations page: 5
- National Marine Service Adds Sixth Drydock At Its Harvey Shipyard page: 6
- General Ship Expands Its Facilities In South Boston page: 6
- Floating Doughnut Crane Shown At Shugart Crane Conference page: 7
- RCA Opens Marine Services Office In Morgan City, La. page: 8
- Hans Schaefer Succeeds Arthur Stout As President Of Todd Shipyards page: 8
- David Parrot To Head New Aldenships Division Of John G. Alden Firm page: 9
- Edward Walsh Named Asst VP And Controller At J.J. Henry Company page: 9
- Second Occidental Tug/Barge Unit Christened At Avondale Yard page: 10
- Megasystems To Provide Automation Package For Southern-Built Dredge page: 10
- Interlake's 'De Lancey' Christened- Longest Vessel On The Great Lakes page: 12
- Dravo Negotiating To Buy Operating Assets Of Nilo Barge Line From Olin page: 14
- Brochure Available On Foster Wheeler Boilers And Auxiliary Equipment page: 14
- Vincent Ferraro Named Estimating VP For Savannah Shipyard page: 15
- Paceco Container Crane Arrives At Massport's Castle Island Terminal page: 15
- NASSCO Lays Keel Of First In Series Of Product Carriers For American Tankships page: 16
- Bay Shipbuilding Completes EMD-Powered Columbia Star page: 16
- Bryant Named Manager Of McGraw-Edison's New Marine Marketing Dept. page: 17
- Three New Technical Reports Available From Ship Structure Committee page: 17
- Penske Offers Brochure On Diesels/Gas Turbines For Marine/Offshore Power page: 18
- Subsidy Approved On USL Conversion Job To Cost $5.3 Million page: 18
- Consolidated Inland Opens East Division Office— R.R. Simms Named Manager page: 18
- El Paso Promotes Three- Harry Ray Named VP Of El Paso Marine page: 18
- Serrie Joins Levingston As VP Of Operations page: 19
- lotron Conducts ARPA Demonstration In New York City page: 20
- First Of Five Hydrofoil Combatants Launched By Boeing Marine Systems page: 20
- Levingston Reorganized— Barrios, Covington And Wise To Head Three Units page: 22
- B IW Awarded $247-Million Navy Contract To Build Three Missile Frigates page: 24
- North Florida Shipyards Appoints Three—White Named Production Manager page: 25
- Captain Barry Roberts Named CO Of USCG's Curtis Bay Shipyard page: 25
- James Retert Joins Waukesha Engine As Director Of Marketing page: 27
- New U.S. Built Coal-Fired Ship To Be Powered By G.E. Steam Turbine page: 27
- Wasacz Succeeds Gray As President Of Matson Navigation page: 28
- Bel-Aire Yard To Build Two Tuna Seiners At Total Cost Of $20 Million page: 29
- Washburn & Doughty Delivers Combination Scalloper-Dragger page: 34
- GE-Powered Product Carrier For Union Oil Christened At NASSCO page: 34
- South Jersey Port Orders Heavy Duty Multi-Purpose Crane From Kocks page: 35
- RORO81 PREVIEW page: 39
- First Of Three Waterman Combination Carriers Features Largest MacGregor Stern Ramp page: 40
- Canadian Yards And Government Speed Up Shipbuilding Training page: 41
- EDO Gets $3.9-Million Navy Award To Improve Existing ASW System page: 42
- Barber Steamship Lines Names Steven Roberts Assistant Vice President page: 43
- Navy Awards $276-Million Contract To Todd For Three Additional FFGs page: 43
- Promet Gets $60-Million Order For Drill Rig For Sedco Incorporated page: 44
- First Aegis Missile Cruiser Christened At Ingalls Yard page: 58
- Blount Delivers Commuter Boat To Fire Island Ferries page: 58