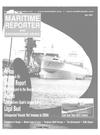
Packing Solutions Help Bear Set Sail
In August 2001, the Delamar Company received a call from the Engineering Officer aboard the 270-ft.
(82.2-m) USCG Cutter Bear. He described an oil leakage problem from the #1 (starboard) reduction gearbox.
The stern outdrive shaft's stuffing box could not maintain a good seal for any length of time, and would allow the leaking gear oil to sling off the rotating shaft onto adjacent clutches. Different types of compression packing had been tried, including graphite-impregnated, but none proved successful against the frictional heat and oil pressure.
Additionally, the shaft was suspected to be skewed and misaligned in relation to the gearbox.
Bear was scheduled to leave port in just a couple of days for duty, and this leakage wasn't acceptable during operation; it had to be fixed immediately.
The Solution After hearing the details of the situation, discussing the operational range of the machinery, and learning what types of packing had failed, Delamar recommended Slade 3300-G general-purpose packing for this application. This is a unique packing of cross-braided proprietary carbon fiber & vermiculated graphite yarns.
The 3300-G can withstand temperatures from 400 to 5,400° F, and handles pressures up to 5,000 psi at the same time. The construction and content of the 3300-G also allow it to seal against worn rotating equipment and without flush-water or seal-water at shaft speeds up to 4,800 ft./min. The 3300-G will also seal well in chemically active environments, with a pH range from one to 14.
The ship's crew removed the gland follower ring, and pulled out the old packing. The inside of the stuffing box was cleaned and new rings of 3300-G were cut to the proper length. Ring ends are cut at a 45-degree angle, and joints are staggered as each ring is installed into the stuffing box. Additionally, each ring of 3300-G is fully compressed before adding the next one. This application required only three rings, so the compression procedure is very important. Because of the shaft misalignment, each ring needed to squeeze each ring before installation.
The usual ,5-in. clearance between the shaft and stuffing box was less than 3/8-in. on one side and over 5/8-in. on the other. Hammering the 3300-G to accommodate the inconsistent clearance has no detrimental effects on the packing. Once the rings are installed and fully compressed by the tightened follower ring, they are die-formed into the stuffing box's geometry.
The Engineering Officer decided to test the repacked reduction gearbox by turning the shaft in port for about eight to 12 hours. There were no leaks, and he determined the repair to be seaworthy so Bear set sail for duty on time. During the first two weeks of the cruise, two minor tightening adjustments were made to the follower ring nuts to eliminate a slight oil drip.
Circle 173 on Reader Service Card www.maritimereporterinfo.com
Other stories from May 2002 issue
Content
- Delta Queen Makes A Comeback page: 3
- USS Cole Returns to Fleet page: 4
- Polar Discovery Christened at Avondale page: 7
- Heidenreich Marine Reorganizes Companies page: 8
- Transas Breaks Through Visual Technology page: 8
- Navibulgar Finalizes Varna Shipyard Deal page: 9
- Horbeck-Leevac To Build Eight OSV's page: 9
- Navibulgar Initiates Fleet Renewal Program page: 9
- OSHA Standards Applicable on Uninspected Vessels page: 10
- Munson Delivers PACKCAT to U.S. Navy page: 11
- U.S. Navy Awards Northrop Grumman $ 1 . 3 B LHD Contract page: 11
- Shipboard Life in Style page: 12
- Has the Fast Cat Come to A Halt? page: 15
- Market Changes Mold RoRo Ship Conversions page: 16
- Seville Delivers RoPax Ferry page: 18
- Crankshaft Care Key to Vessel Profitability page: 19
- AIS:When & Where? Here & Now! page: 20
- Crowley Subsidiary Christens ATB page: 24
- Ballast Water Treatment Through Biodispersion page: 26
- LNG Breakthrough For Wartsila page: 29
- New Measures on Ballast Water Management Approval page: 32
- The GMD Group - A Young, Ambitious Team page: 33
- Seven Seas Mariner Undergoes Pod Adjustment page: 34
- Teekay Foam's Discharge Pipe Repaired in Bilbao page: 36
- Government Ships Spend Time At Cascade page: 38
- ASRY Continues Brisk Repair Pace page: 39
- FRP Pumps Offer Lasting Results page: 40
- Spray-On Insulation Cuts Maintenance Costs page: 42
- SEI Temp-Set Reusable Insulation Covers page: 42
- EU to Develop Sulfur Strategy page: 43
- CITGO Offers "No Sheen" Aquamarine Oils page: 43
- Good Fuel = Good Profits page: 44
- Lubes Keep Step With Diesel Development page: 44
- Jeamar's Winches Are Made To Order page: 45
- Victoria Shipyard Racks Up Cruise Ship Jobs page: 45
- Targeting Greek Shipping's $16B Budget page: 46
- Elefsis Helps Speed LNG Retrofit page: 47
- Stelmar Set To Expand Fleet, Receives Tanker page: 51
- HHI: To Infinity & Beyond page: 52
- Dual-Fuel Finds A New Backer page: 57
- U.S. Navy Selects Gold Team For DD(X) page: 57
- Packing Solutions Help Bear Set Sail page: 57