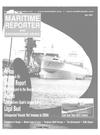
FRP Pumps Offer Lasting Results
There's hardly a marine application — onboard or ashore — where seawater pumps are not considered critical to a vessel's operation or purpose. The ability to pump seawater aboard most vessels represents only a part of their liquid pumping requirements; in many cases other liquids such as caustics, corrosives, and alkalis need to be transferred, either from ship to shore or vice versa.
Corrosion, Erosion, and Pitting For these kinds of harsh applications many shipboard pumps are constructed of metals designed to withstand the continuous flow of severely corrosive liquids. Typically, these metals include Monel and K-Monel, titanium, nickel bronze, alloy 20 steel, and 316 stainless steel. Even though these metals are extremely hard, they are still subject to corrosion, erosion, and pitting as a result of the harsh liquids in contact with them and the abrasive content of seawater.
The rate of corrosion (crevice and galvanic) is a function of the liquid in contact with the metal as well as the specific metal used for pump construction. For example, alloy 20 steel in continuous contact with seawater might corrode at a rate of .002-.006-in. per year: for 316 stainless the corrosion rate is about .002-in. per year. While these are seemingly insignificant rates of corrosion, as internal clearances in the pump widen, performance and efficiency are compromised, and premature pump failure or performance degradation is likely to occur. When 316 stainless is in contact with salt water, its surface also ultimately corrodes; the corroded surface takes on a "protective" layer known as "passivation." This passivation layer is formed as a result of a 12 percent (or greater) chromium content in the steel, which combines with oxygen in the atmosphere to form a thin layer of chrome-containing oxide.
The passivated film protects the underlying metal from further corrosion: however, the film also requires oxygen to self-repair. In seawater, chlorides from the salt attack and destroy the passive film quicker than it can be repaired in a low oxygen environment. But this only explains part of the problem with using metallic pumps in seawater applications.
Erosion, on the other hand, is a different issue, and it does have a negative affect on the passivation layer. Also, as corrosive or abrasive liquids contact metal parts in the pump, another wear factor is introduced: fluid velocity across the surface. With high fluid velocity the protective passivation layer will erode quickly, exposing new metal to start a new cycle. For this reason, corrosion is essentially continuous, since new metal is being constantly exposed to the corrosive liquid.
FRP Pumps — An Alternative An alternative is. Fiberglass Reinforced Plastic (FRP) pumps. FRP pumps have proved to be extremely durable in difficult marine environments.
They are widely employed in many on-shore and shipboard applications for seawater circulation and bilge pumping, in seawater cooled air conditioning systems, reverse osmosis systems, for liquid chemical transfers, and on land in aquariums and industrial facilities for pumping seawater and other difficult liquids.
Large, ABS certified vertical FRP pumps are used on chemical barges today. These pumps extend from the deck to the bottom of the tanks, and incorporate long columns and shafts with associated discharge piping. In addition to reliability and long-life, FRP pumps help reduce overall weight substantially.
This is particularly noticeable when comparing FRP pumps with exotic metal vertical pumps. The lighter weight of FRP pumps also offers an obvious advantage for oil-carrying tankers and barges, which incorporate double hull construction.
FRP pumps are built for the difficult liquids encountered in the marine environment such as brine, acids, caustics, bleaches, solvents and abrasives.
Hydrochloric acid — a particularly difficult liquid — is also transferred with shipboard FRP pumps. They have proved well suited for this application, and their light weight has made a substantial difference in available payload capacity when many large pumps are required. In fact, light weight imparts two key benefits: first, when large pumps must be removed for service they generally require expensive, time consuming labor and heavy riggings equipment; second, aboard any vessel weight is always at a premium — the more equipment weight, the less payload capacity. Instead, FRP pumps can generally be repaired in place, with basic fiberglass technology thus reducing maintenance costs while minimizing downtime. Spare parts cost — particularly impellers made of metals — must also be considered, since their costs alone, in many cases, exceed the total cost of a complete, comparable FRP pump. Mainly, however, the use of FRP pumps can provide an extended service life, sometimes by an order of magnitude over the metal pumps they are designed to replace.
A number of different composite materials are used to manufacture FRP pumps. These include vinyl ester resin, and different grades of epoxy resin.
Generally vinyl ester resin pumps are used for most acids, caustics, bleaches, salt water, or other inorganic chemicals.
Epoxy resins (which can also handle some acids) are more commonly used for solvent based chemicals such as toluene, benzene, high concentration sulfuric acids, and similar chemicals.
FRP pumps are produced in horizontal and vertical configurations, and in a wide variety of sizes and capacities to accommodate most marine applications.
Circle 5 8 on Reader Service Card www.maritimereporterinfo.com The preceding was authored by Ted Beck, Mechanical Engineer, Fybroc Division/Met-Pro Corp.
Other stories from May 2002 issue
Content
- Delta Queen Makes A Comeback page: 3
- USS Cole Returns to Fleet page: 4
- Polar Discovery Christened at Avondale page: 7
- Heidenreich Marine Reorganizes Companies page: 8
- Transas Breaks Through Visual Technology page: 8
- Navibulgar Finalizes Varna Shipyard Deal page: 9
- Horbeck-Leevac To Build Eight OSV's page: 9
- Navibulgar Initiates Fleet Renewal Program page: 9
- OSHA Standards Applicable on Uninspected Vessels page: 10
- Munson Delivers PACKCAT to U.S. Navy page: 11
- U.S. Navy Awards Northrop Grumman $ 1 . 3 B LHD Contract page: 11
- Shipboard Life in Style page: 12
- Has the Fast Cat Come to A Halt? page: 15
- Market Changes Mold RoRo Ship Conversions page: 16
- Seville Delivers RoPax Ferry page: 18
- Crankshaft Care Key to Vessel Profitability page: 19
- AIS:When & Where? Here & Now! page: 20
- Crowley Subsidiary Christens ATB page: 24
- Ballast Water Treatment Through Biodispersion page: 26
- LNG Breakthrough For Wartsila page: 29
- New Measures on Ballast Water Management Approval page: 32
- The GMD Group - A Young, Ambitious Team page: 33
- Seven Seas Mariner Undergoes Pod Adjustment page: 34
- Teekay Foam's Discharge Pipe Repaired in Bilbao page: 36
- Government Ships Spend Time At Cascade page: 38
- ASRY Continues Brisk Repair Pace page: 39
- FRP Pumps Offer Lasting Results page: 40
- Spray-On Insulation Cuts Maintenance Costs page: 42
- SEI Temp-Set Reusable Insulation Covers page: 42
- EU to Develop Sulfur Strategy page: 43
- CITGO Offers "No Sheen" Aquamarine Oils page: 43
- Good Fuel = Good Profits page: 44
- Lubes Keep Step With Diesel Development page: 44
- Jeamar's Winches Are Made To Order page: 45
- Victoria Shipyard Racks Up Cruise Ship Jobs page: 45
- Targeting Greek Shipping's $16B Budget page: 46
- Elefsis Helps Speed LNG Retrofit page: 47
- Stelmar Set To Expand Fleet, Receives Tanker page: 51
- HHI: To Infinity & Beyond page: 52
- Dual-Fuel Finds A New Backer page: 57
- U.S. Navy Selects Gold Team For DD(X) page: 57
- Packing Solutions Help Bear Set Sail page: 57