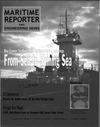
The Holland Project: Leveraging History to Build Tomorrow's Ships
In 1932, after rusting in a public park for more than two decades, the USS Holland was cut up for scrap, a sad and ignoble end for the vessel hailed as the first modern submarine. Beyond sentiment, however, the Holland's unseemly demise was a historical tragedy. With the ship destroyed and most of the plans used to build it scattered and lost, researchers long believed that the opportunity to study the innovative genius of the submarine and its inventor, John P, Holland, had disappeared forever.
In fact, only three as-built drawings from the original set of 90 Holland plans survived. This was a true tragedy, as The Holland was the first vessel to incorporate all the features of a modern submarine, including: a streamlined hull shape; a fixed center of gravity to ensure longitudinal stability; the first dual propulsion system combining an internal combustion engine for surface propulsion with an electric motor for submerged propulsion; and separate tanks for main ballast, variable loads and trim.
Nearly seven decades later, however, engineer Gary McCue, with support from Electric Boat and the Product Lifecycle Management team at IBM and Dassault Systemes, used computerized design tools to bring the Holland back to life in stunning 3-D models and animations.
Electric Boat is applying these models to evaluate next generation information technology and to improve its design and engineering practices.
The Holland Project, as it has come to be known, illustrates the power of digital archaeology and of using the tools of the future to reconstruct the past. It also offers a rare glimpse into the strategies used by today's leading shipbuilders to create the naval, cruise and cargo ships of tomorrow. As such, the Holland Project functions as a mirror of history, reflecting images from the past and projecting them into the future.
Design-in-Context To re-create the Holland, a concept known as "design-in-context" was employed. Using CATIA software, standard parts were modeled using a local part axis and inserted into an assembly model, where they were placed "on location" by specifying their relationship with surrounding parts.
"Place the pump in contact with this mount and line up its mounting holes with the holes in the bulkhead." The value of this technique was apparent in modeling the Holland, including its 1896 "Otto" gasoline engine and a strange new weapon it deployed called The Dynamite Gun.
The "Otto" design ties 160 parts together, not by the absolute placements of parts in space but by their relative positions established by constraints — constraints such as contact, parallel, and concentric define how two parts relate to each other. Because all engine parts are constrained in this way, parts that are fully constrained do not move, but those that are not fully constrained move in accordance with kinematic laws. The result is an operating engine.
John Holland was awarded an 1898 U.S. Patent <708552) for improvements to the Dynamite Gun — and the patent claim included key drawings and specifications, which turned out to be critical for the Project. Detailed drawings included in the patent application helped fill in what the archive drawings left out, are supplemented by detailed text descriptions of how the device worked.
The relationship between intellectual property and design was important to Holland, just as it is to modern designers and inventors. Digital designs are a valuable asset in documenting intellectual property claims. Every product design has intellectual property embedded within it, and CATIA multi-model links are effective in keeping resources associated with the models.
System Behaviors: Incorporating Time and Motion Now that it has been shown how CATIA was used to reconstruct the engine and the Dynamite Gun — and how today's designers can use these same principles to advantage in their work — it is time to explore how product lifecycle management helped the team understand the boat's actual operation and its onboard systems. By applying the principles of kinematics, the team was able to model the behavior of key systems, including the ship's dual propulsion system.
The idea to use different propulsion systems for surfaced and submerged operations dates back to Robert Fulton, who combined a hand-cranked propeller with a sail that folded for submerged operations.
But John Holland was the first to combine an electric motor for submerged propulsion with an internal combustion engine for surface propulsion.
The ship had three modes of plant operation: propulsion by electric motor, propulsion by gasoline engine, and recharging of the batteries using the direct current motor as a generator driven by the gasoline engine. Digital reconstructions of the operation were based on the U.S. Navy's 1903 "Notice on Care and Handling" manual for the Type 7 Holland Submarine Torpedo Vessel.
The complexity and precision of the sequences becomes apparent in these simulations, which also indicates how the crew must have interacted as the sequences were performed.
One of the benefits of combining a digital mockup, kinematic definitions for all propulsion assemblies and a timebased simulation tool is that the design and operation of the propulsion plant can be analyzed for completeness.
Analysis also identified where the crew spent most of its time, how they worked together and where potential missteps were likely.
Construction Sequencing Shipbuilders must design for production, and researchers were eager to learn about the build sequence, tooling and fixtures that might have been used on the Holland.
This was accomplished using a complete digital mockup (DMU), which gave the team the ability to experiment with "what if' production scenarios.
Unlike today's ships, which are built in large blocks or sections, the Holland was built much like a tract house, with stick-and-frame construction. Photos show us that the main frames were erected over a bottom strake plate and shored up along the side.
Minor wooden spandrels positioned the frames. These were probably attached to the frames with bolts through the rivet holes. Large equipment was positioned inside before the frames blocked access to the interior. Piping, electrical and smaller equipment were added in layers as the frames and hull plates were brought up. In this way, Holland could construct the vehicle while minimizing movements of the main lifting mast and guy wires. The Digital Process for Manufacturing tool was used to simulate the construction process.
Today's shipbuilders are focused on the same efficiencies. Cranes today lift huge block sections of a ship as one.
Maximizing the lift capacity, minimizing crane movements and having all materials ready to go is critical to build time.
Integration and Collaboration The ability to create 3-D designs for the Holland — and to test those designs through simulation and virtual operation — illustrates the value of an integrated product lifecycle management solution for today's shipbuilders. Such a solution pulls together information from product description, process and simulation, and for review and commentary — outside the context of CAD/CAM.
It was only in this way that many of the remaining mysteries about the Holland were solved — in much the same way that these same technologies help modern ship designers resolve questions and eliminate conflicts before the first steel is cut.
In many cases, the ability to "watch" systems in operation represents the only way to recognize and address unresolved issues without incurring massive expenses during the construction phase.
This was true in John Holland's day, and it is even truer today. No wonder John P.
Holland is considered the "Father of the Modern Submarine."
Other stories from November 2002 issue
Content
- Bollinger Restructures Management Team page: 8
- I neat Confirms U.S. Military Contract page: 10
- Promoting A Modal Shift page: 12
- FPSO Farwah Launched at Fene Yard page: 16
- The Irony Of Maritime Security page: 18
- Secure Marine Debuts "Fence" at Sea page: 24
- All Set Tracking Launches New Electronic Seal page: 25
- Additional Funding Urged for Port Security page: 26
- Austal to Build Circle Line's First High Speed Vessel page: 27
- Stena Christens Tanker For Coastal Waters page: 29
- New Fast Craft For Kristiansand City F.D. page: 30
- Gladding-Hearn Delivers Fast Ferry for Lake Erie page: 31
- MTU Engine Series Logs Success on Inland Waterways page: 33
- KMSS Training/Simulation Division Is Buoyant page: 34
- Crowley takes lead with "Reliance" page: 36
- Markey Provides the Strong Pull page: 37
- Lerchbacker Puts Austal USA on the Fast Track page: 38
- Field of Dreams page: 41
- Columbian Rope Continues to Hold Strong... After 175 Years page: 42
- Hydralift Skeg Use Gaining Speed page: 44
- Workboat Annual page: 46
- A New Generation of Fireboats page: 48
- Alstom Selected By Otto Candies page: 50
- TechnoFibre Leads In Lifeboat Maintenance page: 50
- Maritime E-Business Growth Continues page: 52
- Wallem, Drew Team to Offer "Total" Solution page: 59
- Marine Software: Aiming to Lower Costs page: 60
- Full Steam Ahead page: 62
- Marine Data Systems Offers AIS Solutions page: 65
- The Holland Project: Leveraging History to Build Tomorrow's Ships page: 66
- John P. Holland: Father of the Modern Submarine page: 70
- MAN B&W Revises 32/40 Engine page: 71
- RIB Report page: 73
- Willard Ready for Defense, Commercial Contracts page: 75
- Griffon Hovercraft Scores Big Contracts Around the World page: 76
- Wartsila s Italian Plant Rolls Out Two Stroke page: 80
- MAN B&W Touts Proven Tech in New 48/60B Engine page: 84
- Manitowoc = 100 Years of Distinction page: 86
- TankRadar System Breaks New Ground page: 87
- North American Marine Jet Expands Its Market page: 87
- HJ403: Hamilton Unveils New Water jet page: 88