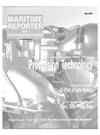
The New MTU 2000 CR Marine Engines
The continuing advancement of the diesel engine propulsion package for the maritime environment follow a common track, ie. higher power with lower weight; increasingly sophisticated and reliable electronic controls; more efficient handling of emission reductions; and ease of maintenance.
While achievement of these objectives vary by manufacturer, as any vessel owner can attest. MTU continues to deliver technological leaps and bounds that are similarly practical.
The new MTU 2000 CR (common rail) marine engines are designed to be smaller, lighter, cleaner, more powerful and more economical than their predecessors, the 2000 series. Improvements to the key technologies of turbocharging, injection and electronics have been redeveloped and advanced.
The 2000 CR engines are designed to deliver a favorable power-to-weight ratio (1.99 kg/kW - 1.48 kg/hp).
The 2000 CR engines have only one exhaust gas outlet instead of two, therefore, only one exhaust gas duct is needed, which saves weight and space in the engine room.
Features including an increased power per cylinder and the extensive use of light alloy contribute to the good power-to-weight ratio. The weight optimization of components and the modular design of the engine are also important factors. In several places in the 2000 CR engines, more than one function is integrated into the same component, helping to save weight and space.
An example: the engine Vee. which together with the outer wall of the charge air cooler situated above it forms the ducting for the charge air How, which goes from the turbochargers to the charge air cooler. Such a design was possible because a common rail injection system is used, and the space in the engine Vee (90 degrees) is therefore not occupied by injection pumps.
As a result of the cleared engine Vee, the crankcase was also redesigned. For example, the water feed and return channels arranged in the V angle were designed as box-shaped components that reinforce the cylinder walls and support the banks against each other. This, according to the manufacturer, is designed to stabilize the cylinder banks and reduce cylinder liner deformation, and therefore piston ring and cylinder liner wear.
MTU has been using the common rail injection system since 1996, and as a result of an overall positive experience, the engine maker has again used a com- mon rail system in the 2000 CR, but with a twist. It is an advanced version, in which an accumulator is mounted on top of the injectors.
The actual storage function is therefore no longer performed, as previously, by the common rail, but by individual storage facilities in the cylinder heads.
This is designed to prevent pressure fluctuations in the fuel line, helping to stop surging at the injectors and the supply of too little or too much fuel. The pressure (max. 1800 bar) remains virtually constant in the entire system. In addition, the fuel lines have a smaller and, in the standard version, single-wall design. The fuel line is situated inside the charge air pipe, and is thus surrounded by a second layer.
The common rail system of the 2000 CR series is fitted with various safety devices. A pressure relief valve in the distributor reduces the maximum system pressure when required, thus protecting the other high-pressure components against overload.
The injectors are actuated by 2/2-way valves, which are activated by the engine electronics. The control voltage here is up to 42 volts. The control valve was positioned very close to the nozzle needle so that there are only slight delays between the opening of the valves and the nozzle needle. This design therefore has the potential for multiple injection without any design changes having to be made to the control unit.
New MTU-Design Turbocharger The 2000 CR engines are fitted with a powerful turbocharger system, in which two (in the 8V and 10V versions) and three turbochargers (in the 12V and 16V versions) are used. Only one turbocharger runs at low engine speeds; the second and third turbocharger are only engaged electronically at higher engine speeds.
This sequential turbocharging ensures a powerful charge air flow and therefore an immediate and strong engine acceleration response across the entire performance map. The efficiency of the turbocharging system is enhanced by the integration of the charge air cooler into the engine Vee, as this shortens the path of the charge air flow.
The ZR 125 turbochargers were developed in-house by MTU, and are also manufactured internally by the company.
At a maximum turbocharger speed of 85,000 rpm, they build up a maximum charge air pressure of four bars. The compressor wheel is made of aluminum, and are housed in a water-cooled carrier housing, which keeps the surface temperatures below 220 degrees Celsius stipulated by the SOLAS regulation (Safety of Life at Sea).
New ADEC Electronics Another new item on the 2000 CR series is the new generation of MTU's Advanced Diesel Engine Control (ADEC) electronic engine management system, designed to be far more robust than previous versions.
During the development of the new ADEC, an easily programmable system interface and a flexibly usable functionality were integrated into the system interface. The engine controller now contains far fewer customer- and system interface-specific settings than previous versions. The variants for the different applications are supplied via the system interface. The use of a commercially available compact flash card in the system interface means that the system interface is easy to program.
An Ethernet interface enables remote diagnosis of the engine management system via the Internet.
Circle 5 on Reader Service Card
Read The New MTU 2000 CR Marine Engines in Pdf, Flash or Html5 edition of May 2004 Maritime Reporter
Other stories from May 2004 issue
Content
- Fincantieri Delivers Westerdam page: 10
- "World's Largest" Heavy Lift Ship Enters Service page: 10
- Damen Delivers Pair of Tugs page: 10
- Not Just Another Dam Ship page: 12
- Welsh Towing Company Growth Continues page: 14
- Gladding-Hearn Starts Construction of New I neat Vessel page: 15
- Despite 11% Increase, Hempel Disappoints page: 15
- Grimaldi-Naples Receives GM Award page: 16
- Schlueter Promoted to VP page: 17
- Misplacing the Place of Refuge page: 20
- Schottel Broadens Electric Propulsion Options page: 26
- CIMAC Congress Set for Kyoto page: 29
- Waterjets for a Difficult Design Task page: 30
- New Shaft Seal from Ocean Venture Seals page: 31
- Gas Turbines: Keeping Fresh With Innovation page: 32
- MAN B&W Diesel Debuts the New S65ME-C page: 33
- Thordon COMPAC Finds Success in FSV page: 33
- Wartsila to Power Australian FPSO page: 34
- VSP: Same Power, 9% More Bollard Pull page: 35
- The New MTU 2000 CR Marine Engines page: 36
- Converting and Repowering One Very Big Ship page: 38
- Power for a New Breed of RoPax page: 40
- ZF Helps to Harness Spirit of Ontario's Power page: 41
- Greece Poised for Posidonia 2004 page: 42
- Leif Hoegh Records Strong First Quarter page: 43
- BV Launches LNG CAP page: 43
- Steel, Ship Prices Soar as Tankers Stay Firm page: 44
- Ice Class & Large Ships Pose New Challenges page: 44
- Royal Caribbean Stays Current with C-MAP CM-93/3 ECs page: 46
- JRC Proposes Integrated Nautical Safety System page: 46
- C-Map's RTU and the Ending of the Paper Trail page: 47
- AutoChief C20 Reports Good Market Penetration page: 48
- Vision FT IBS page: 48
- Research Winches for R/V Maria S. Merian page: 52
- Konecranes Giving Port Efficiency a Lift page: 52
- Chinese Yard Logs Strong Month page: 55
- Fuel Oil Separation Takes Center Stage page: 56
- Security of Ports and Vessels: A New Approach page: 60