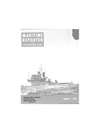
M a r A d Study A v a i l a b le O n D e v e l o p m e n t Of A S t a n d a r d C a r g o Ship
The development of a standardized general cargo ship to help meet the future requirements of the U.S. merchant marine would yield substantial benefits to ship operators, shipbuilders and the Government, according to a study released recently by the Maritime Administration.
Series production of such a ship could significantly lower construction costs and cut production time, helping make the American merchant marine more competitive in the world shipping market. This, in turn, could reduce the level of subsidies paid by the Government to help offset the advantages enjoyed by low-cost foreign competitors.
The study, "Next Generation Cargo Liner: Phase I," was prepared under c o n t r a c t by J.J.
Henry Co., Inc., and Temple, Barker and Sloane, Inc. The cost of the c o o p e r a t i v e effort was shared by the Maritime Administration and seven U.S.-flag operators — Farrell Lines, American Export Lines (now a division of Farrell), Lykes Bros. Steamship Company, M a t s o n N a v i g a t i on Company, Moore M c C o r m a ck Lines, Puerto Rico Maritime Shipping Authority, and United States Lines.
The first step of the study involved forecasting general cargo movements and service requirements on selected worldwide trade routes served by the participating operators. The forecasts, which extended through the year 2000, produced profiles on each carrier's cargo mix (percentages of breakbulk, containerized, and rollon /roll-off cargoes), and service requirements (itinerary, service frequency, and port and canal constraints).
Based on these individual profiles, a conceptual ship design was developed for each operator.
These designs were tailored to each company's specific cargo and service requirements.
The final step was the development of a composite design based on the m o s t i m p o r t a nt characteristics of the seven individual designs. The resulting composite ship, with available options, has the following specifications: length between perpen perpendiculars, 620 feet to 800 feet; beam, 105 feet 6 inches; depth, 69 feet 6 inches; draft 29 feet 6 inches to 32 feet 6 inches; deadweight tonnage, 19,500 to 29,600; service speed, 18 to 23 knots; and shaft horsepower, 14,500 to 42,500.
While the study assumed the use of a steam powerplant, it was recognized that diesel propulsion offers fuel-saving advantages, and would meet the lower speed and horsepower requirements of some shipowners. The report suggested that powerplant trade-off studies be conducted at a later date.
The composite design also can be modified to facilitate different cargo mixes, depending on the container, r o l l - o n / r o l l - o f f or breakbulk requirements of the shipowner.
The report recommends continued development of a standardized vessel and concentrated research on optimizing such a ship. This would involve such eff o r t s as model testing and applying technological advancements to the production of the ship and its cargo-handling systems.
The report is available from the National Technical Information Service, 5285 Port Royal Road, Springfield, Va. 22161. The prices and order numbers are: Executive Summary (PB-297588/ AS) @ $4, Final Report (PB- 297590/AS) @ $9.50, and Final Report/Appendices (PB-297589 / AS) @ $8.
Other stories from January 1980 issue
Content
- Title XI Requested For 2 Lakes Carriers Costing $ 6 0 M i l l i on page: 4
- AWO Reports $2.9 Billion In New Waterways Plants In First Half Of 1979 page: 4
- T i d e w a t e r M a r i n e Tows M o b i l e Supply Vessel Eleven Thousand Miles page: 6
- M o o r e McCormack Names Three To Key Positions page: 6
- Desco Marine Launches Its 100th Cummins-Powered Boat page: 9
- Bay S h i p b u i l d i n g Lays Keel For Turecamo Barge page: 11
- Blount To Build 75-Foot 1 8 9 0 ' s Style Steam Launch page: 11
- Kent And Boling Elected To The NOIA Board page: 11
- D a v i e Launches Second Jackup Drilling Rig For Global M a r i n e Drilling Company page: 12
- Marinette Marine Christens Second And Third Of Seven N e w Tugs For U.S. Navy page: 12
- 1980 Annual Meeting, Water Resources Congress page: 12
- Papers Call For First P a n - A m e r i c a n Conference Of Ocean Engineering page: 14
- M a r A d A w a r d s Contract For Sailing Ship Study page: 14
- McDermott Building Two Bulkfleet Marine Tugs Custom-Made For Future page: 14
- Reduced Towing Costs Subject Of Study On Towing Surge Pendants page: 16
- Todd W i l l Deliver 2 4 0 0 ' Barges To M o n t a uk Oil T r a n s p o r t a t i o n Corp. page: 17
- Raytheon Service Co. Brochure Describes A u t o - A l a rm RCVR/KYR page: 17
- N a t i o n a l M a r i n e Shipyard Division To O p e n N ew Gulf Coast Facilities page: 18
- LNG V i r g o N a m ed At General Dynamics page: 18
- Port Weller Dry Docks Delivers Bulk Carrier With Fuel Efficient Hull page: 18
- 123-Foot Northern Leader From MARCO Equipped As Catcher, Freezer, Packer page: 20
- FMC Releases Study On Virgin Islands Trade page: 20
- H i l l m a n D e l i v e r i n g 14 N e w Chemical Barges To PPG page: 21
- NASSCO Awarded 5-Ship $239-Million Contract By American Tankships page: 22
- M a r A d Study A v a i l a b le O n D e v e l o p m e n t Of A S t a n d a r d C a r g o Ship page: 23
- Chevron Orders Two 3 5 , 0 0 0 - D W T Product Tankers From Mitsubishi page: 24
- M a n g o n e Delivers Research Vessel, W e s t e r n Strait, To Western Geophysical page: 24
- A.L. Kucera Elected President Of A WO page: 24
- Crude Oil Supply And Tanker Demand Report Available From Drewry page: 24
- Fourth British C o l u m b ia T o w b o a t Conference Set For M a r c h 2 1 - 2 2 , 1980 page: 25
- B e t h l e h em Reorganizes S h i p b u i l d i n g D e p a r t m e nt page: 25
- Lips-Doran To Establish Chesapeake, Va., Plant page: 25
- P e r t a m i n a 1020 Delivered By Hitachi Zosen page: 26
- USS H a r r y W . Hill Commissioned At Ingalls S h i p b u i l d i ng page: 27
- Dinko's Marine Service Orders Supply Vessel From Mississippi Marine page: 27
- New Major Shipyard To Be Formed In Hong Kong page: 27
- Shell Orders 11,500-DWT Tanker From Valmet page: 28
- S.G. Dever N a m ed V P Of Colmac Coil M f g. page: 29
- Exxon ULCCs Receive S t a n w i c k M a i n t e n a n ce A n d Inventory Services page: 29
- Shell Offers Literature On New Diesel Oils page: 32
- Halter Marine, Inc. Sets Production Record - 2 2 8 Deliveries In 1979 page: 33
- FMC Signs N e w Barge Contract W i t h Puget Sound Freight Lines page: 34
- t h Ocean Energy Conference Set For June In W a s h i n g t o n , D.C. page: 34
- SNAME Philadelphia Hears Paper On Hopper Dredge Design page: 34
- McAllister Acquires Baker-Whiteley— Now Offers Baltimore-Based Marine Services page: 34
- Gibbs & Cox Names Stark Assistant VP page: 35
- Kings Point Names G.A. Uberti Of NASSCO M a r i n e M a n Of Year page: 35
- De Laval Offers Literature On Centrifuges For Shipboard Use page: 35
- Four Agents N a m e d By N a t i o n a l M a r i n e Service page: 36
- Electro-Nav To M a r k et SATURN Satcom In U.S. page: 36
- North Sea Corrosion Conference Papers Now Available In Book Form page: 36
- Shipping Orders Worth £ 4 2 M i l l i o n For U.K. Y a rd page: 37
- GE's Ground Systems D e p a r t m e n t Renamed page: 37
- Davie Signs $C35-Million Petrobras Rig Contract page: 37
- S t a n w i c k A n d Vickers Form Joint Company page: 38
- M a r t i n o N a m e d Assistant G e n e r a l M a n a g e r At Todd Galveston Yard page: 38
- FMC Marine And Rail Launches Fourth Ro/Ro Barge For Crowley page: 38
- John S. Hollett Joins Crowley Maritime page: 38
- Olson N a m e d President Of W i l l a m e t t e Tug & Barge page: 39
- N e w M A R C O Brochure Describes Hydraulic Pump Drive Units page: 39
- E.C. Flint Promoted At Zidell's Marine Construction Division page: 39
- Construction To Begin On New $20-Million N.Y. Container Terminal page: 39
- G l a d d i n g - H e a r n Delivers Pilot Boat Huron Belle page: 40
- ABS Approves Use Of Protective Ceramic M e t al —Literature A v a i l a b le page: 40
- 3 New Reports Now Available From Ship Structure Committee page: 40
- International Oil Spill Conference To Be Held In Atlanta March 2-5, 1981 page: 40
- Norwegian Firm Offers Porthole/Escape Hatch —Meets Safety Rules page: 41
- Mississippi Marine Towboat Delivers Two New Vessels To Palmer Barge Line page: 41
- Pickands Mather Awards $10-Million Conversion Order To Fraser Shipyard page: 42
- S N A M E N e w England Hears Paper, ' L i a b i l i t y A v o i d a n c e In Ship Design A n d Construction' page: 44
- N e w OMNITHRUSTER For Small Commercial Boats —Literature A v a i l a b le page: 44
- Burton Launches Third Of Seven Tuna Seiners page: 46
- MorMac Appoints Marcelewski Philadelphia Office Manager —Edward J. Desher Retires page: 46
- Farrell Realigns Executive Personnel page: 46
- W e s t e r n Oceanic Inc. To Build 300-Ft. W a t er Depth Jackup page: 47
- Newport News Delivers The U.S.T. Pacific In Record Time page: 47
- Bourgeois And Mitchell Elected Vice Presidents At State Boat Corp. page: 47
- SNAME L.A. Section Hears Paper On Air Cushion Drilling Systems page: 48
- N o r w e g i a n Firm To Buy Jetfoils For Offshore Use From Boeing M a r i ne page: 48
- H i g h Pressure Filter Selection G u i d e From P a u l - M u n r o e Hydraulics page: 49
- Propp N a m e d M a n a g e r Of Z i d e l l ' s Swan Island M a r i n e Repair Division page: 49