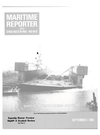
OUTSTANDING RIG DESIGNS
A review of new designs to meet the challenges of deep water and harsh environments Offshore drillers, in 1984, ordered a total of 37 units to be built, includ- ing 24 semisubmersibles. Some of these orders were letters of intent subsequently never material- ized into firm construction con- tracts. However, 22 of the 24 semi- submersible orders were firm. A closer examination of the types of semisubmersibles and when they are scheduled for delivery will help explain why so many of these units were ordered during a rig oversup- ply situation.
Every semisubmersible ordered in 1984 and so far in 1985 is rated for over 1,000 ft. of water except one unit being built by and for the U.S.S.R. which is rated for 650 ft. of water. Three other Russian semi- submersibles are rated for 1,500 ft.
of water. This fact should not be surprising since the offshore indus- try is constantly moving toward ex- ploring deeper and deeper waters, Most of the units presently on order are harsh environment designs, suitand able for use in Arctic conditions and in the North Sea and in northern North Sea waters, where the UK and Norway are beginning to open acreage for leasing. Norway also now allows year around drilling north of the 62nd Parallel, where harsh environment rigs will be needed.
Arctic class semisubmersibles should not be confused with the Arctic class submersibles, of which there also are several new designs, some of which are rated to work in up to 200 ft. of water. The submersi- bles are bottom-supported struc- tures. Drilling semisubmersibles also should not be confused with semisubmersible production units such as the tension leg platform design, which are permanently fixed to the seafloor. However, some drilling semisubmersibles have been converted to floating production units.
A majority of the semisubmersibles are scheduled for delivery between mid-1986 and throughout 1987, with some deliveries stretching to 1989. The latter deliveries, however, are actually options on new rigs. It is apparent these contractors think these rigs will be in demand enough to make a profitable day rate upon delivery. A major factor in several rig orders, especially those being built in South Korean shipyards, are the lucrative construction costs. Sonat placed a seemingly blockbuster order late in 1984 for six Gotaverken Arendal GVA 4500 design semisubmersibles at Daewoo for an average cost of about $71 million each. The contract actually is a firm order for two units with options for four additional rigs. This order was closely followed by a four-rig order from Odeco at Hyundai with an average cost of $65 million each. Odeco's units are of the Ocean Odyssey class.
Most of the semisubmersibles on order are proven designs or enhanced, larger versions of proven designs such as the Aker H-4.2, Friede & Goldman Pacesetter or the Gotaverken GVA 4000. Among the new designs ordered were the Yatzy Class by Dyvi, Friede & Goldman's Trendsetter™ and one designed by Maritime Engineering. The most "radical" of the new semisubmersibles is the Trendsetter™, which moves away from the traditional six or four column unit into a five-column design. Reading & Bates Drilling Company ordered the first Trendsetter™ last February at IHI in Japan, naming it the ZANE BARNES. The Trendsetter™ basically is a four-column unit with a n center drilling caisson which also i serves to store marine riser and - drillpipe. Variable deck load capacn ity is 5,000 tons in the transit, opern ational and survival modes. The rig will be capable of drilling in up to - 5,000 ft. of water with conventional - mooring and thruster assist in mild t climates such as the Gulf of Mexico.
- With dynamic positioning capabilii, ty, which can be added at a later i date, the unit will be able to work in - 5,000 ft. of water in harsh environn ments.
Several new semisubmersible der signs are on the drawing boards - from various firms. Most are for a deepwater and harsh environments.
- One, however, from Marathon Lea Tourneau, best known for its jackn ups, was designed specifically for il mild climates. The GranGulf design s is a four-column unit with two horif zontal cross bracings between the - pontoons. The GranGulf is rated for 0 up to 2,000 ft. of water convention- - ally moored and up to 3,000 ft. of - water using dynamic positioning.
- This design incorporates pontoons t which are flared at each end, a cons cept from SeaTek Corp. of California.
The contoured pontoon ina creases buoyancy and stability.
- Other semisubmersible designers a utilizing the contoured pontoon !, configuration include Gotaverken e Arendal, Rauma Repola, Dyvi and e Friede & Goldman (on the Trendy setter™ design).
s Of the various deepwater, harsh y environment designs, most are eitht er partially or fully winterized by - enclosing and heating work and/or ti storage areas. Finnish shipbuilder x Rauma Repola introduced a new - design earlier this year, dubbed the - RR-2952, which features four colt umns, two horizontal cross bracings 1 and also is winterized with an en- ? closed work area and smooth under- - deck to minimize ice accumulation, This design also incorporates the contoured pontoon concept. Sumitomo of Japan and MSC of Holland teamed together to provide the DSS-40 semisubmersible, a fourcolumn, two horizontal bracing design which also happens to be fully winterized.
Of the new or enhanced semisubmerisble designs, Aker Engineering of Norway continues to stand by its tried and true six-column design. Its latest unit is called the D-6, a sixcolumn, harsh environment, fully winterized unit. However, like most of the new designs, the D-6 is fitted with the two horizontal cross bracings that have become so popular, eliminating the support bracings from the pontoons to the underside of the deck. The mooring equipment and chains are housed inside each of the four corner columns down to the fairleads. The rig also can be configured so that drilling can be carried out through one of the middle columns or through the center of the unit.
Marine Structure Consultants (MSC) and Neddrill teamed together to develop the DSS-10,000 semisubmersible designed to drill in up to 10,000 ft. of water with a maximum payload of 10,000 tons in harsh and Arctic conditions. The four-column unit features a completely enclosed derrick and moonpool and a central drilling column which serves also as a vertical riser storage area. The vessel can operate in up to 10,000 ft. of water with dynamic positioning equipment, and up to 1,500 ft. with an eightpoint conventional mooring system.
Blohm & Voss of West Germany has the P-099 semisubmersible design rated for drilling in up to 6,600 ft. of water with dynamic positioning equipment. Blohm & Voss claim the rig qualifies for operation in Arctic and subarctic areas with ice drift because of structural reinforcements in the waterline areas. The work area also is protected to permit operation in Arctic conditions. Total payload is 11,000 metric tons.
The unit is an eight-column design with the two inside columns on the port and starboard sides inclined toward the center of the deck, providing for greater strength and enabling the use of lighter weight steel during construction.
BOTTOM-SUPPORTED ARCTIC DRILLING STRUCTURES: With the anticipated rush of oil companies to drill in the Beaufort Sea a few years ago, several marine architects introduced new bottomsupported structures for the area.
Of the various designs introduced several years ago and the more recent designs, only three have so far been built.
The first two units were ordered in 1981 by Gulf Canada specifically for its Arctic Drilling program. The MOLIKPAQ, a mobile caisson with an octagonal shaped base, is rated for 60 ft. of water sitting on the seafloor, but also can drill in deeper waters if it is set on a berm. Gulf Canada also ordered the KULLUK in 1981, which is a conical shaped floating barge unit rated for 200 ft.
of water. The KULLUK was part of a package Gulf Canada designed for Arctic exploration, including the MOLIKPAQ, two icebreakers and two supply boats.
The third such Arctic unit was ordered by Global Marine Development.
The unit is a submersible of its own design dubbed the Concrete Island Drilling System, or CIDs.
The structure consists of three sections, a steel mud base which sits on the seafloor, a concrete mid-section which rests on the base and upper steel deck barges for drilling equipment and quarters. The rig is rated for about 50 ft. of water but the water depth can be increased by fitting an extra concrete midsection to the unit. The rig was built under contract for Exxon in the U.S. Beaufort Sea and already has drilled several wells for the oil company.
Other firms with bottom-supported Arctic designs which have not been built include Pool Arctic Alaska, which has a mono-leg jackup concept. Arctic Alaska Drilling originally was working in conjunction with Friede & Goldman on the design before it merged with the Pool Company. The upper hull of the unit measures 200 ft. square and 30 ft. deep, with the lower hull measuring 300 ft. square and 30 ft. deep.
The single 40 ft. diameter leg is raised and lowered by a rack and pinion jacking system. The leg is raised above the upper deck during transit, with the rig package slid to one side. When the lower hull is jacked down, the rig is moved over the column where it has the capacity to drill up to four wells. The unit is rated for 100 ft. of water. To keep the unit on location over soft bottoms, the lower hull has 20 spuds with a maximum 50 ft. penetration.
The rig has a total variable deckload capacity of about 17,000 tons, including about 500 days' worth of fuel which can be stored in the lower hull, enabling the rig to work for one year without resupply.
Global Marine Development also has a mono-leg jackup design similar to the above mentioned Pool Arctic Alaska unit. Global Marine's unit features a 254 ft. square base which is ballasted to the seafloor and an octagonal shaped upper hull which measures 100 ft. across flats.
The base is ballasted until it just reaches the seafloor and then is lowered further via four legs, which are used to jack the upper hull above the water. The four legs then are jacked above the upper hull during drilling operations. This design also features a rig package that is moved to one side during transit and then is placed over the center during drilling.
Sonat Offshore Drilling has a submersible concept called the Sonat Hybrid Arctic Drilling Structure (SHADS) which combines concrete and steel to create a unit similar to Global Marine's CIDS unit. The SHADS consists of a 430 ft. square steel base mated to a concrete midsection and a steel deck. The unit can work in up to 65 ft. of water sitting on the seafloor, and deeper water if set on a berm. The unit can drill up to five wells without resupply- Zapata Offshore and Brian Watt Associates developed the Brian Watt Arctic Steel Pyramid (BWASP) for operations in up to 65 ft. of water or 120 ft. of water, depending on the configuration.
The unit is a one-piece octagonal design which utilizes a steel and concrete sandwich panel for the outer shell and structural bulkheads. In the 65 ft. water depth version, the structure is built with a base width of 480 ft. across flats, with a 430 ft.
base width across flats in the 120 ft.
water depth version. The unit has a storage capacity to enable it to operate for nine months without resupply- .
Brian Watt Associates also has a design of its own called the Arctic Cone Exploration Structure (ACES) which features a 550 ft. diameter base of prestressed, lightweight concrete which is fitted with a floating steel deck. The design is rated for 50-110 ft. water depths. The unit would have the capacity to carry 270 days of supplies or the duration of three 16,000 ft. wells. Brian Watt is the prime contractor for the design, while Zapata Offshore has provided the drilling system design.
CBI Industries also designed an Arctic drilling structure designated the Portable Arctic Drilling Structure (PADS) with a 400 ft. diameter base. The unit is rated for 20-50 ft.
of water. The PADS has the capacity to operate for 270 days without resupply and can be used for exploration and development operations.
The structure, which was designed for Parker Drilling, utilizes a land rig.
Bouygues Offshore is marketing the "Zee-Star 120" for use in the Beaufort Sea. The unit would be capable of year around drilling in 40-120 ft. of water. Other versions of the structure, the "Zee-Star 60" and "Zee-Star 80" are available for shallower water depths. The "Zee-Star 120" would be able to drill three 15,000 ft. wells during a 270 day period without resupply. The structure features an internal concrete space frame, eliminating the need for internal walls or bulkheads.
When Bouygues first introduced the structure in 1984, it envisioned building the unit at Bos-Kaiser Offshore at Ensenada, Mexico, which was formed by Bouygues and Kaiser Steel. Bouygues had all its marketing and equipment suppliers in place for any forthcoming order.
Zeeland Resources, a Netherlands Antilles-based company, was formed to enter into the leasing or charter of the rig. Bouygues also formed Zeeland Parker with Parker Drilling to operate the unit, which would utilize a Parker Drilling Company Arctic land rig.
More recently, Odeco introduced its all-steel Arctic Mobile Drilling Platform (AMDP), a 16-sided coneshaped and multi-sloped hull structure with a 662 ft. base. The unit is rated for up to 200 ft. of water. The AMDP would be outfitted with two enclosed drilling rigs and a moonpool large enough to accommodate up to 48 wells. The AMDP also can be used as a production platform at the same drill site. The unit would be capable of operating up to one year without resupply, equivalent to eight 15,000 ft. wells. The helicopter deck features an enclosed hanger designed to accommodate a Boeing Chinook 234 or Sikorsky S61. The upper hull also provides covered storage for drill pipe and supplies.
Finally, several years ago, Bow Valley Industries and Canarctic Ventures Ltd., both of Canada, developed a concept of a mobile year around drilling structure utilizing surplus supertankers. The firms formed a joint venture known as Bow Arctic Resources to market the concept, which uses ice reinforced tankers with the framework modified considerably to give the unit the stability of a platform. The tanker would be cut in half, with each half placed side by side with the capacity for two drilling packages and oil storage. Water depth would be about 100 ft., which could be increased if the structure rests on a berm.
There are a few more rig designers with semisubmersibles and Arctic class submersibles on the drawing boards, but the units mentioned earlier typify the type of designs currently being touted. These designers and/or rigbuilders are counting on the offshore industry to move toward deeper waters and harsher environments, and this already is happening to a degree. Unfortunately for the rig designers (who receive a fee when their design is built), and for the rigbuilders, oil companies are not in that much of a hurry to drill in the frontier areas which will require the new semisubmersibles and Arctic submersibles as described earlier. That time will come, however, and these designs will become the next generation of mobile rigs.
For additional information and free literature on new rig designs, Circle 50 on Reader Service Card
Read OUTSTANDING RIG DESIGNS in Pdf, Flash or Html5 edition of September 1985 Maritime Reporter
Other stories from September 1985 issue
Content
- Tidewater Marine Acquires 5 Vessels From Otto Candies page: 5
- Hawker Siddeley/Kongsberg Collaborate In Venture page: 5
- American Air Filter Offers N e w Brochure On Cartridge Filters page: 5
- Big Supply Vessel 'Nicor Sailor' Converted By Eastern Marine page: 6
- Owen And Richards Named Managers At Honeywell page: 6
- MSC Announces FSS Award Totaling $30.7 Million page: 6
- Autronica's New NK-5 Unit Monitors Ship's Engine page: 6
- Grow Group Acquires Napko Coatings Division page: 6
- Bollinger Shipyard Dedicates Island Class USCG Patrol Boat Fleet page: 7
- Sulzer ZA40 Diesels Will Power Two Ferries Ordered In U.K. And Japan page: 8
- Cummins-Powered Construction Pushboat Delivered By Keith A. Record page: 8
- Tenneco Oil And Sohio Will Use Canmar Rig For Arctic Drilling page: 8
- Canadian Offshore Resources Exposition page: 8
- Shipboard Liquid-Level Sensor O f f e r e d By Tecnomatic Controls page: 9
- Maritime Association Installs New Officers And Directors page: 9
- Royal Cruise Line To Build Two Luxury Liners At Cost Of More Than $200 Million page: 10
- Goldstein Named Chairman Of COMSAT—Joseph Promoted To President page: 10
- Krupp MaK Consolidates In North America page: 11
- Innovative Triple-Screw Tugboat Launched By Halter Marine page: 11
- Truman Joins INDEECO As A d v e r t i s i n g Manager page: 12
- Moss Point Marine Delivers New Sternwheeler, Colonel page: 12
- Aluminum Boats Delivers High-Speed Crew/Utility Vessel To A&P Boats page: 12
- Matson Asks Bids On $30 Million Conversion of 'Matsonia' page: 14
- Brown & Root Awarded Feasibility Study Contract For Chevron Offshore Unit page: 15
- Congressional Maritime Caucus Establishes An Advisory Board page: 15
- SHIPLIFTING AND DRYDOCKING SYSTEMS page: 16
- OUTSTANDING RIG DESIGNS page: 16
- Bethlehem's Newest Jackup Design Can Drill In Water 600 Feet Deep page: 19
- Congressman To Address OMSA Meeting On Warehouse Vessels page: 19
- Alsthom Unit Strengthens Position In Norwegian Offshore Market page: 20
- Sandy Hook Dispatch Boat Delivered By Gladding-Hearn page: 20
- Saab Receives Order To Supply TankRadars From Tampa Shipyard page: 21
- Bertrem Products Importing Straub Couplings For U.S. And Canadian Distribution page: 21
- Conversion Of Fast Sealift Ship 'Regulus' Completed By NASSCO page: 22
- ASRY's 1984 Revenues Up Nearly 20 Percent page: 22
- Wartsila Wins Contract To Build Rig Transport Vessel For USSR page: 22
- E X P O S H I P Riomar85 page: 24
- Midland Ross Offers Free, 20-Page Brochure On Max-Gard® System page: 25
- Wilson W a l t o n Receives Two Contracts For Emergency Service page: 26
- Sale Of Imperial Survival Suits Approaches 100,000 page: 26
- Laursen Selected As New Managing Director Of Hemple Holding page: 28
- Owen And Richards Named Managers At Honeywell's Marine Systems Division page: 28
- CANADIAN SHIPBUILDING AND REPAIR YARDS page: 28
- Hollming Opens Louisiana Office For Marketing Aquamaster Product Line page: 29
- Two N e w Instruments To Measure C u r r e n t / V o l t a ge Introduced By Amprobe page: 29
- U.S. NAVY SHIP PROCUREMENT page: 30
- Holman and Wildasin Elected At Raymond International page: 31
- MIROS To Market New Products In U.S. page: 32
- Furuno Introduces New Low-Cost, High-Performance Loran Navigator page: 32
- NMEA Plans Expansion Of Interface Standard page: 32
- Kockums Completes Advanced Car/Truck Carrier For Wallenius page: 33
- Cincinnati Gear Completes Testing Of New, Sophisticated Marine Drive For Navy T-AO 187 Class Oilers page: 34
- New Alarm Reduces Boiler Failures, Diesel Failures And Repair Costs page: 34
- ADS Workshop Scheduled For October 2-3 In Chicago page: 35
- Seattle Yard GM Elected To Todd's Board Of Directors page: 35
- Caterpillar Offers 20-Page Catalog On Marine Diesels page: 35
- Wagner Wins $4.5-Million Contract For Steering And Control Systems page: 35
- Three Major Beth Steel Programs Highlight New Offerings To The Offshore Industry page: 36
- LiCausi Establishes New Boiler Consultant Firm page: 36
- West Coast Manly Shipyards Delivers Fisheries Patrol Vessel Leonard J. Cowley page: 36
- Free 12-Page Brochure On Marine Control System Offered By Forney page: 37
- Detroit Diesel Allison Announces Significant Engineering Advancements To Its Series 149 Engines page: 37
- Tyne Shiprepair Awarded Defence Ministry Contract To Convert Fleet Auxiliary page: 37
- Product Carrier 'Lucy' Christened At Hyundai's Ulsan Yard For Overseas Shipholding Group page: 38
- New Brochure Highlights Capabilities Of Marathon LeTourneau Offshore page: 38
- Aalborg Vaerft Awarded Danish Navy Contract For Seven Flex 300 Convertible Combatant Vessels page: 38
- McDermott Completes Twin Drilling Rig Ordered By Helmerich & Payne International page: 41
- Meyer Werft Shipyard Converts Containership Into Livestock Carrier page: 41
- Marine Drive Systems Announces N e w Shaft Systems page: 41
- N e w X-FLO Turbo Compressor Represents Major Advance In Impeller Technology page: 41
- Kockums Yard To Build Universal Ferry For Polish Shipping Company page: 41
- Transtema Kockumation Introduces New Computer System For Shipping Industry page: 41
- Huge Drydock At Bethlehem's New Sabine Yard Now Operational page: 42
- Marinette Marine Lays Keel For First Of 13 Yard Patrol Craft page: 42
- Avondale's Harvey Division Finishes Major Refurbishing Of Offshore Tug page: 44
- Meco's " T a r g a " Technology Boosts Water Maker Efficiency page: 45
- Orders A n d Deliveries Of T w i n - S c r ew Schottel-Tugs Continue W o r l d w i de page: 45
- N e w M e t h o d Of Inspection Used By Pacific M a r i ne Is Cost-Effective page: 45
- Report Shows Amerlock 400 To Be Cost-Effective Maintenance And Repair Coating page: 46
- MHI Develops Energy-Saving Marine Super Turbo Generating System page: 46
- Centurion Industrial Marine Offers The 'Crew Seat page: 47
- New Brochure Available From SKF Steel Couplings On Its OK Coupling page: 47
- New Instrument Manifold Improves Safety In Process Control Systems page: 47
- Inventive Machine Introduces Improved B l a s t / V a c u um Units page: 54
- Barksdale Controls Presents Line of Pressure Transducers page: 54
- Limitorque Introduces New Worm Gear Operators For Valve Or Mechanism Control page: 54
- Electronic Mail Techniques Save Thousands Of Dollars In Message Costs, According To NAV-COM Report page: 55
- Uniden To Introduce Six New Marine Radio Models At IMTEC Show In Chicago page: 55
- A New 12-Inch Radar From Krupp Atlas Elektronik page: 55