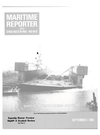
SHIPLIFTING AND DRYDOCKING SYSTEMS
Better Equipment Increases Profitability —A Review— Most U.S. shipyards are in the process of increasing their efforts to expand repair and conversion work, both commercial and military. As many of these projects include drydocking, the efficiency of a shipyard's shiplift/transfer systems plays a vital role in the profitability of any contract.
" The editors of MR/EN asked the leading designers, manufacturers, and users of these systems to tell us about their latest developments and experiences. The following review is based on replies that we had received at press time.
FOR MORE INFORMATION If you wish to receive additional information on any of the products or installations described in this review, circle the appropriate reader service number(s) listed under each company's name, using the postagepaid card bound into the back of this issue.
A M I R I K I A N ENGINEERING Circle 80 on Reader Service Card Amirikian Engineering Company of Chevy Chase, Md., recently announced the development of a revolutionary drydock that features a new concept of stabilization for floating craft. Called "Stabilized Buoyancy Lift Dock and Shore Transfer System," the new floating dock, consisting of a compartmented pontoon and complemented with a stabilizer, can lift a ship out of water and raise it to the needed level for direct roll-on shore transfer.
The drydock, installed in a berth adjacent to a pier, bulkhead, or a corner of a slip, is operated by compressed air—without the aid of winches, cables, or chains, and needs no second flanking pier. Thus, the dock being free of obstructions of such adjuncts, drydocking access of a ship can be made from the side or an end; after elevated lift, the shore transfer is likewise accomplished sideways or endwise. Furthermore, no limitations are imposed on the dock's lifting capacity.
It can raise and shore-deliver any floating craft—whether it be a small fishing vessel, an ocean liner, a supertanker, and even a giant aircraft carrier. The entire operation can be carried out through a programmed remote control.
The stabilizer consists of a specially devised structural framing that is fitted between the inboard face of the dock and the flanking pier or bulkhead. It serves the same stabilizing function as do the sidewalls in a conventional floating drydock; that is, to restore equilibrium after a disturbance due to an external force. However, in a floating drydock, restoration of equilibrium is obtained through jerky motions of pitch, roll, and yaw, while in the lift dock the stabilizer resists such rotational motions to occur, and at the same time provides guidance for free vertical movements under both tidal rise and fall, as well as in operational ascent and descent, thus keeping the deck of the dock in a horizontal plant at all stages of operation.
The stabilizer was conceived by Dr. Arsham Amirikian, president of Amirikian Engineering, who formerly served in the U.S. Naval Facilities Engineering Command as chief designing engineer and chief engineering consultant. Upon retirement in 1971, he established the firm to render private consulting services, specializing in drydocking facilities.
BARDEX HYDRANAUTICS Circle 81 on Reader Service Card Founded in 1963 as an engineering- oriented organization having the capability to develop and manufacture sophisticated hydro-mechanical systems, Bardex Hydranautics is headquartered in Goleta, Calif., with offices in Houston, London, and Singapore. The company designs and manufactures heavyload moving equipment for offshore and shipyard-related activities, including systems for applications ranging in size to more than 50,000 tons.
Bardex systems are specified by the major designers, drillers, oil companies, and shipyards around the world. These systems meet the exacting standards of all certifying and classifying agencies, including the American Petroleum Institute, the U.S. Coast Guard., American Bureau of Shipping, Lloyd's Register of Shipping, and Bureau Veritas.
Bardex has supplied rig-skidding systems for 95 percent of the major offshore platforms in the world, and is said to be the only major shiplift manufacturer whose equipment has a flawless safety record. The company is also a supplier of main deck structure lifting systems for offshore drilling rigs, and pioneered highly flexible, low-cost hydraulic shipyard systems for transferring ships from the water to berths on shore.
Bardex Hydranautics products are to be found virtually wherever there is a requirement to move a heavy load, such as ship and drill rig building and repair, offshore oil and gas drilling and production, and heavy construction.
Where heavy loads, such as ships, must be lifted with precision and safety, a Bardex chain jack lifting system is employed. The key element in this lifting system is the hydraulic chain jack, which consists of a vertical jack that lifts its load by pulling one or more chains upward through two sets of locking pins in precise steps of one chain pitch. As in other Bardex Hydranautics systems, the number, size, and design of the assemblies vary with customer load requirements.
Chain jacks may be used individually, but are normally employed in sets of two or more, and can be controlled by one operator from a single control station. Other system components include the hydraulic power unit, chain, load equalizer-compensator assembly, and the interconnecting high-pressure hydraulic hoses.
The key element in a Bardex skidding system is the jacking assembly that the company calls a gripper jack. It consists of a doubleacting hydraulic jacking cylinder (the jack) mounted to a patented hydraulic locking device (the gripper), which clamps the flange of the beam on which the load is resting and acts as a movable reaction point for the jack.
For rapid turnaround in high-use areas of a shipyard, BH provides wheeled transfer systems (bogie trains). Lifting and lowering of the ship to and from support blocking are performed with a self-contained hydraulic system on the bogie train.
With this system the side transfer pit is eliminated, allowing free movement of vehicles and foot traffic.
The gripper jacks are normally used on skid beams, but transfer systems using roller beams are also available. These require less jacking force than skid beam systems, minimizing initial equipment costs.
Where moving heavy loads over relatively unprepared surfaces is required, a BH Translift "walking" system may be used. The basic Translift system consists of a center load support, connected outer load supports, and an onboard control console. If desired, remote control of all units in the system can be achieved by using a portable pendant console. Translift systems can rotate in a full 360-degree circle, and can "walk" a load using the simple principle of weight transferrence between the center load supports and the connected outer load supports.
Some recent installations of BH equipment in the shipbuilding and repair industry include the following: Hyundai Heavy Industries in Ulsan, South Korea is equipped with a shiplift system and a horizontal transfer system. The shiplift platform is approximately 400 by 66 feet and has a capacity of 4,100 metric tons.
The new $200-million shipbuilding and repair complex of PNOC Marine Corporation at Batangas Bay, Philippines, is equipped with a hydraulic shiplift system and hydraulic wheeled transfer system.
The platform of the elevator measures 566 by 100 feet, said to be the largest hydraulic-actuated elevator in the world.
The floating drydock used at Daewoo's Okpo yard in Korea is equipped with a Bardex roller beam transfer system capable of moving ships or sections weighing up to 6,000 metric tons. The same hydraulic system is also used on fixed or portable beams located in the yard to move offshore structures and jackups as well as ships and sections.
BIW-PORTLAND Circle 82 on Reader Service Card Bath Iron Works opened its Portland, Maine, overhaul and repair facility in late 1983. Since then, four U.S. Navy ships have been accommodated in the huge floating drydock, the largest of its type on the East Coast.
With a certified lifting capacity of 81,000 tons, this drydock could accommodate 80 percent of the ships now operating throughout the world. The dock measures 844 feet in length, 256 in width, and has a clear docking width between wingwalls of 142 feet. Crane service is provided by two 25-ton wingwall units.
As originally designed during World War II, the drydock utilized independent machinery spaces within the hull of each of the nine dock sections. Each of these spaces contained the pumps, diesel generators, electrical switchgear, and controls required to operate that dock section.
The BIW overhaul of the electrical systems included three major objectives: the power distribution system needed to be converted to operate on commercial mains in lieu of the 18 installed generators; facilities had to be added to provide for the greatly increased shore power requirements of modern ships; and a centralized control and monitoring system was necessary to eliminate the need for nine machinery space operating crews.
Commercial power was brought aboard at 12,740 volts using two independent feeders. These supply a new 480-volt distribution switchboard via two new 2,500-kva transformers.
Independent shore power for ships within the dock is distributed from the dock feeders via 2,000-kva transformers and a second new 480/450-volt switchboard.
A 560-kw emergency generator was added to permit limited operation in the event commercial power is lost.
A new centralized control station was provided by construction of a control house above the inboard wingwall. The centralized control and monitoring features added include monitoring of tank levels, control of the ballast pumps, monitoring and limited control of the power distribution and lighting systems, and control of the tank, pump, and flooding valves.
Approximately 900 existing machinery control circuits are interfaced with the control system and multiplexed for transmission back to the central control station by a remote electronics panel installed in each of the machinery spaces. Automatic control and alarm features are provided by a central computer within the control console.
BETHLEHEM STEEL Circle 83 on Reader Service Card Bethlehem Steel Corporation's floating drydock at the new Sabine Yard in Port Arthur, Texas, consists of eight identical sections. They each measure 240-feet long, 101-feet wide, and 23^-feet deep. The eight sections, when fastened together, have a lifting capacity of 64,000 tons, making it one of the largest drydocks in the country.
Each drydock section is a 4,200- ton, all-welded steel structure consisting of a ship-shaped hull (pontoon) that supports two rectangular box-shaped wing (side) walls. The midship portion of the pontoon contains a non-floodable compartment, or buoyancy chamber. The greater part of the mechanical and electrical equipment required for operation of the dock section is located in the various compartments of this chamber.
During normal operation of the dock, access to the buoyancy chamber is gained from the wing walls through two watertight passageways extending through the pontoon, one passageway to each wing wall. The passageways continue upward through the wing walls in the form of circular stairways and terminate at the safety decks.
The remainder of the pontoon is subdivided by two longitudinal and two transverse bulkheads into eight ballast compartments, four on each side of the buoyancy chamber. Each ballast compartment can be flooded or pumped out through a lateral pipe that is connected to the flood- ing and pumping system of the pontoon.
The wing walls, which house more than 28,000 square feet of potential office and shop space, are 48-feet high, 18-feet wide, and 101-feet long. The distance between wing walls is 122 feet.
In the assembled dock—with three-foot spaces between sections— the wing walls of the individual pontoons are connected with welded plates. This creates two continuous box girders extending the full-length of the dock, while it also provides longitudinal moment strength.
To be devoted primarily to the repair and inspection of mobile offshore drilling units and production facilities, the drydock contains electrical generating equipment, utility capacity, and cranes, and is equipped with machine, carpenter, and electrical shops.
The sectional dock can be configured to provide a clear docking area of either 413 by 362 feet or 829 by 122 feet, depending on the size and shape of the incoming vessel. This unique flexibility will accommodate jackup rigs, semisubmersibles, submersibles, and drillships.
The U.S. Navy surplus drydock, built during World War II, was transported earlier this year from Pearl Harbor to Bethlehem's Beaumont Yard, where it was refurbished and modified.
CRANDALL DRY DOCK C i r c l e 8 4 on Reader Service Card Crandall Dry Dock Engineers Inc. of Dedham, Mass., has been involved for more than 50 years in design and construction of ship transfer systems, from railway drydock cradles and floating drydocks ranging from a few hundred tons to up to 50,000 tons. Most have used low-friction rollers on flat rail plates to minimize propulsion requirements, but some, like Ingalls Shipbuilding in Pascagoula, Miss., use the self-propelled Western Gear cars and pallets on heat-treated crane rails.
The floating drydock is the only dock capable of lifting very heavy ships up to yard elevation for transfer to several berths without need for cross-transfer due to the dock's own mobility. In general, Crandall has found the economics of vessel transfer to depend on the duration of storage on the berth. For new construction, as at Ingalls and Avondale, the transfer is vital so that the dock itself can remain unoccupied for short-duration ship repairs. Selectivity is very important when one drydock is to service many land berths. However, if the many berths are basically for winter storage where sequence of springtime launching is unimportant, then a more compact land utilization is more logical, as exists at Marine Industries in Sorel, Quebec.
A recently built 1,200-ton railway drydock at Zeebrugge, Belgium, with two 1,000-ton side transfer berths, has proven very effective and economical, with no land space wasted for a cross transfer. The very shore duration of vessel repairs, ranging from eight hours to about three days, is done mainly on the cradle of the drydock. Side transfer is used in Berth No. 1 for seven- to 30-day work, and in Berth No. 2 for all projects of over two or three weeks, including new construction or major conversions. The slipway and its transfer service the Zeebrugge fishing fleet of about 155 trawlers in a wet basin that permits 24-hour operation, with more than two hauls per day if necessary.
For stability reasons, smaller vessels that have an inclined keel as they float without cargo, must be docked on an inclined dock. Use of a curved track for the railway makes it possible for the cradle deck to be inclined to maintain vessel stability when grounding and yet be horizontal in the up position; the mobility of a floating drydock achieves the same result.
Two recently constructed transfer systems were built to serve two older marine railways where the vessel keel line remains on a declivity. The demand by a few yards to increase their repair capacity by use of transfer berths rather than new drydocks has been solved by using a series of horizontal side transfer ways arranged in a stepped fashion to suit the original incline of the railway cradle.
Modern practice in shipyard development starts with the main drydocking system designed such that in future years if business so demands transfer can later be added without disrupting the original dock. This is the case for shiplifts, railways, or floating drydocks.
Finally, it is interesting to note that even though the best situation for transfer from floating docks is where the tide range is small, Crandall has developed solutions even where water level changes range from 6 feet to 17 feet. Vessel transfer to and from drydocks is a concept not to be overlooked in new or even in existing shipyards.
M A . N . - G HH Circle 91 on Reader Service Card GHH is one of the oldest builders of drydocks, having started in 1876, and since 1956 it has built 88 docks at its facilities in Blexen, Germany, on the southern bank of the Weser River across from Bremerhaven.
Forty-eight of these were delivered after Germany's shipyards were al- Circle 292 on Reader Service Card lowed to resume work in 1953, six of which were sold to the USA.
This year alone, M.A.N, delivered the 22,000-ton dock Mission Bay to Continental Maritime of San Francisco, and is soon to launch a 28,000- ton dock for the Middle East.
Noteworthy about the dock Mission Bay is that it complies with the damage stability requirements in accordance with Mil Std 1625; the dock has been designed to accommodate both modern U.S. combat ships such as the DDG51, and also commercial vessels of the Panamax size; and it features M.A.N.'s unique remote controlled bilge block system that allows easy adaptation to the various different hull forms of modern Navy ships. (See MARITIME REPORTER issue of Mav 15, 1985, page 8.) M.A.N.-GHH's facilities have immediate access to the open sea, and feature large fabrication shops to preassemble dock modules, as well as a slipway of over 1,200 feet in width to accommodate the construction and launching in one piece of docks of any kind or size. At the time of launching, docks are completely outfitted and ready for towage to final destination.
Besides customer-tailored design and building of docks by in-house specialists, M.A.N.-GHH offers additional services, such as consultation for anchorage and offsite preparation, towing to site at fixed prices, commissioning, personnel training for dock operation, and assistance in securing long-term financing.
The management of the Dockbuilding Division, including engineering and sales, is located at M.A.N.-GHH headquarters in Oberhausen-Sterkrade, Germany.
M.A.N.-GHH is represented in the U.S. by American M.A.N. Corporation in New York, with branch offices in Houston, San Francisco, and Seattle.
MARINE TRAVELIFT Circle 92 on Reader Service Card Located in Sturgeon Bay, Wise., Marine Travel, Inc. is one of the world leaders in the design and manufacture of mobile boat hoists.
The latest addition to the company's complete line of hoists is the 100 BFM, called a "little" giant that can handle commercial fishing vessels, workboats, and pleasure craft.
This wide versatility can result in more customers and improved shipyard utilization.
Outstanding design features of the 100 BFM include: "beam forward" design for more rigging and foredeck structure clearance; all slings power-adjustable; highstrength, low-alloy main frame construction; fast, two-speed hoisting and travel; low, enclosed operator's cab; full instrumentation; orbital steering with automatic realignment; stainless steel hydraulic tubing; accurate load weight indicator; radial tubeless tires; mechanical anti-two-block system; fully enclosed, easy-access engine and hydraulic compartment; and better boat handling with forward sling adjustment aft of the front beam.
NORSHIPCO Circle 85 on Reader Service Card Norfolk Shipbuilding and Drydock Corporation in Virginia has announced the arrival of the newest component in its ship repair facilities— a self-contained steel floating drydock that has been named Virginian.
Built in the Netherlands, it has a lifting capacity of 20,000 long tons, an overall length of 669 feet, overall width of 126 feet, and width between wingwalls of 103 feet at the operating deck level.
The first half of the dock arrived at the shipyard in June this year and the second half during the first week of August, both towed across the Atlantic on oceangoing semisubmersible barges. The dock was scheduled to become operational by the end of August.
The new arrival will join the 950- foot-long, 160-foot-wide Norshipco Titan drydock, which has a lifting capacity of 54,250 long tons and gives the Norfolk shipyard one of the most significant privately owned drydock lifting capacities on the East Coast.
The Virginian will be divided by five watertight bulkheads into six compartments, each 98.4 feet long.
Two watertight longitudinal bulkheads, each 23 feet from the center line, and one on the center line, will divide the dock into a total of 24 tanks. The most forward and most aft center tanks are both 118 feet long. Normal pumping time is approximately 140 minutes.
PEARLSON ENGINEERING Circle 86 on Reader Service Card Syncrolift® shiplifts and ship transfer systems are clearly the world leaders in the field, with more than 160 installations in 59 countries.
More than 99 percent of vessels docked on shiplifts worldwide are docked on Syncrolift shiplifts, which provide a means for quickly and easily handling ships between the water and the shipyard, moving them to level on-shore repair berths where material flow and access can be optimized.
Pearlson Engineering Company, Inc. of Miami, Fla., designs Syncrolifts to meet the specific requirements of shipyard owners. Using state-of-the-art computer-aided design and drafting systems, Pearlson prepares detailed design drawings for the shiplift platform and transfer system components that enable the client to fabricate these items locally. The specialized lifting equipment and control system are furnished by Pearlson, along with the services of a commissioning engineer to assist in the commissioning and testing of the Syncrolift system.
Syncrolift systems offer pushbutton ease of operation, drydocking in a minimum amount of space, drydocking on an even keel at yard elevation with no obstructions to impede work area, continuous synchronization of all lifting points, and easy access to all components for lower maintenance costs.
In October this year Pearlson will begin erection of the world's largestcapacity Syncrolift at Vickers Shipbuilding and Engineering Ltd. in Barrow-in-Furness, U.K. The Vickers shiplift will incorporate a platform 161.8 by 21.7 meters and have a lifting capacity of 24,000 metric tons. This installation is part of the Submarine Facilities Project and will include the world's largest single- lever transfer system. Groups of self-powered transfer cars will be used to position individual hull sections during assembly as well as move the completed conventional and nuclear submarines from the construction hall to the Syncrolift platform for launching.
The Vickers installation will feature wire rope using a proprietary " b r i f i l " material from British Ropes. In this process the spaces between individual wires are filled with a "plastic" material while the rope is formed. This results in what is commonly known as a "valleyfilled" wire rope. Ropes manufactured in this way require only a small amount of surface lubrication and effectively eliminate the problem of internal corrosion. It is anticipated that these brifil ropes will, have a useful life in excess of 10 years. Lloyd's Register of Shipping has approved testing of the wire rope assemblies at the site using non-destructive testing equipment.
It is no longer necessary to breaktest wire rope to prove its condition.
During the first half of 1985, three Syncrolift projects were commissioned.
An eight-hoist (137-ton capacity each) shiplift in Howth, Ireland, for the Office of Public Works is now operational. This facility is part of the Department of Fisheries plan to develop Howth as a major fishery harbor. The platform measures 36.5 by 12.2 meters and has a maximum lifting capacity of 875 metric tons.
At the port of Iskerderun in Turkey, the Syncrolift is part of the new Vessel Maintenance Facilities operated by Turkish State Railways.
This installation incorporates eight 244-ton hoists, has a platform 40- meters long and 22-meters wide, and has a maximum lifting capacity of 1,440-metric tons.
In Japan, the second Syncrolift caisson lift has been completed for Penta Ocean Construction Company at Yunotsu. This lift incorporates eighteen 376-ton-capacity hoists, has a platform 30.1-meters long by 21-meters wide, and has a maximum design capacity of 200 tons per meter.
Recent orders include a Syncrolift of the Oman Navy. Hochtief Aktiengesellschaft of Essen, West Germany, has contracted for an 8,580- metric-ton maximum-lifting-capacity shiplift on behalf of the Sultanate of Oman. This facility will have a platform 106-meters long by 18.5- meters wide, and utilize forty 244- metric-ton capacity hoists.
Syncrolift continues to maintain its overwhelming market position with its proven design and easy-tomaintain, reliable components.
Since the original invention in 1954 by Raymond Pearlson, Syncrolift has revolutionized the way modern shipyards are planned.
SENERMAR Circle 87 on Reader Service Card Senermar S.A. of Madrid and Bilabo, Spain, naval architects and shipyard designers, recently received a contract to design a new floating drydock that will be owned by the Peruvian Navy and operated by the Peruvian shipbuilder and repairer, Sima Peru. This dock, with a lifting capacity of 4,500 tons and capable of handling vessels of up to approximately 9,000 dwt, will be built at Sima Peru's Callao shipyard.
Sima Peru, which has three yards—at Callao, Iquitos, and Chimbote—employs about 1,000 workers on newbuilding and 2,100 on repairs, and can construct ships of up to 65,000 dwt including tankers, multi-purpose vessels, and warships.
The company can repair vessels of up to 65,000 dwt including tankers, multi-purpose vessels, and warships. The company can repair vessels of up to 26,000 dwt at the Callao yard.
The Senermar contract involves design, technical assistance, the supply of all major material, and financing. The design of the Sima drydock will be developed by Senermar using its FORAN internationally accepted CAD/CAM system, which will produce architectural calculations, classification drawings, and construction design. During construction of the drydock at Callao, all technical assistance will be provided by Senermar, including the provision of on-site engineers.
Supply of materials will be handled by INDUNARES—the Spanish Association of Shipbuilding Auxiliary Industry—and will cover cranes, pumps, compressors, generating sets, steel, pipe, valves, etc.
This "total package" approach was also taken with the floating dock constructed recently at ASMAR of Chile's Talcahuano yard, which is owned and operated by Socibar, a joint venture of ASMAR and E.N.
Bazan of Spain. Capable of handling vessels of up to 30,000 dwt, this dock was also designed by Senermar, including technical assistance for material specifications.
Having applied this "total package" approach to the construction of two floating drydocks, it seems likely that Senermar will use it again on future contracts.
SOUTHWEST MARINE Circle 88 on Reader Service Card The San Diego shipyard of Southwest Marine, Inc. (SWI) last year accepted delivery of the 22,000-toncapacity drydock Pride of San Die- go, ordered in late 1982 as part of the yard's modernization plan. The computer-operated, self-maneuvering land transfer drydock is a major unit in SMI's $35-million renovation of the San Diego yard. The modernized facilities exceed all U.S.
Navy requirements, and allow the yard to effectively service all types of naval and commercial vessels.
Built by Kawasaki Heavy Industries in Japan, the Pride of San Diego dock has many innovative features.
It is capable of transferring 10,000-ton ships (cruiser/destroyer types) from dock to shoreside platforms using a new transfer method.
Another feature is its ability to transfer ships with its computerized control system, regardless of tide changes.
The Pride of San Diego is equipped with remote-controlled, articulated dock arms that, in most cases, will reduce the need for staging that is normally required. The dock is cathodically protected against corrosion, environmentally safe, and completely energy self-sufficient.
Part of SWI's modernization at San Diego is a new 700- by 60-foot pier that can serve ships with drafts of up to 35 feet. A new 65-ton gantry crane was installed to service ships at the pier and in the drydock.
TODD-SAN PEDRO Circle 89 on Reader Service Card A $47-million Syncrolift shiplift and transfer system, currently the largest and most technologically advanced facility of its kind in the world, was dedicated last year at the San Pedro, Calif., yard of Todd Pacific Shipyards Corporation's Los Angeles Division.
The Syncrolift is a product of Pearlson Engineering Company of Miami, the world leader in shiplift technology and the only firm in the world devoted exclusively to the design and manufacture of shiplift systems.
The San Pedro installation is designed specifically for construction and repair of naval surface combatants, but it is also suitable for commercial vessels. The system increased the Los Angeles Division's new construction capacity by 100 percent and its repair capability by 250 percent.
The Syncrolift permits the San Pedro yard to perform multiple drydockings with one lifting platform that hoists a ship from the water to land level, where it is towed onto a side transfer carriage and moved to any of five work areas. The platform, which can be used as a sixth work station during peak periods, is powered by one hundred and ten 15- hp electric motors. Lifting speed is approximately nine inches per minute; the designed maximum lifting time is 72 minutes.
The platform, which measures 655 by 106 feet, can handle ships with overall length of 780 feet and beam of 105 feet. Maximum lifting capacity, when docking directly on the platform without a cradle, is 22,000 long tons. Maximum draft over the cradle is 32 feet.
The new shiplift system will enable the Los Angeles Division to achieve productivity gains resulting from: multiple access to vessels undergoing overhaul and repair; better material handling and flow, including prepositioning; accelerated preoutfitting of modular units for new hulls under construction; use of the shiplift as a launching platform in lieu of, or supplementing, new construction in progress on the inclined ways; lessening of environmental constraints by working ships on land instead of at a wet berth; and mechanical/electrical utility conservation, including recycling of used blasting grit.
The design of the strategically placed mechanical manifolds, multiservice electrical stations, and crane services at the work bays provide full service to single- or double-ship berths. The demands for each bay were developed using peak loads and other requirements as stipulated for fully crewed Navy ships.
Every anticipated requirement of the ship repair and modular assembly options, including at the landlevel berths, was given full consideration.
Comparable services were designed for installation at the lifting platform to satisfy production requirements at that location.
TTS Circle 90 on Reader Service Card Total Transportation Systems, Inc. (TTS) of Newport News, Va., recently delivered a dual "walking beam" transporter system to Marinette Marine Corporation in Marinette, Wise. Said to be the first of its kind in the U.S., this system consists of eight 200-ton walking beam units, and has been designed to be expanded to handle 3,200 tons by attaching additional walking units.
The dual walking beam is an extremely compact hydraulic transporter system that has been used not only to move large ship sections, or even a complete ship, but will also fit or regulate the sections during the actual construction of the vessel. The system can operate on most rough-graded surfaces without any foundations or walkways. The precise movements of the hydraulics combined with the design of the walking unit.make the dual walking beam a highly effective shipyard tool.
Kenmark Industries of Santa Barbara, Calif., a wholly owned subsidiary of TTS, recently designed and delivered a 200-ton, twin-lift hoist system to Marinette Marine, unique in that it has winches located on only one side of the vessel.
This feature maximizes the flexibility of the shiplift by offering improved access to the vessel. It also allows easier transfer of the vessel on and off the shiplift platform from either the free side or from the end.
This configuration is of special interest to the shipyard owner who wishes to make the most of the valuable land surrounding the shiplift for construction or repair activities.
In addition to the improved arrangement, the twin-lift hoist system design reduces both the initial capital and the maintenance cost of the shiplift.
Kenmark has just received a contract from Hyundai Heavy Industries in South Korea for a jacket loadout and launch system. With a capacity of 20,000 tons, this system will consist of two hydraulic power units and a number of jacking units of the gripper design. HHI intends to use the jacking system for the loadout of the San Miguel jacket now under construction at its Ulsan yard. This system can easily be expanded to handle larger jackets in the future.
Read SHIPLIFTING AND DRYDOCKING SYSTEMS in Pdf, Flash or Html5 edition of September 1985 Maritime Reporter
Other stories from September 1985 issue
Content
- Tidewater Marine Acquires 5 Vessels From Otto Candies page: 5
- Hawker Siddeley/Kongsberg Collaborate In Venture page: 5
- American Air Filter Offers N e w Brochure On Cartridge Filters page: 5
- Big Supply Vessel 'Nicor Sailor' Converted By Eastern Marine page: 6
- Owen And Richards Named Managers At Honeywell page: 6
- MSC Announces FSS Award Totaling $30.7 Million page: 6
- Autronica's New NK-5 Unit Monitors Ship's Engine page: 6
- Grow Group Acquires Napko Coatings Division page: 6
- Bollinger Shipyard Dedicates Island Class USCG Patrol Boat Fleet page: 7
- Sulzer ZA40 Diesels Will Power Two Ferries Ordered In U.K. And Japan page: 8
- Cummins-Powered Construction Pushboat Delivered By Keith A. Record page: 8
- Tenneco Oil And Sohio Will Use Canmar Rig For Arctic Drilling page: 8
- Canadian Offshore Resources Exposition page: 8
- Shipboard Liquid-Level Sensor O f f e r e d By Tecnomatic Controls page: 9
- Maritime Association Installs New Officers And Directors page: 9
- Royal Cruise Line To Build Two Luxury Liners At Cost Of More Than $200 Million page: 10
- Goldstein Named Chairman Of COMSAT—Joseph Promoted To President page: 10
- Krupp MaK Consolidates In North America page: 11
- Innovative Triple-Screw Tugboat Launched By Halter Marine page: 11
- Truman Joins INDEECO As A d v e r t i s i n g Manager page: 12
- Moss Point Marine Delivers New Sternwheeler, Colonel page: 12
- Aluminum Boats Delivers High-Speed Crew/Utility Vessel To A&P Boats page: 12
- Matson Asks Bids On $30 Million Conversion of 'Matsonia' page: 14
- Brown & Root Awarded Feasibility Study Contract For Chevron Offshore Unit page: 15
- Congressional Maritime Caucus Establishes An Advisory Board page: 15
- SHIPLIFTING AND DRYDOCKING SYSTEMS page: 16
- OUTSTANDING RIG DESIGNS page: 16
- Bethlehem's Newest Jackup Design Can Drill In Water 600 Feet Deep page: 19
- Congressman To Address OMSA Meeting On Warehouse Vessels page: 19
- Alsthom Unit Strengthens Position In Norwegian Offshore Market page: 20
- Sandy Hook Dispatch Boat Delivered By Gladding-Hearn page: 20
- Saab Receives Order To Supply TankRadars From Tampa Shipyard page: 21
- Bertrem Products Importing Straub Couplings For U.S. And Canadian Distribution page: 21
- Conversion Of Fast Sealift Ship 'Regulus' Completed By NASSCO page: 22
- ASRY's 1984 Revenues Up Nearly 20 Percent page: 22
- Wartsila Wins Contract To Build Rig Transport Vessel For USSR page: 22
- E X P O S H I P Riomar85 page: 24
- Midland Ross Offers Free, 20-Page Brochure On Max-Gard® System page: 25
- Wilson W a l t o n Receives Two Contracts For Emergency Service page: 26
- Sale Of Imperial Survival Suits Approaches 100,000 page: 26
- Laursen Selected As New Managing Director Of Hemple Holding page: 28
- Owen And Richards Named Managers At Honeywell's Marine Systems Division page: 28
- CANADIAN SHIPBUILDING AND REPAIR YARDS page: 28
- Hollming Opens Louisiana Office For Marketing Aquamaster Product Line page: 29
- Two N e w Instruments To Measure C u r r e n t / V o l t a ge Introduced By Amprobe page: 29
- U.S. NAVY SHIP PROCUREMENT page: 30
- Holman and Wildasin Elected At Raymond International page: 31
- MIROS To Market New Products In U.S. page: 32
- Furuno Introduces New Low-Cost, High-Performance Loran Navigator page: 32
- NMEA Plans Expansion Of Interface Standard page: 32
- Kockums Completes Advanced Car/Truck Carrier For Wallenius page: 33
- Cincinnati Gear Completes Testing Of New, Sophisticated Marine Drive For Navy T-AO 187 Class Oilers page: 34
- New Alarm Reduces Boiler Failures, Diesel Failures And Repair Costs page: 34
- ADS Workshop Scheduled For October 2-3 In Chicago page: 35
- Seattle Yard GM Elected To Todd's Board Of Directors page: 35
- Caterpillar Offers 20-Page Catalog On Marine Diesels page: 35
- Wagner Wins $4.5-Million Contract For Steering And Control Systems page: 35
- Three Major Beth Steel Programs Highlight New Offerings To The Offshore Industry page: 36
- LiCausi Establishes New Boiler Consultant Firm page: 36
- West Coast Manly Shipyards Delivers Fisheries Patrol Vessel Leonard J. Cowley page: 36
- Free 12-Page Brochure On Marine Control System Offered By Forney page: 37
- Detroit Diesel Allison Announces Significant Engineering Advancements To Its Series 149 Engines page: 37
- Tyne Shiprepair Awarded Defence Ministry Contract To Convert Fleet Auxiliary page: 37
- Product Carrier 'Lucy' Christened At Hyundai's Ulsan Yard For Overseas Shipholding Group page: 38
- New Brochure Highlights Capabilities Of Marathon LeTourneau Offshore page: 38
- Aalborg Vaerft Awarded Danish Navy Contract For Seven Flex 300 Convertible Combatant Vessels page: 38
- McDermott Completes Twin Drilling Rig Ordered By Helmerich & Payne International page: 41
- Meyer Werft Shipyard Converts Containership Into Livestock Carrier page: 41
- Marine Drive Systems Announces N e w Shaft Systems page: 41
- N e w X-FLO Turbo Compressor Represents Major Advance In Impeller Technology page: 41
- Kockums Yard To Build Universal Ferry For Polish Shipping Company page: 41
- Transtema Kockumation Introduces New Computer System For Shipping Industry page: 41
- Huge Drydock At Bethlehem's New Sabine Yard Now Operational page: 42
- Marinette Marine Lays Keel For First Of 13 Yard Patrol Craft page: 42
- Avondale's Harvey Division Finishes Major Refurbishing Of Offshore Tug page: 44
- Meco's " T a r g a " Technology Boosts Water Maker Efficiency page: 45
- Orders A n d Deliveries Of T w i n - S c r ew Schottel-Tugs Continue W o r l d w i de page: 45
- N e w M e t h o d Of Inspection Used By Pacific M a r i ne Is Cost-Effective page: 45
- Report Shows Amerlock 400 To Be Cost-Effective Maintenance And Repair Coating page: 46
- MHI Develops Energy-Saving Marine Super Turbo Generating System page: 46
- Centurion Industrial Marine Offers The 'Crew Seat page: 47
- New Brochure Available From SKF Steel Couplings On Its OK Coupling page: 47
- New Instrument Manifold Improves Safety In Process Control Systems page: 47
- Inventive Machine Introduces Improved B l a s t / V a c u um Units page: 54
- Barksdale Controls Presents Line of Pressure Transducers page: 54
- Limitorque Introduces New Worm Gear Operators For Valve Or Mechanism Control page: 54
- Electronic Mail Techniques Save Thousands Of Dollars In Message Costs, According To NAV-COM Report page: 55
- Uniden To Introduce Six New Marine Radio Models At IMTEC Show In Chicago page: 55
- A New 12-Inch Radar From Krupp Atlas Elektronik page: 55