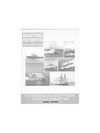
1986 DIESEL ENGINE GUIDE
As we enter 1986, marine engineers and shipowners have available the largest selection of diesel engines ever—low-speed, mediumspeed and high-speed machines; two-stroke cycle and four-stroke cycle designs; crosshead-piston and trunk-piston designs; loop-scavenaged and uniflow-scavenaged designs; conventional- and opposedpiston designs. Not only is the available selection broad enough to satisfy the needs of nearly every ship design but the fuel economy available from the modern diesel engine makes it the undisputed choice of nearly every shipowner building or contemplating to build a ship. Even with the depressed state of the marine industry, the international and domestic diesel engine manufacturers continue their aggressive research and development programs.
One of the greatest problems facing both marine engineers and owners contemplating new ship construction is keeping up with the new developments in diesel engines for both main propulsion and auxiliary duty.
ENGINE AVAILABILITY RANGE Whereas a decade ago there were apparent power ranges for marine diesel engines, today we find very extensive overlapping of the power ranges for diesel engines as classified by specific speed; low-speed engine C s = l - 3 , medium-speed engines C s = 3 - 9 , h i g h - s p e e d engines Cs = 9-27. (Note specific speed is defined as C. = ln2/600,000 where 1 = length of stroke in inches and n = engine speed in rpm.) Lowspeed engines can be found in sizes from just a few thousand horsepower to over sixty thousand horsepower.
Medium-speed engines range from approximately one thousand horsepower to well over twenty thousand. High-speed engines range up to a few thousand horsepower.
With the advent of the super-long stroke and what some may call the ultra-long stroke engines, the engine speed of the diesel engine is as low as 50 rpm at rated power. The upshot of this colossal range of engines available for marine application is that the ship designer can select an engine that will allow him to optimize the vessel design. Power and fuel consumption are not the only variables considered in selecting an engine, for even the largest of ships, but other variables impacting on the economics of the vessel are appropriately considered such as engine dimensions, engine weight and impact on overall system integration and maintenance.
FUEL ECONOMY A few years ago the designers of low-speed engines, responding to the demands caused by the rising fuel prices of the mid-1970s, achieved a significant breakthrough when they developed engines with thermal efficiencies of greater than 50 percent (specific fuel consumption of 125 g/bbp h). The designers of low-speed diesel engines achieved this breakthrough by developing the long-stroke engines with their greater capacity for expanding the cylinder gases and the use of uniflow scavenging. At present, the ultralong stroke engines are approaching stroke/bore ratios of 4:1 and are achieving SFC of 115 g/bbp h. Some medium-speed engine designers have also taken advantage of greater stroke/bore ratios (approximately 1.4:1) to improve the fuel economy of the inherently more efficient, four-stroke cycle engines to a level where it rivals the best of the large bore low-speed engines. Both lowspeed and medium-speed engine manufacturers have adopted more of a systems approach to the configuring of their engine package and have incorporated into their engine packages shaft-geared recovery power turbines yielding SFC of approximately 115 g/bbp h at economy ratings.
FUEL COMPATABILITY Diesel engine manufacturers catering to the needs of the international market have long been aware of the need to have their engines capable of burning low-grade/highviscosity fuels without compromising engine reliability or longevity. In general, they have been very successful on this front. Most manufacturers of marine diesel engines for the international market claim to be capable of burning fuels up to 380- cst viscosity. Some manufacturers claim the engines can burn fuels up to 700-cst viscosity. Several engine manufacturers are researching the potential of using coal/oil and petroleum coke/oil slurries as fuel. One research tack that some of the engine manufacturers are using to make their engines compatible with the poor-quality fuels is the use of ceramics for engine components susceptible to attack by the fuel impurities. The use of ceramic and/ or ceramic-coated parts appears to have the potential to increase the tolerance of the engines to low-quality fuels, especially in high-speed and medium-speed engines.
MAINTENANCE Engine manufacturers continue to improve the maintenance requirements of marine diesel engines by developing new component designs with increased longevity and increased ease of removal and repair.
The manufacturers appear to be well aware of the economic pressures forcing ship operators to complement their vessels with ever smaller crews and are adopting their designs to simplify the maintenance procedures and to lessen the demand for manpower. The use of various types of bolt-stretching devices and specialized removal/assembly fixtures has been common for years and their adaptation to the shipboard maintenance process continues.
UPGRADING OF OLDER ENGINES As the economic climate has forced ship operators to change their mode of operation, sometimes requiring the vessels to be operated at powers significantly below design levels, the engine manufacturers have responded by designing and making available retrofit packages allowing the operator to optimize the existing engine to the new operating conditions. The most encompassing of the retrofit packages available involves replacement of pistons and cylinders among other parts of existing standard stroke low-speed engines to convert them to super long-stroke machines rated at a lower power but with improved specific fuel consumption and a better match between crank/propeller speed and ship hydrodynamics.
Other types of upgrading packages include turbochargers, turbocharger intercoolers and turbocharger bypass systems designed to upgrade the engines to optimize performance at new-load conditions.
ANCILLARY ENERGY RECUPERATION SYSTEMS In attempts to improve on the already phenomenal specific fuel rates of the larger diesel engines and to improve on vessel overall fuel rates, various techniques and systems have been used to recuperate energy from exhaust gases and cooling water. The most common of these systems is the waste-heat boiler supplying steam to turbogenerator and/or to various heating loads aboard ship. With the availability of high-efficiency exhaust gas power turbines, it has become possible to extract significantly more energy from the exhaust gas than can be used by the turbocharge blower.
Various engine manufacturers have adopted the exhaust gas power turbine to supply the excess power back to the engine shaft with improvements of 2.5 to 3 percent in specific fuel consumption. Some marine engineers have opted to use the excess exhaust gas energy to drive or assist in driving an electrical generator.
The following review will highlight the developments of the principal diesel engine manufacturers supplying the marine community with propulsion and auxiliary diesel engines.
Read 1986 DIESEL ENGINE GUIDE in Pdf, Flash or Html5 edition of January 1986 Maritime Reporter
Other stories from January 1986 issue
Content
- Bethlehem Steel Selects Delaval R5 Engines For Two New Navy Vessels page: 5
- Bay Shipbuilding Expands Foreign Trade Zone page: 5
- Elliott White Gill Names Lirette Sales Manager page: 6
- Free Brochure On Modular Bathrooms For Marine Use page: 6
- Gladding-Hearn Shipbuilding To Build Large, Fast Passenger Catamarans On The East Coast page: 6
- Free Literature Describes New Repair Compounds From Philadelphia Resins page: 6
- ODECO Elects Kilpatrick Executive Vice President page: 6
- Avondale Yard Awarded $300-Million Navy Contract To Build Two More LSDs page: 7
- PROPULSION UPDATE First U.S.-Built Twin-Screw Towmaster Rudder System On Tug page: 7
- Combustion Engineering A w a r d e d $12 Million In Navy Boiler Contracts page: 7
- Huthnance Consolidates Management Of Nine Offshore Drilling Rigs page: 7
- Hagglunds Offers Elaborate 72-Page Full-Color Booklet On Cranes And Equipment page: 7
- M.A.N.-GHH Completes Floating Dock For Iran page: 8
- Navy Ends Suspension; Tracor, Inc., Resumes Government Contracting page: 8
- ' 85 Sales Of Imperial Survival Suits Nears 100,000 page: 8
- Aalborg Yard Launches Third Reefer For Delivery To USSR's Sudoimport page: 8
- Unique Sidewheeler Replica Craft Completed By Offshore Shipbuilding page: 9
- ABS Elects John Borum Senior Vice President page: 9
- OUTSTANDING INLAND/OFFSHORE VESSELS AND RIGS OF 1985 page: 12
- 38th Annual CSSRA Conference And First Canadian Shipbuilding & Offshore Exhibition page: 12
- $5-Billion Hibernia Offshore Project Will Get Under Way Early This Year page: 13
- Major Manufacturers Attend First Diesel Propulsion Conference Held In Seat page: 14
- Roger Nejes Appointed Assistant To President, Todd Shipyards Corp. page: 14
- Armco Continues To Upgrade Speciality Steels Facilities page: 14
- Westport Yard Building Fiberglass Passenger Vessel For TravAlaska page: 15
- Simrad, Inc. Opens U.S. East Coast Branch Office page: 15
- Balehi Marine Christens Twin-Screw Harbor Utility Boat page: 16
- Fast Sealift Ship USNS Altair Dedicated At Avondale Industries Shipyard Division page: 16
- Fincantieri Completes Major Overhauls On Two RO/RO-Containerships page: 17
- Shelley To Succeed Holmes As President Of Raytheon page: 17
- Ingersoll-Rand Purchases Fafnir Bearing Division page: 17
- McDermott Gets $48-Million Offshore Contract From Chinese Petroleum Corporation page: 18
- Pool Arctic Alaska Orders Bardex Hydranautics Island Rig Skidding System page: 18
- Bay Shipbuilding Lays Keel For Second Of Three Containerships page: 18
- Omnithrusters Delivered For Canadian Government Vessels page: 18
- Ingram Barge Completes Organization Changes— Reports Rapid G r o w th page: 19
- Optimizing Efficiency Levels Of Boiler Feed Turbo Pumps page: 20
- Russellstoll Offers Full-Color Bulletin On Heliport Lighting System page: 20
- Nichols Brothers Delivering Catamaran To Glacier Bay Yachts page: 21
- Simultaneous Drydocking Requires Separation Of 70,000-Ton Drydock At Penn Ship page: 21
- REDUCING FUEL COSTS page: 24
- OUTSTANDING CONVERSIONS page: 25
- B&R Offers Literature On Company Services, Products And Programs page: 27
- Joseph A. Watters Appointed President, Royal Viking Line page: 27
- BP Offers 60-Page Brochure On Facilities/Capabilities page: 28
- Farboil Offers Two Free Directories On Marine Coatings and Systems page: 28
- Todd Galveston Awarded $21.6-Million Modification Of Second T-AVB Vessel page: 28
- PNOC Marine And Bardex Hydranautics Build World Class Shipyard page: 29
- Gems Sensors Expands Line Of Level Indicators page: 29
- White Named Senior Vice President At American Systems Engineering page: 29
- 1986 DIESEL ENGINE GUIDE page: 30
- Karl Senner Offers Sales And Service For Reintjes Marine Gears page: 30
- DDA Offers Expanded Product Line And Streamlined Manufacturing Facilities page: 30
- Steamship Company Chief Given Top Federal Academy Alumni A w a rd page: 31
- New Marine Overcoat Sea-Slide™ Increases Speed, Saves Fuel page: 31
- Valley Line Reorganizes And Expands Marketing Department— Three N e w Executives Join Firm page: 31
- First Lucander-Designed Tug Nozzle Built By ideal Machine page: 31
- American Metal Bearing's Rubber Bearing Staves Approved By Navy page: 32
- Brochure Explains N e w USCG Survival Suit Regulations page: 32
- Saab Electronics Introduces TankRadar page: 33
- Alden Electronics Introduces Tactical Facsimile Receiver page: 33
- Furuno Introduces Digitized Small Radar page: 33
- Offshore Triple-Effect Water Makers From Atlas-Danmark Save Thousands In Operating Expenses page: 34
- Acoustical Barrier Material Data Sheet Available page: 34
- Robertshaw Literature Describes Versatile Diaphragm Actuators page: 34
- Gladding-Hearn Delivers Two Tugs To Bermuda's Department Of Marine page: 34
- Belgian Shipbuilder "Floats7 Massive GRP Mold On Film Of Air page: 36
- Navigation Sciences Offers VIEWNAV® Master Mariner Brochure page: 36
- Bailey Offers N e w Color Brochure On Recorders And Data Loggers page: 36
- Cummins Uprates B Series Marine Diesel Engines page: 38
- Titeflex Offers 22-Page Catalog On Smooth Bore Teflon Hose page: 38
- Cincinnati Gear Offers Free Color Brochure On Large Gears And Parts page: 38
- Baldt Offers New 12-Page Full-Color Facilities Brochure page: 38
- Texaco Marine Services Receives Ship Management Contracts page: 41
- Wilson Walton Sells Testing Services For Ships/Offshore Structures page: 41
- Eastern Marine Developing One Of Three Facilities As Offshore Supply Base page: 42
- Sulzer Introduces A Longer-Stroke Medium-Speed Engine page: 42
- Chesapeake Marine Engineering Symposium Set For January 24, 1986 page: 43
- N e w Compact Thermocoil Diesel Fuel Heater From Racor page: 43
- Marathon LeTourneau Reorganizes Marine And Offshore Operations page: 44
- Garlock Offers 44 Page Catalog On Sealing Devices page: 44
- Todd Awarded $33-Million Conversion By Matson Navigation page: 45
- McAllister Bros. Acquires Norfolk, Baltimore And Carolina Lines Assets page: 46
- Fine Metering Valves From Nupro Offer Improved Stability & Flow Control page: 47
- Sparrows Point Yard Wins Repair Contract For 'Energy Independence' page: 47
- The Federal Policy Vacuum: We Are Little Known And Less Understood page: 48
- InterTrade Awarded Navy Contract For Fenders page: 55
- Limitorque Introduces HR Series Line Of Pneumatic Valve Actuators page: 55
- The 93rd SNAME Annual Meeting— A Special Report page: 56
- New Company Formed, GCG Consultants page: 57
- Port Allen Marine Delivers Butadiene Tank Barge To Shell page: 66