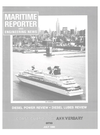
Essex Machine Works Delivers New Steel Propeller Shafts For Coast Guard's 'Eagle'
Essex Machine Works, Inc., Essex, Conn., recently delivered new forged steel propeller shafts for America's Tall Ship, the barque Eagle, to the Coast Guard base at Governor's Island, N.Y.
According to Wilson W. Cross, president of Essex Machine Works, Inc., a new shaft will be installed on the Eagle when she is hauled out for her normal refit later this year.
When not under sail, the 295- foot-long Eagle, which serves Coast Guard Academy instructors and cadets as a seagoing classroom, utilizes her 16-cylinder, 1,000-hp Caterpillar diesel engine to drive her at about 10 knots. Turning an eightfoot- diameter propeller, her new shaft is almost nine inches in diameter, over 20 feet long and weighs 1.8 tons. Her new shaft will replace what is believed to be one installed more than 50 years ago at her launching.
The Eagle bears a name that goes back to the early history of the United States' oldest continuous seagoing service. The first Eagle was commissioned in 1792, just two years after the formation of the Revenue Marine, forerunner of the Coast Guard.
The present Eagle, the seventh in a long line of vessels to bear the name, was built as the German naval training vessel Horst Wessel in 1936 by the Blohm + Voss Shipyard in Hamburg, Germany. In May 1946, she was taken as a war prize by the U.S. and commissioned into the U.S. Coast Guard as the Eagle.
In making the decision to award the contract for the new shafts, the Coast Guard was seeking a supplier with not only the right machining skills and cost efficiency, but also with the practical understanding of marine propulsion systems that would be required to bridge the half-century change from the ways of the pre-WWII German Navy to present-day needs of a demanding— but safe and efficient—cadet training ship.
Essex Machine has completed the work machining the shafts (one for installation and one for stand-by spare). The surfaces of the shafts were also coated with fiberglass and epoxy to protect them from saltwater corrosion.
The original drawings in German, as produced by the Blohm + Voss designers 54 years ago, were translated and redrawn to current standards by Drew Dickson, sales engineer at Essex Machine, and Robert M. Wilkinson, a consulting naval architect on the project.
The entire manufacturing process, which included shaft fabrication, fitting of wear-resistant bronze sleeves, and machinng of one-footdiameter bronze propeller nuts, was completed at the Essex Machine work shop in Essex.
For free literature on the machining services of Essex Machine Works, C i r c l e 8 8 o n Reader S e r v i c e C a rd
Read Essex Machine Works Delivers New Steel Propeller Shafts For Coast Guard's 'Eagle' in Pdf, Flash or Html5 edition of July 1990 Maritime Reporter
Other stories from July 1990 issue
Content
- Wartsila Diesel Announces Executive Appointments page: 10
- Chandris Celebrity's 'Horizon/ Built By Meyer Werft, Makes Her New York Debut page: 11
- Furuno Introduces New Autopilot, Compact, Lightweight Gyrocompass, And 10-Inch Color Video Sounder page: 11
- Radio Holland's Datamation: A Complete Integrated Ship Management System page: 13
- McDermott Awarded $27-Million Exxon Contract For Offshore Platform page: 13
- Avondale To Bid On Construction Of World's Largest Passenger Ship page: 14
- Singmarine Wins $16 Million Contract For New Chemical Tanker page: 15
- Hamilton Introduces Advanced Water Jet For Wide Range Of Vessels page: 16
- Halter Marine To Convert Supply Vessel For EPA Under $4.2-Million Pact page: 18
- Magnavox Introduces New Integrated GPS/Transit Satellite Navigation System page: 18
- Leevac Shipyards A w a r d ed Supply Boat Contract page: 19
- DIESEL POWER REVIEW page: 20
- MARINE LUBRICANTS page: 28
- U.S. Coast Guard Celebrates 200 Years Of Service page: 33
- Our Third Century page: 34
- Overview Of Coast Guard's Fiscal Year 1991 Request page: 36
- Willard Marine Continues Work With U.S. Coast Guard; Introduces SOLAS-Approved 18-Foot RIB page: 42
- Bollinger Receives $73.4-Million Modification To Build USCG Patrol Boats page: 42
- Morgan Crane Receives Order For Knucklebooms For Three Corvettes page: 43
- New Navy Report Outlines Potential Submarine Threat From Third World Nations page: 44
- US Navy Homeports Select Seaward Marine Fenders page: 44
- NORSHIPCO Completes Conversion of Crane Ship (T-ACS 9) For Navy page: 45
- Tano Marine Named Single System Vendor For T-AGS 45 page: 45
- Marinette Marine Launches Its Third MCM Vessel USS Patriot (MCM-7) page: 46
- Essex Machine Works Delivers New Steel Propeller Shafts For Coast Guard's 'Eagle' page: 48
- Viking Seminar Updates Skills of Service Representatives page: 48
- Global Marine Group Changes Company Name To GMG Systems, Inc. page: 53
- Robert Allan-Designed Hydrographic Survey Vessel Delivered By Allied Shipbuilders page: 54
- Aluminum Boats Constructing 140-Foot Dinner Yacht For Chicago page: 54
- Bender Awarded $3-Million Contract For Drill Rig Repair page: 55
- Cummins Diesels Power Cruise Vessel 'America' Delivered By Marine Builders page: 56
- ZF Introduces New Series Of Economical High-Horsepower Marine Transmissions page: 56
- $13-Million, Five-Boat Contract Completed By Moss Point Marine With Delivery Of Tugs To Jordan page: 58
- Deutz MWM Diesels To Power Four Harbor Tugs For Mexico page: 58
- Atlantic Marine Awarded $12.6-Million Contract To Build Three Sternwheel Dinner Vessels page: 59
- ABB Marine To Supply $50-Million Power Package To Fincantieri page: 59
- Blount Marine Delivers 192-Foot Dinner/Excursion Boat M / V Spirit Of Boston page: 60
- Canadian Government Report And New U.S. NOAA Administrator Publish Strong Swath Endorsements page: 61
- Master Marine Completes Repair, Maintenance On USCG Island Class Patrol Boats page: 62
- Trinity Marine To Build Three 220-Foot Supply Boats Under $15-Million Contract page: 62
- MTU-Powered High-Speed Catamaran, Built To New Flying Cat Design, Delivered By Kvaerner Fjellstrand page: 63
- COMSAT Expands Its Mobile Communications To New Ocean Region page: 63
- New Paint Factory For Sigma In Amsterdam page: 64
- Allied-Signal 'Spectra Shield' Panels For Marine Vessels Offer Maximum Ballistic Protection page: 64
- Textron Marine Systems Wins $6.5-Million Contract To Build Two SES Fireboats page: 65
- Congressional Conferees Near Compromise On Double-Hull Tanker Phase-In page: 66
- New Literature Available On Coffin Mechanical Seals For Turbo Pumps page: 67
- ABB Offers Eight-Page, Full-Color Brochure On Turbochargers page: 68
- Marco Shipyard Christens Fourth North Pacific Freezer Longliner page: 68
- Versatile Pacific Shipyards Uses N e w Launching Technique For Hydrographic Survey Ship page: 69
- L&C Associates Completes Deactivation Of M / V Cape Inscription page: 70