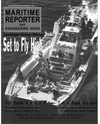
Autostructure - For Ease In The Creation Of Internal Strucutres
In June 2000, Autoship Systems Corporation of Vancouver, Canada launched Autostructure, its new internal structural design program.
Autostructure is used to create a 3-D model of a vessel structure and to output the parts of that model in CAD format. The CAD representation can be used to either prepare construction drawings or for input to NC cutting processors. Autostructure utilizes an Autoship-generated hull and/or superstructure and can also include the shell plate information created in Autoplate. (Autoship and Autoplate are programs from Autoship Systems.) Every aspect of Autostructure was designed to allow parts to be created quickly and with minimal input. While there is a general workflow, no set ways or sequences are forced upon the user, thus enabling maximum productivity with minimum effort. And since parts can be generated rapidly, mistakes can be quickly and easily remedied. Also, if a part is changed or moved, Autostructure can update the surrounding structure for you, saving you time and effort.
The tools that Autostructure provides are: • A part database with a powerful categorization system • The ability to rapidly cut parts to the shell and/or each other • Sophisticated 2-D part editing • Comprehensive CAD output • Extensive reporting capabilities • A user-expandable Material library Autostructure is built on top of SQL7 - Microsoft's most powerful database system. As delivered, Autostructure can support up to five users either in a client-server or peer-to-peer network. For more than five users, a full SQL7 system should be purchased separately. Autostructure allows the user to set up a hierarchical system to organize the model. Three examples are: i) by actual structure i.e.
ring/block/module/subassembly; or ii) by designer: each designer could be assigned his/her own, separate assembly, which could be further subdivided, and would be able access the other designer's work; or iii) by material: for a repair job, the user might want to group individual parts by material type, i.e.
material/size/profile/grade. Also, for each project, Autostructure provides the user with the ability to set up a Permissions scheme that controls which operations each designer is permitted to perform.
Autostructure provides several different methods for creating parts. Autostructure also includes special tools that speed up the part-making process, such as the ability to rapidly copy the details (stiffeners, cutouts, openings and markings) from one part to another or to quickly subdivide a large part into the separate plates from which it would be constructed.
Additionally, each time a part is trimmed at the hull or another part, a weld path is automatically created along the trimmed edge. The weld paths can be used to generate weld relief cutouts on other parts and can be included in weight and scheduling reports.
Autostructure uses AutoCAD 2000 for all 2-D editing functions. Special tools allow the user to easily attach and edit stiffeners, swiftly generate openings, stiffener cutouts and markings and also to perform boolean operations. Of course, all the usual Auto- CAD functionality is available as well.
All CAD output is automatically placed into Auto- CAD as an AutoCAD drawing. Three different formats are available: i) a 2-D array of selected part outlines with cutouts and markings, i.e. the typical information which would be sent to an NC-cutting processor and/or nesting program; ii) a 2-D presentation of parts, such as a cross section which would be used to prepare construction drawings; and iii) 3-D output to use for 3-D drawings to show the relationship of parts, or crucial construction details. Extensive control is provided for output, such as layer creation, size and 'thickness' of cross-section and type of stiffener marking.
Autostructure can generate many different reports, such as Weights and Centers, Bill Of Materials and Weld reports. The output is sent to Crystal Reports, which allows the presentation to be completely customized with minimum effort. Optionally, hull plate information created in Autoplate can be added to the Autostructure model and then included in reports, i.e. a center of gravity report for a sub-assembly can include the weight and centre of the shell plates, thus allowing the user to prepare a proper lifting arrangement for the structure.
Autostructure maintains a library of materials that includes material type, plate thickness, extrusions (stiffener profiles), flat bars and finishes (for rendering purposes). As each part the user creates is assigned properties from the library, consistency of material for all parts is guaranteed.
Circle 48 on Reader Service Card
Read Autostructure - For Ease In The Creation Of Internal Strucutres in Pdf, Flash or Html5 edition of January 2001 Maritime Reporter
Other stories from January 2001 issue
Content
- Innovation on the Irish Sea page: 8
- Genoese Regeneration page: 8
- Coast Guard Announces Marine Casually Reporting Requirements page: 9
- $29.9M Approved For U.S. Shipbuilding Loan Guarantees page: 9
- Southern Hospitality page: 10
- Incat Signs Deal With Bollinger page: 10
- Image Marine Delivers Cruise Catamaran for Private Operation page: 14
- Spain Creates Joint European Company page: 15
- Crowley To Acquire MTC page: 15
- Cammell Laird Awaits Costa Crociere Decision page: 16
- Wartsila Puts More Sulzer RTA84T's On Large Tankers page: 17
- NASSCO Lands $68 Million Continuous Maintenance page: 18
- Northrop Grumman To Acquire Litton Industries For $5.IB page: 20
- Finnlines Consolidates, Announces Appointments page: 21
- Svenska Skum Equipment On New Fireboats page: 22
- Eastern Shipbuilding Delivers Newest OSV page: 23
- Ayton Cross Arrives To Boost Wijsmuller Marine's Fleet page: 24
- USS Roosevelt Is Commissioned At Mayport page: 24
- Blount-Barker Shipbuilding Formed page: 26
- New N.C. Ferry-Linked Water Monitoring Generates Data page: 28
- Largest Aquastrada High Speed Ferry Under Construction At Rodriquez page: 29
- Passenger Vessel page: 31
- International Appeal With Local Customer Service Feel page: 33
- German Dry Cargo Division Breaks Into Super Yachts page: 35
- 3-D Modeling For Small And Large Vessel Construction page: 36
- Autostructure - For Ease In The Creation Of Internal Strucutres page: 38
- Proteus Adds Weight Estimating to FlagShip Suite page: 38
- Onstream Project To Optimize FPSO Design page: 40
- Napa Oy Introduces NAPA Steel System For Ship Design page: 40
- EnSolve Biosystems1 Senior Scientist Receives Top Honor page: 41
- The Doctor Is "In" page: 42
- The Natural Order page: 44
- Wartsila Fits First "Smokeless" Diesel page: 50
- Aloha Kittiwake - USCG Welcomes Bollinger-Built Patrol Boats page: 51
- 71 Countries Make IMO's Initial STCW White List page: 53
- NORSHIPCO Receives Enviro Honor page: 53
- New Executive Appointments ATROCL page: 54
- SJS Selected To Build Panama Canal Tugs page: 55
- Halter Marine Awarded $69M Option For Car Carrier page: 55
- Alstom Integrated Controls For Clough Offshore page: 56
- Transas Engine Room Simulators Offer Enhanced Capabilities page: 56
- Boatracs Launches VComm IP page: 57
- Litton European Unit Advances IB Concept For Workboats page: 58