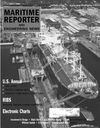
Shipbuilding R&D Supported
The National Shipbuilding Research Program Advanced Shipbuilding Enterprise (NSRP ASE) announced last month the selection of four new research projects as part of the Navy/Industry cofunded portfolio of 33 projects. The four new projects are valued at $10.3M, including industry cost share. A brief description of each project with a list of participants and funding follows: Project:A Lean Enterprise Model for U.S. Ship Construction, Overhaul, & Repair Participants: Atlantic Marine Holding Co., Todd Pacific Shipyards, Bath Iron Works, Puget Sound Naval Shipyard, and five others.
Funding: 3.8M NSRP ASE, $3.8M industry cost share.
Description: The principal objective of this project is to complete a comprehensive model for the application of lean manufacturing concepts to multiple market segments of the U.S. shipbuilding and repair industry. The enterprise-wide model will address lean design, materials, and manufacturing practices. It is anticipated that this model will result in a 20+ percent improvement in overall productivity within 36 months. The project focuses on implementation of world-class shipbuilding and lean enterprise practices in seven U.S.
shipyards covering four key market segments with the scope of full or partial implementation in the participating shipyards.
Project: Development and Commercialization of Laser Assisted Oxygen Cutting Participants: Bender Shipbuilding and Repair, Caterpillar, BOC Gases, Alabama Laser, and Electric Boat.
Funding: $672K NSRP ASE, $672K industry cost share.
Description: The project team will develop and exploit an experimental technology for laser assisted oxygen cutting of thick section (> .25-inch) steel plates which is currently in a laboratory stage of development at BOC Gases. The technology will greatly enhance U.S. shipbuilders' ability to accurately and cleanly cut thicksection steel, possibly greater than 100 mm, without increasing laser power output beyond 6kW. The potential exists for clean and accurate cut edges in both a square and bevel configuration, with minimal secondary part processing after removal from the laser-burning table. The project will provide near term benefits to both Bender Shipbuilding and Repair and Electric Boat, with both cost and quality improvements in ship and submarine construction. Through commercialization and technology transfer, the project will also provide additional impetus for other U.S. shipbuilders to invest in laser-cutting technology, which has demonstrated significant benefits at Bender Shipbuilding and Repair.
Project: Harvest: Finishing the Ship Product Models Participants: STEP Tools, Electric Boat, and Product Data Services.
Funding: $318K NSRP ASE, $376 industry cost share.
Description: The Harvest project seeks to complete the international standardization of the shipbuilding STEP Application Protocols: AP-218 (Ship Structures), AP-216 (Ship Molded Forms), and AP-215 (Ship Arrangements).
This entails the working groups and the editing of the standards documents.
Completion of the STEP Shipbuilding Application Protocols will allow the U.S. shipbuilding industry (and the Navy) to "harvest" the investment it has made in the development of product models for ships. In the final rounds of approval, the primary goal is to ensure the viability and completeness of the standard. This includes validation of information requirements, implementation considerations and harmonization with other STEP and related standards.
These models will give the shipbuilding industries new options for collaboration, for transferring data between different systems and different versions of the same system, and for managing data across the product life cycle.
Project: Enhancement of Evolution of STEP Participants: Kvaerner Philadelphia Shipyard and Sener Funding: $390K NSRP ASE, $398K industry cost share.
Description: The objective of this proposal is to broaden industry participation in the ongoing Evolution of STEP (ESTEP) task of the ISE project.
Specifically, this project would provide commercial translators for another CAD vendor (Sener and their FORAN product) for the three primary shipbuilding application protocols (structures, piping, and hull forms). FORAN is used by Atlantic Marine Holding Co., Friede Goldman Halter, and Kvaerner Philadelphia at the current time. The problem being addressed by ESTEP is the capability to transfer data from one ship product model to another (CAD-to- CAD Interoperability). ESTEP will help enable shipyards with different ship design programs to exchange information easily and quickly.
Read Shipbuilding R&D Supported in Pdf, Flash or Html5 edition of August 2001 Maritime Reporter
Other stories from August 2001 issue
Content
- First Wove Marine Files Reorganization Plan page: 36A
- Danish Contingent Strong At OE2001 page: 36C
- Containership Volume To Slow page: 36D
- Hempel Celebrates 50 Years page: 36G
- SSPC 2001 Set For November in Atlanta page: 36E
- Janet M. McAllister Welcomed To NY page: 4
- Reefership Within A Containership page: 8
- Innovation on the fjords page: 9
- Shipping Internet: Where next? page: 12
- Mahachai Dockyard: Freezers for Southern Waters page: 14
- Rodriquez Cantieri Navali Delivers Newest Fast Ferry page: 14
- Elliott Bay Develops Eco-Tourism Vessel page: 15
- Bollinger Delivers 145-ft. Supply/Utility Boat To Bordelon page: 16
- Gladding-Hearn Delivers Cape Fear Pilot Boat page: 18
- Shipbuilding R&D Supported page: 19
- Top Navy Officer Supports DD-21 page: 21
- Bollinger Incat USA - Marking Its Territory page: 24
- Ready to Burn: Fast Ferry Market Looks Good page: 27
- Palmer Johnson Teams Up With Atlantic Dry Dock For SuperYacht Refit Facility page: 29
- U.S. Report America's Cruise Line Faces Delivery Delays, Job Cuts page: 30
- USN Confident Of Raising Sunken Fishing Vessel page: 31
- Detyens Concludes Largest U.S. Conversion page: 32
- IZAR Lands FPSO Order page: 35
- ABB's Compact Pod Makes Mark In $42M Deal page: 35
- Offshore Inland: Poised To Pounce On Offshore Upturn page: 36
- Izar Ferrol Repairs Eight Vessels At Once page: 38
- Loose Cable Contributed To Crane Collapse page: 40
- Raising the Standard for Bulk Carrier Cranes page: 41
- Belotti Handling Reinvents The Reach Stacker Machine page: 41
- Chartco: The Best of Both Worlds page: 42
- U.S. ENC Availability Starts To Gain Speed page: 42
- Kelvin Hughes Bridge Chosen For Queen Mary 2 page: 45
- Raytheon To Supply T45 With IBS, Nav Package page: 46
- RIB Technology Makes Stronger, Faster Boats page: 49
- Zodiac: From Flying Machines to RIBs page: 51
- Willard Marine, MetalCraft Inc. Launch Hybrid Aluminum/FRP RIB page: 52
- Type 45 Destroyer Build Plans Modified page: 53
- UK Manufacturers Seek To Forge New Partnerships page: 54