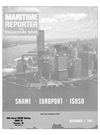
Fuel Conservation And Upgrading Of The Shipboard Boiler Plant
Most operators are not aware that just by operating their boilers within their design criteria, they can save 1.8 percent of their fuel costs. This fact was established by one owner over six years ago. Vessels operating under the U.S. flag today were, for the most part, designed and built in an era long before the present fuel crunch. They were, therefore, not designed with high fuel efficiency in mind. However, even on these vessels fuel rates can be improved and in some cases surpass their original designated rates.
To accomplish this, a thorough survey of the boiler is required, paying particular attention to refractory ; burner throats, angles and dimensions; water sides to insure that no deposits are present ; furnace-side-pressure parts are clean; external surface of steam air heaters for non-fouling; calibration and replacement of instrumentation; overhaul of s o o t - b l o w i n g equipment, and tightness check of all valves.
Combustion controls should be serviced and adjusted. This is an item that is frequently ignored and it should not be as excess air accounts for most of the heat loss up the stack.
Good instrumentation to monitor air and flue-gas pressure drops and stack temperature should be installed. Stack temperature is extremely important as it is an indication of your boiler efficiency. Most of the older vessels do not have flue-gas analyzing equipment. Therefore, an electronic flue-gas analyzer, preferably with chart recorders, should be installed. This expense is justified by savings experienced from better surveillance and control.
Most of the older plants were designed for 15 percent excess air operational. This can be improved at a relatively low cost. In some cases, it is possible to reduce it to 10 percent with a corresponding improvement in performance and maintenance. Fuel quality is most often blamed for boiler fouling problems. However, fuel quality is only one of the contributing factors. There are many documented cases where chronic boiler fouling problems have been eliminated by improving combustion, without any change in fuel quality.
Minimizing combustion air saves fuel, not only by increasing flame temperature, but also by minimizing boiler-tube fouling and refractory slagging. In addition, the decrease in dioxide content retards the corrosion rate of furnace-side metals. The evidence on boilers operating at 5 percent excess air as compared to 15 percent excess air is quite dramatic. Units on 5 percent have operated for periods of two years with no water washing of firesides as compared to a cleaning cycle of three to six months for units on 15 percent.
With fuel conservation and reduced fuel cost in mind, many owners have decided to run their vessels at reduced speed. The boiler designers should be consulted and their recommendations solicited prior to attempting this type of operation. Operation of the boilers at reduced loads can lead to accelerated deterioration and an increase in maintenance costs. If it is anticipated that reduced load operation is to be a long-term condition, it may be possible to modify the boilers and auxiliary equipment for optimum performance at that load. Should a reduction of 50 percent be in consideration, it is recommended that one boiler operation be utilized.
Modifications In upgrading a boiler plant, we must recognize that more emphasis is being put on the refineries to obtain higher quantities of distillates from a given barrel of crude, resulting in a degradation of the bunker fuels used by the majority of our merchant vessels.
It has long been recognized that sulfur, vanadium and sodium are the chief constituents of a fuel oil which contribute to operation difficulties. Special consideration must, therefore, be given to compensate for these degraded fuels. One area of major concern is the economizer.
High sulfur fuels tend to promote dewpoint corrosion and fouling in the economizer tube-bank area. This problem has been dealt with in the past and material design changes have been made to aid in combating the "cold-end corrosion." If the feedwater heating arrangement is such that the feed temperature is below 280 °F, provision should be made to raise it to this level to aid in avoiding dewpoint corrosion. In the economizer, the use of "Corten" or low-alloy steel fins and low-alloy tubes in place of carbon steel will give improved dewpoint corrosion resistance. By using cast-iron gill rings in the top 20 percent of the economizer, the problem of sulfuric acid attack may be minimized.
In this continuing battle of the fuel rate, we have recently examined the possibilities of upgrading an existing 24,000-shp tanker plant. This plant has the standard three feedwater heater economizer cycle operating at 850 psig, 930 F superheat. By adding equipment and incorporating features shown on the heat balance in Figure 1, it is estimated that a 4 percent savings in the fuel rate can be achieved.
These changes encompass the addition of a secondary economizer, one 1-p heater, one h-p heater, replacing steam air ejectors with vacuum pumps, modifying feed-pump turbines to operate on superheated steam, added extraction from h-p turbine, cascading drain system and increasing superheat temperature from 930 F to 950 F. If the vessel were on a long run, such as Persian Gulf to the U.S. or Europe, an attached generator could be included at minimal expense, resulting in an additional savings of 1 percent in the fuel rate.
Another method of plant upgrading presently under consideration is that of modifying an existing nonreheat to reheat. A complete change out of boilers does not appear to be economically feasible. However, adding a reheater section to the existing plant does.
One approach to this concept is to install the reheater in a refractory lined box that is separately fired by a combuster, as is done in separately fired heat recovery applications. This arrangement simplifies reheat control requirements and does not interfere with the normal operating functions of the main boilers.
It is estimated that this modification would result in a 4 percent fuel savings on a plant of approximately 30,000 shp.
Coal Firing In today's environment no upgrading evaluation would be complete unless consideration was given to coal firing. By the year 2000 it is projected that fuel-oil costs will be exorbitant. One owner's representative recently made the statement that the biggest problem facing U.S.-flag carriers is that of the costly conversion from steam turbine to dieselpowered ships. If the projections as indicated are correct, it would appear that he is heading in the wrong direction. The conversions he speaks of are reported to be in the area of 15 to 20 million dollars per ship. This is a sizable investment when you are looking for a quick payback on your outlay.
I believe the advantages of converting to coal, even when you consider that reboilering is required, far outweigh the diesel conversion approach.
On coal firing, history points out that this is not something which is new; we are simply improving on existing technology.
Major improvements have been made in the last 30 years in metallurgy, design and manufacturing techniques used in modern marine boilers, as well as the fuelburning fuel-handling systems employed.
The coal-fired marine plant will utilize a readily available and economical stoker coal. Present day prices, February 1981, place stoker grade coal at $2,201 per million Btu versus oil at $5.20 per million Btu. The prices based on dollars per million Btu equate to $212 per ton for bunker "C" oil and $55 per ton for stoker-grade coal.
The economics, based on a 20,- 000-shp plant operating 300 days a year at rated power, show that the oil-fired plant consumes 173.75 million Btu per hour. This t r a n s l a t e s into $6,505,200 per year. The coal-fired plant would consume 180.00 million Btu per hour, which represents an annual cost of $2,851,200. Thus, the fuel cost savings by using coal would be $3,654,000 per year.
The added cost for the coalfired plant with coal bunkers, fuel and ash handling equipment is estimated at $3,000,000 per ship above that of an oil-fired steamship. Obviously, any investment that can be written off in less than four years is well worth investigating.
The classification of coal under consideration for marine application today is stoker-grade bituminous, which is still available in numerous areas of the United States and the world for marine bunkers.
A present-day land coal-fired boiler generally consists of a combustion system which burns pulverized coal in suspension in the furnace, or s t o k e r - f i r e d units which burn coal on a fixed or moving grate system. Coal-fired utility boilers generally use pulverized coal systems simply because a stoker cannot accommodate the huge quantities of fuel consumed.
Coal pulverizers and the burner system are generally designed for a specific coal. This does not present a problem for land-based plants. Marine bunkering coals, however, will vary in specifications and may not be acceptable to a pulverizer system as originally designed.
We, therefore, feel that a stoker- fired boiler is the best presentday solution for coal firing aboard a vessel. The stoker will more readily accept changes in the fuel specification which are likely to occur in marine coal bunkers.
The main shipboard coal bunkers proposed are of the hopperbottom type. Transportation of the coal from the extraction point at the main bunker to the day bunker can employ one of two basic systems available. One system is mechanical and the second is a pneumatic transport system.
The mechanical coal feed system configuration can vary depending on the machinery space layout.
It is estimated that a reboilering conversion to coal-firing units would be in the five to seven million dollar range. This includes removal of existing boilers, installation of all new equipment, plus an insert into the hull structure for coal bunkers.
In conclusion, in a world which is subject to liquid fuel prices rising uncontrollably and with rapid degradation of liquid fuel, coal is a viable alternate for shipboard application.
For free copies of the full paper, Write 99 on Reader Service Card
Read Fuel Conservation And Upgrading Of The Shipboard Boiler Plant in Pdf, Flash or Html5 edition of November 1981 Maritime Reporter
Other stories from November 1981 issue
Content
- Appoint Daniel Rogers Marketing Manager At Zidell's Marine Division page: 6
- Color Brochures Describe Riverway Shipyard Facilities And Products page: 6
- Title XI Approved For $43-Million Conversion Of Four MorMac Ships page: 6
- NSL Expands Container Capacity Of Ro/Ro Ships page: 7
- Elect Gardner Chairman Of Jacksonville Port Authority page: 7
- Nav-Com Moves To New Facility page: 8
- Issue Call For Papers For SNAME Ship Costs & Energy Symposium page: 8
- Paceco Moves Headquarters To New Gulfport, Miss., Plant page: 9
- Adm. Harold E. Shear Sworn-ln As Maritime Administrator page: 9
- 89th SNAME Annual Meeting page: 10
- President Reagan And Sponsor Authenticate Keel Of 'Yorktown' At Ingalls page: 10
- Marathon Launches Jackup Penrod 86 At Brownsville Yard page: 10
- Halter Delivers New Offshore Express Supply Boat page: 10
- New Compact Oil Water Separator From Sigma —Literature Available page: 10
- Seward, Alaska To Build Large Shipping Facility page: 11
- Inland Marine Delivers Towboat M/V Mike Schmaeng To Pott Industries page: 12
- Top Executive Changes Announced By Marco page: 13
- $30-Million Order Signed By Hongkong United Dockyards Ltd. page: 14
- Westinghouse Credit, Seafirst Leasing Provide Equity In Four- Towboat, 81-Barge Transaction page: 14
- SACM Publishes Brochure On Marine Diesel Engines —Copies Available page: 16
- Approve Application For $22 Million Title XI For Towboat, 68 Barges page: 16
- Literature Available From Marland On Inverto® Oil/Water Separator page: 16
- Publish New Brochure On End Entry Ball Valves From Zidell Explorations page: 18
- Appoint David Daniels National Sales Manager At M&T Chemicals page: 18
- McAllister Brothers Is New Name For Baker-Whiteley Towing page: 19
- IMM To Install New GE Turbine Package At Offshore Installation page: 19
- Study Notes Upsurge In Offshore Rig Orders —U.S. Yards In Lead page: 19
- HUDSHIP Delivers The M/V Charles Haun To Parker Towing Company page: 19
- Chemical Waste Incinerator Ships Discussed At SNAME Chesapeake Section page: 19
- Capt. Cunningham Named Financial Manager At USCG Yard, Curtis Bay page: 20
- Dedicate Computerized Management System For Port Terminals page: 20
- Port Of Portland Appoints European Representative page: 20
- Indonesia To Use Jetfoil In Naval, Commercial Roles page: 20
- Marathon Licensee To Build Third Jackup Rig page: 21
- UPSCO Appoints George Geyer VPResource Mgmt/Admin page: 21
- Northern Radio Announces New HF/SSB Transceiver- Literature Available page: 21
- Mobile Workover Unit Houtech II Christened At Beth Steel's Beaumont Yard page: 21
- Dome Petroleum Signs Agreement To Export LNG For Japanese Utilities page: 22
- Christen Jackup J. Storm XVII At Bethlehem Steel's Beaumont Yard page: 22
- Mississippi Marine Delivers M/V Redneck—Second Of Three Towboats For Captain Hollinger page: 22
- Award $1.6 Million To Sperry For Satellite Positioning System Work page: 23
- $11.8-Million Navy Contract Awarded General Ship For Overhaul Of USS Vulcan page: 23
- Ohio River Officials Meet With Representatives Of Finnish Coal Interests page: 25
- Butterworth To Exhibit At Marintec China '81 page: 25
- Mid-Coast To Build N&SA-Designed Voith Tractor Tug page: 26
- SNAME Los Angeles Holds First Meeting, Discusses Low Power Marine Steam Cycle page: 26
- Form New Repair Company To Service Mexican Gulf -Information Available page: 27
- NASSCO Delivers 'S/S Coast Range'— Second Of Three Carlsbad Class For Union page: 27
- Hitachi Zosen To Build Second Jackup For India page: 28
- BIW Executive Elected To Chair Repair Committee Of Shipbuilders Council page: 28
- Monark Boat Delivers Oil Recovery Vessel For Use On Lake Maracaibo page: 28
- Moss Point Marine Delivers Two Supply Vessels To Golden Gulf page: 28
- Name Michael Donelan Sales Manager For Inland Water Propulsion page: 29
- Dedicate New Container Terminal In Boston page: 29
- Imperial Oil Planning Semisub Drilling Rig With 6,000-Foot Capability page: 29
- Name Two Vice Presidents, Announce Appointments At Gulf Fleet Marine page: 30
- Free Encyclopedia And Technical Article On Anchoring From SeaTec page: 32
- Santa Fe International To Merge With Kuwait Petroleum Corp. page: 32
- Santander Shipyard To Increase Drydock Capacity To 25,000-Dwt page: 34
- Canadian Survey Shows 400 New Vessels Needed During Next Ten Years page: 34
- CP Propeller Order To Tacoma Boat/Escher Wyss For Alaska Patrol Vessel page: 35
- Ship Microcomputers Discussed At SNAME Northern California page: 36
- Aeroquip Introduces New Fire-Resistant Hose —Literature Available page: 36
- M. Rosenblatt Promotes Three To Company Officers page: 36
- NRC Releases Study Assessing The Safety Of OCS Offshore Oil page: 37
- Capt. Chao Awarded Medal Of Honor By St. John's University page: 37
- Levingston Launches The Ed Holt, First Of Two Jackups For Noble Drilling page: 38
- UPSCO Launches Hull Number 001 — A 120-Foot Tug For An ITB page: 38
- SNAME-Hawaii Discusses High-Speed Catamaran Hydrofoils page: 38
- Twelve Prominent Marine Industry Executives Are Elected Members Of ABS page: 40
- Alnor Instrument Publishes Brochure On New Engine Temperature Monitors page: 42
- Silver Knight Award For Carl R. Meurk Of Todd page: 43
- Publish Literature On Stern Tube Lubrication System From Waukesha page: 43
- Sudoimport Orders Jacket-Launching Barge From Blohm & Voss AG page: 44
- Mid-Coast Delivers The Clemente Guillen page: 45
- Literature Available On Satellite Services For Ships And Offshore Rigs page: 45
- Fuel Conservation And Upgrading Of The Shipboard Boiler Plant page: 46
- HUDSHIP To Build Two 176-Ft. Supply Vessels page: 51
- National Marine Completes Acquisition Of Riverways Ship Repair Facilities page: 52
- Chevron Develops New Delo 1000 Marine Oil —Literature Available page: 52
- Marine Fabricators Deliver First Of Two Supply Boats For Arrow Marine page: 53
- Four New Branch Managers Appointed At M. Rosenblatt page: 53
- Armco's New Wire Rope Offers Rotation Resistance —Literature Available page: 54
- New Pall Filter Medium For Hydraulic/Lube —Literature Available page: 56
- Omnipure Produces Five Waste Treatment Units —Literature Available page: 56
- New High-Pressure Pump Has Speeds To 20,000 RPM —Literature Available page: 57
- Burton Delivers 224-Ft. Seiner, Second Of Seven For Van Camp page: 58
- Second Wind-Assisted Diesel Propelled Ship Building In Japan page: 58
- Report On Laser Technology Made To ASNE Long-Beach-Greater L.A. Section page: 58
- Hitachi Zosen Delivers Car Carrier Toyofuji 7 page: 59
- Bayou Black Delivers All-Aluminum 'Frontier I' page: 59
- Three N e w Vice Presidents N a m e d At CDI M a r i n e Co. page: 60
- Two Lightships Ordered For A u s t r a l i a n Waters page: 60
- EUROPORT '81 page: 62
- Cat Announces N e w 1,200 R P M 3412 M a r i n e Engine —Brochure A v a i l a b le page: 86
- New Epoxy Coating From Devoe/Prufcoat —Literature Available page: 89
- Duraline Introduces New Portable Heaters, Blowers —Literature Available page: 89
- Two Ferries From Atlantic Marine For Service In Biscayne Bay page: 90
- SNAME San Diego Section Hears Paper On Unmanned Submersibles page: 90
- Kockumation Names Three Agents In U.S. For Sales And Service page: 90
- MarAd Awards Grant To Develop Computerized Vessel Locator System page: 91
- ISOSO '81 page: 92
- $C11-Million Naval Order To Burrard Yarrows Corp page: 97
- Largest Containership To Be Built In U.S. Is Named President Lincoln page: 98
- Ore/Oil Carrier Purchased By Marine Transport Lines From Italian Company page: 98
- American Iron And Steel Institute Publishes Text On Corrosion Protection page: 99
- EPSCO And Datamarine Sign $1.6M OEM Agreement For Loran-C Receivers page: 99
- Blenkhorn Named A VP At Bath Iron Works page: 100
- Blume To Install Elinca System On 4 Sedco Rigs page: 100
- Navy Extends Use Of MARISAT Satellite Service An Additional Year page: 100
- Andrew A. Sallean Joins Bretagne ACB Corporation As Vice President page: 101
- Navy Awards EAC A Contract To Inspect Carrier Fleet Equipment page: 101
- Marconi Marine Awarded Eight-Ship Communications Equipment Contract page: 102
- Joint Venture Formed To Market Shipboard Computers For Loading page: 102
- ASNE Flagship Section Hears Admiral Beecher On Battleship Reactivation page: 107
- Philadelphia Resins Announces Expansion At Montgomeryville Plant page: 107
- Norcontrol Offers New Anti-Collision System —Literature Available page: 108
- COMSAT To Hold Marine Satellite Service Seminar In New York, December 1 page: 109
- Ohio River Terminal Renovation Increases Throughput By 75 Percent page: 110
- Roy Moffett Named To MarAd Operations Post page: 111
- Swedish Yard To Build $70-Million Tanker page: 111
- Barge-Mounted Polyethylene Plant Delivered To Site In Argentina page: 112
- Energy Freedom Widest Ever To Travel Through Welland Canal page: 113
- Electric Boat's Submarine Facilities Subject Of ASNE Section Presentation page: 113
- ABS Reports Record Number Of Vessels Under Classification page: 114
- Patti Industries Delivers Two Tugs, Receives Contracts For Two More page: 115
- SNAME-New York Honors Past Chairmen, Hears Paper On Hopper Dredge Design page: 131
- New Fuel Efficient Pctnamax Bulk Carrier Christened At Burmeister & Wain Shipyard page: 131
- Publish Brochure On Kockumation's Cargo Distribution Calculator page: 132
- Literature Available On New Electro-Nav EN-RTAG 2-Tone Alarm Generator page: 132