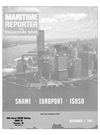
Ohio River Terminal Renovation Increases Throughput By 75 Percent
In June, 1981, Ohio River Company's Huntington, W.Va. coal transfer terminal began operating at a throughput of five million tons per year—up from an average of 3.5 million tons per year. The 75-percent-capacity increase was gained through a 19- month renovation project that was carried out with only V/-2 weeks downtime.
A conceptual feasibility study, completed in September 1978, served as the basis for the construction work, awarded to the Dravo Corporation, that began in November 1979. The conceptual study was undertaken by Soros Associates of New York City, who worked closely with the Ohio River Company to develop a scheme that was keyed to minimizing downtime, while addressing critical problem areas at the 52-year-old terminal. In addition to the design scheme, the study report also suggested new operating procedures, manpower requirements and operator duties necessary for realization of the significant throughput rate increase allowed by the new design.
An option for an improved design, which would allow for a further increase, was also included.
The original six-week downtime requirement projected in the study was reduced to l*/> weeks through the final construction plan proposed by the Ohio River Company.
Previous Limitations The Huntington Terminal yard averaged 75-85 coal cars dumped per eight-hour shift, with the maximum rate of 100 cars per shift, not sustainable due to yard congestion. The yard congestion was amplified by an average of 100 cars with special consignments awaiting assembly to a barge load.
The average total capacity for an eight-hour shift was further limited by the need to use a significant amount of time for car shifting. This procedure was mandated by the use of inside tracks for collecting empty cars, while outside tracks were used for loaded cars. To pull out empty cars, locomotives had to run through switches. This stopped the dumping operation.
Cars were taken to a bottomdump type pit for simultaneous, parallel dumping of two cars.
Problem-ridden car shakers, as well as damage to railroad cars and noise complaints from the community, were endured in an effort to speed coal discharge. In addition, the usual dump hoppers designed for 60-ton cars resulted in some spillage from present-day 100-ton cars.
One of the three coal conveyors was supported by a floating dock, which served as the barge loader. This arrangement required constant movement of barges to adjust to the river level, reducing operational efficiency, and also creating a significant maintenance burden.
Renovation Design The design scheme for renovation was developed to allow for an increase in dumping capacity, from 75-85 coal cars per shift, to Ohio River Company's objective of 150-160 cars per shift, while minimizing downtime.
The Ohio River Company asked Soros Associates to first review a previous renovation proposal based on the installation of a new, 80-foot-long bottom-dump pit.
The scheme allowed for dumping cars while they moved along a single track, with a system of hoist-mounted shakers utilized to increase the dumping rate.
Soros rejected this concept and proposed a rotary-type car dumper as a preferred alternative.
Soros also doubted the workability of a moving shaker system, and cited its high noise levels, longer periods required for coal thawing, expected damage to railroad cars, and probable significant contribution to downtime in the dumper area. As a result of these considerations, the rotarytvpe was accepted.
The project team considered several alternative new rail layout and operational schemes in an effort to gain maximum ad- vantage from the new dumper system.
The accepted scheme featured dividing the car storage yard into two sections, and e s t a b l i s h i ng two pull-out tracks and a distribution switch. These features, along with new operational procedures, provided for a continuous dumping operation in a given shift, eliminating the previous necessity for a three-hour stoppage for car shifting. The accepted scheme also called f o r leasing a d j a c e n t p r o p e r t y , easing yard congestion, and allowing for the delivery of strings of 25 loaded cars to the dumper at a time, up from 20 previously.
The accepted scheme also called for installation of a barge loading conveyor mounted on two 16- foot-diameter cells, and suspended via a hoist system to allow for adjustment to variations in the level of the river. This modification eliminated operational and m a i n t e n a n c e problems experienced with the previous floatingdock barge loader.
Other stories from November 1981 issue
Content
- Appoint Daniel Rogers Marketing Manager At Zidell's Marine Division page: 6
- Color Brochures Describe Riverway Shipyard Facilities And Products page: 6
- Title XI Approved For $43-Million Conversion Of Four MorMac Ships page: 6
- NSL Expands Container Capacity Of Ro/Ro Ships page: 7
- Elect Gardner Chairman Of Jacksonville Port Authority page: 7
- Nav-Com Moves To New Facility page: 8
- Issue Call For Papers For SNAME Ship Costs & Energy Symposium page: 8
- Paceco Moves Headquarters To New Gulfport, Miss., Plant page: 9
- Adm. Harold E. Shear Sworn-ln As Maritime Administrator page: 9
- 89th SNAME Annual Meeting page: 10
- President Reagan And Sponsor Authenticate Keel Of 'Yorktown' At Ingalls page: 10
- Marathon Launches Jackup Penrod 86 At Brownsville Yard page: 10
- Halter Delivers New Offshore Express Supply Boat page: 10
- New Compact Oil Water Separator From Sigma —Literature Available page: 10
- Seward, Alaska To Build Large Shipping Facility page: 11
- Inland Marine Delivers Towboat M/V Mike Schmaeng To Pott Industries page: 12
- Top Executive Changes Announced By Marco page: 13
- $30-Million Order Signed By Hongkong United Dockyards Ltd. page: 14
- Westinghouse Credit, Seafirst Leasing Provide Equity In Four- Towboat, 81-Barge Transaction page: 14
- SACM Publishes Brochure On Marine Diesel Engines —Copies Available page: 16
- Approve Application For $22 Million Title XI For Towboat, 68 Barges page: 16
- Literature Available From Marland On Inverto® Oil/Water Separator page: 16
- Publish New Brochure On End Entry Ball Valves From Zidell Explorations page: 18
- Appoint David Daniels National Sales Manager At M&T Chemicals page: 18
- McAllister Brothers Is New Name For Baker-Whiteley Towing page: 19
- IMM To Install New GE Turbine Package At Offshore Installation page: 19
- Study Notes Upsurge In Offshore Rig Orders —U.S. Yards In Lead page: 19
- HUDSHIP Delivers The M/V Charles Haun To Parker Towing Company page: 19
- Chemical Waste Incinerator Ships Discussed At SNAME Chesapeake Section page: 19
- Capt. Cunningham Named Financial Manager At USCG Yard, Curtis Bay page: 20
- Dedicate Computerized Management System For Port Terminals page: 20
- Port Of Portland Appoints European Representative page: 20
- Indonesia To Use Jetfoil In Naval, Commercial Roles page: 20
- Marathon Licensee To Build Third Jackup Rig page: 21
- UPSCO Appoints George Geyer VPResource Mgmt/Admin page: 21
- Northern Radio Announces New HF/SSB Transceiver- Literature Available page: 21
- Mobile Workover Unit Houtech II Christened At Beth Steel's Beaumont Yard page: 21
- Dome Petroleum Signs Agreement To Export LNG For Japanese Utilities page: 22
- Christen Jackup J. Storm XVII At Bethlehem Steel's Beaumont Yard page: 22
- Mississippi Marine Delivers M/V Redneck—Second Of Three Towboats For Captain Hollinger page: 22
- Award $1.6 Million To Sperry For Satellite Positioning System Work page: 23
- $11.8-Million Navy Contract Awarded General Ship For Overhaul Of USS Vulcan page: 23
- Ohio River Officials Meet With Representatives Of Finnish Coal Interests page: 25
- Butterworth To Exhibit At Marintec China '81 page: 25
- Mid-Coast To Build N&SA-Designed Voith Tractor Tug page: 26
- SNAME Los Angeles Holds First Meeting, Discusses Low Power Marine Steam Cycle page: 26
- Form New Repair Company To Service Mexican Gulf -Information Available page: 27
- NASSCO Delivers 'S/S Coast Range'— Second Of Three Carlsbad Class For Union page: 27
- Hitachi Zosen To Build Second Jackup For India page: 28
- BIW Executive Elected To Chair Repair Committee Of Shipbuilders Council page: 28
- Monark Boat Delivers Oil Recovery Vessel For Use On Lake Maracaibo page: 28
- Moss Point Marine Delivers Two Supply Vessels To Golden Gulf page: 28
- Name Michael Donelan Sales Manager For Inland Water Propulsion page: 29
- Dedicate New Container Terminal In Boston page: 29
- Imperial Oil Planning Semisub Drilling Rig With 6,000-Foot Capability page: 29
- Name Two Vice Presidents, Announce Appointments At Gulf Fleet Marine page: 30
- Free Encyclopedia And Technical Article On Anchoring From SeaTec page: 32
- Santa Fe International To Merge With Kuwait Petroleum Corp. page: 32
- Santander Shipyard To Increase Drydock Capacity To 25,000-Dwt page: 34
- Canadian Survey Shows 400 New Vessels Needed During Next Ten Years page: 34
- CP Propeller Order To Tacoma Boat/Escher Wyss For Alaska Patrol Vessel page: 35
- Ship Microcomputers Discussed At SNAME Northern California page: 36
- Aeroquip Introduces New Fire-Resistant Hose —Literature Available page: 36
- M. Rosenblatt Promotes Three To Company Officers page: 36
- NRC Releases Study Assessing The Safety Of OCS Offshore Oil page: 37
- Capt. Chao Awarded Medal Of Honor By St. John's University page: 37
- Levingston Launches The Ed Holt, First Of Two Jackups For Noble Drilling page: 38
- UPSCO Launches Hull Number 001 — A 120-Foot Tug For An ITB page: 38
- SNAME-Hawaii Discusses High-Speed Catamaran Hydrofoils page: 38
- Twelve Prominent Marine Industry Executives Are Elected Members Of ABS page: 40
- Alnor Instrument Publishes Brochure On New Engine Temperature Monitors page: 42
- Silver Knight Award For Carl R. Meurk Of Todd page: 43
- Publish Literature On Stern Tube Lubrication System From Waukesha page: 43
- Sudoimport Orders Jacket-Launching Barge From Blohm & Voss AG page: 44
- Mid-Coast Delivers The Clemente Guillen page: 45
- Literature Available On Satellite Services For Ships And Offshore Rigs page: 45
- Fuel Conservation And Upgrading Of The Shipboard Boiler Plant page: 46
- HUDSHIP To Build Two 176-Ft. Supply Vessels page: 51
- National Marine Completes Acquisition Of Riverways Ship Repair Facilities page: 52
- Chevron Develops New Delo 1000 Marine Oil —Literature Available page: 52
- Marine Fabricators Deliver First Of Two Supply Boats For Arrow Marine page: 53
- Four New Branch Managers Appointed At M. Rosenblatt page: 53
- Armco's New Wire Rope Offers Rotation Resistance —Literature Available page: 54
- New Pall Filter Medium For Hydraulic/Lube —Literature Available page: 56
- Omnipure Produces Five Waste Treatment Units —Literature Available page: 56
- New High-Pressure Pump Has Speeds To 20,000 RPM —Literature Available page: 57
- Burton Delivers 224-Ft. Seiner, Second Of Seven For Van Camp page: 58
- Second Wind-Assisted Diesel Propelled Ship Building In Japan page: 58
- Report On Laser Technology Made To ASNE Long-Beach-Greater L.A. Section page: 58
- Hitachi Zosen Delivers Car Carrier Toyofuji 7 page: 59
- Bayou Black Delivers All-Aluminum 'Frontier I' page: 59
- Three N e w Vice Presidents N a m e d At CDI M a r i n e Co. page: 60
- Two Lightships Ordered For A u s t r a l i a n Waters page: 60
- EUROPORT '81 page: 62
- Cat Announces N e w 1,200 R P M 3412 M a r i n e Engine —Brochure A v a i l a b le page: 86
- New Epoxy Coating From Devoe/Prufcoat —Literature Available page: 89
- Duraline Introduces New Portable Heaters, Blowers —Literature Available page: 89
- Two Ferries From Atlantic Marine For Service In Biscayne Bay page: 90
- SNAME San Diego Section Hears Paper On Unmanned Submersibles page: 90
- Kockumation Names Three Agents In U.S. For Sales And Service page: 90
- MarAd Awards Grant To Develop Computerized Vessel Locator System page: 91
- ISOSO '81 page: 92
- $C11-Million Naval Order To Burrard Yarrows Corp page: 97
- Largest Containership To Be Built In U.S. Is Named President Lincoln page: 98
- Ore/Oil Carrier Purchased By Marine Transport Lines From Italian Company page: 98
- American Iron And Steel Institute Publishes Text On Corrosion Protection page: 99
- EPSCO And Datamarine Sign $1.6M OEM Agreement For Loran-C Receivers page: 99
- Blenkhorn Named A VP At Bath Iron Works page: 100
- Blume To Install Elinca System On 4 Sedco Rigs page: 100
- Navy Extends Use Of MARISAT Satellite Service An Additional Year page: 100
- Andrew A. Sallean Joins Bretagne ACB Corporation As Vice President page: 101
- Navy Awards EAC A Contract To Inspect Carrier Fleet Equipment page: 101
- Marconi Marine Awarded Eight-Ship Communications Equipment Contract page: 102
- Joint Venture Formed To Market Shipboard Computers For Loading page: 102
- ASNE Flagship Section Hears Admiral Beecher On Battleship Reactivation page: 107
- Philadelphia Resins Announces Expansion At Montgomeryville Plant page: 107
- Norcontrol Offers New Anti-Collision System —Literature Available page: 108
- COMSAT To Hold Marine Satellite Service Seminar In New York, December 1 page: 109
- Ohio River Terminal Renovation Increases Throughput By 75 Percent page: 110
- Roy Moffett Named To MarAd Operations Post page: 111
- Swedish Yard To Build $70-Million Tanker page: 111
- Barge-Mounted Polyethylene Plant Delivered To Site In Argentina page: 112
- Energy Freedom Widest Ever To Travel Through Welland Canal page: 113
- Electric Boat's Submarine Facilities Subject Of ASNE Section Presentation page: 113
- ABS Reports Record Number Of Vessels Under Classification page: 114
- Patti Industries Delivers Two Tugs, Receives Contracts For Two More page: 115
- SNAME-New York Honors Past Chairmen, Hears Paper On Hopper Dredge Design page: 131
- New Fuel Efficient Pctnamax Bulk Carrier Christened At Burmeister & Wain Shipyard page: 131
- Publish Brochure On Kockumation's Cargo Distribution Calculator page: 132
- Literature Available On New Electro-Nav EN-RTAG 2-Tone Alarm Generator page: 132