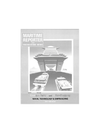
MWH Offers High-Quality, Inlet And Exhaust Valves For Marine Engine Applications
—Color Brochure Available— West Germany-based Markisches Werk Halver (MWH) has more than 50 years' experience in the design and production of high-quality inlet and exhaust valves. MWH offers a complete range of valves, valve cages, valve rotators, accessories and complete exhaust valve assemblies for diesel engines in ship propulsion and generator applications.
Two characteristics of the company's products are high quality and precision manufacturing, both of which result in a longer service life, lower maintenance costs and higher profitability for MWH customers.
Specially designed modifications and general improvements are constantly introduced by MWH engineers in an effort to increase costeffectiveness for the company's customers.
Examples of this, according to MWH, are its improvements in the area of cylinder heads for gas engines and in its development of Nimonic valves.
MWH reports that its bi-metal Nimonic valves have proven to be the best solution for heavy fuel operation use because they show better resistance against corrosion and high material strength at high temperatures.
MWH Nimonic valves have already been in use for over 20,000 running hours.
To protect against corrosion, MWH valves are chromed, nitrided, coated with Molybdenum or other special alloys. The company has developed special techniques to polish the valves so as to take account of all the special forces and gas flows to which the valves are exposed during operation.
Markisches Werk maintains strict manufacturing and production controls to ensure the quality of its products. These controls begin with the receipt of the raw materials.
Each shipment is checked against the requested nominal values. In case where these values are not achieved, the shipment is rejected.
During the manufacturing process, each worker checks and controls his own work. MWH reports that this system has proven to be a highly successful practice for maintaining quality standards.
In addition, MWH's modern process equipment ensures a quality product. Each piece is checked 100 percent before it is packed for shipment.
This checking includes, of course, crack testing by fluorescent penetrants.
Quality assurance is the direct responsibility of senior management as well as line management. This ensures tight control and underlines the importance given to quality assurance at MWH.
The company's new laser marking machine protects against imitation and also reduces cost.
MWH also has developed watercooled exhaust valve cages. The cooling water flows a few millimeters from the valve seat, substantially reducing temperature. Consequently, the service life of the valve spindle and valve cage are increased.
Another area where MWH's precision engineering is of particular importance is in the supply of complete valve assemblies. All components are specifically made to achieve the best match possible.
The company also offers a new valve cage reconditioning service.
The valve cages are first checked in order to determine if the repair is economically viable. Repair work is carried out at the company's facilities.
MWH can also supply reconditioned cages on an exchange basis.
For free color literature detailing the complete line of valves, valve cages, valve assemblies, etc., offered by MWH, C i r c l e 7 7 o n R e a d e r S e r v i c e C a rd
Read MWH Offers High-Quality, Inlet And Exhaust Valves For Marine Engine Applications in Pdf, Flash or Html5 edition of May 1989 Maritime Reporter
Other stories from May 1989 issue
Content
- NAPVO To Review Subchapter T Proposal page: 6
- Trinity Industries To Buy Bethlehem Steel's 74-Acre Beaumont, Texas, Facility page: 7
- Caterpillar Announces New Trademarks page: 7
- Comsat Maritime Services Publishes Cruise Ship SatCom Brochure page: 8
- CE&MCO Receives Order For Three Portainers From Maersk Container page: 8
- N.Y. Shipyard Drydocks 925-Passenger Cruise Ship page: 10
- MAN B&W Diesel To Takeover Sulzer's Diesel Activities page: 10
- BoatUFE Supplies Deck Caulking Compound For Cruise Ship Fantasy page: 11
- Port Canaveral Offers Homeport Development Package To 'Phoenix' Cruise Ship page: 11
- CRUISE + FERRY '89 page: 12
- THE EXPANDING CRUISE INDUSTRY—STILL MORE ROOM FOR GROWTH page: 14
- Construction Of First Of Two 70,000-GRT Cruise Ships Under Way At Fincantieri-Monfalcone Yard page: 17
- 70,000-GRT Superliner Takes Shape At Wartsila Marine's Turku Yard page: 18
- Nichols Bros/ Deutz MWM-Powered Ocean Catamaran Goes Into Service Between Nantucket And Boston page: 20
- Gladding-Hearn Building Another High-Speed INCAT Ferry page: 20
- Selecting Machinery For High-Powered Cruise Ships page: 21
- Fast SES Ferry Used In New Commuter Service Between L.I. And Manhattan page: 22
- Literature On Onboard Potable Water Disinfection Available From Everpure page: 22
- Service Marine Launches Modern 500-Passenger Dinner Boat For Cruise International page: 24
- Mackay, C.PIath Announce U.S. Sales, Service Pact page: 24
- Avondale Industries Wins Floating Prison Contract page: 25
- Seaco/Elliot Offers Improved Inflatable Rafts page: 25
- Liebherr Wins Large Gantry Crane Order From Japanese Shipbuilder page: 28
- LQMoffitt Merges With BFGoodrich page: 28
- ZF Of NA Introduces Extended Service Plan For Marine Transmissions page: 29
- Directions In Design Completes Interior Work On Two Sister Vessels page: 29
- New WD 234 Is Notable Addition To Line Of Deutz MWM High Performance Boat Propulsion Units page: 30
- COMSAT'S 'Cruise Calling' Makes Telephone Calls To And From Ship Easy, Clear, Direct And Private page: 30
- Alden's New Marine Fax Recorder Receives Weather Charts As Well As Navtex And Radioteleprinter Data page: 30
- AN UPDATE ON U.S. NAVY SHIP AND EQUIPMENT PROCUREMENT page: 33
- Avondale Awarded $319-Million Contract To Build Three Oilers page: 37
- Ingalls Shipbuilding Readies USS Wasp (LHD-1) For Delivery page: 38
- U.S. Navy Selects Bailey Network 90 System For New YTT Vessel page: 39
- Albert L. Bossier Jr. Named 1989 Nimitz Award Winner page: 40
- Sperry Marine, Philips To Cooperate On German ESM/ADF System page: 43
- Datrex Introduces Hydrostatic Release For Inflatable Life Rafts page: 43
- Poppe To Head Bailey Refrigeration's Miami Branch Operation page: 44
- SPD Awarded Contract To Supply Electric Plant Control Panel For Seawolf page: 44
- Robert A. Spoerl Named Chief Executive Officer At Coast Engineering page: 44
- Advanced Joiner Systems From Rockment Featured On New Cruise Vessels page: 45
- Mike Mitchell Appointed Raytheon Marine Company Marketing Manager page: 46
- New Free Brochure From Graboski Associates Details Graphics Work page: 46
- Coritz Appointed New VP And GM At IMO Pump Division page: 47
- J.M. Martinac To Build 2,560-Bhp Z-Drive Ship-Berthing Tug page: 47
- First Allison Gas Turbine Genset Shipped For DDG-51 Installation page: 48
- Universal Marine Medical Offers Reliable Source For Medical Supplies page: 49
- Mid-Coast Delivers Cummins-Powered Crabber-Tender page: 50
- Trinity Marine Group Delivers Two Crew Boats To Saudi Arabia page: 51
- Peters Named Managing Director, Raytheon Marine European Operations page: 52
- Jeffboat To Construct Three River-Tank Barges In $3-Million Contract page: 52
- Conrad Industries Delivers Second Set Of Twin Barges page: 53
- Unitor Group Reports 1988 Was Best Year Ever page: 53
- NOR-SHIPPING '89 Exhibition And Conference page: 54
- MWH Offers High-Quality, Inlet And Exhaust Valves For Marine Engine Applications page: 56
- Royal Schelde Launches Second Frigate In New Series page: 57
- Goldstar Precision Introduces New Generation Of Mono Radar page: 60
- Elomatic Group, Design Specialists, Offer Brochure On Engineering Services page: 60
- TFC Offers Major Price Reductions On New Line Of Waste Compactors page: 61
- Precision Control Offers Detailed Brochure On New Vacuum Flush Toilet page: 61
- Thomson-Gordon Appoints Hampton Sales Distributor page: 67
- MarineSafety Demonstrates Prince William Sound Simulation page: 68
- Furuno's New Improved Loran Provides Even Higher Position-Fixing Accuracies And Display Stability page: 68
- Viking's Commercial-Grade Six-Person Life Raft Exemplifies Modern Lifesaving Technology page: 71
- New Worldwide Distributor Network For EMD Power Products page: 72
- New SEA 156 VHF Marine Radio Keeps Complex Functions Simple page: 72