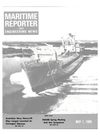
T e n v i g Offshore A.S Develops Low-Cost Early Oil Production Ship
An entirely new concept in offshore oil production facility, called the BTMM Production and Storage Ship, has been designed and developed by Tenvig Offshore A.S (Tenvig) of Oslo, Norway. The fully developed design of the ship and its systems was performed by Tenvig in cooperation with A/S Kongsberg Vapenfabrikk (KV).
The latter firm designed the riser and riser-handling systems and Aukra Bruk A.S d e s i g n e d and engineered special parts of the ship's systems.
The project's most outstanding feature, in addition to its storage capability, is the possibility of permitting early on-stream production at a modest investment.
The planning and conversion period (ready for tie-in) is estimated to be 20 to 30 months after the decision is made to proceed.
Also, the completion time is dependent on the characteristics of the oilfield. Estimates prepared by the designers indicate that such a project has the potential to reduce the general production costs.
The concept involves using a ship, either new or converted, up to the VLCC size as a floating production facility. The main advantages in using such a ship are: large storage capacity, large deck p a y l o a d c a p a c i t y , ample deck space for equipment, gas and water injection capacity, easy to maintain and dock if necessary, and low conversion/building costs.
The converted ship, or new, will be fitted with the BTMM Ship Stabilizing System, giving it motion characteristics comparable to a semisubmersible structure — a necessity for using ships as floating production facilities in the North Sea as well as under other conditions. This system and the newly developed BT Turret Production Platform, together with KV's multibore riser system, have made this project possible. The turret-table mooring allows the ship to always choose the optimum heading against the prevailing wave trains.
In designing the ship and its systems, North Sea weather conditions were used as a reference.
Tests by the designers and calculations have indicated high regularity and working time.
Whether an existing ship is converted or a new ship is especially designed for this purpose will have a minor effect on the overall technical concept. Converting a modern tanker does not create classification problems, and when converted it will be able to remain on location during the lifetime of the field without docking, p r o v i d e d proper protection, inspection and maintenance are arranged.
Preliminary Quality Assurances have been given by classification societies. Should docking be necessary, however, then it is a relatively easy job to disconnect the ship, pull the riser and proceed to a shipyard.
It is considered that the BTMM P r o d u c t i o n and Storage Ship's main application will be on medium and marginal fields as well as for deep-water fields. The feasibility study and projects executed have been based on a 100,- 000-dwt tanker—a size which can accommodate a peak production of up to 100,000 barrels of oil per day and will provide a storage capacity of about 500,000 barrels.
The design may easily be adapted to a larger tanker if increased capacities are desirable. For this purpose a larger turret production platform for three risers has been considered.
The proposed production systems o n b o a r d will be of wellknown designs, and will be provided to the client's specifications.
All the high-pressure parts of the processing system are located inside the turret production platform.
Additional l o w - p r e s s u re processing facilities and storage are on the main deck and in the cargo tanks. The p i p e l i n e for transferring oil is connected either to a loading buoy or to a pipeline where this is possible.
Off-loading also may take place from a boom at the stern of the ship.
Various s a f e t y a s p e c t s have been considered in the design.
Some of t h e s e c o n s i d e r a t i o ns were: the distance between the living quarters and the hazardous area; location of living quarters in order to reduce heat transference, and a water-sprayed blast and fire wall. An anchor quickrelease system combined with the emergency-generator-driven bowthrusters enable the ship to move away from a danger zone.
Stabilizing System The BTMM Ship Stabilizing System is the key to this project.
The submerged adjustable stabilizing pontoons, Figure 1, fore and aft have the capability of tying up huge oscillating water masses at a level in the sea where the energy is low. Besides, there is a time lag between the wave forces acting on the hull and on the pontoons, resulting in considerable dampening of the ship's motions and accelerations.
This Tenvig system has been thoroughly model tested and highly s o p h i s t i c a t e d computer programs imperative for the complex calculations and design of the pontoons and their exact positioning were d e v e l o p e d in cooperation with Franlab Marine (the French Petroleum Institute). Aukra Bruk A.S participated in the detailed design of the vertical movement and locking system.
Tenvig is presently preparing a full-scale test of the system. The test is expected to be carried out in the North Sea with a 500 to 600-foot vessel.
Production Platform The BT Turret Production Platform is octagonal in shape and is placed on top of a central turret table mooring. It comprises two or more decks on which all highpressure processes are arranged, i.e., first stage separation as well as gas and water injections. Consequently, all transfers between the stationary turret and the rotating ship are arranged via flexible hoses under low pressure.
In addition to the production facilities, the turret also carries a constant tension mooring system for eight piled anchors, the riser tensioners and the riser handling crane and equipment. A moon pool in the center of the turret is arranged to house the riser. The diameter of the moon pool will allow for the required riser angles.
Turret mooring has been used successfully by several drillships for a number of years by The Offshore Company. The turretmoored drillship Discoverer 534 has drilled in water depths ranging from 130 to 3,500 feet.
The mooring system permits a moored vessel to alter its heading to meet changing sea and weather conditions. Vessel headings may be readily changed to minimize motion during well operations to p r o v i d e p r o t e c t i ve shelter for offloading supply boats or to reduce mooring loads during a storm.
Subsea Systems The riser and subsea systems were developed by A S Kongsberg Vapenfabrikk, who in turn collaborated with Cameron Iron Works on oil tool equipment.
Kongsberg has provided arrangement, calculations and d e s i g ns for: riser tensioning and handling system; riser body including the riser lower package with universal joint and riser stab-in section, including isolating valves package, and riser base including retrievable flowline box with tiein points and valve-less water injection and service header manifolds.
Kongsberg has tailormade the arrangement to the BT Turret Production Platform to avoid interface problems. Also, the riser handling procedures have been given special attention in order to increase the overall system regularity.
The three systems described above are patented. Full details of these three systems may be obtained through Tenvig Offshore A.S, P.O. Box 2315, Solli, Oslo 2, Norway.
Read T e n v i g Offshore A.S Develops Low-Cost Early Oil Production Ship in Pdf, Flash or Html5 edition of May 1980 Maritime Reporter
Other stories from May 1980 issue
Content
- M a r A d W i l l Sponsor C o a l - F i r i n g Seminar page: 4
- Lobster Boat To Be D e s i g n e d By B l a n c ke page: 4
- Kormarine Will Have International Exhibits page: 4
- A m e r i c a n T r a d i n g Asks T i t l e X I For Six Tankers C o s t i n g $ 4 0 8 M i l l i on page: 6
- Halter Delivers Two Large-Capacity Crewboats page: 6
- T r a n s a m e r i c a D e l a v a l, Research-Cottrell Form Joint V e n t u re page: 6
- General Dynamics Christens Its First LNG Carrier Built For U.S. Trade page: 6
- Sembawang Yard To Invest In Construction Of New Floating Dock page: 8
- L i t e r a t u r e A v a i l a b l e On M a r i n e A n d O f f s h o re H y d r a u l i c Equipment page: 8
- S i f c o P r o v i d es O n b o a r d P l a t i n g - L i t e r a t u r e A v a i l a b le page: 8
- Australian Navy Heavy-Lift Ship Launched At Carrington Slipways page: 10
- D e l a w a r e V a l l e y ASNE Discusses Computer M o d e l i n g And Ship Performance page: 10
- Utility Vessel And Tugboat Delivered By Service Machine Group page: 10
- Promotions A nd Retirements At El Paso LNG Company page: 11
- Literature Available On New Decca Loran C Unit page: 11
- Guidance Notes For Coal-Burning Ships Available From Lloyd's page: 11
- Self-Unloading Bulk Carrier Delivered To ASC By Bay Shipbuilding page: 12
- Honeywell-ELAC Names Reimann As Consultant page: 12
- Hillman Changes Name To HBC Barge, Inc. page: 12
- George K. Geiger Joins Bay Shipbuilding Corp. page: 15
- Delaval Will Test Use Of Coal-Derived Fuel page: 15
- Navy Contracts Totaling $203 Million Awarded To Todd Shipyards- Backlog Is $1.5 Billion page: 16
- Halter Delivers Third 110-Foot Supply Vessel To C & E Boat Rental page: 17
- Amsterdam Dry Dock Announces Major Modernization Of Facilities page: 17
- First Of 60-Barge Order Delivered By NABRICO page: 17
- Garlock Introduces Expandable Packing- Literature Available page: 17
- Four Supply Vessels Of New Class Delivered To Tidewater Marine page: 18
- Fourth Crandall Drydock For Belgium Placed In Service page: 18
- Two Executives N a m ed At Mississippi M a r i ne page: 19
- Tacoma B o a t b u i l d i n g Appoints Two N e w M a r k e t i n g Directors page: 19
- N a i k a i Zosen Delivers The P r a n e d y a Pratama page: 19
- Designers & Planners Sold—Names Four To Top M a n a g e m e n t Posts page: 20
- Balehi M a r i n e Delivers Two O f f s h o r e Crewboats page: 20
- Sarex Oil/Water Separators Approved By U.S. Coast Guard —Literature Available page: 20
- Paceco Cranes Delivered To Matson's L.A. Terminal page: 22
- AP L A n d Encinal To Develop Container Terminal In A l a m e da page: 23
- Norshipco To Complete O c e a n Barge For CCT page: 24
- The Shipbuilding Market In The USA page: 24
- Bulletin A v a i l a b l e On Elliott Tube Puller page: 26
- Bethlehem's Sparrows Point Y a r d Gets First Drilling Rig Contract page: 26
- McAllister Brothers Acquires Independent Towing Of Philadelphia page: 27
- N e w York Section SNAME Meeting Discusses Crude Oil Washing Systems page: 27
- L i t e r a t u r e A v a i l a b l e On B u t t e r w o r t h Systems N ew O i l / W a t e r Separators page: 28
- Hudship Reenters Pushboat M a r k et page: 28
- Literature Available On Bomar Deck Hatches page: 28
- Joint Venture Formed By Taylor And Hydrospace page: 28
- Record A t t e n d a n c e At I N A A n n u a l M e e t i ng page: 29
- Six A p p o i n t m e n ts Announced For I n t e r l a k e Steamship page: 29
- Literature Available From Elliott Co. On High-Speed Gears page: 29
- Santa Fe International And Acres Consulting Form Joint Venture page: 31
- New Rust Inhibitor Introduced By Farboil —Literature Available page: 31
- Paceco Awards Contract - P a r t Of $26-Million Expansion At Gulfport page: 31
- G u i d e d - M i s s i l e D D G Christened At Ingalls S h i p b u i l d i n g Y a rd page: 32
- Shaft A l i g n m e n t Was Topic At P h i l a d e l p h i a Section SNAME M e e t i ng page: 34
- Three A p p o i n t m e n t s Announced By R.J. Brown & Associates Firms page: 34
- Westinghouse Gets $ 6 - M i l l i o n Contract For Cruiser Gears page: 36
- W a r r e n T. M y e r s Joins W h i t e h a l l Brokerage page: 36
- Halifax Yard Awards $1.3-Million Contract For Modernization page: 36
- . J . Henry Elected To Norshipco Board page: 36
- Vincent Fiorenza Gets Added Duties At Moore McCormack page: 37
- M a g n a v o x O f f e r s N ew M o n i t o r i n g System — L i t e r a t u r e A v a i l a b le page: 38
- N e w Diesel Introduced By C u m m i n s E n g i n e - L i t e r a t u r e A v a i l a b le page: 38
- $C19.5-Million Modernization Under Way At Halifax Shipyards page: 38
- Student Paper Presented At SNAME Chesapeake Section page: 38
- T e n v i g Offshore A.S Develops Low-Cost Early Oil Production Ship page: 39
- $46.8-Million Research Facility To Be Built In St. John's, Newfoundland page: 40
- Blancke Gets Contract For Fishboat Design page: 41
- Tracor W i l l Develop Communications System For I n l a n d W a t e r w a ys page: 41
- New Salvage Technique Developed In Sweden page: 41
- $ 2 4 . 6 - M i l l i o n Contract A w a r d e d To Sperry For W o r k On Frigates page: 42
- L i t e r a t u r e A v a i l a b le On ITT Decca M a r i n e 's N e w A u t o p i l o t System page: 42
- M.A.N. Acquires Majority Shares in B & W Diesel A/S page: 42
- Literature Available On Chesterton Pump And Valve Packings page: 42
- Samson Offers Literature On Synthetic Ropes page: 43
- Literature Available On Tracor Automatic Omega page: 43
- NKK To Build Two Drill Rigs For Sedco At Cost Of $29 Million page: 43
- Safety And The Marine Environment page: 44
- R.A. Sleiertin Joins Career Associates page: 46
- Brochure Available On Comsat General Marisat Terminal page: 46
- N e w York City's Big A p p l e Goes To Sea page: 47
- Second Trident Submarine Launched At Electric Boat page: 47
- IME Meeting Discussed Combustion Systems And Use Of New Fuels page: 48
- Levingston And Asmar Deliver First Drill Rig Of A New Class page: 48
- New Oil/Water Emulsion System From Hoffert— Literature Available page: 49
- L P G / A m m o n i a Tanker D e l i v e r e d By W a r t s i la page: 50
- Literature Available On Simrad's Latest Digital Echosounders page: 50
- R.R. Barkerding Joins Ryan-Walsh Stevedoring page: 50
- SNAME New York Section Hears Paper On SWATH Vessels page: 51
- J.H. Leonhard Named Marketing Manager At International Paint page: 51
- Literature Available On Rockwell's Redesigned Steel Globe Valves page: 51
- Electric Boat Division Launches Navy Attack Submarine 'Boston' page: 55