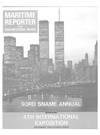
Renk Gear System Provides Constant-Frequency Power Generation From Main Engine
As the second largest consumer of energy aboard ships, the power generation equipment has been the object of many studies aimed at obtaining overall higher efficiency and lower electrical power costs.
One solution is driving a generator, at constant speed, off the main propulsion engine that is operated at varying speeds when fitted with a fixed-pitch propeller. Zahnraederfabrik Renk AG of Augsburg, West Germany, has developed a special gear system able to accomplish that result.
The company's RCF (Renk Constant Frequency) unit is a differential epicyclic gear capable of insuring constant-speed drive to the power generator in a fully automatic mode. This gear is usually mounted on the forward end of the engine crankshaft. The RCF allows a flexible layout in five different positions of the generator system, depending on the space available in the engine room. An additional possibility is to install the RCF along the propeller line on the main engine power takeoff side.
The RCF's speed superposition is achieved by hydrostatic or electric control. The basic gear ratio is cho- _ sen so as to obtain generator syn- chronous speed output for a stan- dard frequency generator at 85 percent of the engine rated speed. In this way the hydrostatic or electric controls of the RCF will drive the generator at constant speed while the main engine is operating between 70 and 100 percent of its rated speed. The annulus of the epicyclic gear will remain fixed while the engine is running at 85 percent of its rated speed; in this case the power transmission is merely mechanical.
If the engine speed drops, one portion of the power output is transmitted to the gear unit via a dc motor. The annulus is driven against the supporting torque by the motor, and the epicyclic gear is superimposed motorwise. The diesel engine associated with the mains and the current converter supplies the power for the dc motor/generator undergoing regulation.
In the event the diesel engine speed rises, the dc motor becomes the generator, and the surplus power transmitted by the gear unit is fed into the mains via the dc motor/ generator and the current converter.
The annulus is then rotated by the dc motor/generator towards the supporting torque, being simultaneously restrained, and the epicyclic gear is superimposed generatorwise.
The gear unit is connected to the forward crankshaft end of the diesel engine through a highly flexible coupling that dampens the vibration of the plant.
The dc motor/generator of vertical design is fitted on the gear casing (photo). It features an attached electromagnetic brake that makes it possible to mechanically lock the annulus. The generator is coupled to the gear unit through a bevel gear train at a 90-degree angle to the crankshaft. Between the gear unit and the generator there is an electromagnetic clutch that allows connection and disconnection of the generator during operation. This clutch also provides overload protection.
For single generator operation, the auxiliary diesel engine generators are cut out after the load has been taken over by the shaft-driven generator. The regulating system of the dc motor/generator now insures frequency regulation of the shaftdriven generator. In parallel operation, the auxiliary diesel engine generators remain coupled to the bus after the shaft generator has been connected.
By adopting a suitable simulating calculation method, an optimal inter- related behavior of all drive train components is studied, including the propeller, main propulsion engine, gear unit, shaft-driven generator, and the mains supply including diesel-driven generators operating in parallel.
The high efficiency of the gear unit is one of the essential factors for the economy of the plant. The RCF system operates with an efficiency ranging between 93 and 97 percent. The system, which requires a relatively low capital investment, is also advantageous to use because of the potential fuel cost savings.
Renk has sold approximately 30 RCF systems to be powered by M.A.N.-B&W two-stroke engines.
This is a joint development of Renk and M.A.N.-B&W. Four 1,100-kw electrically controlled units are now in service on refrigerated containerships with fixed-pitch propellers built at the German shipyard Bremer Vulkan. Two 700-kw hydraulically controlled systems are for 79,900- dwt tankers built at the Uljanik shipyard in Yugoslavia, and one 900-kw unit is on order for Burmeister & Wain, Copenhagen.
The German company's U.S. subsidiary is Renk Corporation of Duncan, S.C.
A complete full color 26-page brochure fully describing in detail the Renk organization and its equipments and services on a worldwide basis is available free of charge. For your copy, Circle 20 on Reader Service Card
Read Renk Gear System Provides Constant-Frequency Power Generation From Main Engine in Pdf, Flash or Html5 edition of November 1985 Maritime Reporter
Other stories from November 1985 issue
Content
- BPNAP Marine Lubricants Relocates In N e w Jersey page: 5
- Clemlite® System Offers Economy And Safety page: 5
- Fifth Maritime Prepositioning Ship Delivered By Bethlehem-Beaumont page: 6
- Versatile Vickers Awarded Refit Contracts Worth $15 Million From Canadian Navy page: 6
- Todd-Seattle A w a r d ed $ 6 - M i l l i o n N a v y Contract For Work On Support Ship page: 7
- Oceaneering Uses Signals From GPS Satellites To Position Drilling Rig page: 7
- Newman's Offers N ew Brochure On Complete Line Of Ball Valves page: 8
- Royal Navy Purchases Raytheon Bathy System page: 8
- Africa Ocean Lines Getting First N e w Containerships From East German Shipyard page: 9
- Waller Heads N e w Firm Based In San Diego To Provide Contract Management page: 10
- Foss Initiates New Container Feeder Service page: 10
- Fuel Tech Adds F.A. Hughes As Subsidiary, Amalgamating Combustion Technologies page: 10
- Moon Engineering Expands— Moves To Portsmouth, Va. page: 11
- Ingalls Shipbuilding Christens Another Aegis Missile Cruiser page: 12
- Penn Ship Delivers USNS Denebola To The Navy Three Weeks Early page: 16
- Hartley Marine To Operate Walker General Cargo Terminal In Paducah, Ky. page: 16
- Bailey Controls Forms Marine Market Group To Handle Worldwide Sales page: 18
- Metropolitan Offers N ew Grooved Pipe Fittings page: 18
- Jeffboat, Incorporated Delivers Twin-Screw Towboat 'Alois Luhr' page: 20
- Envirovac Receives Contract To Equip Twelve U.S.C.G. Cutters page: 24
- Canadian Engineers To Hold MariTech '86 In Vancouver, June 5-7 page: 24
- Transamerica Delaval's Deltex Repair Facility Offers Free Color Brochure page: 26
- New Manual Details Tank Protection Against 5,000 Products page: 28
- Jorgensen Company New Licensee For Escher Wyss CP Propellers page: 28
- Blue Streak Industries Delivers First Lift Boat With 110-Foot "legs' page: 30
- Pyramid Pump Offers Brochure On Deepwell Barge Pumps page: 32
- Nissen Metal Marker Readable At 2,100° F page: 32
- SNAME Southeast Section Holds General Meeting page: 32
- Alexander Industries Appointed Microphor Representative page: 40
- Hitachi Zosen To Build Giant Submersible Barge page: 41
- Samson Ocean Introduces H i g h - S t r e n g t h Dock Lines page: 41
- MacGregor-Navire Wins Contracts For RO/RO Ramps In U.K. And India page: 42
- Vikubo Offers Free Brochure On Foam-Filled Floating Fenders page: 42
- ' 85 Sales Of Imperial Survival Suits Nears 100,000—Literature Offered page: 43
- BPNAP Offers Free Color Brochure On Products And Services page: 44
- New Chemical Parcel Barging Service Offered In Port Of N e w York page: 45
- 93rd S N A M E Annual Meeting Fourth International Maritime Exposition page: 50
- Raytheon Adds New Frequency To DSF-6000 Fathometer Depth Sounder page: 79
- High-Performance Bearings Reduce Costs By Extending Dredge Life page: 80
- New Edition Of 'Research Manufacturing, Engineering' Now Available From M.A.N. page: 80
- Ogden Completes Sale Of Avondale Industries Common Stock page: 80
- Systonetics Offers Free Brochure On Automated Project Management Systems page: 81
- P.A.D.D. Co. Opens New Drydock To Begin Shipyard Improvements page: 82
- USS Safeguard Commissioned At Peterson Builders' Sturgeon Bay Yard page: 84
- Nippon Kokan To Build Semi-Submersible Rig For Norwegian Firm page: 85
- Transamerica Delaval Offers Broad Range Of Solenoid Valves page: 85
- Moss Point Marine Will Build Two Fireboats Designed By Nickum & Spaulding For Long Beach page: 86
- Marine Machinery Association Sponsors Government-Industry Forum page: 86
- Brown Announces Organizational Changes At Maritime Administration page: 89
- Bretvin Named President And COO Of Stolt-Nielsen page: 89
- Norcontrol Engine-Room Simulator For Singapore Nearing Completion page: 90
- Fiori Named Director Of Special Services At American President page: 90
- W a t e r w a y Operator Survey Launched page: 90
- Newport News/lntelmach Introduce The IM (Intelligent Machine) Series page: 91
- NRL Names Bradley New Superintendent, Acoustics Division page: 91
- N e w Portable Transmitter Provides Emergency Shutdown Control page: 91
- Duramax Introduces Two N e w Styles Of Tow-Knees page: 91
- New Mono-Hull Form Provides Ultra-Stable Drilling Platform page: 92
- MSI Offers 21 MarineSafety Training Courses For 1986 page: 95
- No Lubrication Required For Falk 'Torus' Couplings page: 97
- Eastern Marine Contracted To Build Scallop Trawler page: 98
- TeleSystems' Compact Communications Unit Approved page: 98
- D r e w AMERGIZE® Tested And Chosen For All Ships In Major Fleet page: 99
- Falk Fluid Couplings Provide xSoft-Touch' page: 99
- VIEWNAV® Offshore Platform Monitoring System Installed In North Sea And Off California page: 100
- MSC Awards $22.3-Million Contract To Trailer Marine page: 101
- Hagglund Introduces New Hydraulic Motor page: 101
- KHD And MWM Form New Diesel Engine Group page: 102
- New X-FLO Steam Compressor Fabricated To Withstand Corrosion page: 102
- Renk Gear System Provides Constant-Frequency Power Generation From Main Engine page: 104
- Oerlikon Introduces N e w Line Of Maintenance And Repair Alloys page: 105
- HydroComp Develops Naval Engineering Software Programs page: 109
- Nineteen N e w Members Elected To American Bureau Of Shipping page: 109
- Almerico Joins Moss Point As Vice President page: 109
- Sperry's New Satellite Communicator Granted Unrestricted Type Approval page: 110
- Raytheon Introduces New Commercial 'IMO' Recording Echo Sounder page: 110
- Navigation Sciences Offers Viewnav® Master Mariner Brochure page: 111
- Norcontrol Wins Contracts For Liquid Cargo Control And Monitoring Systems page: 111
- Free Full-Color Brochure On Monitoring System Offered By Siemens AG page: 111
- Aeroquip Offers Bulletin On International Fluid Connector Identification page: 112
- Bethlehem-Sparrows Point To Begin Work On Navy Ocean Survey Ships page: 112
- New Chesterton Cartridge Seal Meets API 610 Specs page: 112
- Japan Radio Introduces Two N e w Products—GSC-80 ODARS And JLR-4000 GPS Navigator page: 113
- Avondale Christens First Of Five Fleet Oilers Building For Navy page: 119
- Alaska Diesel Electric's 'Lugger' Engines Chosen For N e w Tug page: 122
- Uniden® Offers Three New Electronic Aids page: 122
- Polymer Alloy Extends Icebreaker's Propeller Shaft Bearing Life page: 123